Karn Custom Woodwork creó un exitoso programa de mantenimiento preventivo en menos de un año
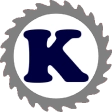
Tosca es líder mundial en envases reutilizables para alimentos y ayuda a las empresas a alejarse de los envases de un solo uso. Con 1000 empleados en 17 sedes de EE. UU., que atienden a clientes como Walmart y Kroger, la empresa administra y limpia millones de contenedores plegables, contenedores a granel y palés como parte de su objetivo de eliminar el desperdicio en las cadenas de suministro de alimentos.
El equipo implementó previamente un sistema de administración de mantenimiento computarizado (CMMS) heredado para ayudar a administrar sus operaciones. Sin embargo, si bien el sistema ayudó a digitalizar sus procesos, rápidamente descubrieron que creaba más problemas de los que resolvía. «Tuvimos que dedicar mucho tiempo a trabajar en el software», afirma Lily Burkett, ingeniera de procesos de Tosca.
Al lidiar con los complicados flujos de trabajo del sistema, las dificultades para rastrear los datos y la pérdida de oportunidades de mejora, el equipo de Tosca decidió que era hora de hacer un cambio.
El CMMS anterior de Tosca generaba frustración en todo momento. «El software no era intuitivo», afirma Scott Schneider, director de ingeniería de Tosca. «La gente tardó mucho tiempo en aprender a usarlo. Incluso tenías que memorizar ciertas pulsaciones de teclado para navegar por él».
La herramienta también carecía de funcionalidad móvil, lo que limitaba el acceso del equipo de primera línea. «Todo estaba basado en un navegador», dice Lily. «Así que los técnicos de mantenimiento no podían acceder a ese sistema. Serían solo los gerentes».
Debido a esto, los gerentes de mantenimiento no podían crear y asignar automáticamente órdenes de trabajo a los técnicos. Esto significaba que cada semana, los gerentes dedicaban varias horas a imprimir, clasificar y distribuir cientos de órdenes de trabajo, horas que deberían haberse dedicado a tareas más estratégicas.
«Tenían que entregar las órdenes de trabajo a mano», recuerda Lily. Esta dependencia del papel generaba riesgos adicionales: las órdenes de trabajo podían perderse, dañarse o completarse de forma incorrecta, lo que ponía en peligro la precisión de los datos y el seguimiento del mantenimiento. «Un archivo de Excel habría sido mejor que ese sistema», afirma Lily.
El sistema anterior tampoco ofrecía una forma fiable de realizar un seguimiento de las métricas de mantenimiento y el rendimiento. «No sabíamos cómo funcionaban las plantas con los PM», afirma Lily.
Como los líderes no sabían lo que estaba sucediendo (o lo que funcionaba), no podían aprender de las experiencias pasadas. Esto significaba que no podían crear procesos de mantenimiento estandarizados para sus equipos. Como resultado, durante los períodos de inactividad, los técnicos tenían que trabajar desde cero para decidir qué hacer, lo que desperdiciaba horas en tareas infructuosas.
«Era el enfoque de la escopeta», dice Scott. «Los técnicos tenían que adivinar cuáles eran los problemas y, en muchos casos, acababan trabajando en las cosas equivocadas».
Scott sabía por experiencia que un sistema sencillo fomentaría la adopción. Por eso, al seleccionar un nuevo software, priorizó la facilidad de uso.
Al examinar las opciones, buscó un sistema simple y fácil de usar que se ajustara a los flujos de trabajo del personal de primera línea. Las funciones de MaintainX, como la gestión del mantenimiento preventivo, la funcionalidad de chat y la posibilidad de añadir fotos a las órdenes de trabajo, impresionaron a Scott.
«Cuando me di cuenta de lo fácil que era para las personas usar MaintainX, no había duda», afirma.
Junto con MaintainX equipo de implementación, Tosca inició una implementación sitio por sitio, incorporando 16 instalaciones en menos de cinco meses. A pesar de implicar la migración de activos y datos del sistema anterior, cada sitio completó su implementación en «un máximo de tres semanas por sitio», según Lily. Esto permitió a los líderes comenzar a implementar procesos de mantenimiento preventivo en los sitios en tan solo unas semanas.
Uno de los principales objetivos de Tosca al implementar MaintainX era mejorar su OEE. A pesar de empezar con unas cifras de OEE de alrededor del 55%, el equipo se fijó un ambicioso objetivo del 80% en su primer año.
«Hemos superado el 80% y estamos ahí de forma continua», afirma Scott, y atribuye esto a la combinación de MaintainX y el sistema de informes internos de Tosca. «Gracias a MaintainX, podemos ver de dónde proviene el tiempo de inactividad, qué equipo nos causa más problemas y saber dónde concentrarnos».
Históricamente, las averías en las plantas de Tosca requerían la participación de varios equipos, y los líderes dedicaban horas a solucionarlos.
«Si una máquina se estropeaba, necesitábamos celebrar una reunión tras otra para averiguar cómo resolver el problema», afirma Lily. «En cada reunión, teníamos que preguntarnos: ¿qué está pasando realmente aquí? ¿Cómo podemos resolver esto? ¿Cómo podemos conseguir un ingeniero allí?»
Con MaintainX, los líderes han implementado procesos estandarizados, lo que permite a las plantas gestionar los problemas de forma independiente. «Las plantas tienen los datos y los recursos para hacer ese trabajo por sí mismas», afirma Lily. «Pueden acceder a los procedimientos operativos estándar, revisar las órdenes de trabajo anteriores y saber qué hacer».
Las auditorías de seguridad alimentaria, a las que está sujeta Tosca, son mucho más fáciles con MaintainX. «En el pasado, la gente utilizaba los correos electrónicos para mostrarle a un auditor que teníamos un sistema de gestión privada», afirma Scott. Ahora, con solo unos pocos clics, el equipo puede obtener datos históricos para demostrar el cumplimiento.
La funcionalidad móvil de MaintainX también permite al equipo acceder a información crucial sobre la marcha. «Ha habido varias ocasiones en las que he estado fuera de la oficina y alguien me ha pedido datos para respaldar una auditoría», afirma Lily. «Todo lo que tengo que hacer es ir a MaintainX y acceder fácilmente a la información».
Tosca ya está tomando medidas para obtener aún más valor de MaintainX. Por ejemplo, el equipo ha comenzado a integrar MaintainX con su sistema ERP Microsoft Dynamics 365 para optimizar la gestión del inventario de piezas.
«Si alguien comprueba algo en MaintainX, se actualiza automáticamente en nuestro sistema ERP», afirma Lily, explicando cómo esta función ya facilita la vida de los trabajadores de primera línea de Tosca. Y este es solo el primer paso. A medida que Tosca integre completamente MaintainX con el ERP de Dynamics 365 en todas las instalaciones, podrá eliminar la doble entrada, reducir los errores y ofrecer a los equipos una visibilidad en tiempo real de la disponibilidad de las piezas. «Nuestras plantas están muy entusiasmadas con eso», afirma Lily.
Con estas integraciones (y más) en el horizonte, Tosca está posicionada para continuar transformando sus operaciones de mantenimiento y establecer nuevos estándares en la industria de los envases reutilizables.
Logra más con MaintainX