Tosca Improves Overall Equipment Effectiveness by 25 Percentage Points with MaintainX
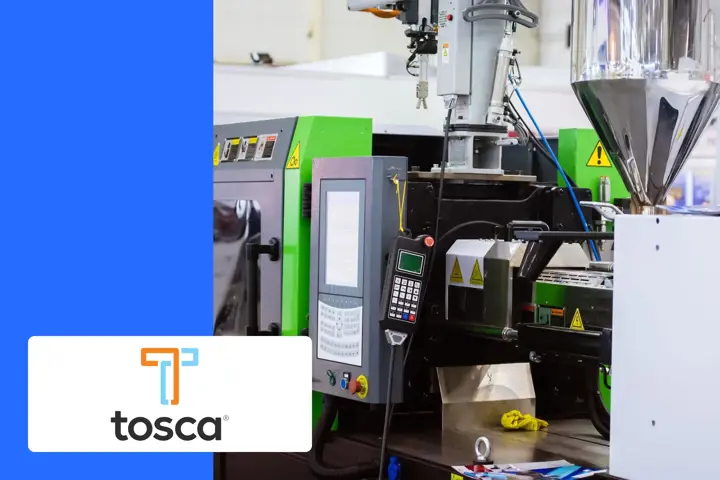
Tosca is a global leader in reusable food packaging, helping companies move away from single-use containers. With 1,000 employees across 17 US sites—serving customers like Walmart and Kroger—the company manages and cleans millions of collapsible containers, bulk bins, and pallets as part of its goal to eliminate waste in food supply chains.
The team previously implemented a legacy computerized maintenance management system (CMMS) to help manage their operations. However, while the system helped digitize their processes, they quickly discovered it created more problems than it solved. “We had to spend a lot of time just working on the software,” says Lily Burkett, Process Engineer at Tosca.
Dealing with the system’s convoluted workflows, difficulties tracking data, and lost opportunities for improvement, the Tosca team decided it was time for a change.
Challenges
A difficult-to-use system
Tosca's previous CMMS delivered frustration at every turn. “The software wasn't intuitive,” says Scott Schneider, Director of Engineering at Tosca. “It took a long time for people to learn how to use. You even had to memorize certain keystrokes to navigate it.”
The tool also lacked mobile functionality, which limited the frontline team’s access. “It was all browser-based,” says Lily. “So the maintenance techs couldn’t get into that system. It would just be the managers.”
Because of this, maintenance managers couldn’t automatically create and assign work orders to technicians. That meant every week, managers spent several hours printing, sorting, and distributing hundreds of work orders—hours that should have been spent on more strategic tasks.
“They had to pass work orders out by hand,” Lily recalls. This reliance on paper created additional risks—work orders could be lost, damaged, or filled out incorrectly, compromising data accuracy and maintenance tracking. “An Excel file would have been better than that system,” says Lily.
Missed insights and poor standardization
The previous system also didn’t offer a dependable way to track maintenance metrics and performance. “We didn't know how plants were performing with PMs,” says Lily.
Because leadership didn’t know what was happening (or working), they couldn’t learn from past experiences. This meant they couldn’t create standardized maintenance processes for their teams. As a result, during downtime events, technicians would have to work from scratch to figure out what to do, wasting hours on fruitless tasks.
“It was the shotgun approach,” says Scott. “Technicians had to guess what the issues were—and in many cases, they would end up working on the wrong things.”
Choosing MaintainX
Scott knew from experience that a straightforward system would encourage adoption. So, when selecting a new software, he prioritized ease of use.
When vetting options, he looked for a simple, user-friendly system that would fit the frontline staff’s workflows. MaintainX’s features—such as preventive maintenance management, chat functionality, and the ability to add photos to work orders—impressed Scott.
“Once I saw how easy it was for people to use MaintainX, there was no question,” he says.
Results: 25 percentage point increase in Overall Equipment Effectiveness (OEE)
Three-week implementation per site
Together with MaintainX’s implementation team, Tosca initiated a site-by-site implementation, onboarding 16 facilities in under five months. Despite involving asset and data migration from the previous system, each site completed its implementation in “three weeks max per site,” according to Lily. This allowed leadership to begin implementing preventive maintenance processes at sites in just a few weeks.
Boosting Overall Equipment Effectiveness (OEE)
One of Tosca’s main goals when implementing MaintainX was to improve their OEE. Despite starting with OEE numbers around 55%, the team set an ambitious target of 80% in their first year.
“We've gone above 80%, and we’re there continuously,” says Scott, crediting this to the combination of MaintainX and Tosca’s internal reporting system. “Because of MaintainX, we're able to see where the downtime is coming from, which piece of equipment is giving us the most trouble, and know where to focus.”
Streamlined work processes
Historically, breakdowns at Tosca plants required several teams to get involved, and leadership would spend hours troubleshooting.
“If a machine broke down, we needed to have meeting after meeting to figure out how to solve the problem,” says Lily. “In each meeting, we had to ask: What’s really going on here? How do we solve this? How do we get an engineer there?”
With MaintainX, leaders have implemented standardized processes, empowering plants to handle problems independently. “The plants have the data and the resources to do that work themselves,” says Lily. “They can access SOPs, look at past work orders, and know what to do.”
Seamless audits
Food safety audits—which Tosca is subject to—are significantly easier with MaintainX. “In the past, people would use e-mails to show an auditor that we had a PM system,” says Scott. Now, with just a few clicks, the team can pull up historical data to demonstrate compliance.
MaintainX’s mobile functionality also enables the team to access crucial information on the go. “There have been a handful of times I’ve been away from the office, and someone has asked me for data to support an audit,” Lily says. “All I have to do is go into MaintainX and easily pull up the information.”
Tosca's next move: Finish integrating Microsoft Dynamics 365 ERP with MaintainX
Tosca is already taking steps to unlock even more value from MaintainX. For example, the team has begun integrating MaintainX with their Microsoft Dynamics 365 ERP system to optimize parts inventory management.
"If someone checks something out in MaintainX, it automatically updates in our ERP system," Lily says, explaining how this feature is already making life easier for Tosca’s frontline workers. And this is only step one. As Tosca fully integrates MaintainX with the Dynamics 365 ERP across all facilities, they’ll be able to eliminate double-entry, reduce errors, and give teams real-time visibility into parts availability. “Our plants are really excited about that,” says Lily.
With these integrations—and more—on the horizon, Tosca is positioned to continue transforming its maintenance operations and set new standards in the reusable packaging industry.
See MaintainX in action
Get more done with MaintainX
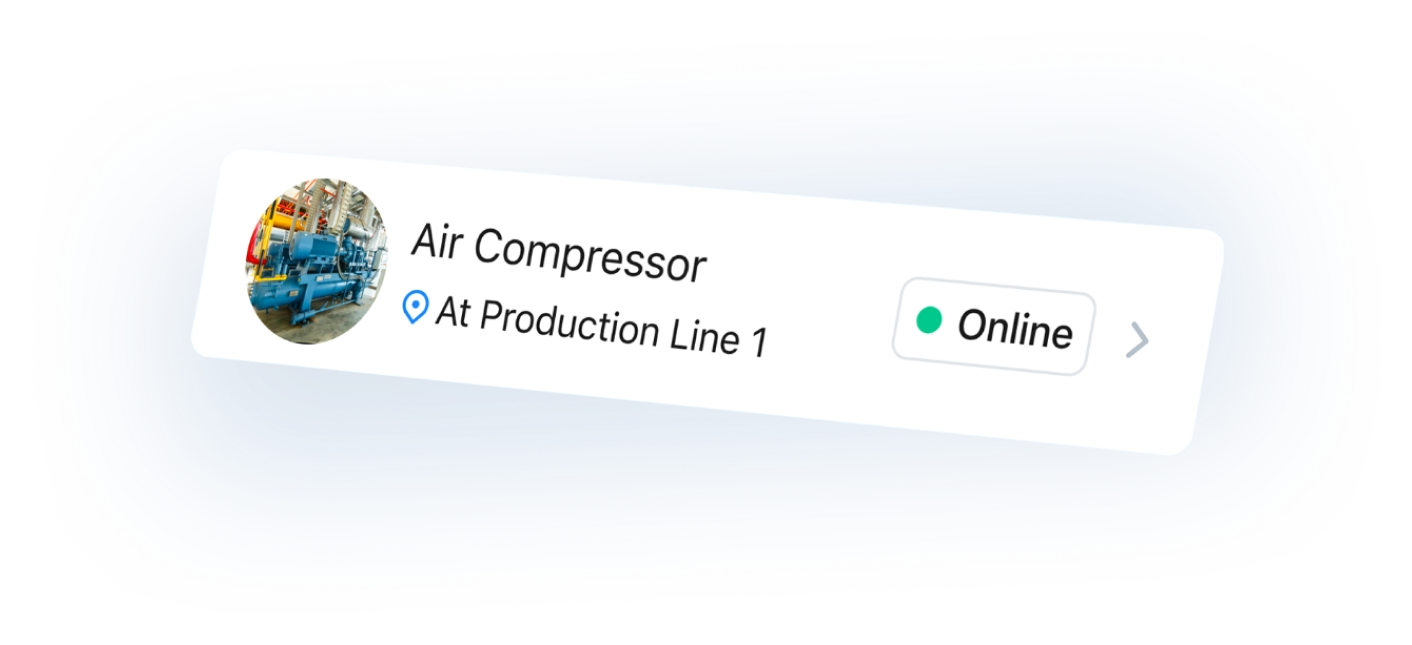
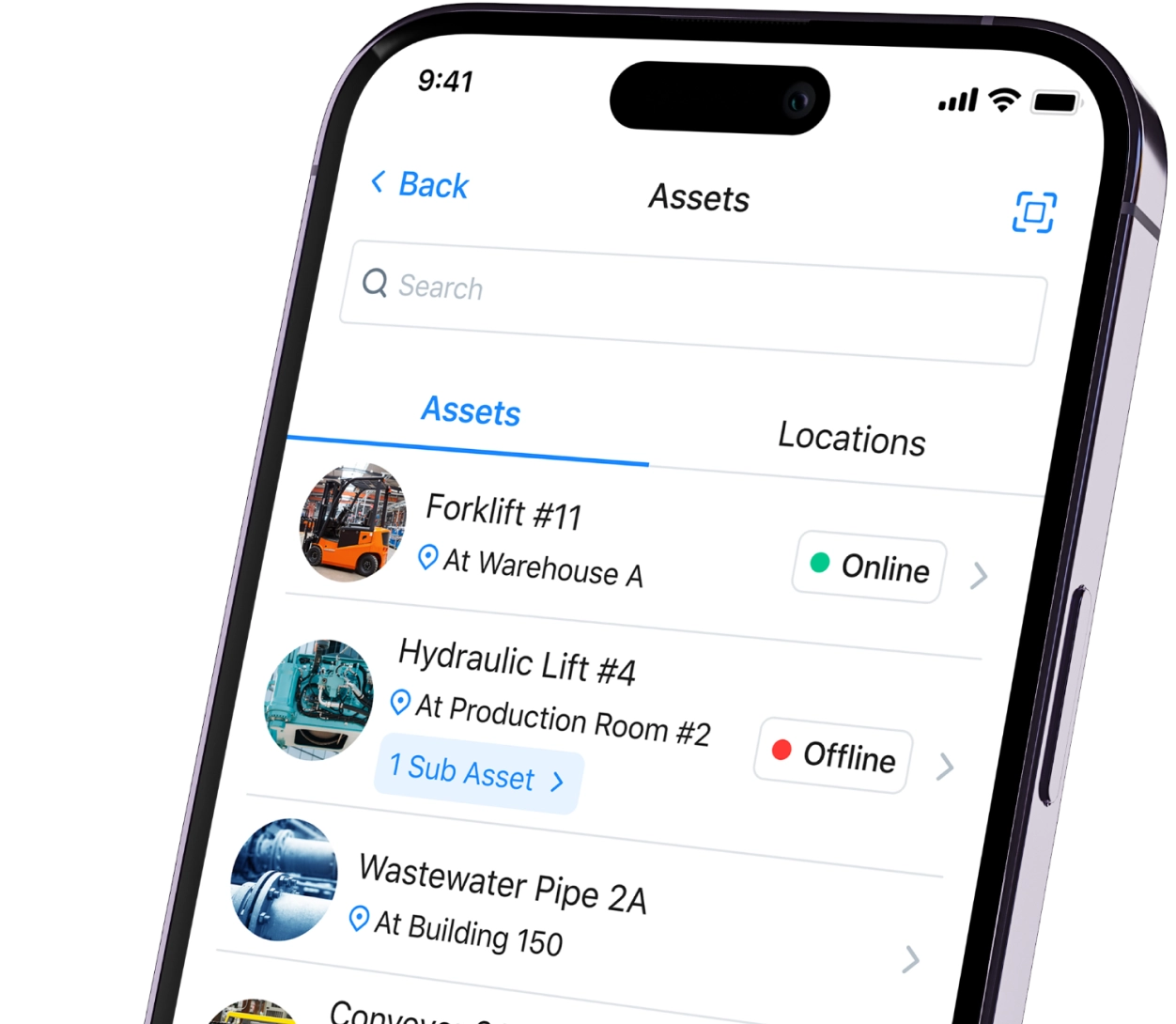