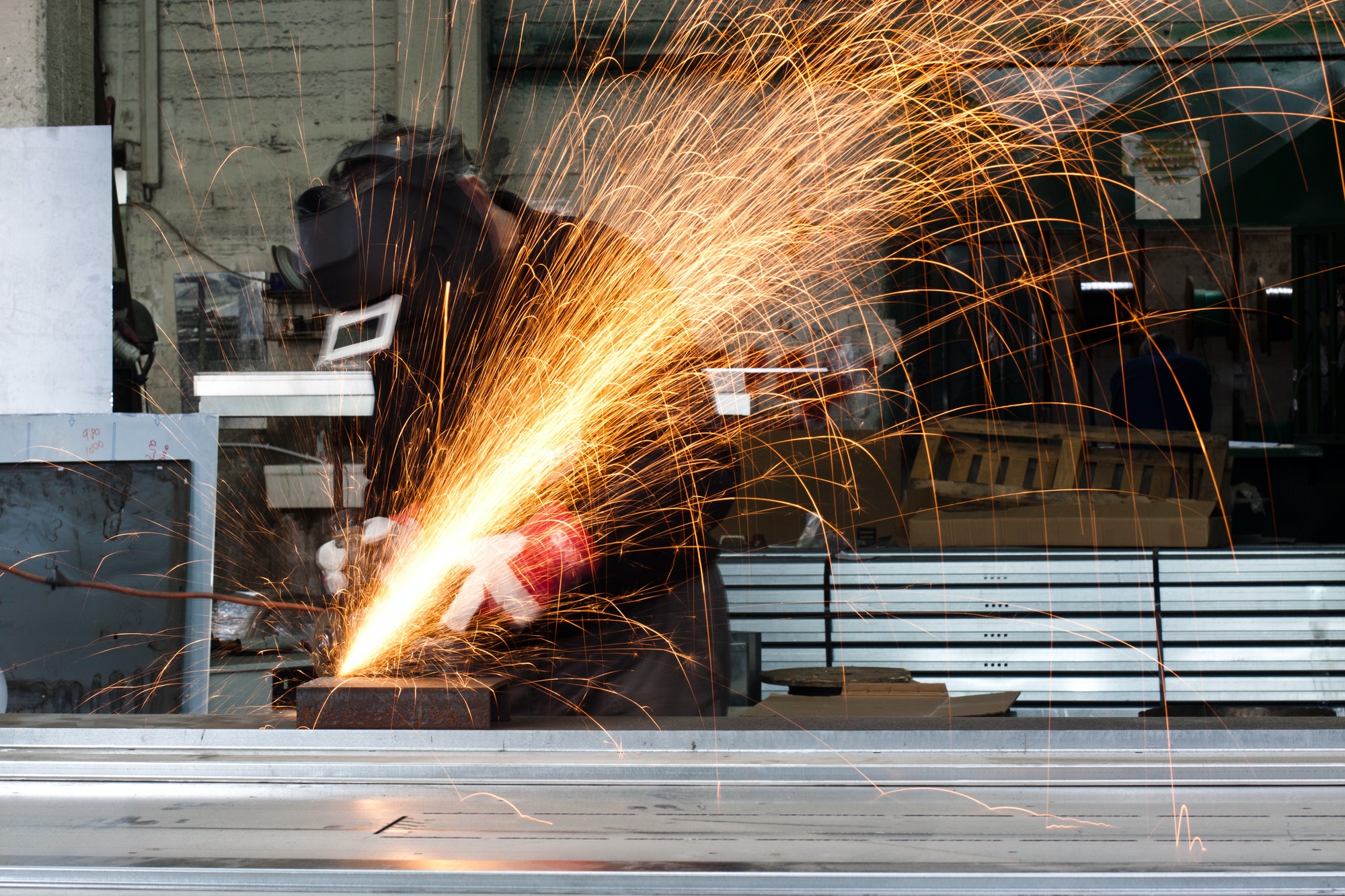
Todos los equipos comerciales, desde una freidora en una cocina comercial hasta una cinta transportadora en una planta de fabricación, eventualmente fallarán. Si bien un plan de mantenimiento proactivo puede mitigar algunas fallas, averías inesperadas aún puede ocurrir, paralizando la producción, distrayendo a los técnicos de las tareas rutinarias de mantenimiento preventivo y costando mucho dinero a su organización.
Por estas razones, O&M (operación y mantenimiento) los gerentes deben tomar medidas proactivas para mantener la maquinaria funcionando de manera óptima, y entender por qué fallan los equipos es el primer paso para gestionar el tiempo de inactividad imprevisto.
Afortunadamente, si utiliza sistemas de gestión de mantenimiento sólidos, emplea técnicos cualificados y aprovecha las tecnologías y el software conectados, puede reducir considerablemente las consecuencias de las fallas de los equipos en su organización.
En este artículo, analizaremos las cuatro causas más comunes de fallas en los equipos y cómo prevenirlas. La realidad es que probablemente no podrá eliminar las fallas al 100 por ciento, pero sabrá cómo empezar a reducir su incidencia y su impacto en las operaciones.
¿Qué es una falla en el equipo?
Antes de profundizar en las causas de las fallas en los equipos, hablemos de qué se trata.
Fallo del equipo es una condición en la que un activo o una máquina no funciona como debería, es decir, algo está roto. Las fallas inesperadas pueden tener un impacto significativo en los cronogramas de producción, los niveles de satisfacción del cliente y la calidad del producto.
La falla del equipo es más costosa de lo que cree
Si bien la pérdida de tiempo de producción es el problema más obvio, las consecuencias de una falla en el equipo son de gran alcance:
- El costo de las horas extras no planificadas para los técnicos
- Costos de inactividad para los operadores de máquinas
- El aumento del costo del envío urgente de piezas de repuesto de los proveedores
- Materias primas desperdiciadas, como ingredientes de producción de alimentos perecidos que deben desecharse
- Productos defectuosos o un fuerte aumento de las fallas de control de calidad cuando el equipo tiene un rendimiento inferior
- Reducción de los niveles de satisfacción de los clientes y de la percepción de la calidad
- Pérdida de negocios por no cumplir con los objetivos de DIFOT o las fechas prometidas
- Coste de oportunidad debido al exceso de recursos que se centran en la reparación del activo
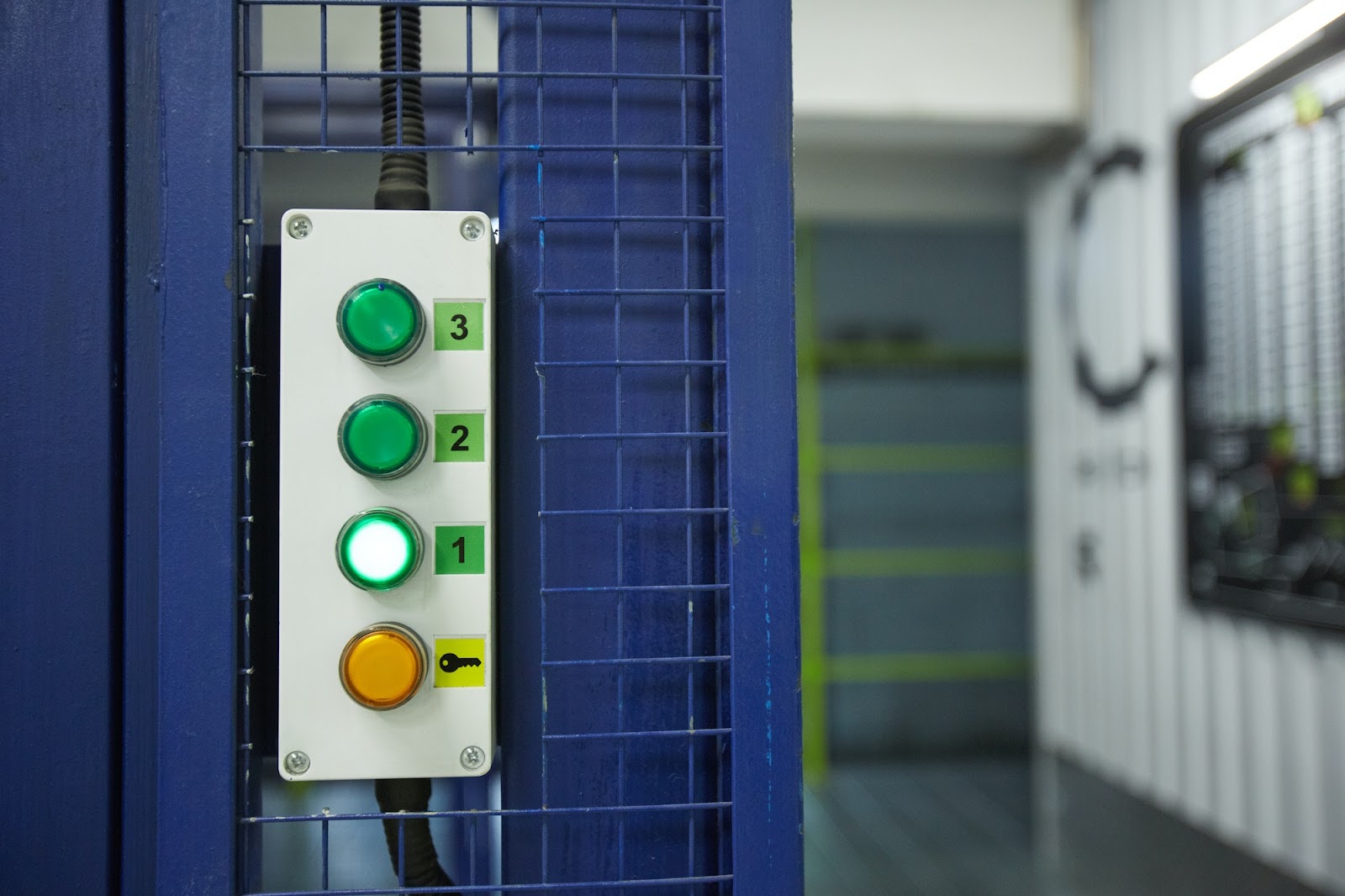
3 tipos de equipos que fallan
Independientemente de la industria (agrícola, manufacturera, de almacenamiento, de energía y gas o de servicio de alimentos), los equipos pueden fallar en todos los tipos de activos. Los fallos en cualquiera de estas categorías pueden tener un gran impacto en las operaciones:
- Equipo motorizado: Estas máquinas dependen de motores eléctricos o de combustible para funcionar. También conocida como equipo pesado, esta categoría incluye excavadoras, grúas y montacargas.
- Equipo mecánico: Los equipos mecánicos suelen incluir componentes móviles que trabajan juntos para realizar una tarea específica. Las unidades de refrigeración, los condensadores, las extrusoras, las cintas transportadoras y los compresores de aire son ejemplos de equipos mecánicos.
- Equipos no mecánicos: Los equipos no mecánicos son generalmente más pequeños y carecen de partes móviles. La mayoría de las herramientas manuales entran en esta categoría, incluidas las tuberías, las líneas de gas, los paneles eléctricos y las herramientas del sistema HVAC.
Ahora, veamos las causas más frecuentes de averías en las máquinas.
Las 4 causas comunes de falla del equipo
La mayoría de los tipos de fallas en los equipos se deben a una de las cuatro razones más comunes:
- Equipo envejecido
- Error del operador
- Falta de mantenimiento preventivo
- Mantenimiento excesivo
Afortunadamente, todo esto se puede prevenir con los procesos, los procedimientos y la tecnología correctos.
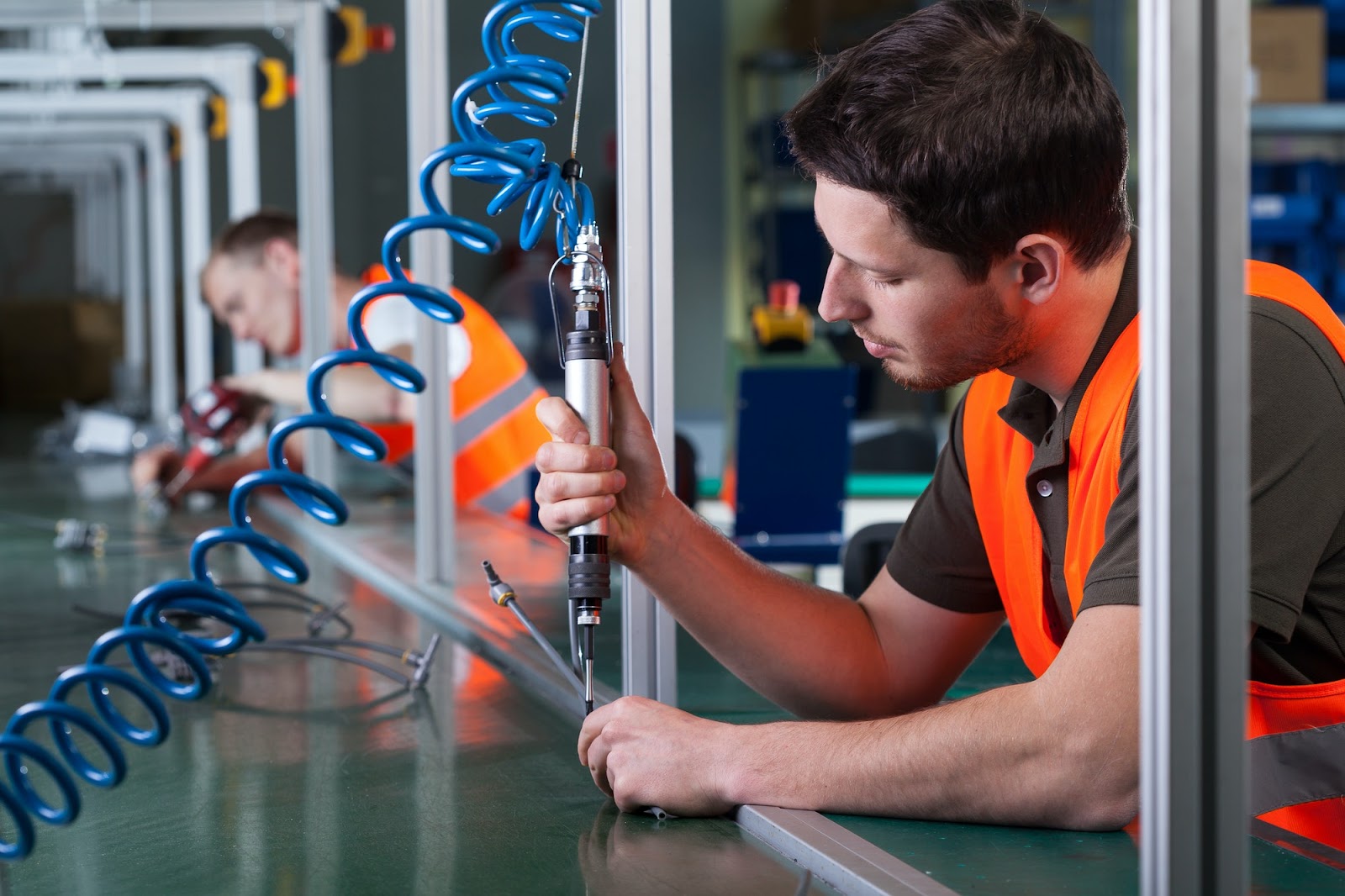
1. Equipo envejecido
Según el estudio de mantenimiento de ingeniería de planta, el envejecimiento de los equipos es la principal causa de fallas en los equipos, ya que representan el 40 por ciento de las fallas no planificadas tiempo de inactividad en las plantas.
Los activos que funcionan de manera constante año tras año requieren reparaciones más frecuentes a lo largo del tiempo.
Desafortunadamente, este deterioro natural se traduce en un mayor gasto de dinero en piezas, tarifas de envío de inventario e interrupciones de la producción. También requiere que los técnicos cambien de mantenimiento preventivo (PM) a mantenimiento reactivo más a menudo.
Además, cuanto más anticuado se vuelve un activo, más difícil es conseguir piezas de repuesto. Dado que los fabricantes suelen producir cantidades más bajas de piezas de repuesto antiguas, los administradores de equipos más antiguos suelen tener problemas para conseguir lo que necesitan cuando lo necesitan.
Por estas razones, las plantas deberían considerar la posibilidad de permitir los activos que hayan superado su vida útil a correr hasta el fracaso. Si bien la compra de maquinaria nueva es indudablemente cara, la mayoría de las organizaciones ahorrarán dinero a largo plazo al reducir los gastos de reparación, aumentar la producción y ser más eficientes gestión de piezas.
2. Error de operador
Otra causa común de fallas en los equipos es el error del operador: a veces, los operadores de las máquinas cometen errores debido a la fatiga, el olvido, la falta de experiencia o la falta de capacitación. Según el Estado del mantenimiento industrial 2024 Según un informe, el 12% de los encuestados anticipó que el error del operador sería la principal causa de tiempo de inactividad no planificado en los próximos doce meses.
La mayoría de las plantas preparan a los operadores de máquinas para operar correctamente equipos complejos con la capacitación adecuada y de fácil acceso procedimientos operativos estándar (SOP), y directrices de seguridad claras. Sin embargo, no es raro que los trabajadores trabajen de vez en cuando en máquinas desconocidas cuando sustituyen a otras.
Es posible que un operador no capacitado no tenga los conocimientos especializados necesarios para hacer funcionar la máquina con confianza. Esto podría provocar una avería en el equipo o un accidente laboral, así como una brecha Los requisitos de formación de operadores de la OSHA,
3. Falta de mantenimiento preventivo
Hay una razón por la que los programas de mantenimiento de equipos de primera clase practican predominantemente el mantenimiento preventivo: se ha demostrado que reduce el costoso tiempo de inactividad de los equipos. Los estudios sugieren que los programas de mantenimiento preventivo pueden reducir las fallas de los equipos en la misma medida 45 por ciento.
Sin embargo, muchos gerentes siguen bajo el adagio: «Si no está roto, no lo arregles».
Si bien el mantenimiento continuo hasta el fallo suele ser la estrategia ideal para los equipos más antiguos y no críticos, la falta de inspecciones planificadas puede hacer que no se detecten las primeras señales de una falla inminente y que el rendimiento disminuya.
Mantenimiento continuo frente a mantenimiento preventivo
El mantenimiento continuo es una estrategia de mantenimiento en la que las actividades de mantenimiento se realizan después de que se produce una falla. Es una estrategia reactiva que permite que un activo se descomponga antes de decidir si se debe reparar o reemplazar.
También denominado»mantenimiento de averías», esta estrategia es la más adecuada para los activos no críticos, los activos económicos y aquellos con una vida útil más corta. También se usa a veces para equipos remotos, como satélites, a los que es difícil realizar un mantenimiento regular.
Sin embargo, el mantenimiento continuo hasta la falla nunca debe usarse para activos críticos que afecten la producción y la seguridad.
El enfoque alternativo:mantenimiento preventivo (PM)—implica programar y realizar el mantenimiento recomendado de acuerdo con el tiempo o los intervalos basados en el uso. Es una estrategia proactiva que se adapta mejor a equipos costosos, activos críticos y componentes que son esenciales para la seguridad de los empleados.
En última instancia, las organizaciones que se dedican exclusivamente a correr hasta el fracaso pierden la oportunidad de resolver problemas menores antes de que se conviertan en grandes problemas. Además, las tareas de mantenimiento incumplidas o retrasadas con frecuencia, como la lubricación periódica de las piezas de los equipos, pueden reducir la vida útil de un activo y provocar la necesidad de nuevas compras de capital.
4. Mantenimiento excesivo
Puede parecer contradictorio, pero realizar un mantenimiento excesivo también puede ser perjudicial.
El mantenimiento excesivo puede acelerar la depreciación de un activo al desarmar y reconfigurar constantemente los componentes del equipo. Este enfoque exagerado puede perturbar incluso los sistemas más estables y hacer que pierdan eficacia.
Además, es más probable que los técnicos de mantenimiento «sigan las instrucciones» y vean las tareas frecuentes como un elemento más que hay que comprobar.
El mantenimiento excesivo también consume un tiempo innecesario que los técnicos podrían utilizar mejor en otros equipos.
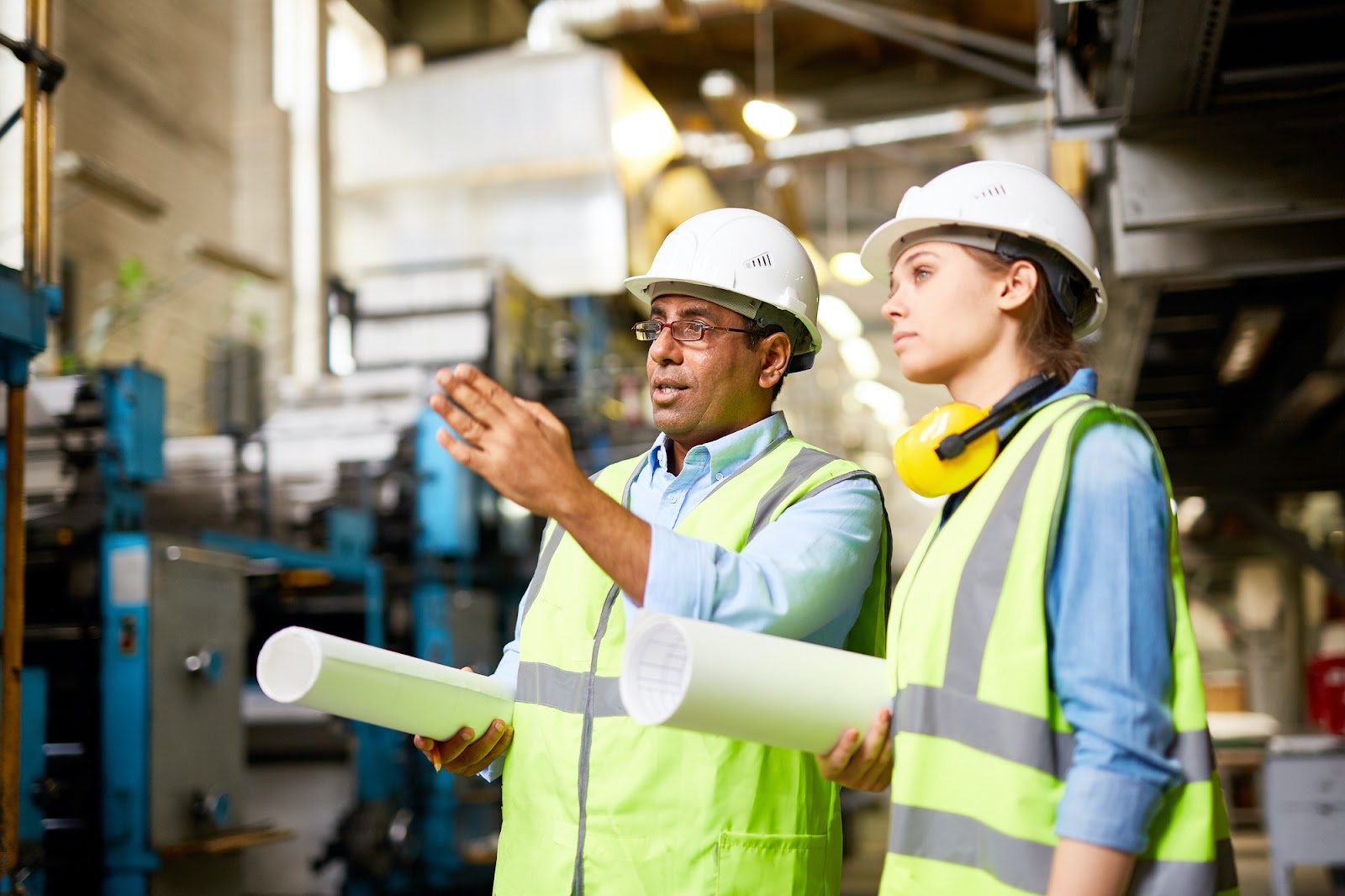
5 maneras de prevenir fallas en los equipos
Como se mencionó anteriormente, la falla del equipo puede ser extremadamente costoso, según la industria. El Estado del mantenimiento industrial 2024 descubrió que «en 2024, el costo promedio de una hora de inactividad no planificada ronda los 25 000 USD y puede alcanzar los 500 000 USD en el caso de las organizaciones más grandes».
Ya sea que una falla del equipo sea gradual, intermitente o repentina, por lo general se puede rastrear hasta una causa raíz. Descubrir la «caída del dominó» original debería ser el objetivo final de todo gerente que desee aumentar la confiabilidad operativa y reducir los costosos tiempos de inactividad.
Los gerentes de mantenimiento pueden usar una variedad de métodos de análisis para ayudar a identificar las causas fundamentales. Los 5 porqués, diagramas de espina de pescado, y análisis de causa raíz son solo algunas de las técnicas deductivas que se utilizan comúnmente en mantenimiento industrial departamentos.
Sin embargo, encontrar la causa raíz es solo una parte de la solución. Estos son algunos consejos sobre cómo prevenir las fallas en los equipos para minimizar el impacto en su organización y en sus resultados.
Proporcione una formación exhaustiva a los operadores y mantenga el cumplimiento
Garantizar que los operadores de los equipos reciban la capacitación adecuada puede ayudar a minimizar las fallas que se derivan de un error humano. Los gerentes también deben incorporar la redundancia en sus operaciones capacitando a los trabajadores sobre cómo usar máquinas que normalmente no utilizan. De esa manera, siempre estará disponible alguien que haya recibido la capacitación adecuada de acuerdo con las normas de la OSHA.
Del mismo modo, la administración debe hacer cumplir estrictamente las políticas que impiden que los empleados no capacitados operen maquinaria.
Supervise y analice el equipo digitalmente
La supervisión del estado de los activos y el aseguramiento contra fallos resulta mucho más fácil cuando se invierte en sistemas conectados y preparados para el IoT. Al conectar los medidores y sensores de los equipos a su sistema computarizado de gestión del mantenimiento (CMMS), puede automatizar el seguimiento de los activos y obtener una visión de alto nivel de todos sus activos en un único panel de control.
Este monitoreo remoto del estado permite a su organización aprovechar el ahorro de tiempo y costos mediante la detección temprana de condiciones operativas inusuales antes de que un activo se estropee.
Equilibre el mantenimiento preventivo con el basado en el estado
Las actividades regulares de mantenimiento preventivo (PM) ayudan a prevenir fallos y a prolongar la vida útil de los activos. Por otro lado, mantenimiento basado en el estado (CBM) permite realizar ajustes oportunos en función de las condiciones de los activos (y antes de que se produzca una falla).
La ejecución simultánea de los programas de PM y CBM requiere una base de datos sólida que garantice que todos los equipos reciban la cantidad exacta de atención que necesitan en el momento adecuado. Un sistema de gestión del mantenimiento computarizado (CMMS) compatible con dispositivos móviles, como MaintainX, proporciona información, programación, gestión de datos y seguimiento de activos basados en inteligencia artificial para que los administradores de mantenimiento tengan una visión integral de su programa de mantenimiento.
Adjunte los SOP a las órdenes de trabajo
Los procedimientos operativos estándar (SOP) garantizan que el equipo reciba el mantenimiento y el mantenimiento adecuados de la misma manera en todo momento.
Al asignar las órdenes de trabajo a los técnicos con un SOP previamente preparado, los gerentes de mantenimiento pueden asegurarse de que las reparaciones, el reemplazo de piezas y otras tareas de mantenimiento se lleven a cabo de manera efectiva para reducir la aparición de futuras averías.
Realice inspecciones de mantenimiento de rutina
Los procedimientos operativos estándar y las listas de verificación también son vitales para las actividades de mantenimiento rutinario y la gestión eficaz de los activos. Las listas de verificación creadas en MaintainX ayudan a los técnicos a realizar inspecciones rutinarias con facilidad, además de crear un «registro documental» para que los gerentes de mantenimiento analicen el estado de los activos y detecten las primeras evidencias de anomalías, todo ello desde la comodidad de una aplicación.
Ahorre tiempo y dinero con MaintainX
No siempre se puede superar la falla del equipo, pero se puede minimizar su impacto. El CMMS de MaintainX puede ayudar a que su equipo de mantenimiento vaya un paso por delante de las incómodas averías y a que las máquinas vuelvan a estar en funcionamiento rápidamente cuando se produzcan fallos.
MaintainX ayuda a su organización a mitigar las costosas fallas de los equipos con herramientas y sistemas para administrar el mantenimiento proactivo y reactivo. Minimice el tiempo de inactividad y maximice la productividad con un CMMS fácil de usar que le permite monitorear el estado de los activos en tiempo real, asignar órdenes de trabajo con rapidez y rastrear el historial de los equipos para anticiparse a los problemas.
Equipment failure FAQs
¿Cuánto tiempo lleva implementar MaintainX?
Para el cliente promedio, la implementación de un sitio lleva tres semanas. Para los clientes de nuestros planes Premium y Enterprise, nuestro equipo garantiza una transición sin problemas a MaintainX dentro de su organización. Asóciese con un especialista en implementación dedicado a través de nuestro proceso de incorporación estructurado de tres semanas. Obtenga más información sobre nuestros servicios de implementación aquí.
¿MaintainX es seguro?
MaintainX cumple con estándares de seguridad, incluyendo SOC 2, ISO 27001 y GDPR. También soporta inicio de sesión único (SSO), autenticación de múltiples factores (MFA) y permisos y roles personalizados. Para más información, visita nuestra página del Centro de Confianza.
¿MaintainX soporta múltiples sitios?
Sí, MaintainX Enterprise te permite gestionar múltiples plantas o instalaciones en la misma plataforma. También puedes crear paneles de informes personalizados para rastrear KPIs en varios sitios en una sola pantalla.
¿Cuáles son las industrias más afectadas por las fallas de los equipos?
Casi todas las industrias, desde la producción de alimentos hasta la fabricación de automóviles, pueden sufrir desastrosas quiebras de activos. El sistema de refrigeración de un supermercado es fundamental para las operaciones, del mismo modo que el robot soldador de un fabricante de automóviles es vital para mantener la producción en marcha.
¿Cuáles son las señales de advertencia de una falla inminente del equipo?
Las fallas intermitentes, la degradación física, como las carcasas agrietadas, las vibraciones excesivas, las fugas de fluidos, la acumulación de contaminantes y las temperaturas inusualmente altas son señales comunes de que algo anda mal con los equipos mecánicos. Los ruidos inusuales y un aumento inesperado del tiempo de producción también pueden ser indicios tempranos de que es necesario realizar una inspección o un mantenimiento.
¿Qué debe incluirse en un plan de respuesta ante fallos del equipo?
La planificación de las fallas del equipo comienza con la seguridad, así que asegúrese de que el equipo esté aislado, bloqueado o etiquetado y de que los operadores estén al tanto de la avería. Los técnicos de reparación pueden responder con rapidez al establecer procedimientos para las averías. Los procedimientos operativos estándar deben incluir medidas para inspeccionar el equipo, un proceso de reparación claro, cómo agilizar las piezas de repuesto y cómo mitigar el impacto en la producción diaria.
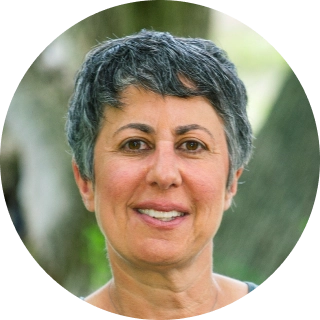
Caroline Eisner es escritora y editora con experiencia en los sectores con y sin fines de lucro, el gobierno, la educación y las organizaciones financieras. Ha ocupado puestos de liderazgo en instituciones de educación primaria y secundaria y ha dirigido proyectos digitales a gran escala, sitios web interactivos y una consultoría de redacción empresarial.