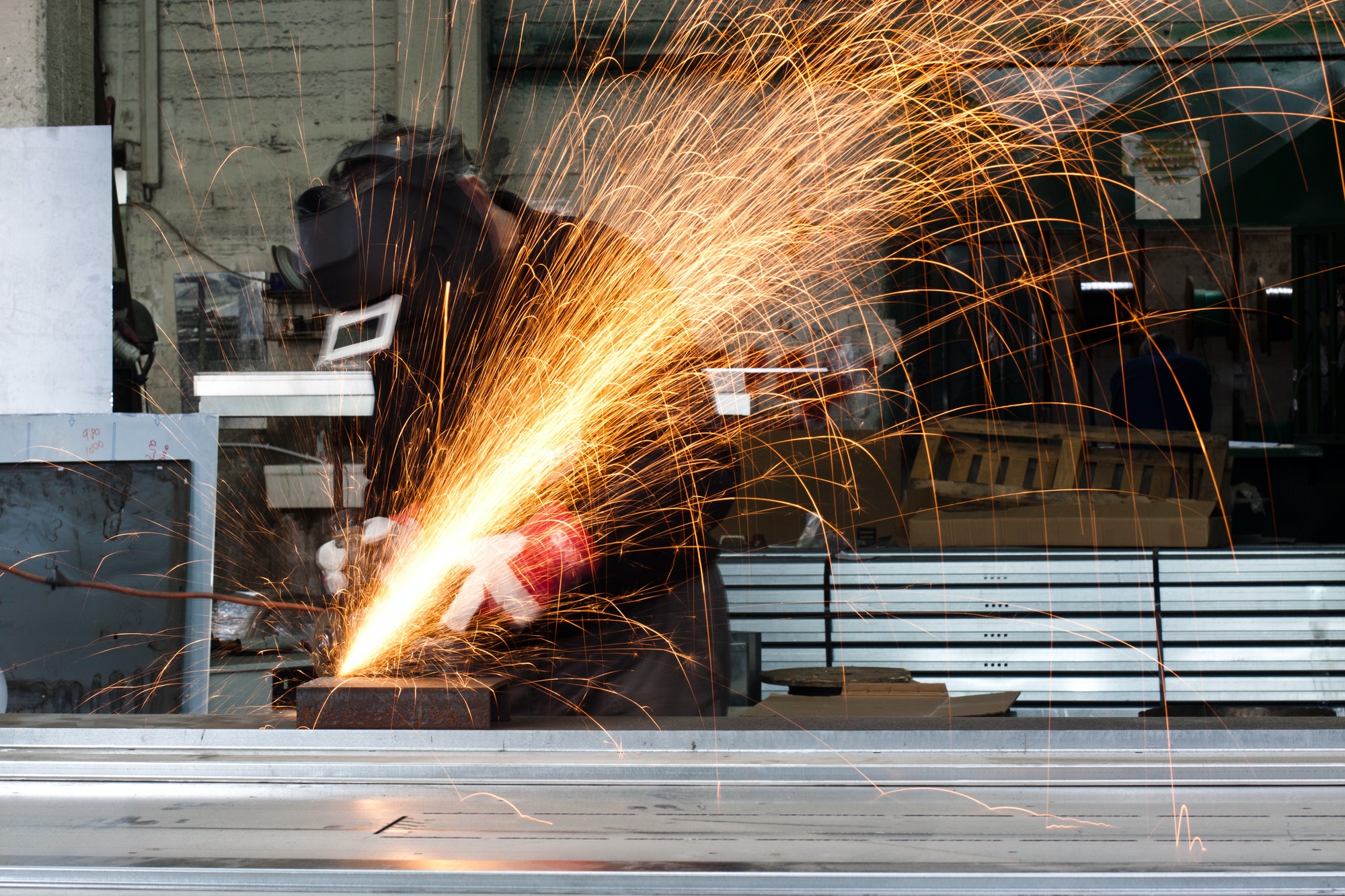
All commercial equipment, from a deep fryer in a commercial kitchen to a conveyor belt in a manufacturing facility, will eventually fail. Although a proactive maintenance plan can mitigate some failures, unexpected breakdowns can still happen, stalling production, distracting technicians from routine preventive maintenance tasks, and costing your organization serious money.
For these reasons, O&M (Operation & Maintenance) managers must take proactive measures to keep machinery running optimally, and understanding why equipment fails is the first step to managing unforeseen downtime.
Fortunately, by using robust maintenance management systems, employing skilled technicians, and taking advantage of connected technologies and software, you can heavily reduce the consequences of equipment failure in your organization.
In this article, we’ll discuss the four most common causes of equipment failure and how to prevent them. The reality is that you probably won’t be able to eliminate failure 100 percent, but you will know how to begin reducing its occurrence and impact on operations.
What is equipment failure?
Before diving into what causes equipment to fail, let’s get on the same page about what it is.
Equipment failure is a condition in which an asset or a machine does not work as it should—i.e. something is broken. Unexpected failures can have a significant impact on production schedules, customer satisfaction levels, and product quality.
Equipment failure is more costly than you think
While lost production time is the most obvious issue, the consequences of equipment failure are far-reaching:
- The cost of unplanned overtime for technicians
- Stand-down costs for machine operators
- The increased cost of urgently shipping spare parts from suppliers
- Wasted raw materials, such as perished food production ingredients that need to be discarded
- Defective products or a sharp increase in QA failures when equipment is underperforming
- Reduction in customer satisfaction levels and quality perception
- Lost business due to not meeting DIFOT targets or promised dates
- Opportunity cost due to excess resources being focused on repairing the asset
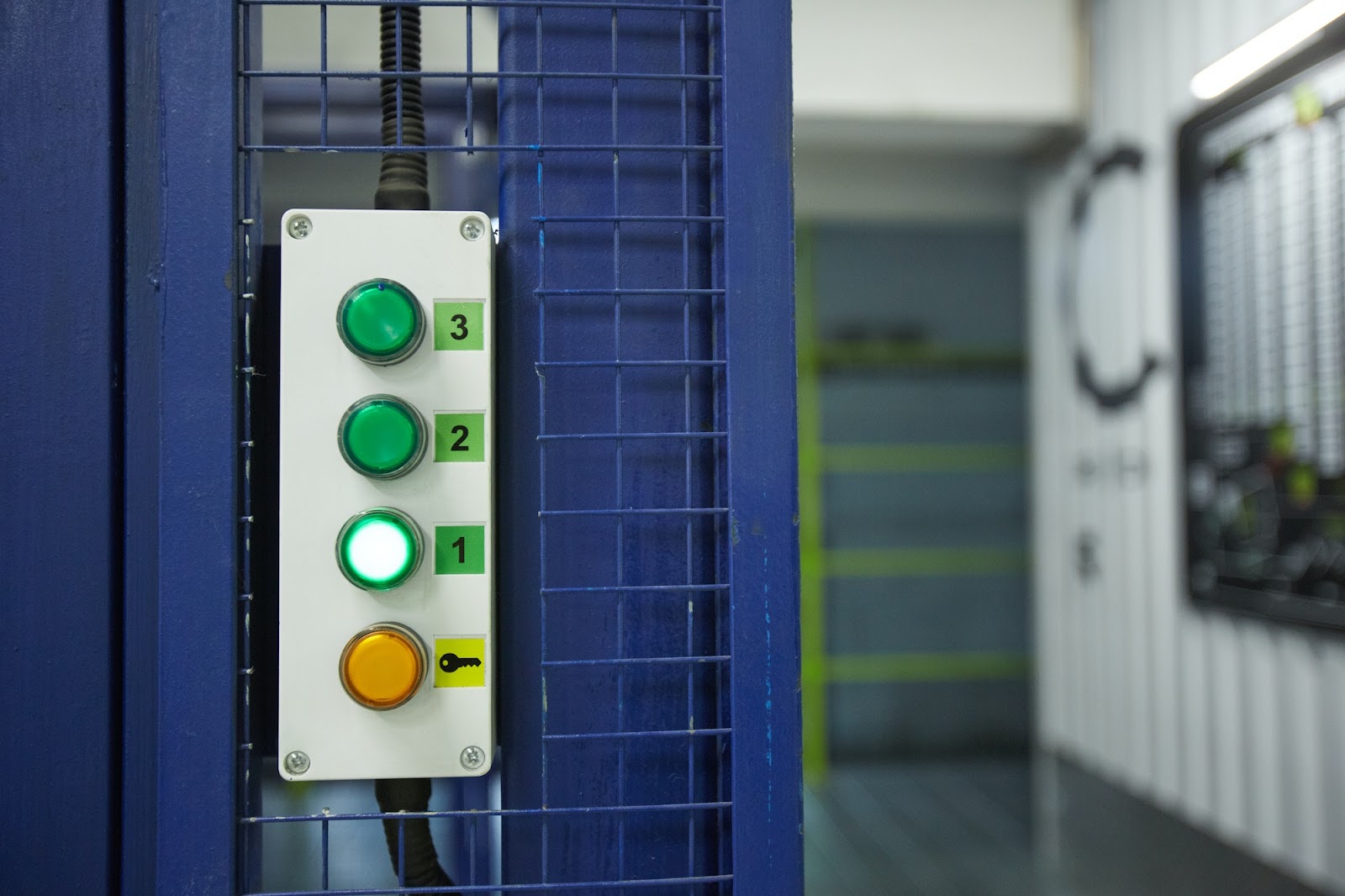
3 Types of equipment that fail
Regardless of the industry – agricultural, manufacturing, warehousing, energy and gas, or food service – equipment failure can happen to all types of assets. Failure in any of these categories can heavily impact operations:
- Powered equipment: These machines rely on fuel or electric motors to operate. Also known as heavy equipment, this category includes bulldozers, cranes, and forklifts.
- Mechanical equipment: Mechanical equipment usually includes moving components that work together to perform a specific task. Refrigeration units, condensers, extruders, conveyor belts, and air compressors are examples of mechanical equipment.
- Non-mechanical equipment: Non-mechanical equipment is generally smaller and lacks moving parts. Most hand tools fall into this category, including pipes, gas lines, electric panels, and HVAC system tools.
Now, let’s look at the most frequent causes of machine breakdowns.
The 4 common causes of equipment failure
Most types of equipment failure are caused by one of the four most common reasons:
- Aging equipment
- Operator error
- Lack of preventive maintenance
- Over-maintenance
Fortunately, all of these are preventable with the right processes, procedures, and technology in place.
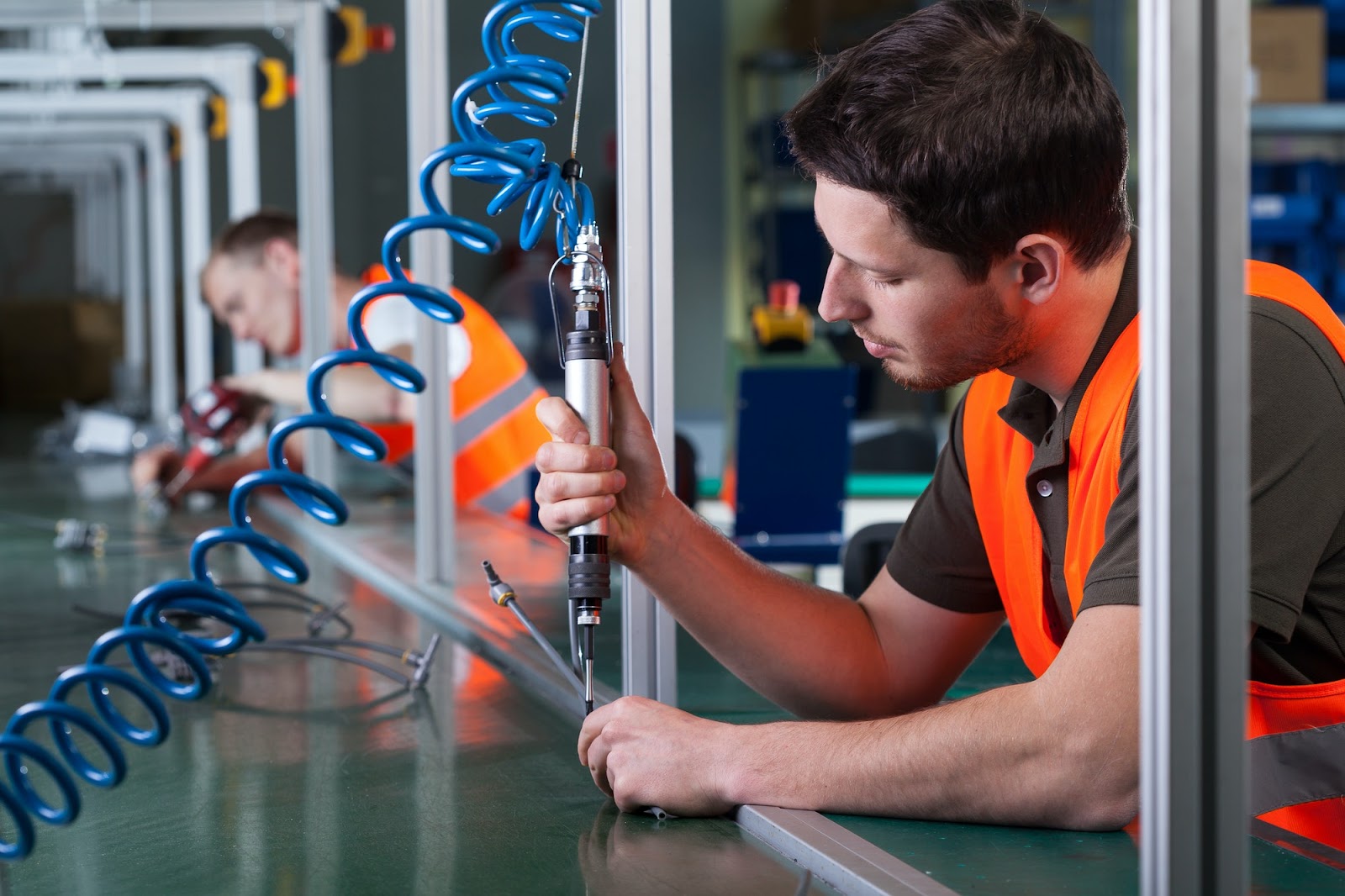
1. Aging equipment
According to the Plant Engineering Maintenance Study, aging equipment is the leading cause of equipment failure, accounting for 40 percent of unplanned downtime in plants.
Assets that consistently run year after year require more frequent repairs over time.
Unfortunately, this natural deterioration translates to more money spent on parts, inventory shipping fees, and production interruptions. It also requires technicians to switch from preventive maintenance (PM) to reactive maintenance more often.
Additionally, the more outdated an asset becomes, the harder it is to procure replacement parts. Since manufacturers generally produce lower quantities of old spare parts, managers of older equipment often have trouble securing what they need when they need it.
For these reasons, plants should consider allowing assets that have passed their useful life to run to failure. Though purchasing new machinery is undoubtedly expensive, most organizations will save money in the long run through less frequent repair expenses, increased production, and more efficient parts management.
2. Operator error
Another common cause of equipment failure is operator error – sometimes, machine operators make mistakes due to fatigue, forgetfulness, inexperience, or lack of training. According to the State of Industrial Maintenance 2024 report, 12% of respondents anticipated operator error to be a leading cause of unplanned downtime in the next twelve months.
Most plants prepare machine operators to properly run complex equipment with adequate training, readily accessible standard operating procedures (SOPs), and clear safety guidelines. However, it’s not unheard of for workers to occasionally work on unfamiliar machines when filling in for others.
An untrained operator may not have the specialized knowledge required to confidently run the machine. This could result in an equipment breakdown or a workplace accident, as well as breaching OSHA’s operator training requirements,
3. Lack of preventive maintenance
There’s a reason why world-class equipment maintenance programs predominantly practice preventive maintenance: it is proven to decrease costly equipment downtime. Studies suggest PM programs can reduce equipment failure by as much as 45 percent.
However, many managers still operate under the adage, “If it ain’t broke, don’t fix it.”
While run-to-failure maintenance is often the ideal strategy for older, non-critical equipment, a lack of planned inspections can lead to missing early signs of impending failure and depreciating performance.
Run-to-failure maintenance vs. preventive maintenance
Run-to-failure maintenance is a maintenance strategy in which maintenance activities are performed after a failure occurs. It’s a reactive strategy that allows an asset to break down before deciding whether to repair or replace it.
Also referred to as “breakdown maintenance,” this strategy is best suited for non-critical assets, inexpensive assets, and those with shorter lifespans. It’s also sometimes used for remote equipment, such as satellites, that are difficult to perform regular maintenance on.
However, run-to-failure maintenance should never be used for critical assets that impact production and safety.
The alternative approach—preventive maintenance (PM)—involves scheduling and performing recommended upkeep according to time or usage-based intervals. It’s a proactive strategy best suited for expensive equipment, critical assets, and components that are essential to employee safety.
Ultimately, organizations that solely practice run-to-failure miss out on solving minor issues before they become big problems. Additionally, frequently missed or delayed maintenance tasks, like periodic lubrication of equipment parts, can reduce an asset's lifespan and prompt the need for new capital purchases.
4. Over-maintenance
It may sound counterintuitive, but performing too much maintenance can also be detrimental.
Over-maintenance can speed up an asset’s depreciation by constantly taking apart and reconfiguring equipment components. This overzealous approach can disrupt even the most stable systems, causing them to become less effective.
Additionally, maintenance technicians may be more likely to “go through the motions,” viewing frequent tasks as yet another item to be checked off.
Over-maintenance also takes up unnecessary time that technicians could put to better use on other equipment.
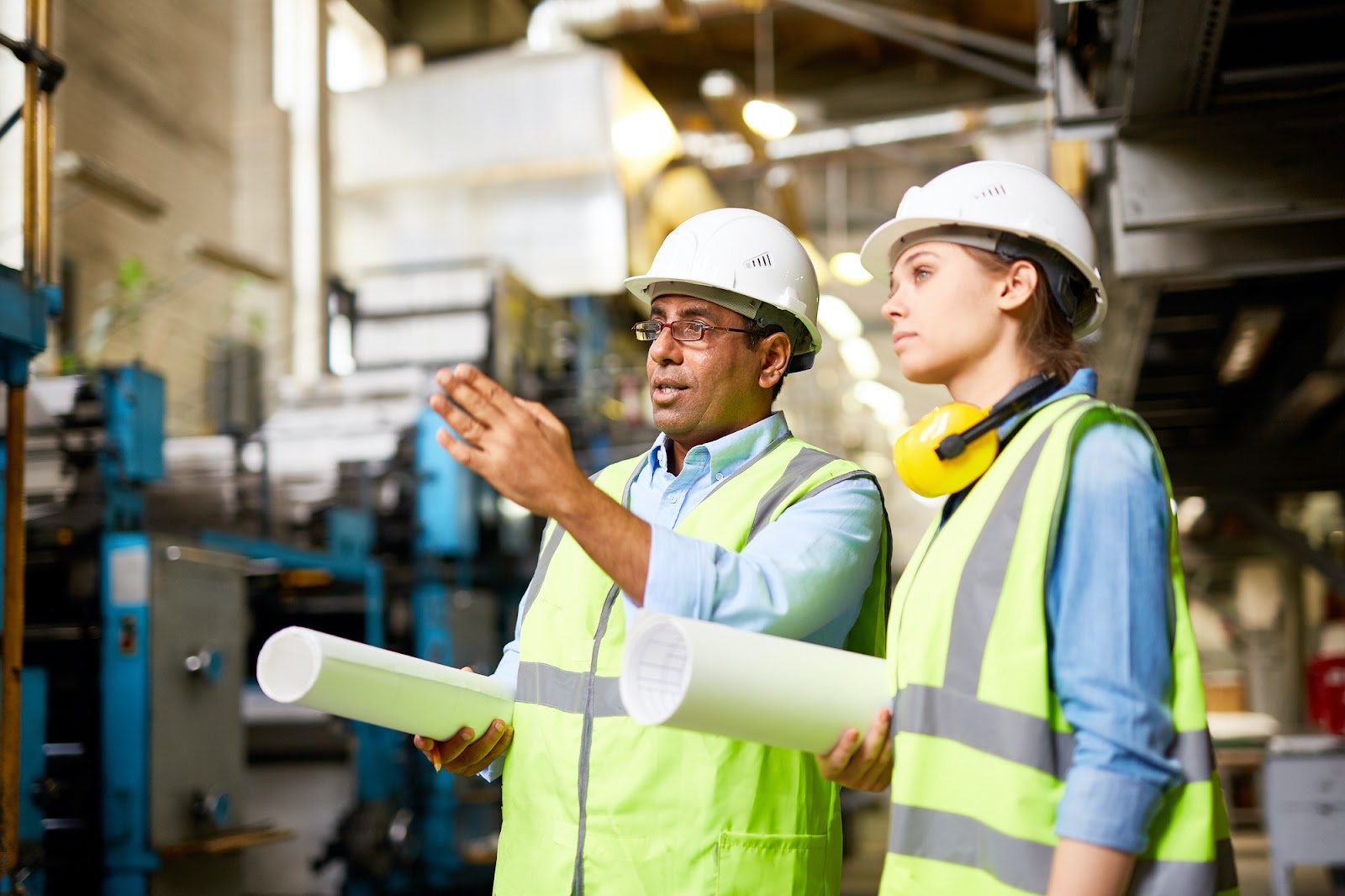
5 Ways to prevent equipment failure
As previously mentioned, equipment failure can be extremely costly, depending on the industry. The State of Industrial Maintenance 2024 found that “in 2024, the average cost of an hour of unplanned downtime hovers around $25,000 and can skyrocket to over $500,000 for larger organizations.”
Whether an equipment failure is gradual, intermittent, or sudden, it can usually be traced back to a root cause. Uncovering the original “falling domino” should be the ultimate goal of every manager wanting to increase operational reliability and reduce costly downtime.
Maintenance managers can use a variety of analysis methods to help pinpoint root causes. The 5 Whys, fishbone diagrams, and root cause analysis are just some of the deductive techniques commonly used within industrial maintenance departments.
Finding the root cause, however, is only part of the solution. Here are a few tips on how to prevent equipment failure to minimize the impact on your organization and your bottom line.
Provide thorough operator training & maintain compliance
Ensuring equipment operators receive adequate training can help minimize failures that stem from human error. Managers should also build redundancy into their operations by training workers how to use machines they don’t normally operate. That way, someone who has been properly trained according to OSHA standards will always be available.
Likewise, management must strictly enforce policies that prevent untrained employees from operating machinery.
Monitor & analyze equipment digitally
Monitoring asset health and insuring against failures becomes significantly easier when you invest in connected, IoT-ready systems. By connecting equipment meters and sensors to your computerized maintenance management system (CMMS), you can automate asset tracking and get a high-level view of all your assets on a single dashboard.
This remote condition monitoring allows your organization to tap into time and cost savings through early detection of unusual operating conditions before an asset breaks down.
Balance preventive with condition-based maintenance
Regular preventive maintenance (PM) activities help prevent failures and extend asset lifespans. On the other hand, condition-based maintenance (CBM) enables timely adjustments based on asset conditions (and before failure occurs).
Running both PM and CBM programs concurrently requires a robust database that ensures all equipment receives the exact amount of attention it needs at the right time. A mobile-friendly computerized maintenance management system (CMMS) like MaintainX provides AI-powered insights, scheduling, data management, and asset tracking to give maintenance managers a 360-degree view of their maintenance program.
Attach SOPs to work orders
Standard operating procedures (SOPs) ensure that equipment is properly maintained and serviced in the same way every time.
By allocating work orders to technicians with a pre-prepared SOP attached, maintenance managers can be sure that repairs, parts replacement, and other maintenance tasks are carried out effectively to reduce the occurrence of future breakdowns.
Run routine maintenance inspections
SOPs and checklists are also vital for routine maintenance activities and effective asset management. Checklists created in MaintainX help technicians easily conduct routine inspections, as well as create a “paper trail” for maintenance managers to analyze asset health and detect early evidence of anomalies – all from the convenience of an app.
Save time and money with MaintainX
You can’t always outrun equipment failure, but you can minimize its impact. MaintainX’s CMMS can help keep your maintenance team one step ahead of inconvenient breakdowns – and swiftly get machines back online when failures do occur.
MaintainX helps your organization mitigate expensive equipment failures with tools and systems to manage proactive and reactive maintenance. Minimize downtime and maximize productivity with a user-friendly CMMS that lets you monitor asset health in real-time, assign work orders at speed, and track equipment history to stay ahead of issues.
Equipment failure FAQs
How long does it take to implement MaintainX?
For the average customer, it takes three weeks to implement one site. For customers on our Premium & Enterprise plans, our team ensures a smooth transition to MaintainX within your organization. Partner with a dedicated implementation specialist through our structured three-week onboarding process. Learn more about our Implementation services here.
Is MaintainX secure?
MaintainX is compliant with security standards, including SOC 2, ISO 27001 & GDPR. It also supports Single Sign-On (SSO), multi-factor authentication (MFA) and custom permissions and roles. For more information, visit our Trust Center page.
Does MaintainX support multiple sites?
Yes, MaintainX Enterprise allows you to manage multiple plants or facilities within the same platform. You can also create customized reporting dashboards to track KPIs across multiple sites on the same screen.
What industries are most affected by equipment failure?
Almost every industry, from food production to auto manufacturing, can experience disastrous asset failures. A supermarket’s refrigeration system is critical to operations, just as a car manufacturer’s robot welder is vital to keeping production on track.
What are the warning signs of impending equipment failure?
Intermittent faults, physical degradation, such as cracked housings, excessive vibration, leaking fluids, a build-up of contaminants, and unusually high temperatures are common signs that something is awry with mechanical equipment. Unusual noises and an unexpected increase in production run time can also be early indications that inspection or maintenance is required.
What should be included in an equipment failure response plan?
Equipment failure planning starts with safety, so ensure that equipment is isolated, locked, or tagged out and operators are aware of the breakdown. Repair technicians can respond swiftly by having set procedures in place for breakdowns. Standard operating procedures should include steps to inspect the equipment, a clear repair process, how to expedite spare parts, and how to mitigate the impact on day-to-day production.
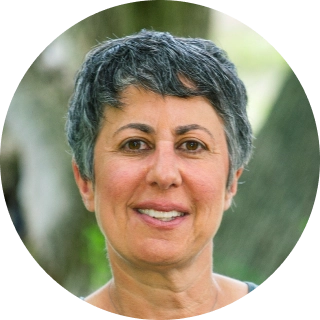
Caroline Eisner is a writer and editor with experience across the profit and nonprofit sectors, government, education, and financial organizations. She has held leadership positions in K16 institutions and has led large-scale digital projects, interactive websites, and a business writing consultancy.