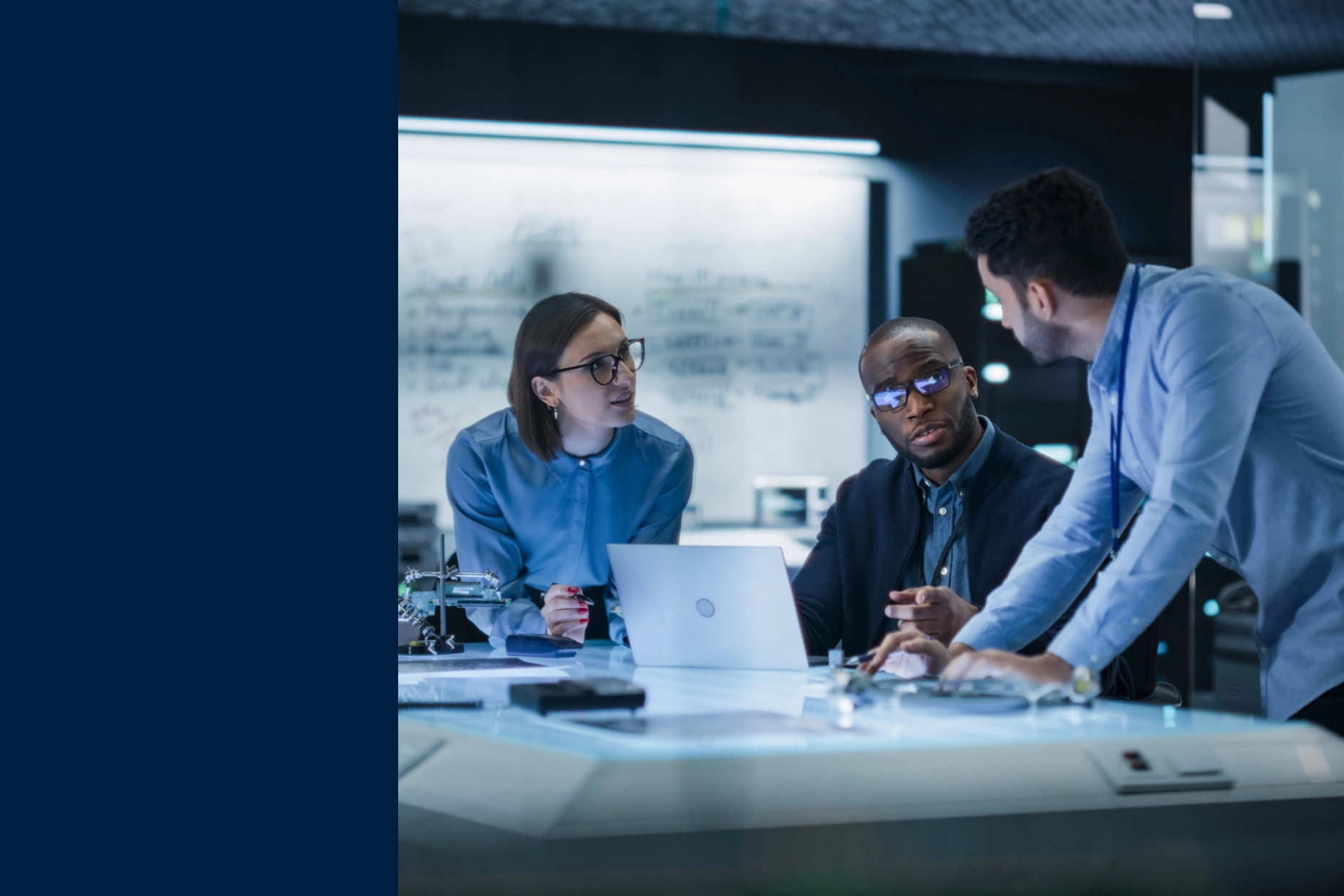
¿Qué es la FMEA?
FMEA son las siglas de Failure Modes and Effects Analysis. Se trata de un análisis de ingeniería que se realiza para evaluar las posibles causas de las fallas operativas relacionadas con el diseño del producto, la producción en línea de ensamblaje y las averías de los equipos de fabricación.
No importa el negocio, el objetivo final de FMEA es simple: ¡mantener en marcha la producción de productos de alta calidad! Con ese fin, el proceso de la FMEA implica tomar medidas basadas en datos para evitar cualquier posible contratiempo desde el diseño hasta el envío.
Según la Sociedad Estadounidense para la Calidad, el FMEA requiere un equipo multifuncional de expertos en la materia para intercambiar ideas sobre cómo los equipos pueden fallar y sus efectos. Los equipos de la FMEA analizan paso a paso los procesos actuales de los sistemas, subsistemas y asambleas organizacionales para concebir todos los posibles resultados.
Además de respaldar la confiabilidad de los equipos, los datos del FMEA también pueden proporcionar información que ayude a promover mejores estrategias de mantenimiento, medidas de seguridad y cumplimiento normativo.
FMEA frente a FMECA
En algún momento, es posible que también se haya topado con el término Análisis de modos de falla, efectos y criticidad (FMECA). Tanto la FMEA como la FMECA son metodologías que los profesionales del mantenimiento utilizan para identificar, evaluar y abordar los posibles modos de falla.
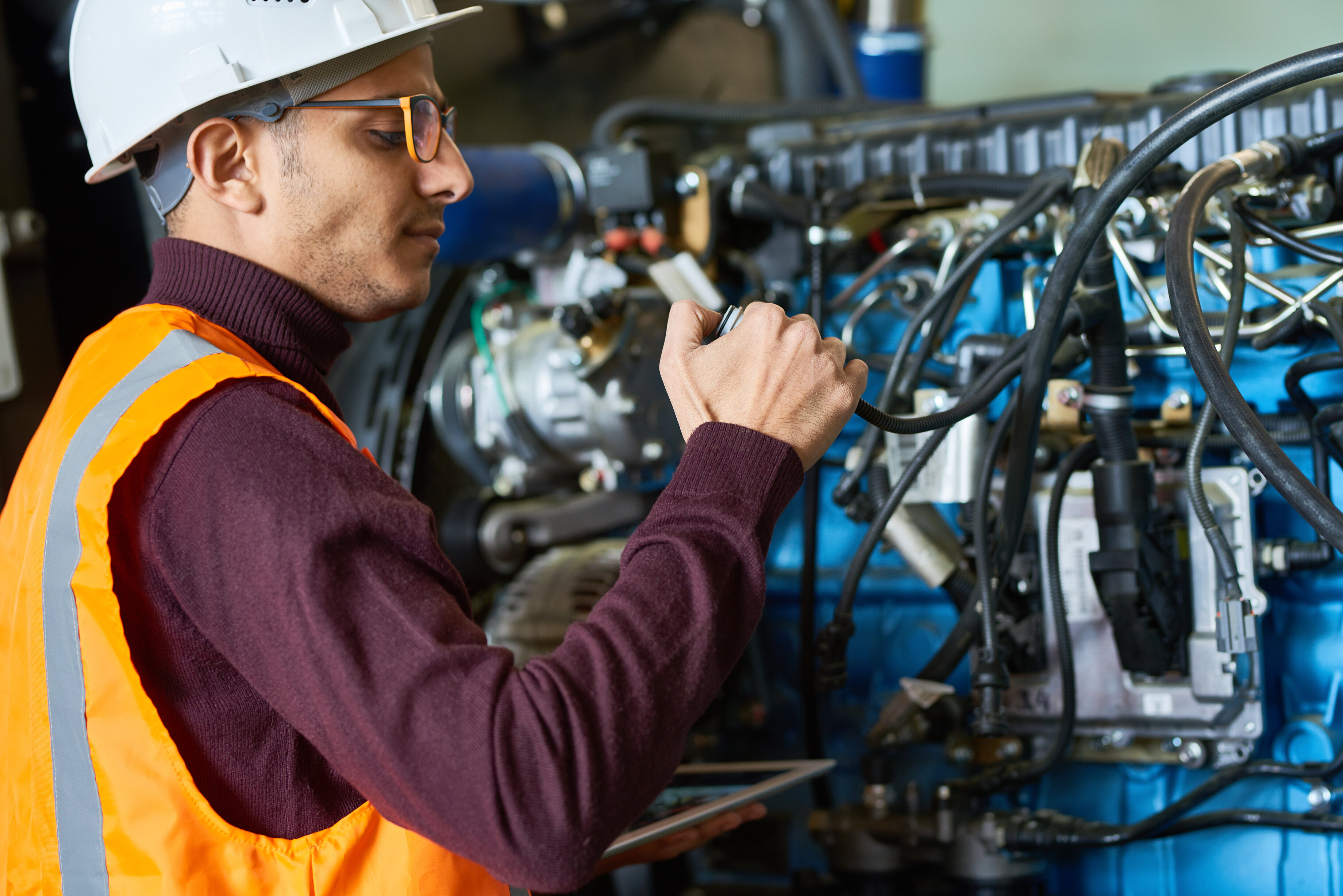
Si bien el FMEA es una herramienta excelente para generar información cualitativa, el FMECA incorpora una evaluación adicional denominada análisis de criticidad en la mezcla.
La norma ISO 31000:2009: Principios y directrices de gestión de riesgos describe un análisis de criticidad como el proceso de asignar a los activos una clasificación de criticidad en función de sus riesgos potenciales.
En este caso, cualquier factor que introduzca incertidumbre para alcanzar los objetivos de producción se clasifica como «riesgo». En pocas palabras, FMECA es FMEA + un análisis de criticidad.
Es más probable que los fabricantes, los almacenes y los proveedores de petróleo y gas utilicen este componente adicional para informar a los programas de mantenimiento basados en sensores.
Dicho esto, tanto la FMEA como la FMECA ayudan a las organizaciones a satisfacer las crecientes demandas de los clientes al permitirles ofrecer productos de calidad, funcionales y seguros. Sin embargo, durante el resto de este artículo, nos centraremos en los pormenores de la FMEA.
La historia de la FMEA
Durante la década de 1940, el Las Fuerzas Armadas de los Estados Unidos desarrollaron el FMEA clasificar las fallas «según su impacto en el éxito de la misión y en la seguridad del personal y el equipo».
Pasamos rápidamente a 500 millones de personas viendo a Neil Armstrong dar «un pequeño paso para el hombre y un gran salto para la humanidad» en 1969. La mayoría de los televidentes no se dieron cuenta de que el Apolo 11 nunca habría aterrizado en la Luna sin el FMEA.
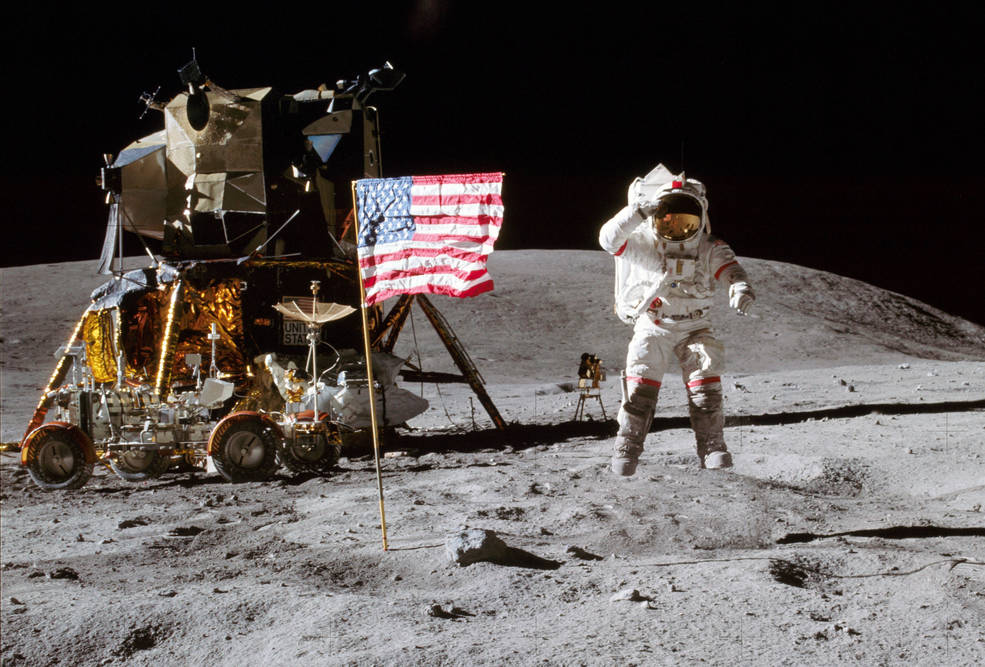
Durante una entrevista para el Proyecto de Historia Oral del Centro Espacial Johnson, Armstrong dijo que las especificaciones de confiabilidad del hardware de la NASA permitían hasta cuatro fallas por cada 100 000 operaciones.
«Solo puedo atribuirlo al hecho de que todas las personas del proyecto, todas las personas del banco que construyen algo, todos los ensambladores, todos los inspectores, todos los que preparan las pruebas, ponen en marcha la llave dinamométrica, etc., dicen: 'Si algo sale mal aquí, no será mi culpa, porque mi pieza va a funcionar mejor de lo que tengo que fabricar'».
Continuó diciendo que su equipo no habría tenido éxito sin el compromiso de los miles de trabajadores de la NASA con excelencia operativa. Poco después de que la NASA adoptara el FMEA, otras industrias importantes que dependían de la confiabilidad de los equipos (automoción, atención médica, minería y petróleo) siguieron su ejemplo.
¿Cómo se relaciona el FMEA con el mantenimiento?
FMEA ayuda a los profesionales del mantenimiento a responder a la antigua pregunta: ¿qué debemos solucionar primero? Priorizar el mantenimiento de cientos de miles de máquinas y piezas no es fácil.
Todos los gerentes de O&M saben que correr mantenimiento preventivo en activos críticos es ideal, pero eso no significa que siempre suceda. Los presupuestos limitados, las limitaciones de tiempo y la escasez de mano de obra a menudo obligan a los líderes operativos a tomar decisiones difíciles a la hora de asignar las órdenes de trabajo.
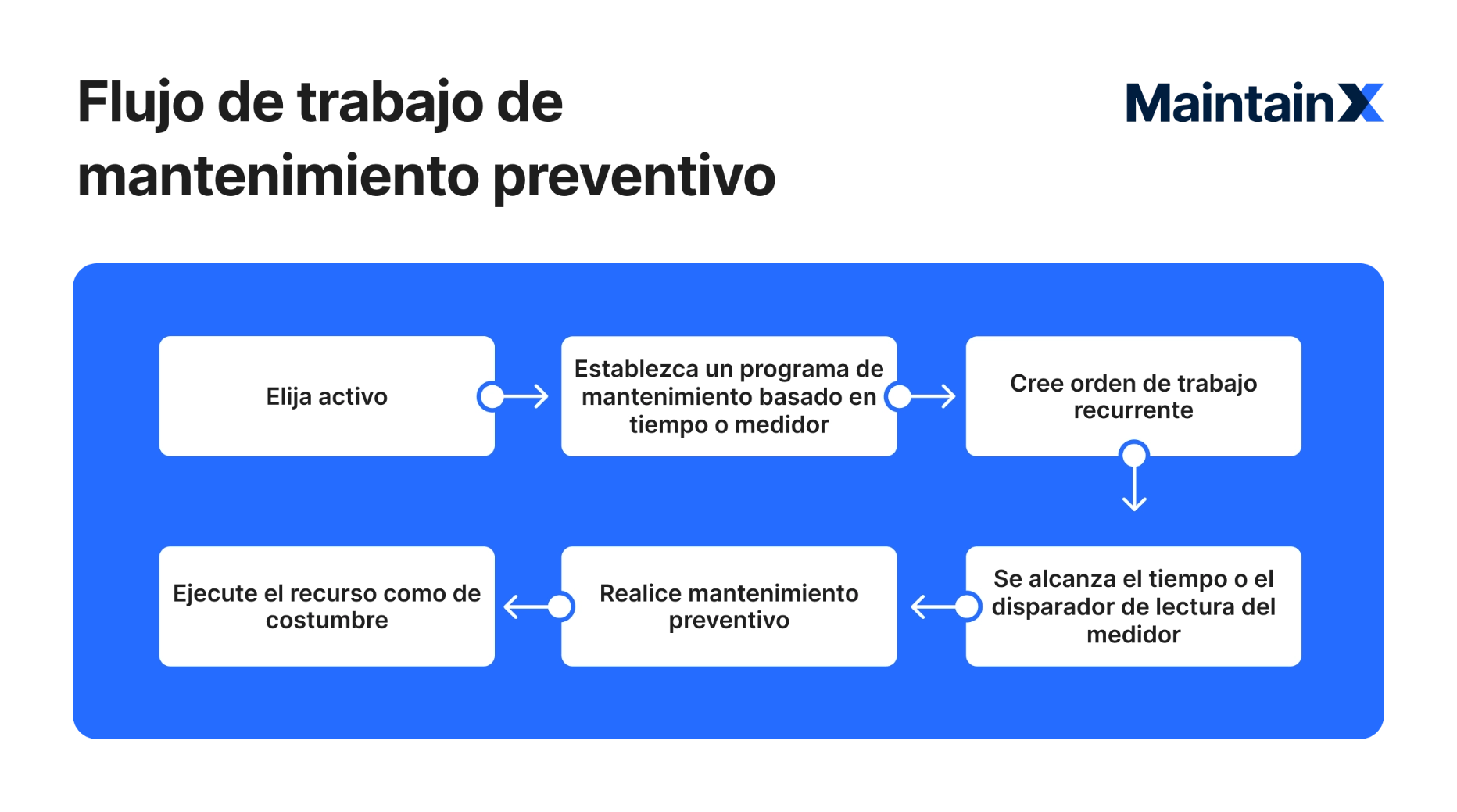
Aquí es donde el FMEA puede ser particularmente útil. Los responsables del mantenimiento pueden utilizar este enfoque sistemático para identificar el potencial fallo del equipo modos, estime la frecuencia de su aparición y evalúe la gravedad del impacto.
El resultado es una imagen más clara de cómo los diferentes procesos operativos se impactan entre sí, lo que se traduce en optimización programación de mantenimiento.
Actuar sobre la base de datos realistas de la FMEA reduce el tiempo de inactividad del equipo, mantenimiento de averías gastos y mejora de la seguridad de los miembros del equipo.
Sin embargo, lanzar un programa de FMEA no es para un departamento de mantenimiento dirigido de manera informal. Para tener éxito, los equipos de mantenimiento deben comprometerse a seguir las recomendaciones del grupo de trabajo.
Además, los gerentes de mantenimiento deben hacer cumplir los procedimientos operativos estándar para evaluar el progreso del programa de manera consistente. La forma más fácil de organizar, analizar y actuar en función de los datos del programa es utilizar un dispositivo móvil software de gestión de mantenimiento computarizado (CMMS) sistema.
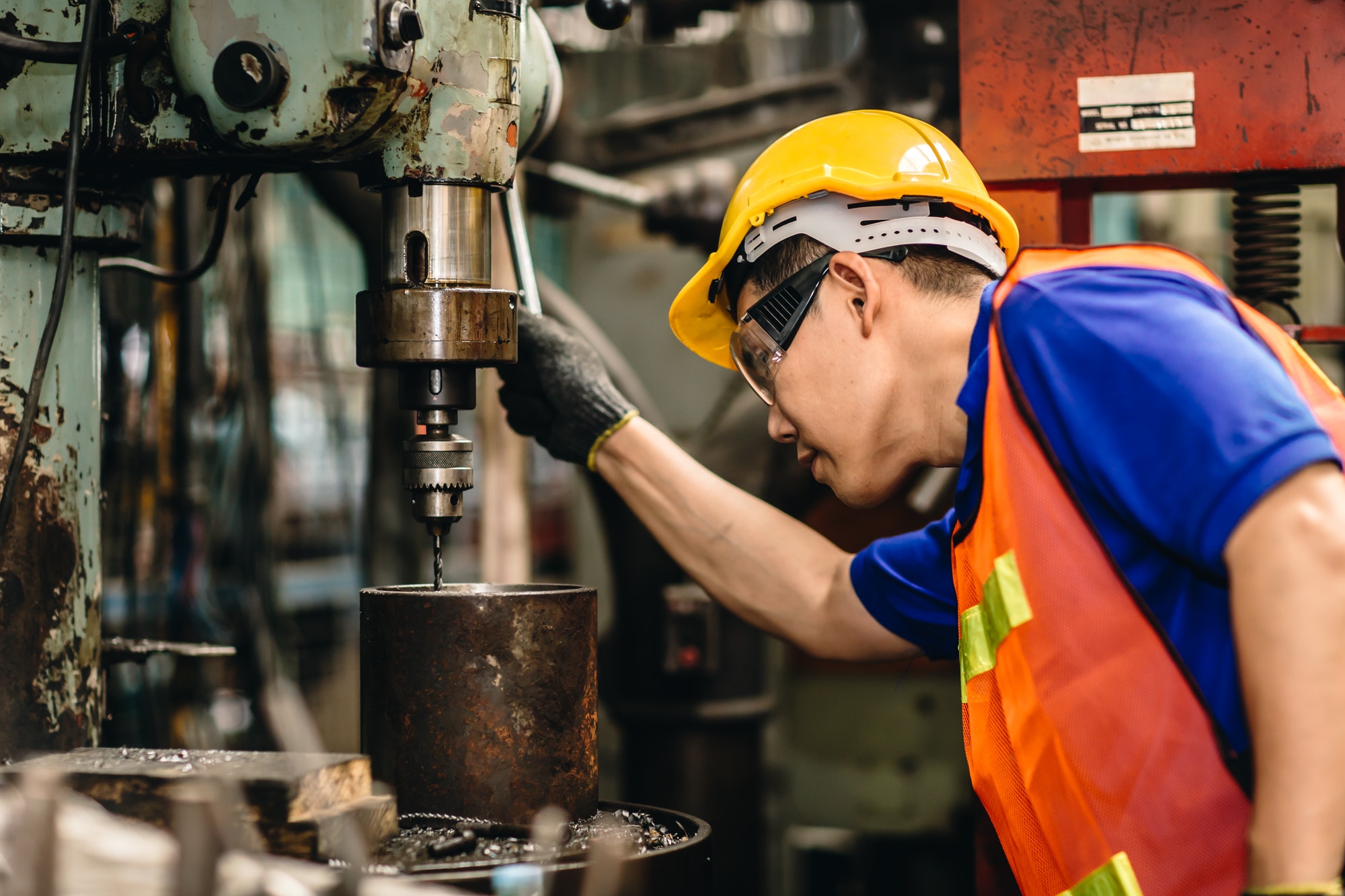
3 tipos de FMEA
Los líderes empresariales suelen llevar a cabo las FMEA al diseñar, rediseñar y volver a implementar productos y procesos. También resulta útil a la hora de preparar planes de control para los procesos operativos. Si bien el método analítico incluye varios subconjuntos, lo más común es dividirlo en tres categorías:
1. Sistema FMEA
Sistema FMEA, también denominado FMEA_ funcional, analiza los modos de fallo a vista de pájaro. Se centra en sistemas y subsistemas completos relacionados con la integración de sistemas, la seguridad en el lugar de trabajo y cualquier otra cosa que pueda afectar a la productividad general.
El sistema FMEA se centra en el hecho de que pueden producirse fallos entre varios activos y procesos. En otras palabras, rara vez una falla del sistema es un evento aislado. Estos incluyen los modos de fallo de un solo punto que afectan a varios puntos de contacto y los modos de fallo complejos aislados de una maquinaria específica. Los expertos recomiendan realizar el FMEA del sistema antes de decidirse por diseños de sistemas funcionales.
2. Diseño FMEA
Como su nombre indica, el enfoque principal de Diseño FMEA es el diseño de productos y servicios. Los líderes organizacionales diseñan el FMEA para evaluar las posibles fallas, los problemas de seguridad y los requisitos reglamentarios relacionados con los productos finales.
El objetivo es garantizar que los productos de la empresa sean seguros, confiables y de alta calidad para los clientes. Los líderes operativos realizan el FMEA del diseño tanto antes de que los nuevos productos pasen a la producción como durante las reiteraciones del diseño del producto. El resultado de una sesión de diseño exitosa del FMEA son las acciones que mitigarán el mal funcionamiento de los productos.
3. Procesar FMEA
Proceso FMEA se centra en el proceso utilizado para fabricar el producto en lugar del producto final en sí. Los gerentes usan procesar FMEA para identificar los problemas en los procesos de producción relacionados con la comercialización de un producto.
Por ejemplo, un portátil incluye varias piezas, cada una de las cuales es el resultado de procesos de producción únicos en sí misma. Suponiendo que la dirección identifique un problema con el procesador de la computadora, tendrá que evaluar todos los procedimientos necesarios para instalarlo en la computadora.
El alcance del proceso FMEA incluye las operaciones de ensamblaje, el etiquetado de productos, la gestión de piezas y el transporte de materiales. Las organizaciones suelen llevar a cabo este tipo de FMEA durante la «fase de estudio de viabilidad» de la fase de preproducción. El objetivo final es crear procesos de producción sólidos que cumplan con las especificaciones de diseño con un tiempo de inactividad mínimo y las modificaciones necesarias.
Vale la pena mencionar que algunos líderes operativos segmentan el FMEA en categorías adicionales. FMEA conceptual, FMEA de servicios, FMEA de análisis de peligros y FMEA de software son algunos de los términos que puede escuchar al hablar del tema con otras personas. Independientemente del tipo de FMEA, el proceso siempre contiene facetas similares.
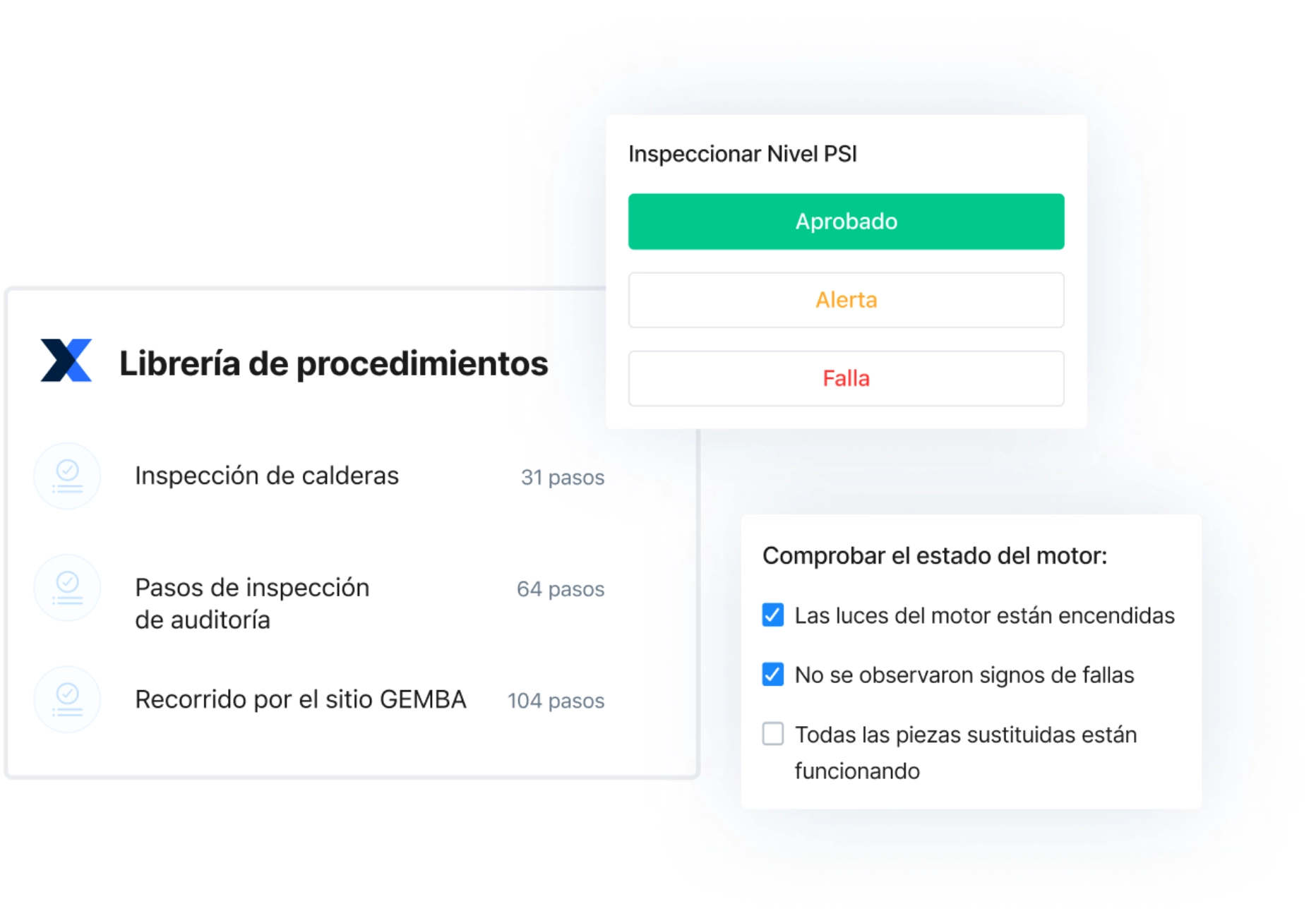
Cuatro elementos clave del FMEA
El FMEA se basa en los siguientes elementos para profundizar en los posibles problemas operativos:
- Modos de fallo: Los modos de falla se refieren a las diversas formas en que un activo, o sus partes, pueden dejar de funcionar correctamente. Por ejemplo, una bomba centrífuga puede sufrir un fallo hidráulico, un fallo mecánico o corrosión.
- Causas de fallo: Este componente del análisis implica una buena lluvia de ideas a la antigua usanza. Los líderes de los grupos de trabajo deben realizar evaluaciones del riesgo sistémico de cada posible modo de falla basándose en experiencias pasadas. Sorprendentemente, las causas fundamentales suelen tener su origen en procedimientos comunes, departamentos hermanos, obstáculos en los sistemas y formas de despilfarro operativo.
- Análisis del modo de fallo: Una vez que los líderes han identificado las posibles causas del fracaso, es el momento de medir la frecuencia y la gravedad de sus ocurrencias. Este aspecto de la FMEA implica clasificar la gravedad estimada de los efectos de cada fallo (por ejemplo, la seguridad de los empleados, la rentabilidad empresarial y la fiabilidad de los activos), la probabilidad de que se produzca y su probabilidad de detección. A continuación, el equipo multiplica las tres clasificaciones para obtener un número de prioridad de riesgo (RPN) que sirva de base para la priorización de las tareas de mantenimiento y operaciones.
- Acción y revisión: Por último, el equipo desarrolla un plan de acción para ejecutar las recomendaciones del FMEA. Una vez más, el CMMS adecuado puede automatizar todo el proceso, desde la asignación de listas de verificación digitales hasta la gestión de activos y el análisis de costes y tiempos, afeitarse hasta 20 horas por semana en comparación con los procesos de administración de datos analógicos.
Ahora que comprende los conceptos básicos de FMEA, profundicemos en el meollo del proceso: el proceso de análisis del modo de falla, que incluye la clasificación de las puntuaciones de las fallas.
Comprensión de las puntuaciones de fracaso del FMEA
Un análisis del modo de falla del FMEA incluye los tres atributos de puntuación siguientes:
- Gravedad: Las clasificaciones de gravedad revelan a qué modos de falla se les debe dar prioridad. Considera qué factores son esenciales para la empresa, sus clientes y la industria en general. Los directivos pueden sopesar las normas de seguridad, la continuidad empresarial, los requisitos medioambientales y los daños a la reputación al asignar las clasificaciones de gravedad. Una clasificación de gravedad baja significa que un modo de fallo tiene un impacto mínimo en la empresa o sus clientes, mientras que una clasificación alta significa un efecto perjudicial más grave.
- Detección: La clasificación de detecciones determina la probabilidad de prevención antes de que se produzca una posible falla. En otras palabras, mide la probabilidad de que los trabajadores detecten el problema antes de que ocurra. Las clasificaciones de detección baja representan problemas fácilmente detectables, mientras que las clasificaciones de detección alta representan problemas impredecibles.
- Ocurrencia: Esta clasificación muestra la probabilidad de que se produzca un modo de falla durante la vida útil de un activo. Una clasificación de ocurrencia baja significa que es poco probable que la falla ocurra, mientras que una clasificación de ocurrencia alta implica que la falla del activo es una ocurrencia más probable.
A cada atributo se le asigna una clasificación por categoría, normalmente entre uno y 10. Los modos de error que es poco probable que se produzcan reciben una calificación de uno. Luego, las tres métricas se multiplican para obtener un número de prioridad de riesgo (RPN) para cada modo de falla.
Ejemplo de puntuación de error
Por ejemplo, si una máquina de café espresso tiene una clasificación de gravedad de 10, una clasificación de detección de dos y una clasificación de ocurrencia de cuatro, su número de prioridad de riesgo sería 80. Recuerde que el objetivo a largo plazo es reducir sus niveles de riesgo mediante la corrección proactiva de los factores catalizadores del riesgo.
En algunos casos, no es posible reducir las calificaciones de severidad de los activos. Por este motivo, es mejor centrarse en reducir lo que se puede controlar: los índices de aparición y detección. Esto significa que minimizará las probabilidades de que se produzca un problema y, al mismo tiempo, mejorará su capacidad para detectar los errores antes de que ocurran.
En última instancia, cuanto más alta sea la clasificación de gravedad, mayor será el impacto de la falla en la productividad empresarial, la satisfacción del cliente y los resultados finales.
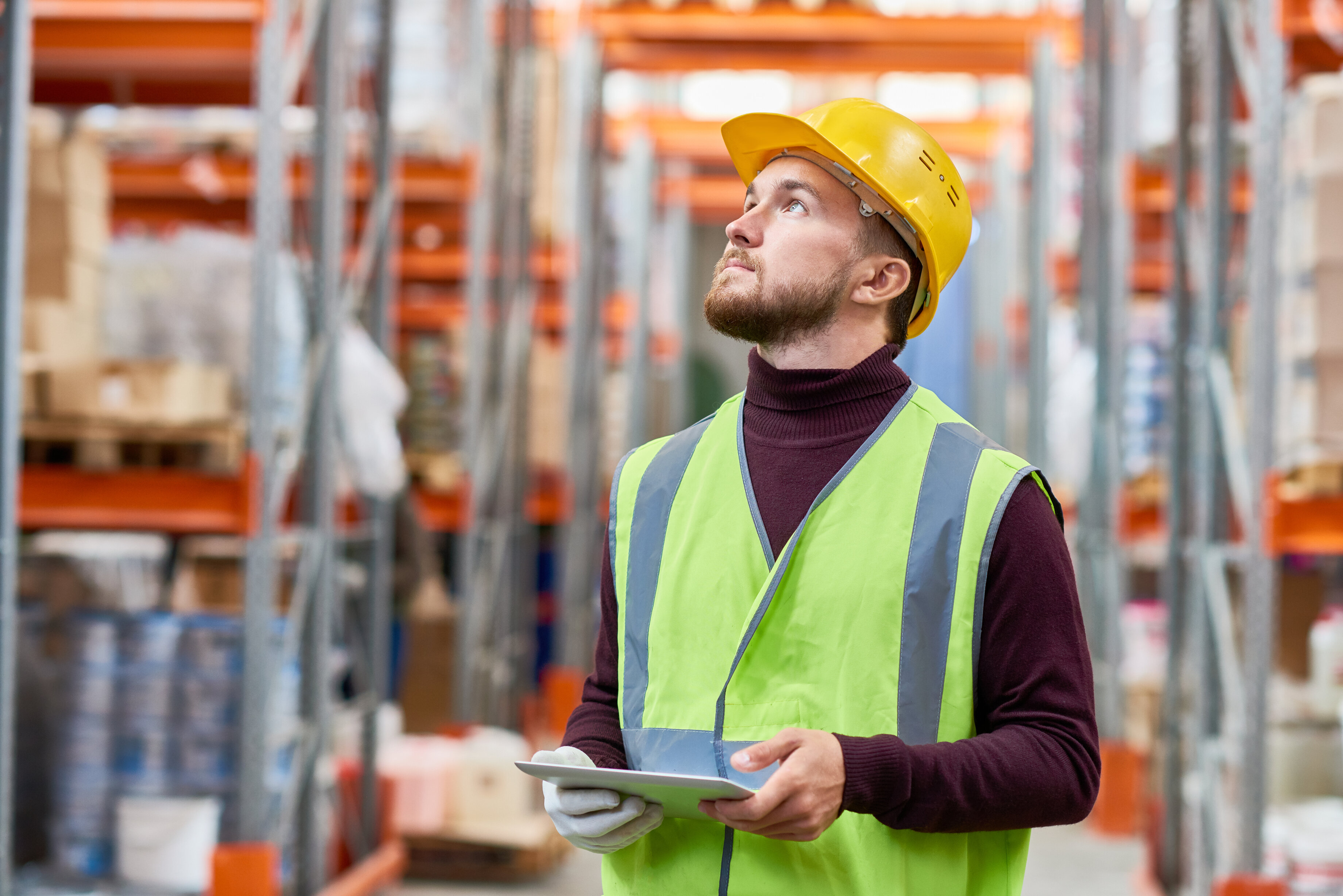
Cómo realizar un análisis de los efectos del modo de falla
El mejor momento para ejecutar un FMEA inicial es durante la fase de desarrollo del producto de su organización. Esto permite disponer de tiempo suficiente para implementar modificaciones a fin de agilizar el diseño del producto y procesos de fabricación. Por supuesto, puede realizar el FMEA en cualquier momento que desee mejorar el control de calidad, aumentar la rentabilidad o aumentar la eficiencia.
Antes de empezar, vale la pena mencionar que se puede encontrar un desglose más completo de cómo llevar a cabo un FMEA en J1739_202101: Análisis de modos y efectos de posibles fallos (FMEA), incluido el FMEA de diseño, el FMEA-MSR complementario y el FMEA de proceso.
Siga leyendo para obtener una descripción general para comenzar:
Paso 1: Reúne a tu equipo de FMEA
A pesar de la palabra «yo» en el FMEA, el análisis debe incluir a muchos miembros clave del equipo para tener éxito.
Con esto en mente, reúna un grupo de trabajo para encabezar la iniciativa. En la mayoría de los casos, un ingeniero de producción o un gerente de mantenimiento dirigirá el equipo. Otras funciones potencialmente relevantes son los ingenieros de procesos, los diseñadores de procesos, los proveedores, los comercializadores e incluso los clientes.
Paso 2: Reúna sus datos
Una vez que tengas tu equipo listo, reúne la siguiente información:
- Diagramas de límites
- Diagramas de parámetros
- Mantenimiento de activos
- Diagramas de trabajo
- Matriz de características
A continuación, determine qué tipo de FMEA realizará.
Paso 3: Especifique su alcance
Identifique las relaciones entre los sistemas, subsistemas, ensamblajes y piezas que su equipo evaluará en el FMEA. Además, configure procedimientos operativos estándar para dirigir, ejecutar y dar seguimiento a sus esfuerzos.
Puede usar un diagrama de flujo para visualizar los detalles con mayor claridad. Es crucial asegurarse de que todos los miembros del equipo estén en sintonía antes de que comience el proyecto.
Paso 4: Identificar los posibles modos de falla
En este punto, está listo para considerar las diversas formas en que sus activos pueden fallar. Utilice el historial de mantenimiento, los conocimientos de los empleados de primera línea, las directrices del fabricante y otros recursos útiles para intercambiar ideas sobre los posibles resultados.
Su objetivo es generar una lista exhaustiva de lo que podría salir mal. Es fundamental hacer hincapié en que los modos de fallo específicos pueden provocar otros fallos en los sistemas o subsistemas. Por este motivo, siempre tenga en cuenta el contexto general al identificar posibles problemas. Además de los modos de fallo que provocan que los activos se estropeen por completo, tenga en cuenta aquellos que pueden provocar:
- Funciones o resultados no deseados de un activo.
- Rendimiento deficiente.
- Funcionalidad reducida.
Aísle cada activo y sus componentes para identificar todos los posibles modos de falla, incluidos los ocultos. Los modos de fallo estándar del equipo incluyen grietas, deformaciones del producto, fatiga por torsión y cortocircuitos eléctricos.
Paso 5: Determinar las clasificaciones de gravedad
Como se mencionó anteriormente, las clasificaciones de gravedad miden el efecto general de los modos de falla. Los gerentes de mantenimiento suelen utilizar una escala del uno al 10 para clasificar el impacto de menor a mayor.
Por lo general, los modos de fallo que afectan a la seguridad o a los resultados de la empresa reciben una clasificación de gravedad más alta. Siempre se debe dar prioridad a los modos de fallo con una clasificación de gravedad alta. Por ejemplo, un fabricante de automóviles puede asignar una clasificación de gravedad alta a un problema relacionado con la instalación de un airbag debido a su impacto negativo en la seguridad y los retrasos en la producción.
Paso 6: Determinar las clasificaciones de ocurrencias
La clasificación de ocurrencias mide la frecuencia con la que es probable que ocurran los modos de falla. También se mide en una escala del uno al 10.
Al determinar la clasificación de ocurrencias, es esencial tener en cuenta todas las posibles causas del modo de falla y el control de prevención existente para evitar que ocurra.
Utilizando el ejemplo mencionado en el paso anterior, ¿por qué el fabricante del automóvil recibiría airbags defectuosos o retrasaría las entregas? Podría deberse a una confusión por parte del proveedor, a discrepancias a la hora de hacer el pedido o a una interrupción de la comunicación. ¿Hay algún control para garantizar que esto no suceda? En caso afirmativo, la instalación incorrecta del airbag recibirá una clasificación de incidencia baja o moderada.
Paso 7: Determinar las clasificaciones de detección
En esta etapa, determine la clasificación de detección para los modos de falla identificados. Esto significa establecer qué tan fácil será identificar la falla antes de que ocurra. Las altas clasificaciones de detección significan que es casi imposible identificar y resolver los problemas antes de que se produzcan las fallas.
Paso 8: Calcular la RPN y priorizar las acciones
Ahora, calcule el número de prioridad de riesgo (RPN) para cada modo de falla multiplicando las tres clasificaciones: detección, ocurrencia y gravedad. Esto le permitirá priorizar las iniciativas de diseño, mejora de procesos y mantenimiento. He aquí un vistazo a la fórmula de la RPN:
Número de prioridad de riesgo (RPN) = Gravedad * Ocurrencia * Detección
Tenga en cuenta que las diferentes industrias y organizaciones tienen diferentes definiciones de «crítico». Por lo tanto, es tu equipo el que debe determinar qué es lo que se debe considerar como RPN para los modos de fallo crítico a los que se debe dar prioridad.
Sin embargo, debe evaluar las RPN no críticas para determinar su relación con otros sistemas y si existe la posibilidad de provocar un error en esos sistemas. También se debe dar prioridad a estos modos de fallo.
Paso 9: Desarrollar un programa de mantenimiento preventivo
Esta es la etapa en la que se centra en el objetivo principal de su programa de FMEA: mitigar los riesgos identificados mediante acciones basadas en datos. Desarrolle un mantenimiento proactivo programa para ayudar a minimizar el riesgo de falla de los activos. Siempre se debe dar prioridad a los modos de fallo con RPN altos.
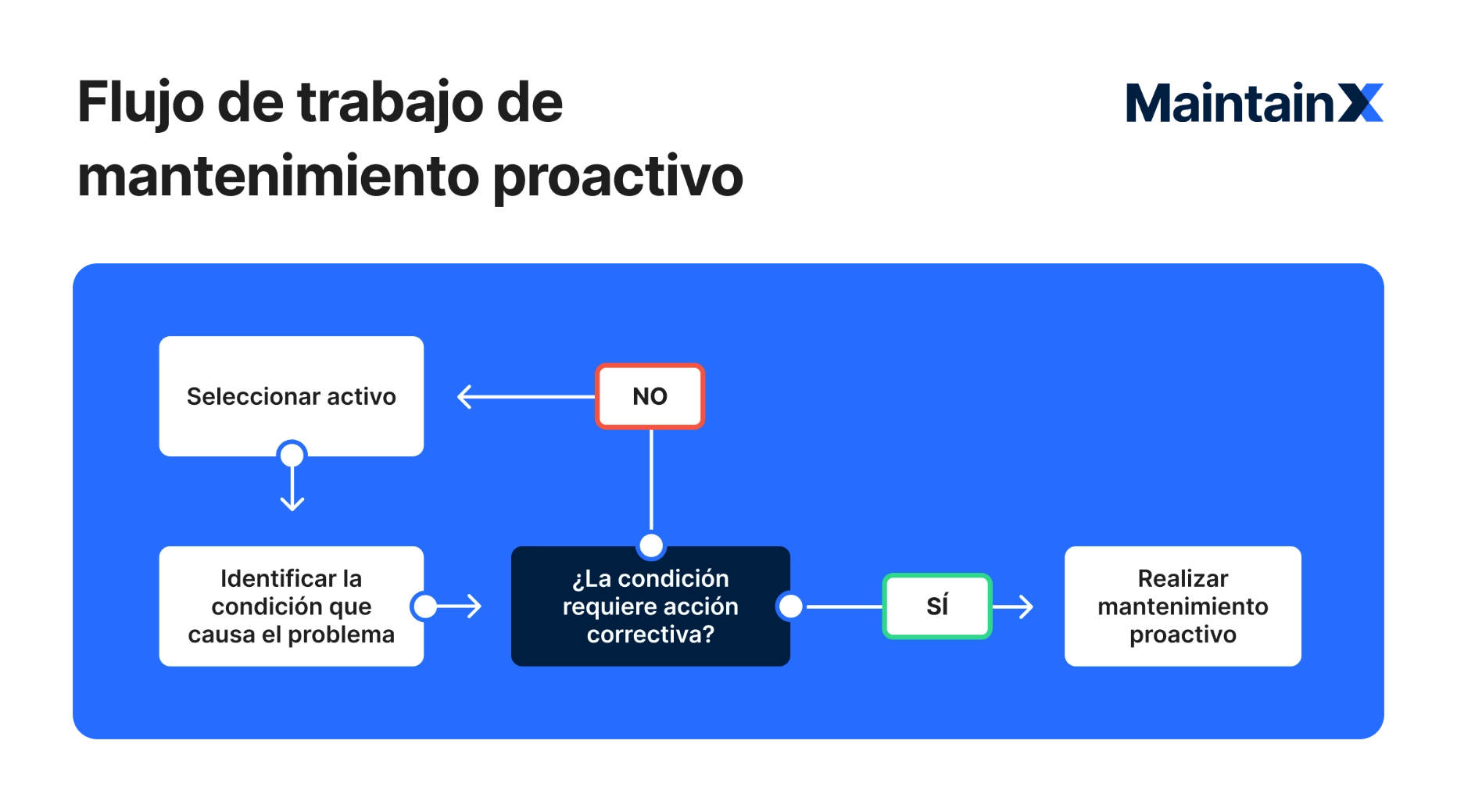
Como es imposible hacer frente a todos los posibles modos de fallo a la vez, concentre su energía en los que más afectan a la productividad, seguridad, y la satisfacción del cliente.
Recopile datos de mantenimiento y analice sus esfuerzos para determinar el curso de acción más adecuado para cada modo de falla. También puede realizar cambios en las funciones o considerar la posibilidad de introducir mejoras en los procesos y el diseño.
Además, dé prioridad a los activos con clasificaciones de gravedad altas, independientemente de si su RPN es bajo. ¿Por qué? Porque una clasificación de gravedad alta significa que la falla afectará significativamente a la productividad empresarial, la satisfacción del cliente y la seguridad.
Paso 10: Vuelva a calcular sus RPN
Por último, recalcule periódicamente sus RPN para ver si las acciones que implementó generan resultados. El grupo de trabajo debe volver a clasificar cada valor (gravedad, incidencia y detección) para calcular un RPN nuevo para cada modo de fallo y, a continuación, compararlo con el RPN anterior.
El objetivo es desarrollar e implementar continuamente nuevas estrategias que reduzcan las RPN hasta el punto de que ya no sea necesaria ninguna intervención. Por esta razón, el FMEA es un proceso continuo, no un evento aislado.
Ejemplo de proceso de FMEA
Este es un ejemplo rápido de un proceso de FMEA llevado a cabo para la instalación de un airbag en un vehículo:
Función: Instalación del airbag
Modo de fallo: El airbag está instalado de forma incorrecta
Efectos de falla: Mal funcionamiento del despliegue que provoca lesiones físicas al conductor
Clasificación de gravedad: 10
Causas del fracaso: Error humano
Clasificación de ocurrencias: 4
Controles de prevención: Inspeccione manualmente los airbags después de que el proveedor los entregue
Controles de detección: Use sensores para probar el funcionamiento del airbag después de la instalación
Clasificación de detección: 6
RPN: 240
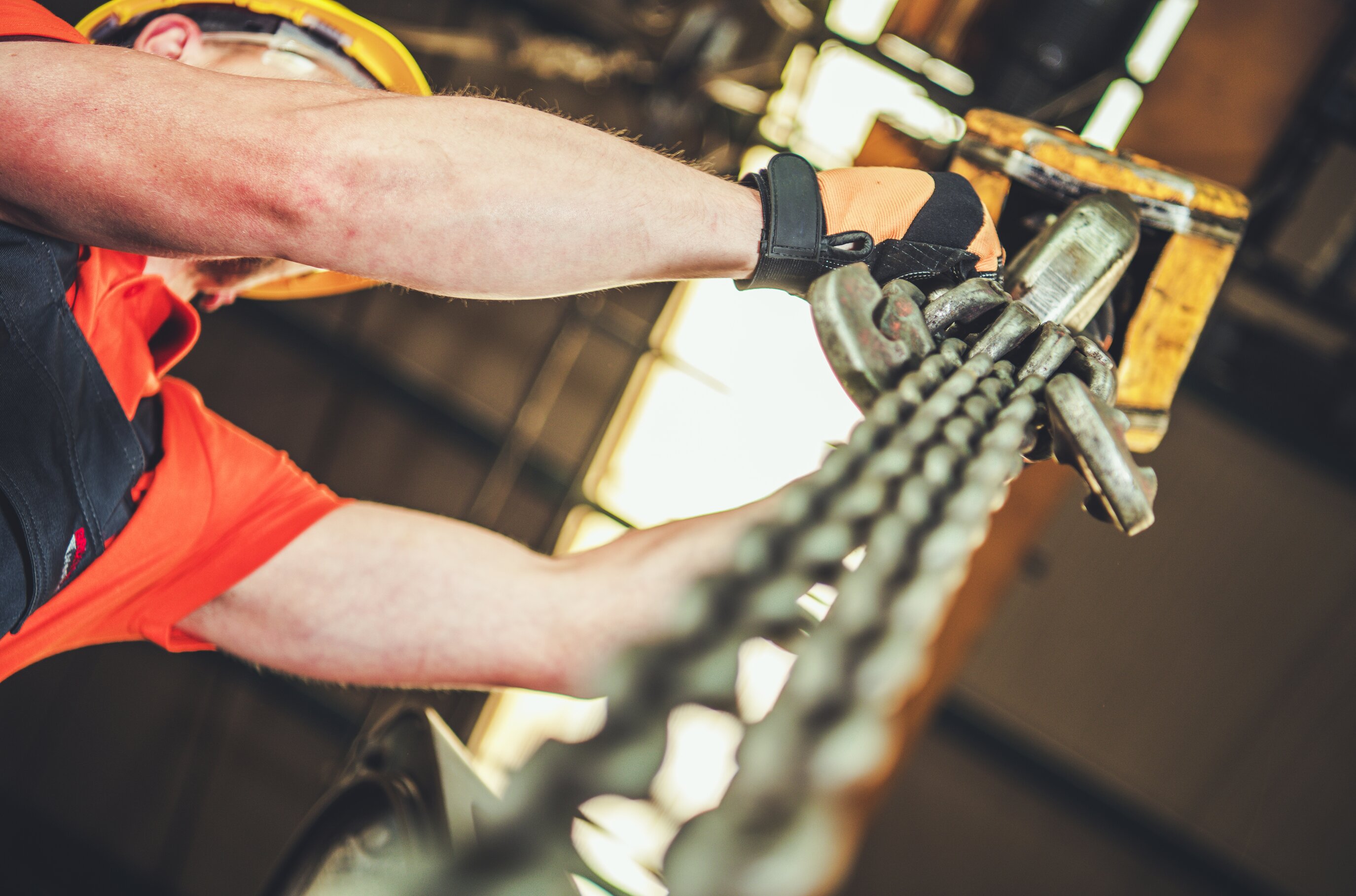
Obstáculos comunes con el FMEA
El FMEA es una herramienta poderosa para mejorar la confiabilidad del proceso y del producto. Cuando se lleva a cabo con precisión, se ha demostrado que ayuda a los líderes organizacionales a mitigar los riesgos, minimizar los plazos de desarrollo de los productos y salvaguardar el control de calidad.
Sin embargo, no todos los que emprenden un proceso del FMEA logran los resultados esperados. Algunas organizaciones se encuentran con los siguientes obstáculos comunes:
- Mala comunicación: Muchas empresas abordan el FMEA como un elemento de cumplimiento que debe tacharse de la lista de verificación. El hecho de no ver el FMEA como una herramienta para mejorar la calidad y la confiabilidad conduce a un proceso poco entusiasta sin ningún éxito real.
- Equipo ineficaz: Es probable que reunir un equipo de FMEA sin representación de partes del ciclo de vida del producto o proceso no sea efectivo. El equipo no tendrá un conocimiento suficiente de todo el ciclo de vida del producto o proceso. El FMEA es un proceso continuo que abarca todo el ciclo de vida del producto. Esto significa que hay que abordar todos los problemas, desde la fase inicial de diseño hasta el desarrollo, la fabricación y la implementación, para que el proceso sea un éxito.
- Documentos desorganizados: Algunos equipos, que se apresuran a completar el proceso, recopilan información y documentos al azar de manera desorganizada. Desafortunadamente, se convierten en víctimas de las fallas de sus propios sistemas cuando intentan revisar el progreso. La frustración, el agobio y la confusión les impiden volver a calcular sus RPNS y centrar sus esfuerzos en función de las necesidades.
- Confianza excesiva en la RPN: Por último, los equipos que se centran únicamente en las RPN sacan conclusiones inexactas sobre los modos de falla. Es mejor usar el RPN como punto de referencia general sin dejar de considerar el impacto de las puntuaciones individuales.
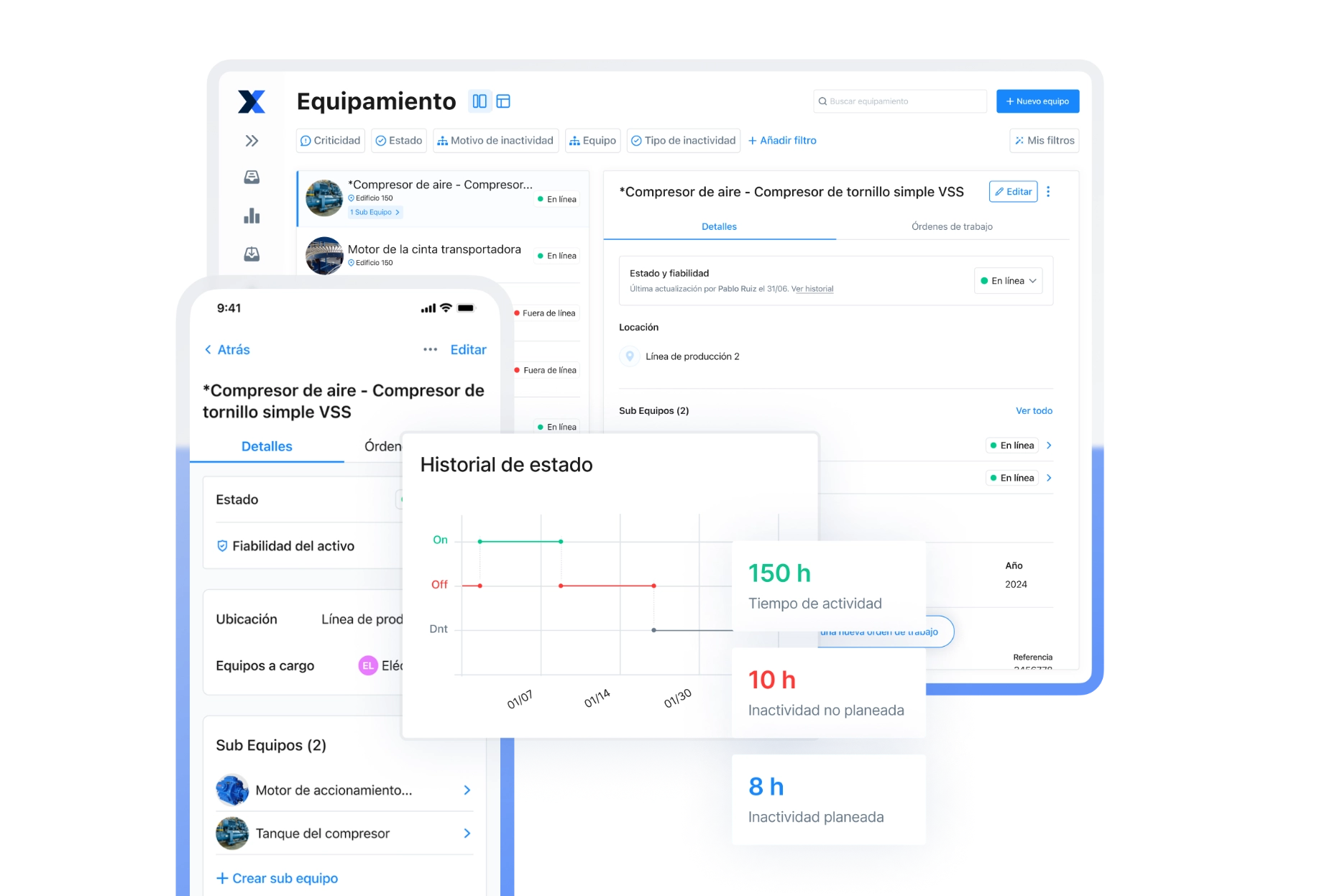
Optimice FMEA con MaintainX
Como hemos demostrado, el FMEA es una herramienta valiosa para las empresas que buscan aumentar la confiabilidad de los activos, priorizar las iniciativas de operación y mantenimiento y optimizar el diseño de los productos. ¿Cuál es la clave del éxito?
¡Implemente las recomendaciones que resulten de su grupo de trabajo y siga un proceso de revisión de datos periódico! El progreso no se logrará de la noche a la mañana, así que planifica revisar los RPN y los esfuerzos en equipo.
MaintainX permite a los equipos de fabricación compartir puntos de datos cruciales, mejorar la comunicación del equipo y obtener información a partir de informes avanzados fáciles de usar. Nuestro software de órdenes de trabajo recibe constantemente altas calificaciones por su usabilidad, exhaustividad y valor en los sitios de reseñas de terceros.
Pero no confíe en las palabras de nadie más: pruebe MaintainX usted mismo.
FAQs
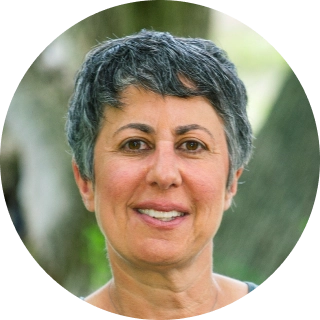
Caroline Eisner es escritora y editora con experiencia en los sectores con y sin fines de lucro, el gobierno, la educación y las organizaciones financieras. Ha ocupado puestos de liderazgo en instituciones de educación primaria y secundaria y ha dirigido proyectos digitales a gran escala, sitios web interactivos y una consultoría de redacción empresarial.