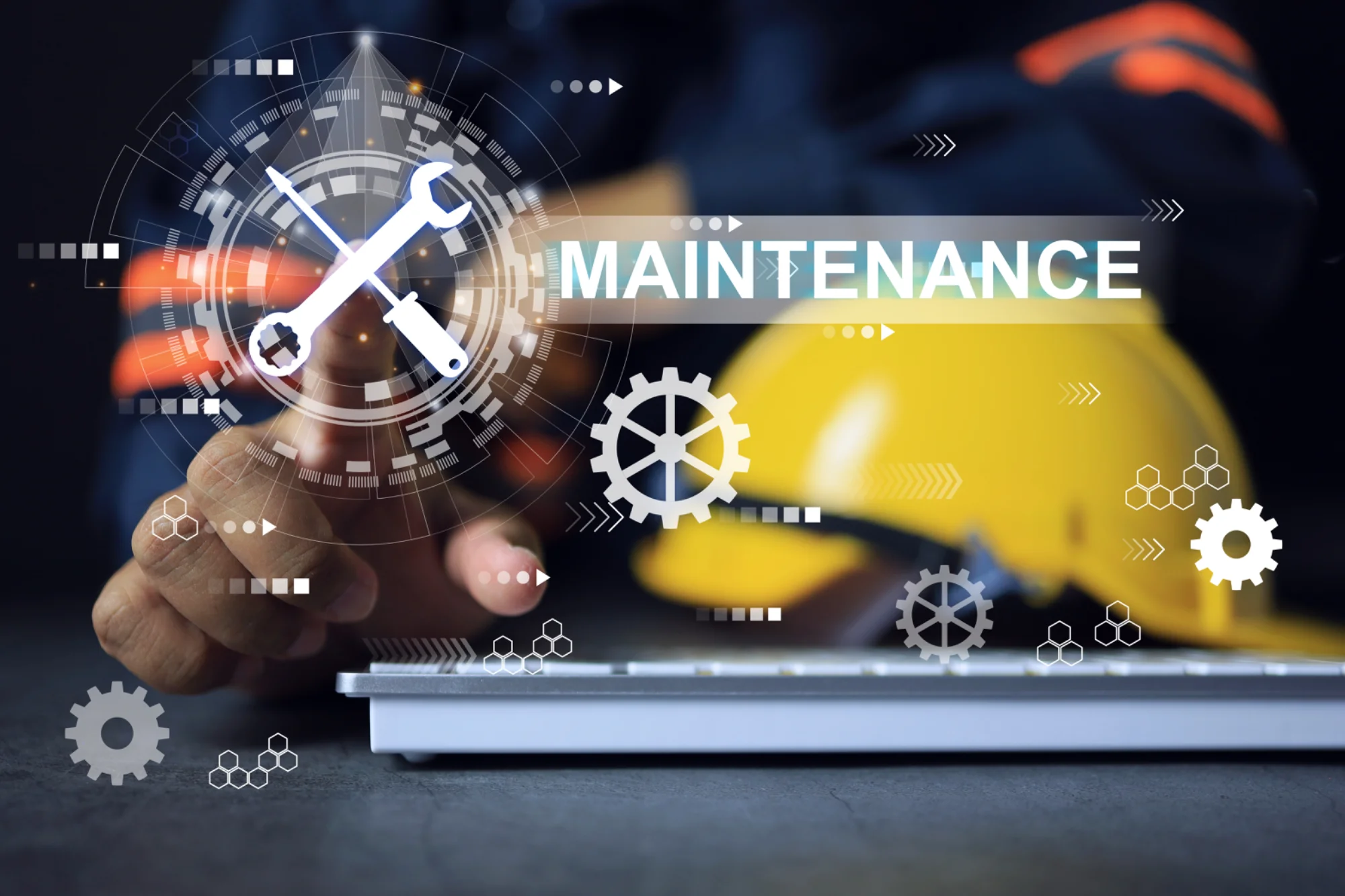
¿Quiere mejorar su estrategia de mantenimiento o implementar una desde cero? Elegir la estrategia de mantenimiento adecuada puede marcar la diferencia entre un sistema de operaciones optimizado y uno plagado de interrupciones y tiempos de inactividad.
Si bien ciertos principios pueden ayudar a cualquier persona a mejorar su mantenimiento, un enfoque único no es la solución más eficiente o rentable, ya que no todos los activos necesitan el mismo tipo o nivel de mantenimiento.
En esta guía, lo guiaremos a través de cinco tipos diferentes de estrategias de mantenimiento, cómo elegir la mejor estrategia de mantenimiento para sus activos y cómo implementar cada estrategia en su negocio.
¿Cuáles son los 5 tipos diferentes de estrategias de mantenimiento?
Los cinco tipos diferentes de estrategias de mantenimiento incluyen:
- Mantenimiento reactivo
- Mantenimiento preventivo
- Mantenimiento basado en el estado
- Mantenimiento centrado en la confiabilidad
- Mantenimiento predictivo
Mantenimiento reactivo (mantenimiento de averías)
¿Qué es el mantenimiento reactivo?
UN mantenimiento reactivo La estrategia, también conocida como mantenimiento continuo hasta que falle, implica retrasar todos los trabajos de mantenimiento hasta que los activos funcionen mal o se estropeen.
Este programa de gestión del mantenimiento requiere poco trabajo proactivo por parte del equipo y, en muchos sentidos, parece ser el enfoque más obvio. Después de todo, ¿por qué arreglar lo que no está roto?
Supongamos que tiene un presupuesto de mantenimiento limitado y un personal reducido dedicado a los trabajos de mantenimiento y confiabilidad. Es posible que dedicar varias horas al cronograma de producción a poner a punto equipos y máquinas que parecen funcionar correctamente no sea un enfoque viable o intuitivo.
Sin embargo, hay que tener cuidado, ya que una estrategia de mantenimiento puramente reactiva puede llevar al caos. Como un glaciar sumergido en el agua, las apariencias engañan. No es raro que máquinas y equipos que funcionan perfectamente se estropeen sin previo aviso. Además, si dirige una instalación con un personal de mantenimiento limitado, el tiempo de inactividad no planificado puede provocar graves pérdidas de ingresos y productividad.
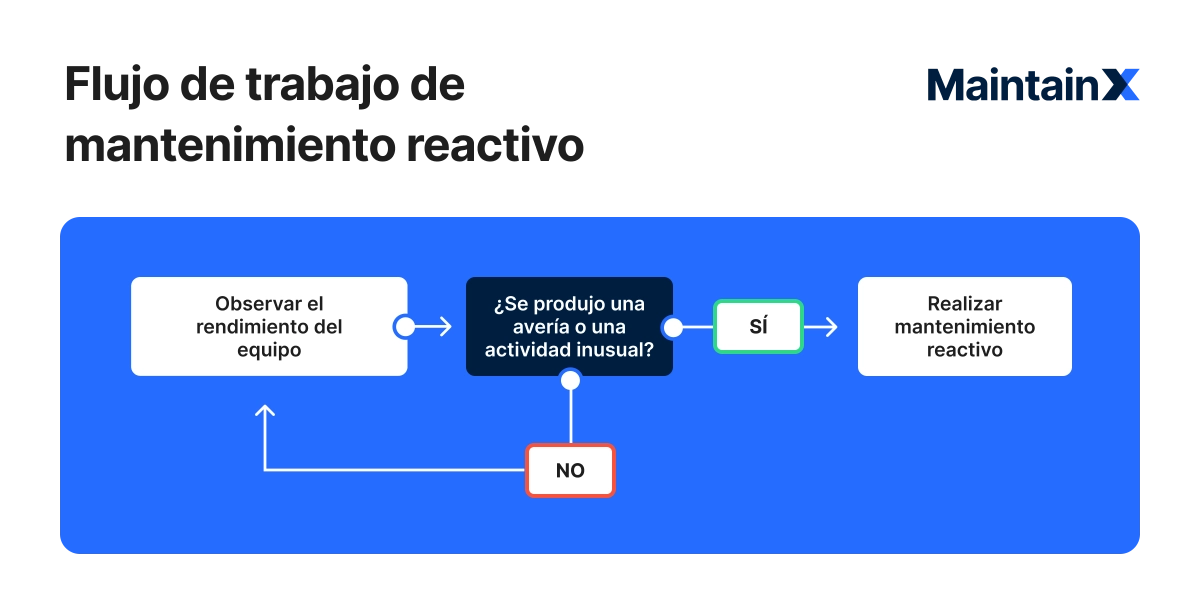
¿Cuál es la cantidad perfecta de mantenimiento reactivo?
¿Con qué frecuencia debe planear dejar que el equipo funcione hasta fallar? Si bien no existe una cantidad «perfecta» de mantenimiento reactivo, los expertos recomendar la adopción de un enfoque 80/20 (basado vagamente en el principio de Pareto), según el cual el 80% de las actividades de mantenimiento se centran en el trabajo proactivo y el 20% restante en el trabajo reactivo.
¿Por qué preocuparse por el mantenimiento reactivo?
Si el mantenimiento proactivo ocupa el 80% de su tiempo, probablemente suene como un enfoque más beneficioso que reactivo. Y aunque en la mayoría de los casos es recomendable tratar de evitar los fallos de funcionamiento (hablaremos de esto en breve), no hay que abandonar por completo el trabajo reactivo. El mantenimiento reactivo es inevitable; a pesar de tus mejores esfuerzos, es posible que se produzcan averías y fallos de funcionamiento.
Si bien desea limitar la cantidad de mantenimiento reactivo que realiza, debe contar con un sólido mantenimiento correctivo planifique para cuando las cosas se estropeen. El mantenimiento correctivo se refiere a las medidas que se toman para corregir un mal funcionamiento o restaurar la funcionalidad de un equipo. Disponer de un plan de medidas correctivas significa que, cuando un equipo deja de funcionar, no se pierde tiempo pensando en cómo restablecer la funcionalidad. Sin un plan establecido, se enfrentará a obstáculos, como reunir el equipo de mantenimiento adecuado, comprender el problema y determinar cómo resolverlo. Como resultado, es posible que tenga dificultades para volver a poner en marcha las operaciones lo antes posible.
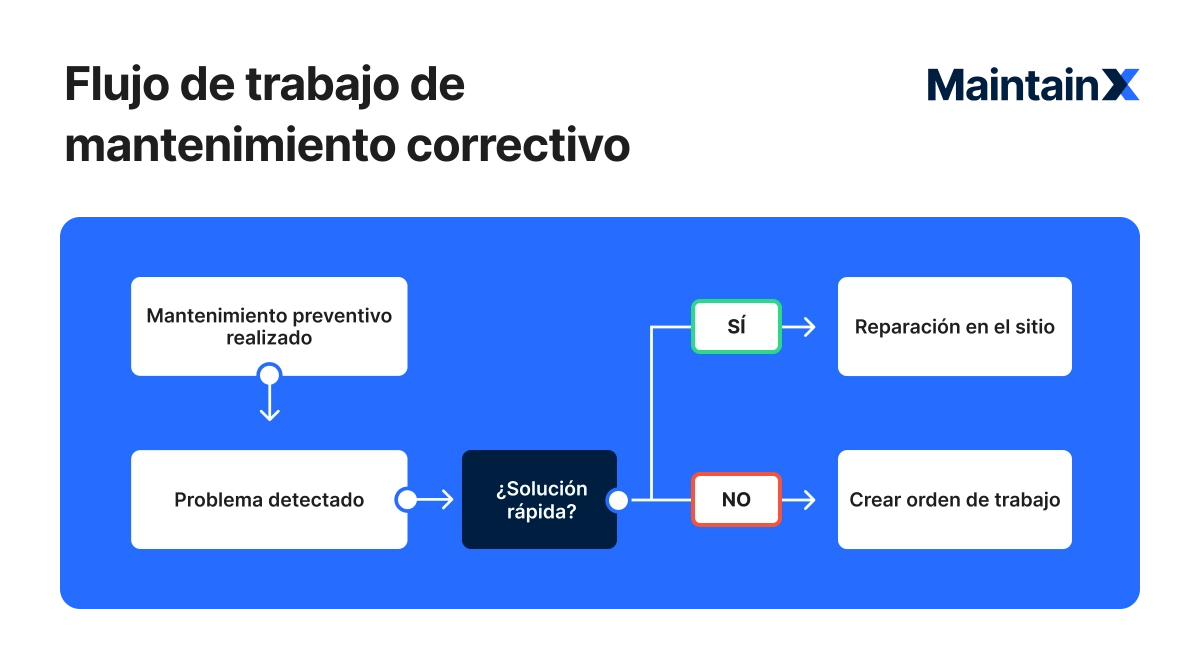
Cuándo elegir el mantenimiento reactivo
Al considerar la implementación de una estrategia de mantenimiento reactivo, compare el costo de realizar un mantenimiento regular con el costo de la falla de los activos. Si el costo del mantenimiento proactivo continuo supera el costo del tiempo de inactividad, la reparación y el reemplazo, el mantenimiento reactivo es el programa de mantenimiento adecuado para ese activo. Los costos de mantenimiento nunca deben superar los incurridos debido a una avería.
Limitaciones del mantenimiento reactivo
Si bien uno de los principales atractivos del mantenimiento reactivo es su bajo costo, los beneficios a corto plazo derivados de limitar las actividades solo a los activos que se estropean a menudo pueden compensarse con pérdidas significativas a largo plazo debido al aumento del tiempo de inactividad y las interrupciones de la producción.
Y en algunos casos, arreglar activos después se descomponen pueden ser más costosos que prevenir para que no se derrumben en primer lugar. Las reparaciones de emergencia y las piezas de repuesto pueden ser más costosas que los trabajos de mantenimiento regulares, ya que suelen requerir tiempo y recursos para restablecer la disponibilidad.
Sin embargo, la mayoría de las veces, con el mantenimiento reactivo, simplemente no lo sabes. No sabes qué tipo de día vas a tener, qué tipo de cronograma esperar de manera realista, qué producción esperar y cómo hacer planes serios. Entras todos los días sabiendo que existe la posibilidad de que alguien te agarre en el pasillo y te impida almorzar porque hay que arreglar algo de inmediato.
Como gerente de mantenimiento, desea poder planificar su día sabiendo que, en su mayor parte, las cosas seguirán un cronograma establecido. Puedes tomarte descansos a determinadas horas, comunicarte con los trabajadores en otras ocasiones y programar reuniones cuando sea conveniente. Apoyarse completamente en una estrategia reactiva significa que todo está en el aire, lo que ejerce mucha presión sobre los líderes.
Como dice Sara Ghali, gerente de producto de MaintainX: «Imagina que conduces un automóvil y se descompone en medio de la carretera. Sus pasajeros están agitados y confundidos por lo que está sucediendo. Se supone que tienes que saber qué hacer, y todos esperan de ti una solución. Lo que sientes en ese momento es estrés, que no es en absoluto la actitud lúcida que necesitas a la hora de decidir cómo reparar un equipo».
Confiar únicamente en un programa de mantenimiento reactivo también supone un riesgo innecesario para sus operaciones. Las averías inesperadas de los equipos representan un riesgo de seguridad para los operadores y los empleados del taller. La falta de mantenimiento e inspección regulares puede conllevar multas y infracciones normativas y de cumplimiento. Además, la imprevisibilidad de las averías de los activos dificulta presupuestar y asignar los recursos en consecuencia, lo que supone una carga para los recursos de la empresa.
Mantenimiento preventivo (mantenimiento planificado o programado)
¿Qué es el mantenimiento preventivo?
A diferencia del mantenimiento reactivo, mantenimiento preventivo (PM) tiene como objetivo evitar que se produzcan averías en primer lugar. Es una estrategia de mantenimiento proactivo basada en actividades regulares y recurrentes que protegen los activos, mantienen los equipos en buenas condiciones de funcionamiento y evitan el tiempo de inactividad no planificado.
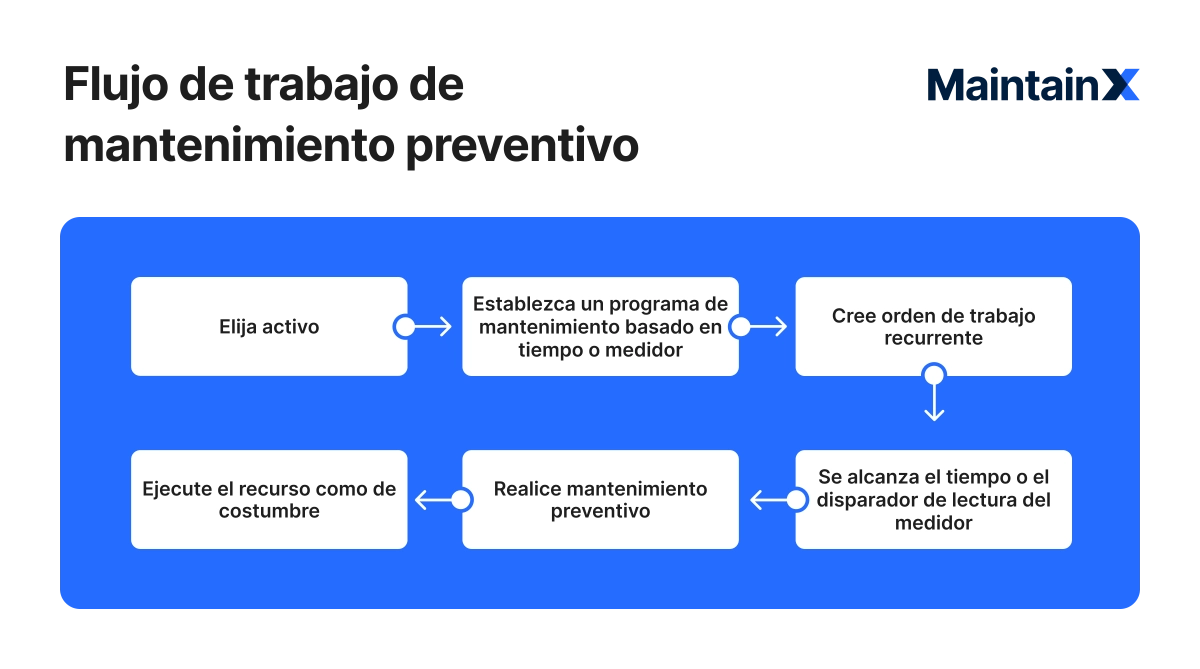
El mantenimiento preventivo puede seguir un cronograma basado en el uso, el calendario y el período de tiempo. Estos tipos de mantenimiento programado se incluyen en mantenimiento periódico.
Cuándo elegir el mantenimiento preventivo
La PM es más eficaz cuando el desgaste de los equipos y las piezas sigue un patrón predecible, lo que le permite programar el mantenimiento en función de los intervalos de tiempo o el uso. Además, seguir las directrices del fabricante en materia de mantenimiento garantiza el cumplimiento de las condiciones de la garantía y se ajusta a las mejores prácticas establecidas tras exhaustivas pruebas.
El mantenimiento preventivo hace mucho más que mantener los activos disponibles para la producción. Al mantener el equipo en buenas condiciones de funcionamiento, puede asegurarse de eliminar cualquier posible problema de calidad debido a un mal funcionamiento del equipo. Un equipo óptimo proporcionará productos óptimos.
En última instancia, el mantenimiento es colaborativo y, si bien reducir el tiempo de inactividad no planificado es un beneficio clave del mantenimiento preventivo, esta estrategia de mantenimiento va de la mano con la gestión de la calidad y la seguridad.
Además, con una estrategia reactiva, no solo no tiene idea de cuándo fallarán sus activos, sino también de qué manera. Siempre hay que lanzar una moneda entre pequeños fallos y averías que conllevan graves consecuencias para la salud y la seguridad. Tomar el control mediante el mantenimiento preventivo significa que puede reducir considerablemente el riesgo de que se produzcan fallos catastróficos que comprometan la seguridad de su personal y de sus instalaciones.
Para crear una estrategia de implementación de PM eficaz, comience con un inventario exhaustivo de los activos. Luego, determine las prioridades definiendo los equipos que requieren un mantenimiento regular y son fundamentales para la producción y la seguridad.
Determine sus intervalos de PM ideales en función de la capacidad de su fuerza laboral, los requisitos de los activos individuales y los requisitos reglamentarios. Después de programar e implementar las órdenes de trabajo recurrentes, asegúrese de evaluar constantemente su progreso para identificar las áreas en las que mejorar y ajustar sus planes de mantenimiento cuando sea necesario.
Algunos ejemplos de PM son:
- Realizar comprobaciones rutinarias de lubricación y alineación de los motores eléctricos para evitar el sobrecalentamiento y garantizar un funcionamiento eficiente, siguiendo un cronograma basado en las horas de funcionamiento.
- Reemplazar los filtros e inspeccionar los conductos a intervalos regulares para mantener la calidad del aire y la eficiencia del sistema, evitar averías inesperadas y prolongar la vida útil del equipo.
Considera cuánto durará un activo sin mantenimiento y cuánto costará reemplazarlo, y luego compáralo con el costo potencial de ejecutar un PM regular durante ese tiempo. Además, determine si estos activos tienen modos de fallo que el mantenimiento regular pueda prevenir. Si un activo solo experimenta fallas debido a errores aleatorios que el mantenimiento preventivo no puede solucionar, el mantenimiento preventivo desperdicia tiempo y dinero y se vuelve redundante.
Limitaciones del mantenimiento preventivo
El mantenimiento preventivo es un enfoque rentable que ahorra dinero al evitar las averías y las consiguientes pérdidas de producción. El principio rector es que las horas y los recursos dedicados a las actividades rutinarias serán inferiores a los que, de otro modo, se dedicarían a restaurar la funcionalidad de los activos durante el tiempo de inactividad.
Sin embargo, encontrar ese equilibrio puede ser un desafío. Un mantenimiento preventivo mal planificado puede provocar trabajos de mantenimiento redundantes o innecesarios, consumiendo activos y recursos humanos que podrían ser útiles en otros lugares. Además, gestionar varios programas de gestión de proyectos para una variedad de activos puede resultar cada vez más complicado.
Además, una estrategia de mantenimiento preventivo es redundante para los activos no reparables o de un solo uso. Por lo general, es mejor reemplazar los activos que están cerca del final de su ciclo de vida o que ya no se pueden reparar, en lugar de dedicar tiempo y esfuerzo a prolongar su ya limitada vida útil.
Mantenimiento basado en el estado (CBM)
¿Qué es el mantenimiento basado en el estado?
El mantenimiento basado en la condición (CBM) es una estrategia de mantenimiento proactivo que se centra en monitorear y evaluar el estado real de los equipos y activos para determinar cuándo se debe realizar el mantenimiento. El CBM se basa en la supervisión continua o periódica del estado de los equipos mediante diversas herramientas y técnicas de diagnóstico. Los métodos comunes incluyen el análisis de vibraciones, la termografía, el análisis de aceite y las pruebas ultrasónicas.
El CBM puede minimizar el tiempo de inactividad y reducir los costos generales de mantenimiento. Con esta estrategia, se inician las tareas de mantenimiento cuando ciertos indicadores sugieren una disminución del rendimiento o un fallo inminente. El CBM es un enfoque reactivo que puede resultar menos complejo y costoso en comparación con el mantenimiento predictivo, que analizamos a continuación.
Por ejemplo, una aplicación común del mantenimiento basado en el estado implica el uso de lecturas de presión en los sistemas de tuberías. El personal de mantenimiento monitorea constantemente los niveles de presión, lo que les permite identificar cuándo pueden producirse posibles fugas. Las organizaciones que dependen de sistemas de tuberías o líquidos, como los productores de alimentos y bebidas, utilizan el CBM para rastrear la presión y diagnosticar problemas.
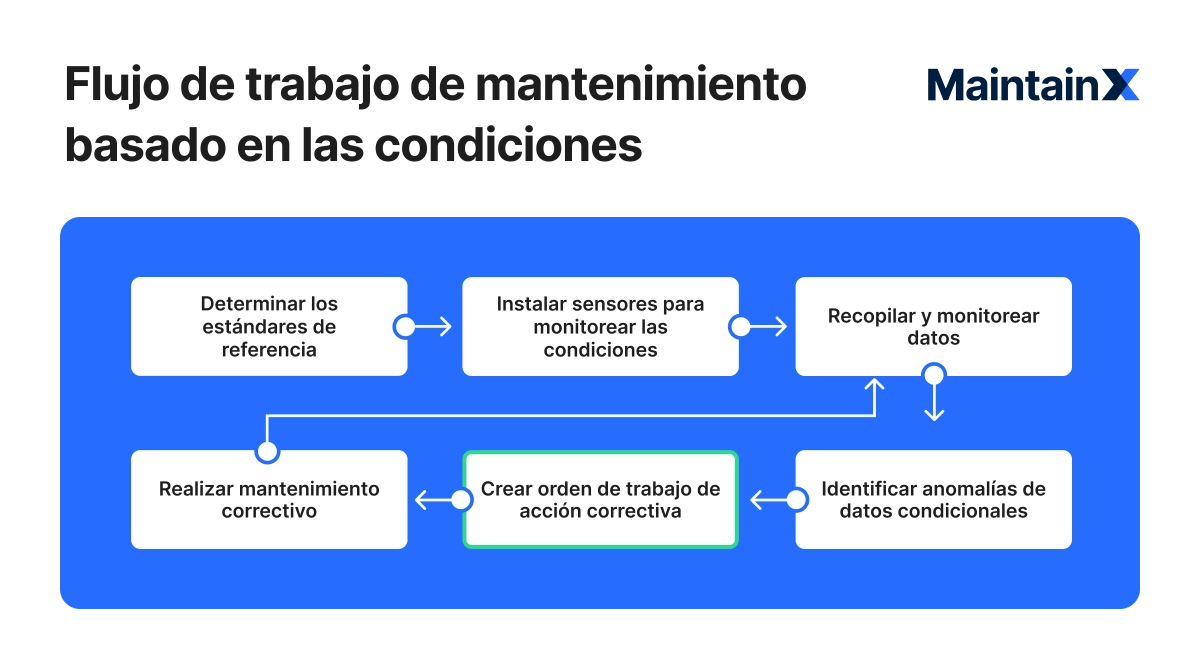
6 técnicas principales de monitoreo basadas en la afección
Las tecnologías CBM recopilan datos de forma continua mientras el equipo está en funcionamiento. Estos dispositivos registran los números a intervalos determinados o de forma continua mediante inspecciones visuales, sensores y pruebas programadas. Las seis técnicas principales de monitoreo basadas en la afección incluyen las siguientes:
Análisis de vibraciones: Este tipo de sistema de monitoreo basado en el estado mide las frecuencias y los niveles de vibración de la maquinaria. Luego, los equipos de mantenimiento utilizan esta información para analizar el estado de los equipos y sus componentes a fin de detectar problemas, como ejes doblados, resonancias, holguras, fallas en los rodamientos y desequilibrios. Por ejemplo, un ventilador dañado producirá más señales de vibración.
Termografía infrarroja: La termografía infrarroja es un sistema de monitoreo basado en el estado que utiliza cámaras termográficas para detectar la radiación de un objeto. Los generadores de imágenes convierten la radiación en temperatura y muestran su distribución en tiempo real. Este proceso ayuda a detectar cuándo un equipo se sobrecalienta. Entre los ejemplos de herramientas de infrarrojos se incluyen las cámaras termográficas infrarrojas, los sistemas de escaneo infrarrojo y los termógrafos infrarrojos. Los equipos de mantenimiento los utilizan principalmente para comprobar los niveles de gas, líquidos y lodos; inspeccionar los rodamientos; examinar el aislamiento refractario; y supervisar las condiciones mecánicas y eléctricas de los motores.
Análisis ultrasónico: El análisis ultrasónico detecta y convierte los sonidos de alta frecuencia en audio y datos digitales para ayudar a identificar los activos que podrían fallar. Este sistema de monitoreo basado en el estado utiliza métodos de recopilación de datos con y sin contacto para determinar los diferentes tipos de fallas detectables. Los métodos de contacto (basados en la estructura) generalmente detectan fallas que generan ruido de alta frecuencia, como problemas de lubricación, fallas en los rodamientos, barras de rotor rotas y daños en los engranajes. Los métodos sin contacto (aerotransportados), por otro lado, ayudan a detectar fugas de presión y vacío en los sistemas de gas comprimido, además de en diversas aplicaciones eléctricas.
Análisis de aceite: Los equipos de mantenimiento analizan el estado del aceite, la contaminación y el desgaste de la máquina. Pueden determinar si los aditivos están activos o agotados y si la viscosidad es correcta, entre otras propiedades del fluido oleoso. Un programa de análisis de aceite ayudará a confirmar si un equipo funciona como debería.
Análisis eléctrico: En este caso, la atención se centra en la calidad de la energía entrante de los activos. La corriente del circuito se mide utilizando las lecturas de corriente del motor de los amperímetros con pinza. El análisis eléctrico ayuda a determinar si un activo tiene un suministro eléctrico anormal.
Análisis de presión: Es importante que los equipos que transportan aire, gas o fluido mantengan la presión correcta. Los equipos de mantenimiento utilizan el análisis de presión para monitorear continuamente los niveles de presión en tiempo real. Reciben alertas en caso de caídas o picos repentinos y pueden responder antes de que la situación se agrave.
Cuándo elegir el mantenimiento basado en el estado
El mantenimiento basado en el estado es más efectivo cuando se aplica a equipos y activos críticos que podrían afectar significativamente la producción, la seguridad o las operaciones en caso de falla o que tienen altos costos de mantenimiento y reparación. El CBM funciona mejor con activos que tienen modos de fallo bien definidos y que experimentan un desgaste gradual y predecible a lo largo del tiempo. Antes de elegir CBM, asegúrese de tener acceso inmediato a las tecnologías de monitoreo, como los sensores, que sean compatibles con su equipo.
Limitaciones del mantenimiento basado en el estado
El CBM ofrece varias ventajas, pero también es importante reconocer sus limitaciones. En primer lugar, los costos iniciales de implementar sistemas de monitoreo basados en el estado pueden ser altos debido a la necesidad de invertir en sensores, medidores y otros instrumentos de monitoreo.
El mantenimiento basado en el estado también puede ser menos efectivo en condiciones de trabajo hostiles, donde los sensores son vulnerables a daños o están expuestos al ruido. Además, el CBM es más eficaz para los activos críticos que tienen modos de fallo bien documentados, en los que la detección temprana de los problemas puede evitar un desglose de los costes. En el caso de equipos menos críticos o más simples, el costo y el esfuerzo de implementar la CBM pueden resultar difíciles de justificar.
Mantenimiento centrado en la confiabilidad (RCM)
¿Qué es el mantenimiento centrado en la confiabilidad?
Mantenimiento centrado en la confiabilidad (RCM) se centra en crear enfoques sistemáticos y estructurados para mantener los activos individuales. Su objetivo principal es garantizar que los esfuerzos de mantenimiento se centren en actividades que maximicen la confiabilidad y el rendimiento de los activos y, al mismo tiempo, minimicen los costos y los riesgos operativos. La RCM implica, en primer lugar, realizar un análisis detallado de los posibles modos de fallo y su posible impacto y, a continuación, crear planes personalizados para evitarlos.
El objetivo de RCM es responder a cuatro preguntas fundamentales sobre el mantenimiento de los activos individuales:
- ¿Cuáles son las funciones del activo? ¿Cómo ha funcionado en el pasado?
- ¿Cuáles son los posibles modos de falla y las causas de cada activo?
- ¿Cuáles son las consecuencias de estas fallas en términos de seguridad, impacto ambiental y pérdidas financieras?
- ¿Qué tareas de mantenimiento, ya sean proactivas (preventivas) o correctivas, deben aplicar los equipos para mitigar estas consecuencias?
Desea evaluar las posibles consecuencias de las fallas para averiguar cómo prevenirlas. Repita este procedimiento para todos los activos, creando un enfoque de mantenimiento personalizado para cada equipo, mejorando la confiabilidad y garantizando que los activos permanezcan disponibles en todo momento.
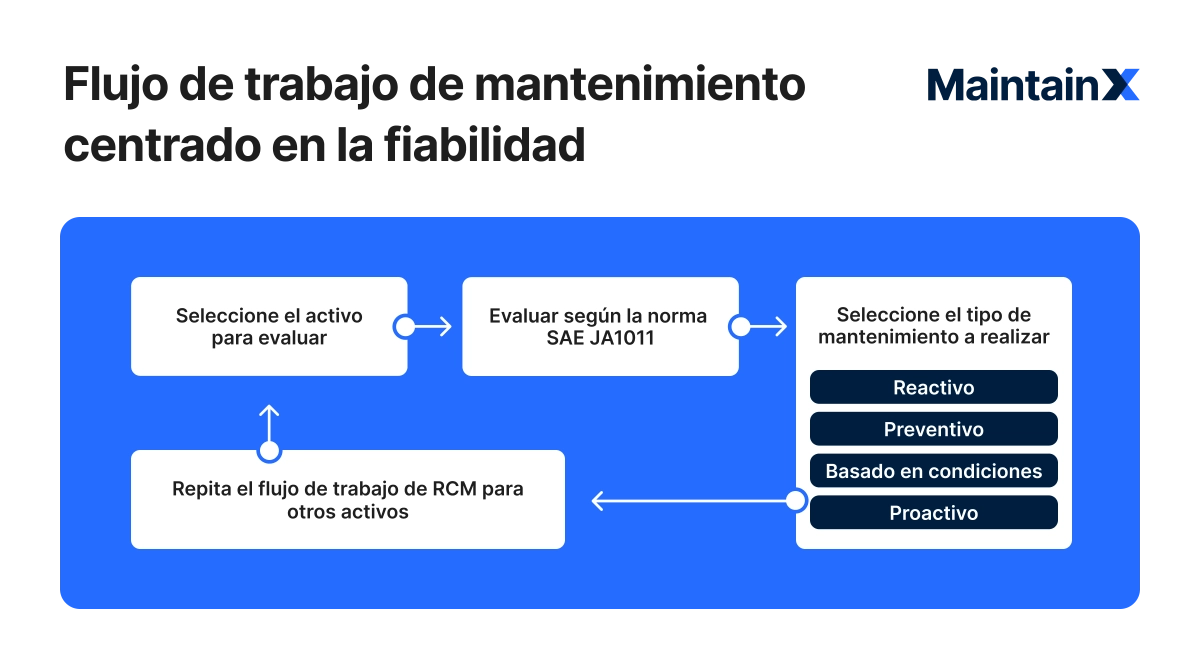
Cuándo elegir un mantenimiento centrado en la confiabilidad
Si necesita asignar estrategias de mantenimiento en función de las necesidades específicas del equipo, el RCM es una gran idea. En lugar de aplicar una estrategia de mantenimiento (preventiva, reactiva o predictiva) en toda la instalación, RCM optimiza los datos para personalizar las soluciones clasificando los activos según su criticidad. Por ello, el RCM es una buena opción para las instalaciones con activos cuya criticidad varía considerablemente y ayuda a los equipos a optimizar los recursos en función de la prioridad.
Limitaciones del mantenimiento centrado en la confiabilidad
Al proporcionar soluciones personalizadas para diferentes activos, el RCM puede ser increíblemente poderoso cuando se trata de equipos cuyo mal funcionamiento podría tener un impacto desastroso en los ingresos, la producción y la seguridad. Sin embargo, la creación de estas soluciones requiere datos de mantenimiento detallados, un proceso de integración complejo y mucho tiempo y recursos.
Si tiene los recursos para dedicar personal a integrar la RCM en todos sus activos o está dispuesto a trabajar con un socio con experiencia en este campo, entonces esto podría ser para usted.
Del mismo modo, si tiene registros de mantenimiento detallados y claros, le resultará más fácil implementar RCM. Sin los datos adecuados, el RCM puede ser más difícil de lo que merece.
Mantenimiento predictivo (PdM)
¿Qué es el mantenimiento predictivo?
A diferencia del mantenimiento basado en condiciones reactivas, mantenimiento predictivo (PdM) es una forma de mantenimiento proactivo que funciona mediante el uso de información sobre el estado del equipo (como la temperatura, la presión y otros factores de estado de los activos) para predecir una falla inminente.
A diferencia del mantenimiento basado en el estado, el basado en condiciones los datos recopilados incorporan algoritmos avanzados de análisis, minería de datos y aprendizaje automático, que buscan patrones y tendencias para predecir el estado futuro del activo. Los equipos de mantenimiento pueden utilizar las predicciones del tiempo de inactividad de los equipos para aislar las tareas de mantenimiento y centrarlas únicamente en los activos más necesarios a fin de reducir cualquier trabajo de mantenimiento redundante.
La diferencia clave entre el CBM y el PdM es que el PdM se centra en pronosticar las condiciones futuras para optimizar la planificación del mantenimiento, mientras que el CBM reacciona principalmente a las condiciones actuales del equipo.
IIoT y mantenimiento predictivo
El PdM utiliza sensores de monitoreo del estado para rastrear las condiciones del equipo en tiempo real. Estos sensores funcionan mediante el IIoT (Internet industrial de las cosas), que son dispositivos e instrumentos interconectados conectados en red con aplicaciones informáticas para mejorar la fabricación, el mantenimiento y otras actividades industriales.
Algunos ejemplos de dispositivos sensores PdM son los equipos de análisis de vibraciones, la tecnología acústica ultrasónica y otros equipos que controlan los factores relacionados con el estado del equipo.
El PdM introduce los datos recopilados a través de los sensores en algoritmos de aprendizaje automático para predecir posibles fallos comparando el comportamiento actual de un activo con su comportamiento esperado. En este caso, la detección de anomalías (comportamiento anormal) activa el PdM.
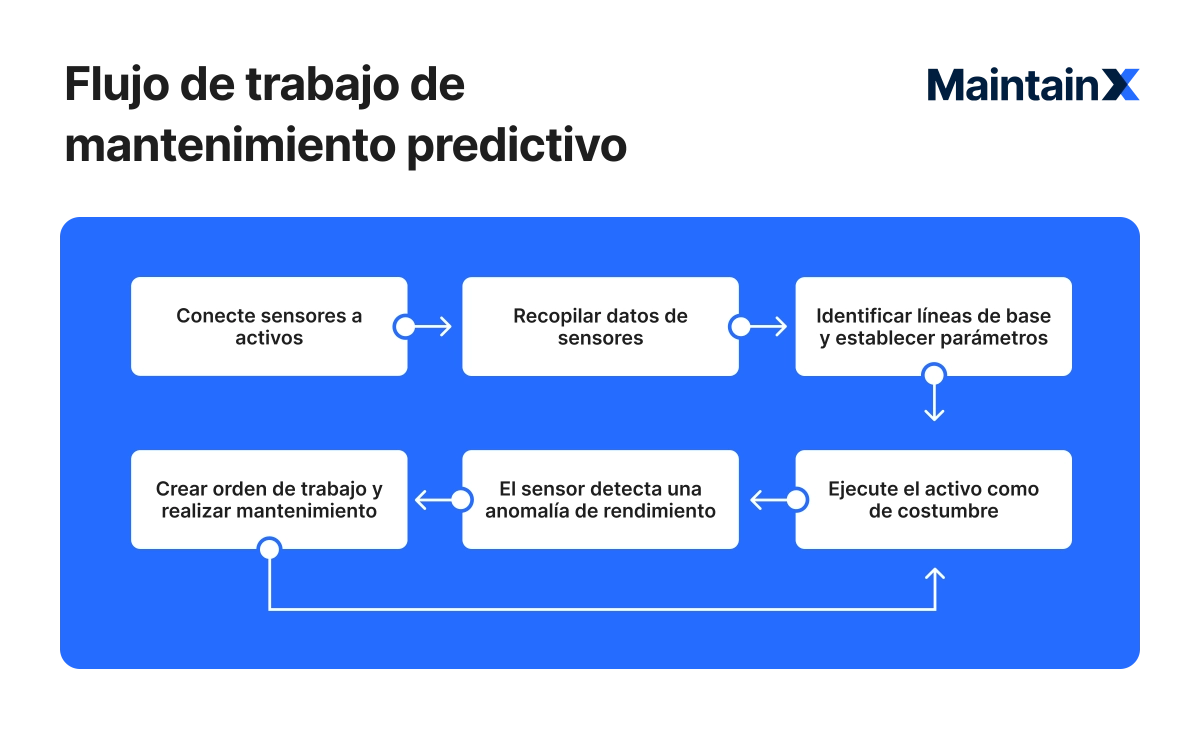
Cuándo elegir el mantenimiento predictivo
La implementación del mantenimiento predictivo solo tiene sentido cuando se cuenta con las capacidades de recopilación y análisis de datos necesarias, ya que depende en gran medida de la supervisión y el análisis en tiempo real de las condiciones de los equipos mediante complejos algoritmos predictivos. Sin la infraestructura necesaria o la voluntad de invertir en la infraestructura requerida, es difícil implementar con éxito una estrategia de mantenimiento predictivo. Sin embargo, si los equipos de mantenimiento están listos o dispuestos a invertir en mantenimiento predictivo, pueden aumentar la confiabilidad de los activos, disminuir los costos de mantenimiento y reducir el tiempo de inactividad no planificado.
Cuadro resumido de estrategias de mantenimiento
Cómo elegir la estrategia de mantenimiento adecuada para sus instalaciones
En la práctica, será difícil encontrar una instalación que dependa exclusivamente de una estrategia. Si bien un programa de mantenimiento preventivo ayuda a reducir los costos, mantener el tiempo de actividad y evitar las paradas de emergencia, es necesario un plan de mantenimiento reactivo para hacer frente a las emergencias cuando se producen. Tenga en cuenta estos factores al crear su programa de mantenimiento:
- Los activos en cuestión: Examine minuciosamente su registro de activos para determinar qué tipo de mantenimiento requiere cada activo. ¿Qué dicen las directrices del fabricante sobre cómo y cuándo abordar el mantenimiento? ¿Se aplica alguna normativa de cumplimiento a determinados equipos? ¿Qué notan usted y su equipo de mantenimiento acerca de estos activos y cómo funcionan cuando se utilizan? Considera los costos potenciales de las fallas de los equipos para cada activo y el costo de la supervisión de los equipos para priorizar el mantenimiento de activos específicos.
- Capacidades y recursos internos: No importa lo sólidos que sean sus recursos, no querrá desperdiciar ninguno de ellos. Piense en formas de optimizar el personal de mantenimiento y las piezas de repuesto al crear una estrategia de mantenimiento. ¿Cuenta con suficiente personal para implementar cada una de sus estrategias de mantenimiento? ¿Y cuánto le costaría confiar estrictamente en el mantenimiento reactivo?
- Datos, datos, datos: Al implementar cualquier estrategia, asegúrese de recopilar, registrar y analizar datos constantemente. Utilice estos datos para identificar qué acciones producen los resultados deseados y cuáles no. «Los datos sólidos le ahorran la molestia y la energía de recordar cosas», afirma Sara Ghali. «Incluso en ausencia de un experto, el conocimiento está dentro del sistema. No solo tendrá acceso a información sobre cómo manejó los problemas en el pasado, sino que también podrá identificar tendencias, establecer mejoras graduales y optimizar la administración del tiempo». Con esto en mente, continúe reiterando y ajustando su enfoque de mantenimiento para lograr una mejora constante.
Lleve su mantenimiento al siguiente nivel
La elección del tipo correcto de mantenimiento es específica para su empresa y para cada activo. Si bien las estrategias específicas pueden parecer perfectas sobre el papel, la estrategia adecuada para usted siempre será la que pueda implementar con éxito.
Cuando empieces a implementar la estrategia elegida, recuerda que no tienes que hacerlo solo. Reserva un recorrido con MaintainX para averigüe cómo nuestro sistema de gestión de mantenimiento computarizado (CMMS) puede ayudarlo a crear o mejorar su estrategia de mantenimiento.
FAQs
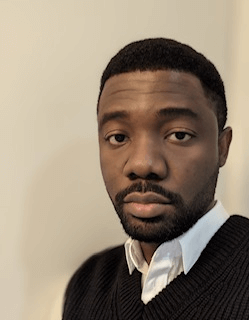
Lekan Olanrewaju es un escritor de contenido con años de experiencia en medios y creación de contenido. Ha ocupado cargos en varias organizaciones de medios, trabajando y liderando equipos en revistas impresas, publicaciones digitales y producciones televisivas.