Imagine spending months purchasing a new machine. You research suppliers, secure the budget, and place the order. When it arrives, you realize there’s been a crucial oversight: no one knows how to set it up or train your team. Suddenly, every task becomes a challenge—from installing to running the machine.
This is how the Computerized Maintenance Management System (CMMS) implementation process goes for many facilities. Companies invest in software but struggle to get it off the ground.
So, how can you avoid the most common CMMS implementation stumbling blocks? Let’s dive in.
Pitfalls to avoid
After getting the right software, you want to see returns on your investment as quickly as possible. To keep your CMMS implementation on track, avoid the following mistakes.:
1. Misaligned leadership
Without alignment at the leadership level, projects can stall before they even begin. To avoid this, get everyone on the same page about what success looks like in terms of ROI and timelines.
Key steps to take here include:
- Set clear implementation milestones with actual numbers. For example, aim for 100% user training completion within one week or 75% work order completion rates within the first three months.
- Create a realistic timeline with resource allocation for each phase. For example, MaintainX allocates three weeks per site for implementation.
- Document and communicate roles and responsibilities across departments so everyone knows who is supposed to do what and by when.
2. Rushing past the basics
Many organizations make a critical mistake: trying to implement every CMMS feature at once before they've mastered fundamental maintenance best practices. It might be tempting to run—but before that, you need to crawl and walk.
Get the basics right with these key steps:
- Assess your current maintenance practices and identify gaps. Before implementing new software, understand how your team currently handles tasks like work orders and preventive maintenance. This way, you can focus on the most critical improvements first.
- Master fundamental features, like work orders, before moving to advanced capabilities, like predictive maintenance.
- Create a phased rollout plan that considers your team's current workload and skills.
3. Poor data foundations
Imagine your technicians wasting hours searching for equipment because one team calls it "Pump 1" while another calls it “Pump One.” The difference might seem small, but inconsistencies like this can derail an implementation. Before implementation begins, take time to establish and document clear standards.
Here's how to get it right:
- Establish clear, consistent naming conventions before migration.
- Clean and validate existing data before moving it to the new system.
- Set up a process for regular data quality checks.
4. Inadequate training
A CMMS can only deliver value if your team knows how to use it properly. Too often, organizations schedule a single generic training session and expect everyone to become experts immediately.
The result? Frustrated technicians who revert to old methods, managers who don't get the reports they need, and an investment that gathers dust.
Make sure the software you choose offers your team the resources they need to get started. For the Public Works Department of the Cayman Islands government, this was critical to implementation success.
“We had videos and step-by-step PDFs,” recalls Acting Facilities Manager Davanni James. “These materials guided the team through everything from creating work orders to indexing their locations in MaintainX, ensuring that our team could confidently manage tasks right away.”
Here's how to build an effective training program:
- Develop role-specific training plans that match actual day-to-day work.
- Create hands-on exercises using real equipment and scenarios.
- Build a library of quick reference guides and procedures for common tasks.
- Identify and train super-users who can support their colleagues.
From pitfalls to performance: Turn your CMMS investment into long-term value
Companies that take time to get the basics right don't just avoid these common implementation pitfalls—they create the foundation for long-term maintenance excellence.
Take it from PharmaNZ, a health supplement manufacturer who saved $70K on maintenance after implementing MaintainX: “We are definitely far from hitting the peak with our savings from MaintainX—it’s only going to get better,” explains Scotty Death, PharmaNZ’s chief operations officer. “MaintainX will definitely get us to predictive maintenance rather than just preventive maintenance.”
Get more ideas from our CMMS implementation whitepaper
Our comprehensive CMMS implementation whitepaper combines insights from thousands of successful implementations to create your roadmap for success. Download it today to access:
- A detailed checklist of must-have CMMS features for manufacturing facilities.
- A step-by-step preparation guide for smooth implementation.
- Best practices for driving long-term adoption and ROI.
Ready to turn your CMMS investment into lasting value? Download the whitepaper now and get the steps to implementation success.
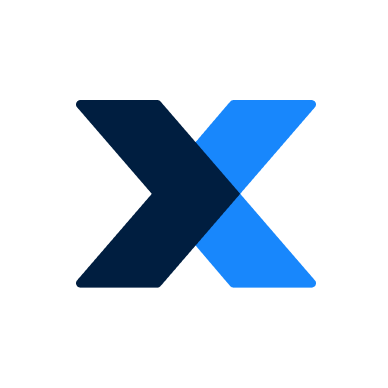
Equipo Editorial de MaintainX
The MaintainX team is made up of maintenance and manufacturing experts. They’re here to share industry knowledge, explain product features, and help workers get more done with MaintainX!