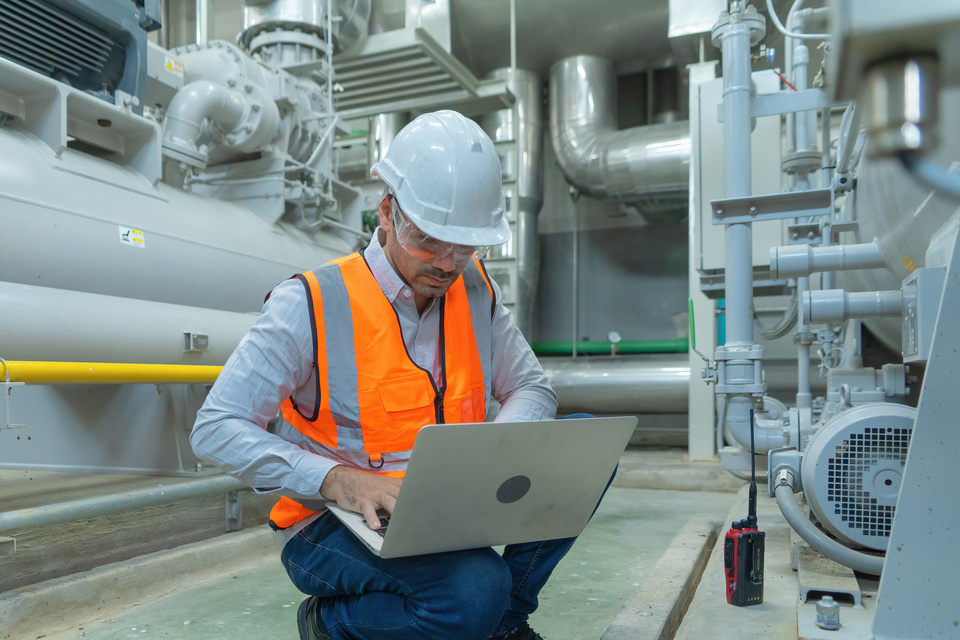
Los fabricantes utilizan FMEA (Análisis de modos de falla y efectos) para identificar las posibles formas en que se puede producir un error en sus flujos de trabajo. Por supuesto, esto puede incluir una amplia gama de fallos (como fallos en el equipo, el proceso o el diseño). Esta publicación compara dos tipos de FMEA (PFMEA frente a DFMEA), que ayudan a identificar los modos de falla del proceso y del diseño.
En primer lugar, ¿qué es la FMEA?
El FMEA es un enfoque estratégico para identificar posibles fallas en un proceso (fabricación, ensamblaje o logística) o diseño (de un producto o servicio).
Como el La Sociedad Estadounidense para la Calidad explica:
«El análisis de modos y efectos de falla (FMEA) es un enfoque gradual para identificar todas las posibles fallas en un diseño, un proceso de fabricación o ensamblaje, o un producto o servicio. Es una herramienta común de análisis de procesos».
El FMEA incluye dos componentes principales:
- Modos de fallo: la manera o el modo en que un proceso o diseño puede fallar. Por ejemplo, un empleado con exceso de trabajo puede pasar por alto un defecto cuando está a cargo de las inspecciones.
- Análisis de efectos: las consecuencias del fracaso. Por ejemplo, un cliente podría demandarte si un producto defectuoso le perjudica de alguna manera.
DFMEA y PFMEA son tipos de FMEA. Si bien los procesos DFMEA y PFMEA son similares, las entradas y las salidas son diferentes.
«La resolución de problemas desde la raíz, mediante enfoques como el análisis de árboles de fallas y el análisis de causa y efecto o modos y efectos de falla (FMEA), es una parte fundamental de la estrategia de mantenimiento y confiabilidad de cualquier organización».
McKinsey
¿Qué es DFMEA?
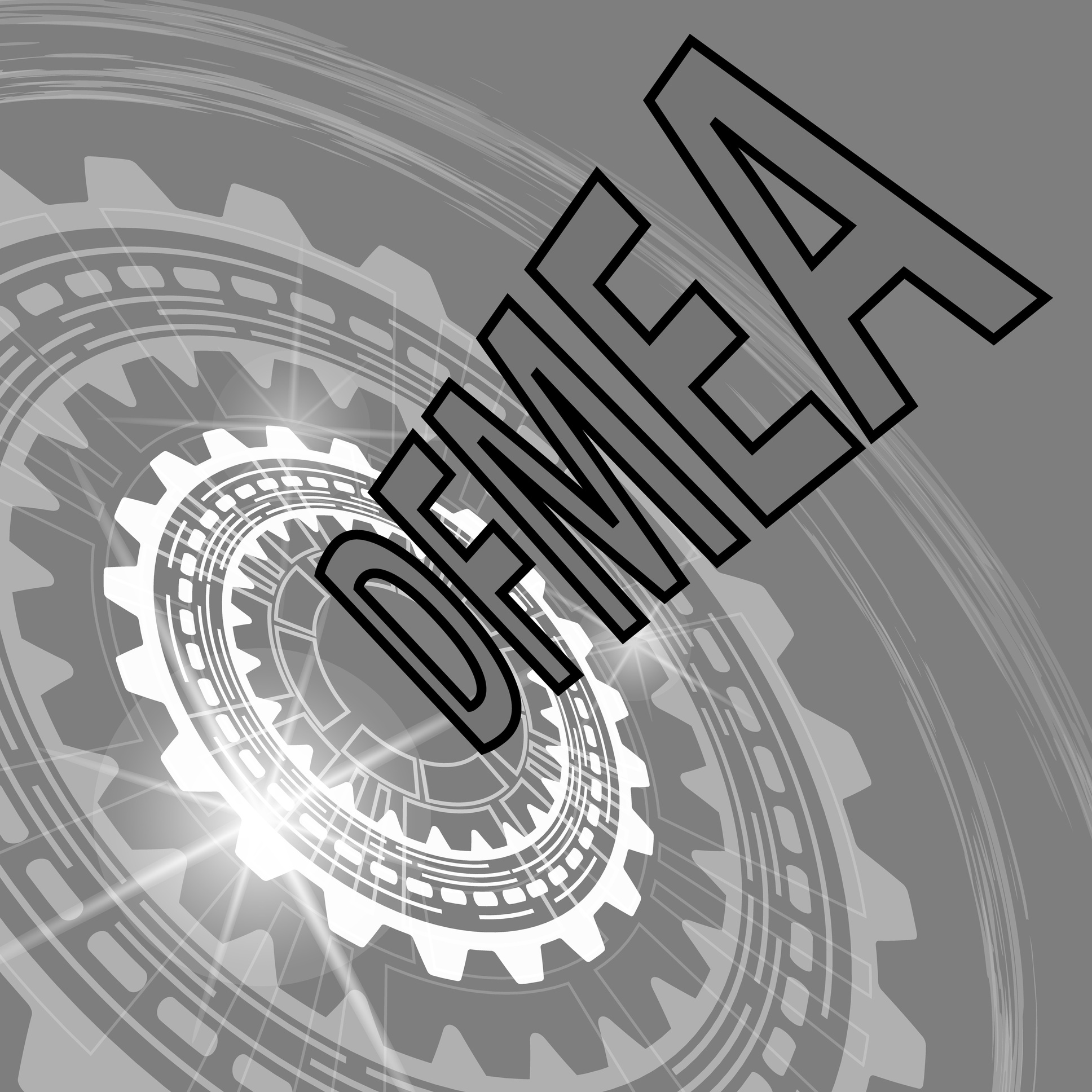
DFMEA (Design FMEA) es una técnica que ayuda a identificar y corregir errores de diseño. El método se usa en todos los sectores para minimizar los costos asociados a las fallas de diseño, como las retiradas de productos o las demandas de clientes afectados por fallas en el diseño.
El DFMEA implica enumerar los posibles modos de falla y sus posibles efectos, junto con una clasificación de gravedad, detección, ocurrencias y seguridad. A continuación, calcule un RPN.
RPN es el Número de prioridad de riesgo, una evaluación numérica del riesgo asignado a un proceso, o a los pasos de un proceso, como parte del análisis de modos y efectos de falla (FMEA). Un equipo asigna a cada modo de falla valores numéricos que cuantifican la probabilidad de que ocurra, la probabilidad de detección y la gravedad del impacto».
Debe ejecutar DFMEA cuando aún esté desarrollando el diseño del producto. Pensar en los posibles modos de fallo durante el desarrollo del producto ayuda a evitar fallos que, de otro modo, podrían incorporarse directamente al diseño.
«Resolver los problemas conocidos con soluciones conocidas le ayuda a obtener un rápido retorno de la inversión y ganancias tempranas que pueden duplicarse en todas las instalaciones. Estas pequeñas ganancias también ayudan a mejorar el apoyo organizacional por parte de los empleados, que es fundamental para cualquier programa de análisis, y a mejorar la gestión para mantener la inversión».
Forbes
¿Qué es el PFMEA?
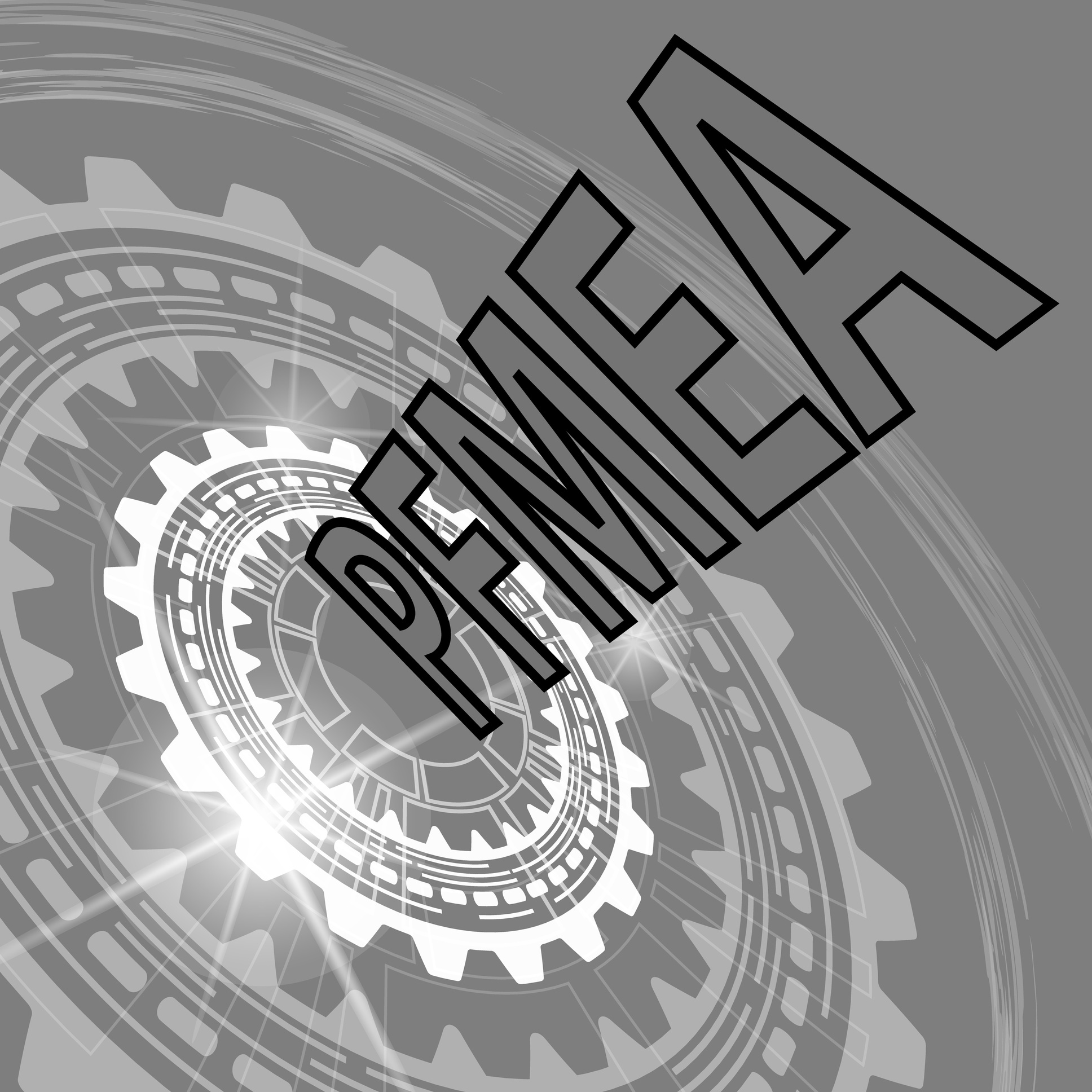
PFMEA (Process FMEA) ayuda analizar modos de fallo de proceso. En otras palabras, el PFMEA ayuda a identificar las posibles fallas causadas por un proceso. Un PFMEA actúa como un documento vivo (físico o digital) creado para cada proceso y actualizado a lo largo del ciclo de vida del producto.
En este caso, debe comprender el impacto de la interrupción de un proceso para minimizar el efecto de la falla o evitarla por completo.
Tenga en cuenta que es posible que se produzcan errores incluso cuando utilice PFMEA. De lo contrario, no necesitaría administradores de confiabilidad y mantenimiento. Sin embargo, el PFMEA puede ayudar a minimizar la posibilidad de que se produzcan fallos. Debe revisar el PFMEA cuando se produzca una falla o si se produce un cambio significativo en su equipo, entorno de fabricación y recursos.
DFMEA frente a PFMEA: diferencias clave
Ahora que conoce el significado de PFMEA y DFMEA, analicemos algunas diferencias clave entre los dos:
FMEA frente a PFMEA: el proceso
Ambos tipos de FMEA siguen un proceso ilustrado en el Manual de AIAG-VDA FMEA—puede usarlo como guía para ayudarlo a desarrollar el análisis del modo de falla y los efectos de su producto y diseño.
El manual incluye las mejores prácticas desarrolladas por un equipo global de OEM (Fabricantes de equipos originales) y las pymes de primer nivel (expertos en la materia). Combina las metodologías de AIAG (Grupo de acción de la industria automotriz) y VDA (Asociación Alemana de la Industria Automotriz) en un enfoque más estructurado.
Estos son los pasos del proceso del FMEA según el manual AIAG-VGA:
- Paso 1: Planificación y preparación
- Paso 2: Análisis de estructura
- Paso 3: Análisis de funciones
- Paso 4: Análisis de fallos
- Paso 5: Análisis de riesgos
- Paso 6: Optimización
- Paso 7: Resultados y documentación
¿Qué modo de fallo debe priorizar?
El paso 5 del proceso DFMEA y PFMEA le permite determinar los modos de falla que debe abordar primero. Puede priorizar los modos de falla en función de la gravedad, la frecuencia y la facilidad con la que puede detectar los modos de falla.
Debes proporcionar una calificación para los siguientes factores durante el FMEA:
- Gravedad: ¿Qué tan grave será el impacto de la falla del sistema o la máquina?
- Detección: ¿Qué probabilidades hay de que se detecte la falla cuando se convierta en una posibilidad?
- Ocurrencias: ¿Cuál es la probabilidad de que se produzca una falla en un período de tiempo determinado?
- Seguridad: ¿Cuál es el riesgo para las personas y los sistemas si el sistema o la maquinaria fallan?
- Número de prioridad de riesgo (RPN): el RPN se calcula en función de la gravedad, las ocurrencias y la detección.RPN = gravedad x ocurrencias x detección Es deseable un RPN más bajo. Un RPN alto indica un riesgo alto.
Una vez que haya enumerado los modos de falla y asignado una clasificación, debe enumerar la posible causa de falla para cada modo de falla (utilizando técnicas como análisis de causa raíz). Luego, debe determinar una acción correctiva para minimizar el impacto de un modo de falla en función de su RPN.
Cuándo usar PFMEA y DFMEA
Puede utilizar PFMEA o DFMEA en las siguientes situaciones:
- Está a punto de desarrollar planes de control para un proceso
- Cuando aplicas un producto existente o proceso diferentemente
- Antes de introducir un nuevo producto, proceso, paso, método o tecnología
- Antes de implementar un proceso de fabricación rediseñado
- Durante el proceso como control de calidad herramienta
- Al analizar las fallas de un proceso o producto existente
Recopile datos para mejorar la precisión de DFMEA y PFMEA
UN CMMS (sistema de gestión de mantenimiento computarizado) puede ayudar a recopilar los datos necesarios para mejorar la precisión del FMEA. Entre los ejemplos del tipo de datos que el CMMS puede recopilar se incluyen avería del equipo historia, tiempo de inactividad el historial y el costo de reparar un activo cada vez que falló en el pasado.
Estos datos pueden proporcionar información valiosa a la hora de evaluar y revisar los modos de fallo. Además de recopilar datos, un CMMS agiliza los procesos de mantenimiento y reduce el riesgo de fallas. Con MaintainX, puede realizar un seguimiento de los activos, emitir órdenes de trabajo y colaborar mediante la opción de chat integrada.
Si desea utilizar el FMEA en sus instalaciones, prueba MaintainX hoy.
FAQs
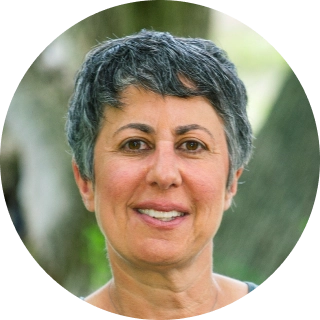
Caroline Eisner es escritora y editora con experiencia en los sectores con y sin fines de lucro, el gobierno, la educación y las organizaciones financieras. Ha ocupado puestos de liderazgo en instituciones de educación primaria y secundaria y ha dirigido proyectos digitales a gran escala, sitios web interactivos y una consultoría de redacción empresarial.