Many teams pour their energy into implementing a Computerized Maintenance Management System (CMMS) and assume that once it’s in place, their job is done. However, nearly 95% of plant maintenance managers report not using their CMMS to its full potential after implementation. As a result, they leave significant value on the table in the months and years after implementation. That’s why it’s important to have a plan for post-implementation.
Using your CMMS to its full potential comes down to continually demonstrating its benefits to your frontline workers. When they experience its advantages firsthand, they'll be motivated to keep using the system.
For example, Wauseon Machine found that having a CMMS made it easier for the team to tackle tasks efficiently. “Our maintenance guys have the app on their phones, so managers just approve the work order, they get a notification immediately, and it’s on their schedule,” Bill Johnson, Wauseon’s Vice President of Precision Machining. “I think it saved our maintenance team a good 45 to 50% of work time from what our old system was.”
Watch the video for advice on the challenges maintenance professionals face when getting started with a CMMS, then read on for more post-implementation tips.
Three keys to long-term CMMS success
After implementing your CMMS, keeping up the momentum is crucial for long-term success. Here are three key strategies to ensure your system delivers value well after launch.
1. Track what matters
Feeling like your CMMS provides value isn’t as compelling as proving it. To do that, focus on metrics directly linked to operational goals and stakeholder priorities.
For example, if reducing emergency repairs is a priority, track Mean Time Between Failures (MTBF). This way, you’ll be able to continuously show your team how the CMMS is improving their performance—which keeps both leadership and frontline workers invested in the CMMS’ success.
That said, no matter your specific goals, here are some key metrics you should always consider:
- Monitor work order data: Look beyond simple completion percentages. Track how long work orders stay open and which types take the longest. This data helps you spot bottlenecks—like whether certain equipment consistently needs more attention or if specific shifts complete fewer work orders. By identifying these patterns, you can make targeted improvements to your CMMS workflows and ensure the software is actually helping your team improve.
- Measure preventive maintenance vs. reactive maintenance ratios: Watch how this ratio changes over time. If you still have 70% reactive maintenance six months after implementation, you might need to adjust your PM schedules or improve task descriptions. Try to move towards an 80/20 preventive to reactive ratio. This metric directly shows whether the CMMS is actively improving your processes.
- Calculate ongoing ROI: Keep tracking the numbers that matter—from downtime savings to reduced inventory spending. These concrete numbers help justify continued investment in your CMMS and motivate your team.
2. Keep your team engaged
Forming a new habit takes time—between three weeks to a few months, depending on the person. That means you need to keep your team regularly engaged with the CMMS until using it becomes second nature. To keep up the momentum and encourage continuous improvement, you can:
- Share success stories: For example, highlight when a technician's detailed work order notes helped prevent a failure. Or showcase how the team's CMMS use directly reduces downtime. These concrete examples show your staff that their efforts make a real difference.
- Gather regular feedback and refine processes: Set up regular check-ins to discuss what's working with the CMMS and what isn't. Also, pay attention to how your team is using the tool. For example, if workers often add the same notes to particular tasks, update the standard procedures to include this information. Small refinements based on actual usage can significantly improve efficiency.
- Update training materials: Keep your documentation fresh and relevant. For example, when workers discover better ways to handle specific tasks, add these tips to your guides.
3. Start small, then scale
A CMMS implementation is a big undertaking, so be realistic about where your team is. Rather than turning on every feature at once, make sure everyone learns and masters the basics. Here’s how it could look:
- Crawl, walk, run: Although the allure of cutting-edge technology—like AI for smarter maintenance—is strong, your implementation will backfire if you move too quickly. Just because your team isn’t ready for advanced features yet doesn’t mean they won’t be in the future. First, start with basic asset management, then move to advanced inventory tracking, and later you can introduce predictive maintenance and AI.
- Scale across facilities: When a strategy works well at one site, document it for broader implementation. For example, if one facility's PM scheduling method reduces downtime significantly, create a standardized process for other sites. This helps you replicate successes and maintain consistency across your organization. It also reinforces the CMMS’ benefits—as your teams see these wins spread across facilities, they're more likely to continue embracing the CMMS in their workflows.
Get the full insights in our CMMS Implementation Whitepaper
A successful CMMS implementation isn't the end goal—it's the foundation for continuous improvement in your maintenance operations.
Our CMMS Implementation Whitepaper gives you a roadmap for success, combining insights from thousands of successful implementations. Download it today to access:
- A detailed checklist of must-have CMMS features for manufacturing facilities.
- Step-by-step preparation guide for smooth implementation.
- Common pitfalls and proven strategies to avoid them.
Ready to get real, lasting results from your CMMS investment? Download the whitepaper now and get the insights you need to succeed.
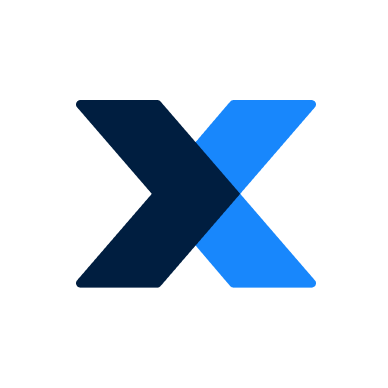
Equipo Editorial de MaintainX
The MaintainX team is made up of maintenance and manufacturing experts. They’re here to share industry knowledge, explain product features, and help workers get more done with MaintainX!