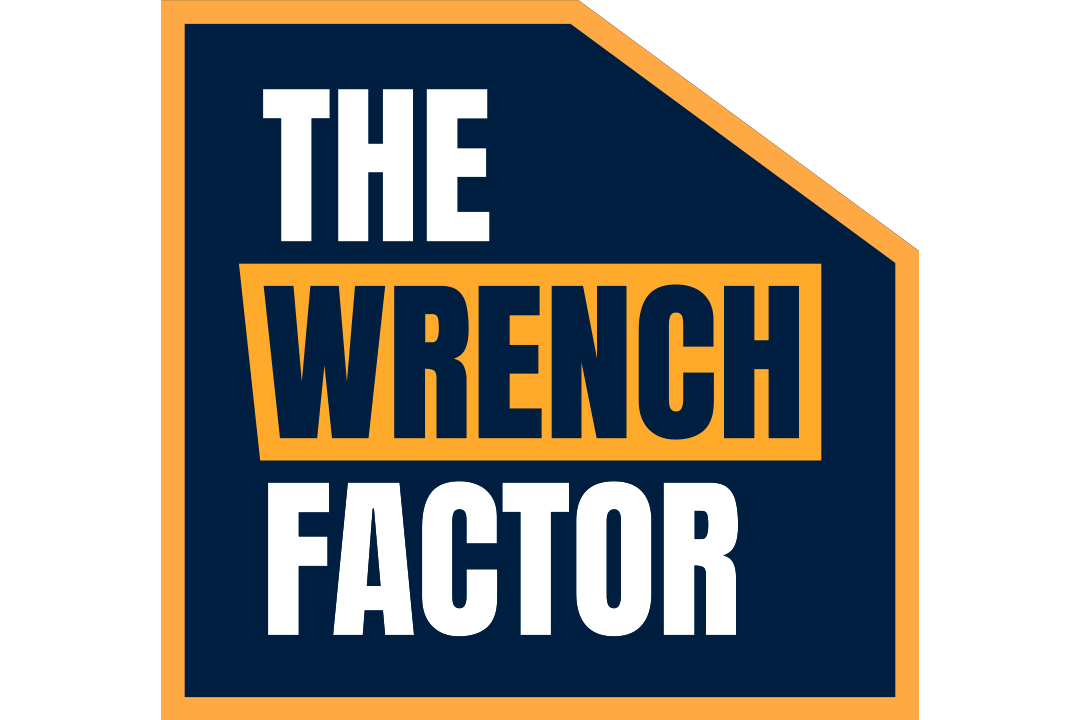
By introducing unique points of view and challenging conventional practices, women are transforming industrial operations.
As a senior operations leader in chemical manufacturing, Shari Patrick observes women embracing technological change, particularly in data science and automation. Kate Schifani, a senior director of mountain operations, notes that a willingness to envision different futures and push boundaries is key to maintenance innovation.
We had the privilege of featuring these two operations leaders on our podcast, The Wrench Factor. Read on or watch the podcast below to get their perspectives on ways the industry can shift toward more innovative thinking and technological adoption.
Forging unique paths in industrial operations
Both our guests share fascinating journeys to their leadership roles in maintenance-intensive industries. Kate's career began at the Air Force Academy, where a summer experience on the flight line sparked her passion for aircraft maintenance. Hands-on work launching and fixing jets translated perfectly to ski resort operations after her military service. Her twelve-year mountain operations career now spans lift maintenance, snow making, and safety operations at Keystone Resort.
Shari’s path began with early STEM activities in middle school during the late 80s, when such opportunities for young women were scarce. Her persistence led to a chemical engineering degree from Georgia Tech, followed by 15 years at DuPont before expanding her horizons in manufacturing. She's thrived in this environment for nearly three decades, drawn to the fast pace, variability, and complex problem-solving opportunities.
Driving success through metrics
Both leaders highlight how they've used data and KPIs to transform their operations and create cultural change within their teams.
Shari aligned her team with daily performance discussions. By establishing clear metrics for each role—from equipment downtime for operators to repair completion times for maintenance teams—she empowered employees to take ownership of their contributions to overall success. This approach created a clear escalation path when issues arose, ensuring problems were addressed at the appropriate level.
Kate revolutionized her resort's snowmaking operations by questioning traditional output-based measurements. Rather than simply maximizing production volume, she worked with her team to map out an ideal season that prioritized snow placement in the right locations at the right time. This strategic shift led to their most successful seasons on record, demonstrating how rethinking key performance indicators can drive both operational excellence and cultural transformation.
Uniting teams with technology
Technology plays a crucial role in transforming industrial operations—it has the power to unite maintenance and operations teams that have traditionally existed in separate silos.
This divide is a persistent challenge for Kate. Operations uses the equipment while maintenance fixes it, often creating friction between teams. But she now sees modern technology platforms like MaintainX bridging this gap by creating shared ownership and accountability for asset success. When both teams can access the same information and align to the same goals, collaboration naturally improves.
In the chemical industry, Shari sees automation transforming data collection and decision-making processes. With automated systems for downtime reporting, quality deviation notifications, and environmental monitoring, teams can respond faster. And thanks to collaborative platforms, everyone can gain insights simultaneously.
Inspiring the next generation
A critical challenge facing industrial sectors is attracting new talent, particularly as digital natives enter the workforce with different technological expectations.
During a recent school visit, Shari observed classrooms where every student had an iPad, highlighting the stark contrast between educational environments and traditional industrial workplaces. This generation has grown up with intuitive digital tools and expects similar experiences in their professional lives.
Both leaders emphasized that modernizing industrial workplaces isn't about abandoning hands-on work, it's about enhancing it. Many young people still enjoy building and creating things, but they expect modern tools to support these activities. By incorporating familiar tech into maintenance workflows, organizations can attract talent that might otherwise overlook these career paths.
Looking to the future
Kate envisions a future where technology helps remove barriers to entry in industrial careers, making these fields more accessible to diverse candidates. In her own industry, where women in mountain operations are relatively rare, technological advancement could accelerate progress toward gender parity by creating new pathways for involvement.
Shari anticipates a significant digital transformation in chemical manufacturing, moving facilities from outdated 80s-era systems to modern interfaces that match everyday consumer experiences. This evolution will help close the STEM talent gap by creating environments where younger workers can apply their natural technological aptitude to solve complex industrial challenges in innovative ways.
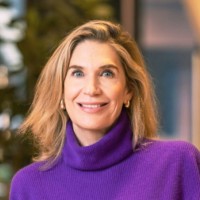
Directora de Comunicaciones Corporativas