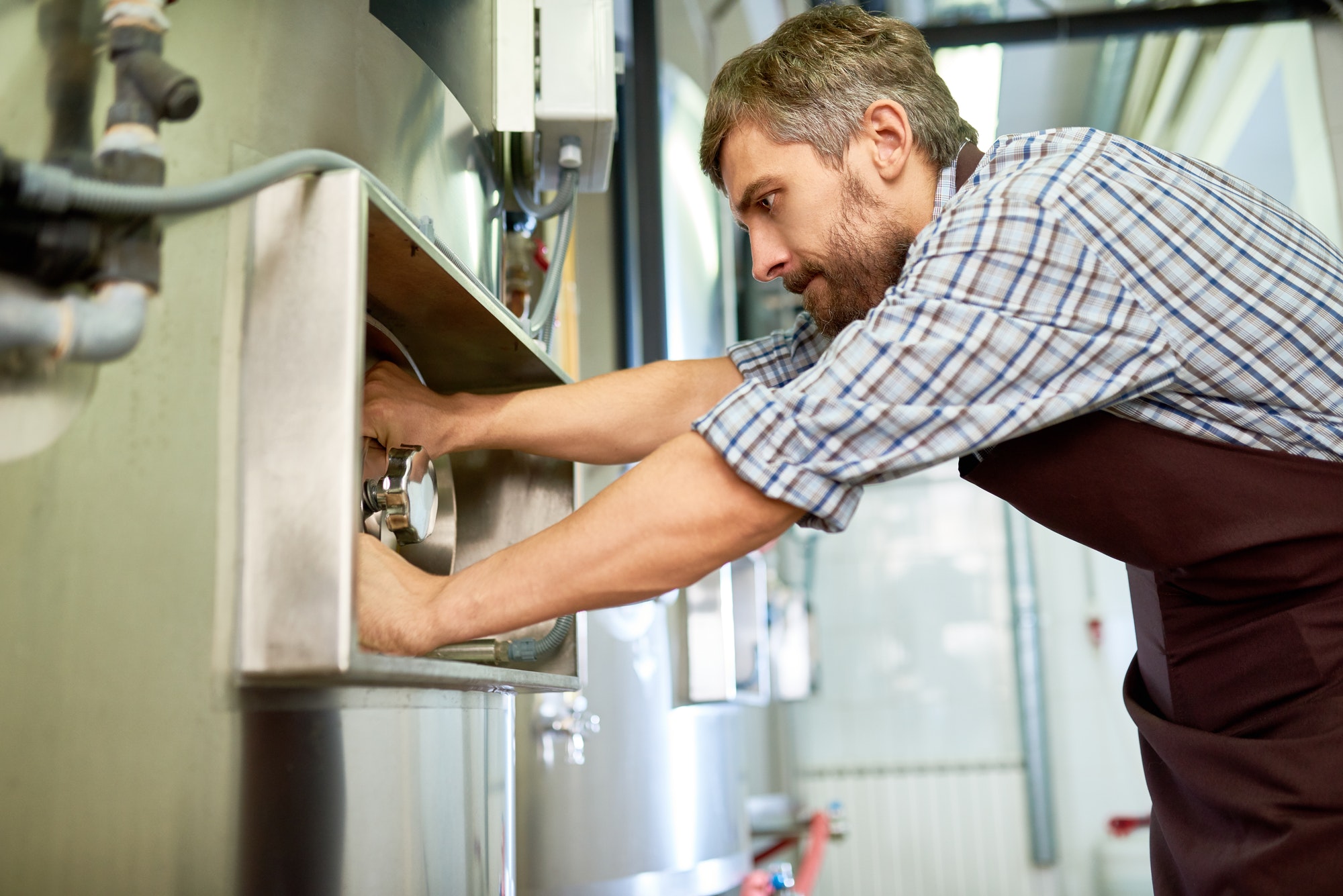
Los departamentos de mantenimiento de todos los sectores comparten un objetivo: mantener los activos operativos. Entender la diferencia entre reparación y mantenimiento repercute directamente en sus resultados finales.
Cuando el equipo falla, las consecuencias van más allá de los costos de reparación. Según Siemens El verdadero costo del tiempo de inactividad en 2024 informe, el tiempo de inactividad no planificado cuesta a las 500 empresas más grandes del mundo 1,4 billones de dólares al año, lo que representa el 11% de sus ingresos. En la fabricación de automóviles, cada hora de inactividad cuesta 2,3 millones de dólares.
El mantenimiento preserva la funcionalidad a través de las actividades planificadas, mientras que las reparaciones restauran la funcionalidad después de las fallas. Esta distinción determina si su operación se ejecuta de manera proactiva o reactiva, lo que influye en la vida útil del equipo, la confiabilidad, las mejoras de capital y los presupuestos.
Para los profesionales de mantenimiento, reconocer esta diferencia permite una mejor asignación de recursos y una planificación estratégica con menos situaciones de emergencia. Entender cuándo mantener o reparar ayuda a los equipos a equilibrar los costos con las necesidades operativas y, al mismo tiempo, a maximizar el tiempo de actividad.
Conclusiones clave
- Las reparaciones y el mantenimiento representan enfoques fundamentalmente diferentes para gestión de activos—uno reactivo, otro proactivo.
- La diferencia de costos entre las reparaciones y el mantenimiento va mucho más allá de los gastos directos, ya que el tiempo de inactividad no planificado cuesta a los principales fabricantes hasta 2,3 millones de dólares por hora en algunos sectores.
- Las organizaciones deben aspirar a una proporción de 80/20 entre el mantenimiento preventivo y las reparaciones reactivas para lograr una rentabilidad y una confiabilidad óptimas.
- Las estrategias de mantenimiento eficaces reducen el tiempo de inactividad no planificado, prolongan la vida útil de los equipos y proporcionan importantes ahorros de costos al evitar costosas reparaciones de emergencia.
- Moderna CMMS soluciones como MaintainX ayudan a las organizaciones a pasar de estrategias reactivas a proactivas mediante una mejor programación, seguimiento, comunicación y análisis de datos.
¿Cuál es la diferencia entre reparación y mantenimiento?
La reparación y el mantenimiento representan enfoques fundamentalmente diferentes para la administración de equipos. Las reparaciones reparan los activos de capital rotos, mientras que el mantenimiento evita que se produzcan averías.
Reparación: medidas tomadas para restaurar la funcionalidad después de un fallo del equipo. Las reparaciones son medidas reactivas que abordan los problemas una vez que se producen.
Mantenimiento: actividades realizadas para preservar la funcionalidad y evitar fallos. El mantenimiento es un trabajo proactivo que prolonga la vida útil de los activos y evita el tiempo de inactividad no planificado.
Las implicaciones financieras de las reparaciones en comparación con el mantenimiento van más allá del gasto inmediato de piezas y mano de obra. Cuando los equipos fallan inesperadamente, las empresas se enfrentan a:
- Primas de reparación de emergencia
- Pérdidas de producción durante el tiempo de inactividad
- Posibles incidentes de seguridad
- Depreciación a lo largo del tiempo
- Reducción de la vida útil del equipo
- Costos laborales de horas extras
Las estrategias de mantenimiento más eficaces se centran en la prevención más que en la reacción, y los expertos en mantenimiento recomiendan una proporción de 80/20 entre el mantenimiento preventivo y las reparaciones reactivas para lograr una rentabilidad y una fiabilidad óptimas.
¿Qué son las reparaciones?
Las reparaciones son acciones que se toman para restaurar la funcionalidad del equipo después de una falla o cuando se produce una avería en el equipo. De acuerdo con la Informe sobre el estado del mantenimiento industrial de MaintainX 2024, el 41% de los encuestados mencionó el deterioro de los activos como el principal factor del costoso tiempo de inactividad no planificado.
Cuándo falla el equipo, las reparaciones se hacen necesarias para que los activos vuelvan a estar operativos. A diferencia de otras operaciones de mantenimiento, las reparaciones son medidas reactivas que abordan los problemas una vez que se han producido, en lugar de prevenirlos.
Tipos de reparaciones
Reparaciones correctivas: Problemas identificados durante las inspecciones o el funcionamiento normal antes de que se produzca una falla total. Aunque siguen siendo reactivas, las reparaciones correctivas son respuestas planificadas a los problemas descubiertos, como la sustitución de un rodamiento que muestre signos de desgaste o la reparación de una cinta transportadora desalineada en una planta de fabricación.
Reparaciones de emergencia: Soluciones urgentes para fallos repentinos, completos o preventivos en los equipos que detengan la producción. Algunos ejemplos son la reparación de una línea hidráulica rota en un equipo de excavación, la sustitución de un motor averiado en un sistema HVAC o la reparación de una bomba averiada en una instalación de petróleo y gas. Las reparaciones de emergencia generalmente conllevan costos superiores y causan interrupciones operativas significativas.
Reparaciones aplazadas: Reparaciones pospuestas por problemas no críticos en los que no se requiere la atención inmediata a las reparaciones urgentes. Por ejemplo, posponer la reparación del equipo secundario de una planta de procesamiento de alimentos durante la temporada alta de producción o retrasar las reparaciones cosméticas de los accesorios de las instalaciones minoristas hasta después de los períodos de compras navideñas.
Actividades de reparación comunes
Las actividades de reparación comunes en los entornos industriales incluyen:
- Sustitución de componentes o piezas defectuosas
- Reconstrucción de conjuntos mecánicos dañados
- Abordar las fallas del sistema eléctrico
- Reparación de daños estructurales a los equipos
- Reparación de fugas en sistemas hidráulicos o neumáticos
- Restauración de equipos después de paradas de seguridad
- Solución de problemas y resolución de averías del sistema de control
- Corregir los problemas de alineación después de un fallo
- Restauración de equipos después de daños ambientales
- Reparación de componentes de transmisión de potencia dañados
A diferencia de las actividades de mantenimiento que tienen como objetivo preservar la funcionalidad, estas tareas de reparación se centran en hacer que el equipo vuelva a funcionar después de que ya se haya producido una falla.
¿Qué es el mantenimiento?
El mantenimiento se refiere al cuidado y mantenimiento sistemáticos de los activos para preservar su funcionalidad, rendimiento y seguridad durante toda su vida útil operativa. Mantenimiento adecuado prolonga la vida útil de los equipos, garantiza un rendimiento fiable y evita los costosos tiempos de inactividad no planificados.
Tipos de mantenimiento
Mantenimiento preventivo: Actividades rutinarias programadas que se realizan mientras el equipo sigue funcionando correctamente para evitar fallas. Mantenimiento preventivo incluye inspecciones periódicas, lubricación, limpieza y reemplazos de componentes según los intervalos de tiempo o las métricas de uso. Por ejemplo, programar el mantenimiento trimestral del sistema HVAC en las instalaciones de fabricación o realizar cambios de aceite periódicos en los vehículos de la flota.
Mantenimiento predictivo: Enfoque basado en datos que utiliza tecnologías de monitoreo del estado para determinar cuándo es realmente necesario el mantenimiento. Esto incluye el análisis de vibraciones, las imágenes térmicas y el análisis del aceite para detectar posibles fallos antes de que se produzcan. Algunos ejemplos son la supervisión de los patrones de vibración de los rodamientos en los equipos industriales o el seguimiento de las tendencias de consumo de energía en los sistemas de refrigeración.
Mantenimiento correctivo: Aborda los problemas identificados antes de que provoquen fallas en el equipo. Si bien es de naturaleza reactiva, mantenimiento correctivo se diferencia de las reparaciones porque se centra en los problemas menores descubiertos durante las inspecciones antes de que provoquen averías o reparaciones importantes. Esto incluye apretar las conexiones sueltas o reemplazar las correas desgastadas descubiertas durante las comprobaciones de rutina.
Mantenimiento centrado en la confiabilidad: Enfoque estratégico que analiza las funciones, las posibles fallas y las consecuencias de cada activo para determinar la estrategia de mantenimiento más adecuada. Esto podría incluir la implementación de la supervisión del estado de los equipos críticos y, al mismo tiempo, utilizar el mantenimiento cronológico para los activos menos críticos.
Actividades de mantenimiento comunes
Actividades de mantenimiento comunes centrarse en preservar la funcionalidad del equipo y prevenir las fallas. Estas actividades suelen incluir:
- Inspeccionar el equipo en busca de signos de desgaste o daños
- Lubricar las piezas móviles para reducir la fricción
- Limpiar los componentes y las áreas circundantes
- Sustitución de filtros y fluidos según lo previsto
- Instrumentos y controles de calibración
- Apretar los sujetadores y conexiones flojos
- Probar sistemas y controles de seguridad
- Documentar el estado y el rendimiento del equipo
- Ajustar los componentes para un rendimiento óptimo
- Realización de pruebas predictivas (de vibración, térmicas, eléctricas)
Estas actividades de mantenimiento proactivo forman la base de un programa exitoso de administración de activos, ya que ayudan a las organizaciones a maximizar la confiabilidad de los equipos y, al mismo tiempo, minimizar las fallas inesperadas y las costosas reparaciones que requieren.
Ejemplos de gastos de reparación y mantenimiento
Los gastos de reparación y mantenimiento varían ampliamente según el tipo de equipo, la industria y si el trabajo de reparación y mantenimiento se realiza interna o externamente. Comprender estos costos ayuda a los departamentos de mantenimiento a asignar los recursos de manera efectiva.
Costos de personal
Los trabajos de mantenimiento y reparación requieren varios profesionales cualificados:
- Técnicos de mantenimiento: Gestione las tareas de mantenimiento rutinario y las reparaciones básicas, normalmente como miembros del personal interno con tarifas por hora que van desde 30 a 40 dólares según la experiencia y la ubicación.
- Ingenieros especializados: Abordar problemas complejos de equipos que requieren un conocimiento técnico más profundo. Los ingenieros mecánicos, eléctricos y de automatización exigen tarifas más altas, ya sean empleados internos o contratados.
- Especialistas en comercio: Incluya electricistas para sistemas eléctricos, técnicos de HVAC para equipos de control climático, especialistas en hidráulica para sistemas de energía fluida y técnicos de control para sistemas de automatización. Estos especialistas suelen tener requisitos de certificación y herramientas especializadas.
- Profesionales de confiabilidad: Concéntrese en analizar los datos de mantenimiento, implementar técnicas predictivas y optimizar los programas de mantenimiento para reducir los costos de reparación.
Recursos internos frente a recursos externos
La evaluación del costo total de las reparaciones debe tener en cuenta tanto los gastos directos incurridos (mano de obra, piezas, equipos) como los costos indirectos (pérdidas de producción, impactos en la calidad, demoras en la entrega). En el caso de los equipos críticos, estos costos indirectos suelen superar con creces los gastos directos de reparación, lo que refuerza el valor de estrategias de mantenimiento preventivo.
Las organizaciones se enfrentan a decisiones estratégicas críticas al asignar las responsabilidades de mantenimiento entre sus equipos internos y los especialistas externos.
- Equipos de mantenimiento interno:
- Tarifas por hora más bajas en comparación con las de los contratistas
- Mayor familiaridad con los equipos de las instalaciones
- Tiempos de respuesta más rápidos para reparaciones de emergencia
- Disponibilidad constante para el mantenimiento programado
- Requieren una inversión en capacitación, herramientas y administración
- Contratistas externos:
- Proporcionar experiencia especializada que no esté disponible internamente
- Suministro de equipos especializados sin inversión de capital
- Ofrezca una fuerza laboral escalable para proyectos grandes o plazos de entrega rápidos
- Puede proporcionar un servicio certificado por el fabricante para el cumplimiento de la garantía
- Por lo general, cobran tarifas superiores (a menudo entre 1,5 y 3 veces el costo de la mano de obra interna)
Cómo reducir sus gastos de mantenimiento, reparación y operaciones (MRO)
Reduciendo MRO los gastos requieren un cambio estratégico de reparaciones reactivas a un mantenimiento proactivo. Las organizaciones que minimizan con éxito estos costos se centran en la prevención más que en la reacción.
Estrategias de mantenimiento proactivo
Implemente programas de mantenimiento preventivo: Desarrolle programas de mantenimiento sistemático basados en las recomendaciones del fabricante, los patrones de uso del equipo y los datos históricos. Las inspecciones de rutina detectan los problemas antes de que provoquen fallos, lo que reduce los costos de reparación de emergencia.
Invierta en la formación del personal: Los técnicos de mantenimiento bien capacitados identifican los posibles problemas antes, realizan las tareas de mantenimiento de manera más eficaz y cometen menos errores. La capacitación regular sobre los equipos, los procedimientos y la seguridad reduce tanto la frecuencia como la gravedad de las reparaciones.
Utilice el software CMMS: Los sistemas computarizados de administración de mantenimiento rastrean el historial de los activos, automatizan las órdenes de trabajo, administran el inventario y analizan los datos de mantenimiento. Esta tecnología elimina las ineficiencias, evita la falta de mantenimiento y proporciona información valiosa sobre el rendimiento de los equipos y los costos de mantenimiento.
Adopte el monitoreo del estado: Implemente tecnologías que rastreen el estado de los equipos en tiempo real, incluidos el análisis de vibraciones, las imágenes térmicas y el análisis del aceite. Estas herramientas detectan los patrones de deterioro antes de que provoquen fallos, lo que permite realizar intervenciones planificadas en lugar de realizar reparaciones de emergencia.
Estandarice los equipos y las piezas: Reduzca los costos de inventario y los requisitos de capacitación de los técnicos estandarizando los modelos y piezas de los equipos siempre que sea posible. Este enfoque agiliza los procesos de mantenimiento y permite descuentos en compras al por mayor.
Costo-beneficio de la prevención frente a la reacción
Los argumentos financieros a favor del mantenimiento preventivo son convincentes si se comparan los costos totales:
Costos de mantenimiento preventivo:
- Horas de trabajo programadas a tarifas estándar
- Sustitución planificada de piezas a precio normal
- Interrupción mínima de la producción durante el tiempo de inactividad programado
- Asignación presupuestaria predecible
Costos de reparación reactiva:
- Tasas de mano de obra de emergencia (a menudo 1,5-2 veces las tarifas estándar)
- Piezas solicitadas con urgencia a precios superiores
- Pérdidas de producción durante tiempos de inactividad no planificados
- Problemas de calidad derivados de reparaciones apresuradas
- Posibles incidentes de seguridad debidos a fallos en el equipo
Los expertos en mantenimiento recomiendan una proporción de 80/20: el 80% de los recursos se dediquen a actividades preventivas y el 20% a reparaciones reactivas. Las organizaciones que logran este equilibrio suelen ver reducciones significativas en los gastos totales de mantenimiento y reparación, a la vez que mejoran la confiabilidad de los equipos, prolongan la vida útil de los activos y mejoran la eficiencia operativa.
Simplifique el mantenimiento preventivo con MaintainX
MaintainX permite a los equipos de mantenimiento crear, asignar y realizar un seguimiento de las tareas de mantenimiento preventivo a través de una interfaz intuitiva accesible desde cualquier dispositivo. El sistema de órdenes de trabajo integrado en la plataforma garantiza que nada pase desapercibido, mientras que las listas de verificación digitales sustituyen los procesos en papel poco fiables.
Con MaintainX, las organizaciones suelen lograr:
- Reducción del 32% en el tiempo de inactividad no planificado
- 30% de ahorro en los costos de mantenimiento mensuales
- Mejora del 39% en la eficacia general del equipo
- Mejora del 53% en las tasas de finalización de órdenes de trabajo
- Aumento del 49% en el porcentaje de mantenimiento planificado
La plataforma también facilita la comunicación en tiempo real entre técnicos y gerentes a través de la mensajería integrada, lo que permite a los equipos resolver los problemas con mayor rapidez. Las funciones avanzadas de generación de informes proporcionan visibilidad de las métricas de mantenimiento, lo que ayuda a las organizaciones a identificar patrones y tomar decisiones basadas en datos.
Preguntas frecuentes sobre mantenimiento y reparaciones
¿Qué se considera reparación o mantenimiento?
El mantenimiento se refiere a las actividades rutinarias y programadas que se realizan para preservar la funcionalidad de los activos y evitar averías. Esto incluye las inspecciones, la limpieza, la lubricación y otras reparaciones y ajustes menores que prolongan la vida útil del equipo. El mantenimiento es proactivo y planificado.
Las reparaciones son respuestas reactivas a un equipo que ya ha fallado o averiado. Si bien las reparaciones restauran la funcionalidad, abordan los problemas una vez que se producen en lugar de prevenirlos. Las reparaciones suelen producirse de forma inesperada y, con frecuencia, provocan tiempos de inactividad no planificados.
¿Cuál es un ejemplo de un costo de reparación frente a un costo de mantenimiento?
Ejemplo de costo de reparación: Sustitución de emergencia de un motor de bomba averiado en una línea de fabricación, con un coste de 5000$ por la pieza, 2000$ en envíos urgentes, 3000$ en tarifas de mano de obra de emergencia y 60 000$ en pérdidas de producción durante las 8 horas de inactividad (7500 dólares/hora).
Ejemplo de costo de mantenimiento: Inspección y lubricación trimestrales programadas del mismo motor de bomba durante el tiempo de inactividad planificado, con un costo de 200 dólares en mano de obra y 50 dólares en lubricantes, sin pérdidas de producción, ya que los trabajos de mantenimiento se realizan fuera del horario laboral.
¿Cuáles son los 3 tipos de reparaciones?
- Reparaciones correctivas: Respuestas planificadas a los problemas identificados durante las inspecciones antes de que se produzca una falla total. Por ejemplo, reemplazar un rodamiento que muestre signos de desgaste detectados durante una inspección de rutina.
- Reparaciones de emergencia: Correcciones urgentes para fallos repentinos y totales que detienen la producción. Estas reparaciones no planificadas a menudo requieren atención inmediata, como la reparación de una línea hidráulica rota en un equipo de excavación o la sustitución de un motor de HVAC averiado.
- Reparaciones aplazadas: Problemas no críticos en los que la reparación se pospone hasta un momento más conveniente. Por ejemplo, posponer las reparaciones cosméticas de los accesorios de las tiendas minoristas hasta después de los períodos de compras navideños o retrasar las reparaciones de equipos secundarios hasta el tiempo de inactividad programado.
¿Cuáles son los 4 tipos de mantenimiento?
- Mantenimiento preventivo: Actividades rutinarias programadas que se realizan mientras el equipo aún está en funcionamiento para evitar fallas. Los ejemplos incluyen las inspecciones periódicas, la lubricación, la limpieza y el reemplazo de componentes en función de los intervalos de tiempo o las métricas de uso.
- Mantenimiento predictivo: Enfoque basado en datos que utiliza tecnologías de monitoreo del estado para determinar cuándo es realmente necesario el mantenimiento. Esto incluye el análisis de vibraciones, las imágenes térmicas y el análisis del aceite para detectar posibles fallos antes de que se produzcan.
- Mantenimiento correctivo: Aborda los problemas identificados antes de que provoquen fallas en el equipo. Si bien es de naturaleza reactiva, se centra en los problemas menores descubiertos durante las inspecciones antes de que provoquen averías.
- Mantenimiento centrado en la confiabilidad: Enfoque estratégico que analiza las funciones, las posibles fallas y las consecuencias de cada activo para determinar la estrategia de mantenimiento más adecuada para los diferentes tipos de equipos y niveles de criticidad.
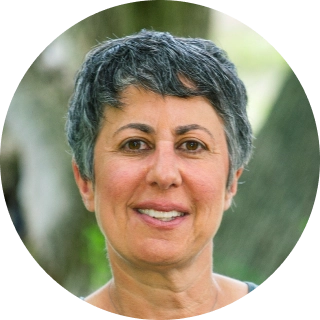
Caroline Eisner es escritora y editora con experiencia en los sectores con y sin fines de lucro, el gobierno, la educación y las organizaciones financieras. Ha ocupado puestos de liderazgo en instituciones de educación primaria y secundaria y ha dirigido proyectos digitales a gran escala, sitios web interactivos y una consultoría de redacción empresarial.