To prepare for an OSHA Inspection, you need to know what to expect. The best organizations prepare for the unexpected.
The simplest approach: create an operational culture that encompasses OSHA (Occupational Safety and Health Administration) policies.
The idea is similar to the concept of having a three-day emergency preparedness kit in your home. Granted, there’s a low probability of a disaster ever occurring that requires your kit. However, you’ll be glad you made an effort if it makes the difference between life and death when there’s imminent danger.
OSHA Inspections
Unlike low-probability natural disasters, OSHA-related accidents happen daily across the country, with an average of 14 workplace fatalities occurring every day.
Like-minded business owners also see the wisdom of being prepared for OSHA on-site visits, with or without advanced notice. And to be fair, worksite and workplace safety, PPE (personal protective equipment), and other Department of Labor requirements aren’t just about not wanting to receive OSHA citations, they also are about making sure your employees are safe from physical harm while on the job.
This post does not propose any trade secrets to get you through an inspection. We simply want you to avoid any workplace violations stemming from potential hazards, poor working conditions, health hazards, and/or employee complaints.

Should You Be Concerned about OSHA Inspections?
It depends. Yes. And maybe.
For the most part, OSHA applies to any business with more than ten employees. Those businesses are required to meet OSHA standards and maintain appropriate records.
When it comes to exemptions from OSHA, there are general exclusions tacked onto the less than ten employees' disqualification.
Generally speaking, OSHA exclusions and exemptions include churches, federal and state-level government organizations, and their political subdivisions. Businesses that are regulated by federal statutes (ex., mining and nuclear power companies) tend to also be exempt.
If you have less than ten employees and meet the above exemptions, then you might not need to worry about getting an inspection.
Why the uncertainty? OSHA doesn’t have a limitless roster of inspectors to carry out limitless workplace inspections. And the OSHA inspectors that they do have already manage about 100,000 inspections a year.
There are roughly 8-10 million OSHA-regulated businesses in the US, so there is a ~1% chance your business is selected for one of the 100,000 inspections.
That said, just as you would immediately regret not having an emergency preparedness kit if a disaster strikes, it pays to be prepared. Plus, OSHA regulations are in place for a reason—keeping your employees safe should be a priority even without the threat of legal liabilities.
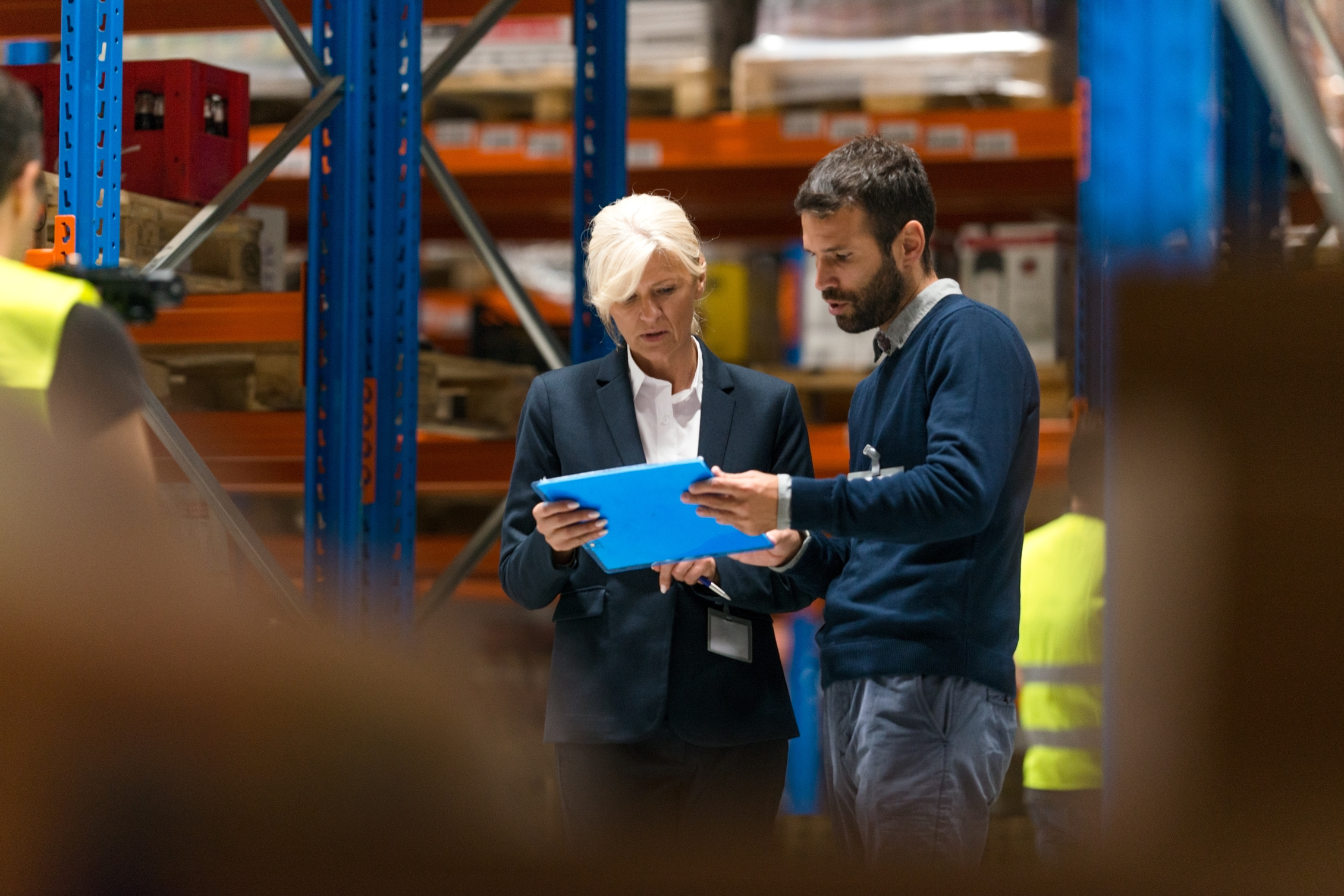
6 Steps to Prepare for the OSHA Inspection Process
Suppose your business falls under the purview of OSHA regulations. In that case, you need to have an accessible recordkeeping system in place to maintain reports of compliance safety, previous on-site inspections, past OSHA violations, and information regarding safety programs and safety training your company offers. In the event of an inspection, you’ll thank yourself for making the effort.
Here we detail six ways you can be ready and prepared if an inspection comes knocking on your door. If you want more information about OSHA or the Occupational Safety and Health Review Commission, visit OSHA's website.
1. Establish Key Points of Contact
It’s imperative that you chose and designate key points of contact before an inspection. This person should be intimately familiar with your business’s inspection protocols and recordkeeping. Without this person, you’ve already significantly lowered your chances of passing inspection. An employee representative can be a key point of contact and should be someone who understands the scope of the inspection.
This person should be extremely professional, calm under pressure, and able to maintain composure should the inspector ask tough questions.
Your key contact needs to be familiar with the OSHA inspection process, particularly with the rules that apply to your industry and processes.
It’s also the responsibility of your contact person to make sure your team is aware of their rights when being interviewed.
It’s a good idea to have a backup or assistant contact in place who is also familiar with your records and the general inspection process in the event an inspector arrives when your key contact isn’t there or available.
2. Put a Response Team in Place
Readiness should include having a response team in place.
This response team can be made up of two or three people who want to be involved and responsible for understanding inspection processes.
This team needs to have a solid understanding of your company’s compliance practices and standards so they can help enforce them throughout your company.
This team will likely include your ‘backup’ key contacts so that they can be ready to jump into action should an inspector come knocking.
3. Maintain Your Professionalism
Professional behavior should be common sense, but unfortunately, inspectors are frequently treated with hostility and disrespect.
Being rude or argumentive lowers the chance of you passing your inspection. Make sure your contact and response personnel—and frankly, everyone else too—can maintain a professional demeanor at all times.
If, during the course of the inspection, you enter areas where protective gear is necessary, politely ask the inspector to suit up. This is a good way to show that your company pays attention to and maintains compliance with safety standards at all times.
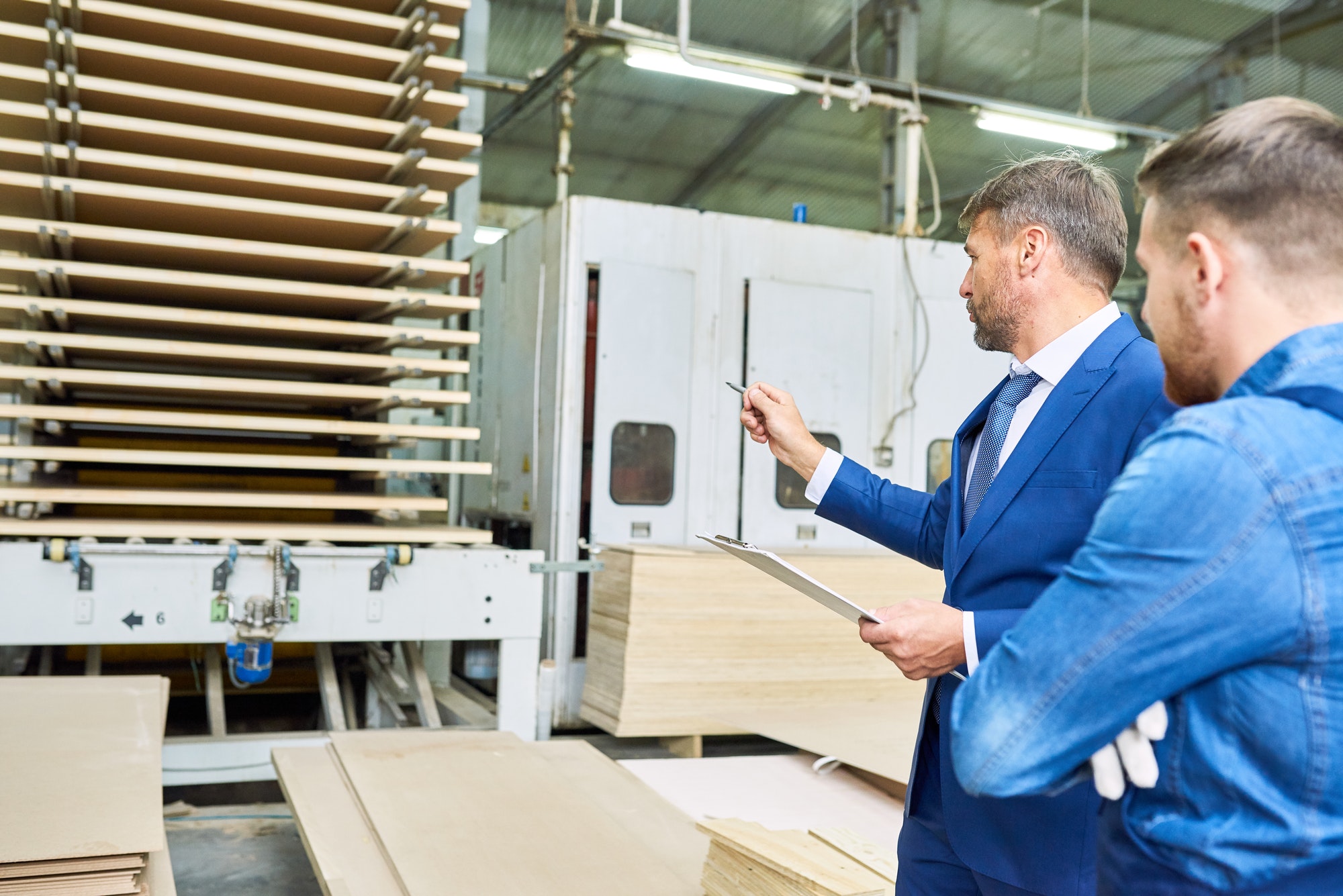
4. Make the Right Information Available
Members of your contact and response teams must be able to provide the needed information and answer any questions.
Important information could include:
- General information about your business—including the number of employees, products/services produced, materials used, etc.
- The names and contact information for management personnel – managers, supervisors, etc.
- Employee injury and illness logs.
- Inspection processes and procedure records.
The above criteria are the bare minimum that you should expect to procure for an inspection. Being able to quickly retrieve your inspection history with an audit trail of dates will go a long way toward leaving a positive impression and passing the inspection.
5. Plan a Predetermined Walk-Around Route
There’s a good chance the inspector may want to inspect a certain part of your plant and/or specific machines and equipment. Your key contact needs to have a planned walkthrough route ready and know what they will be showing.
However, the inspector is within their rights to pick and choose what to look at and where to go. If they do have specific objectives in mind, it’s important to be equipped to answer any questions they may have or have a nearby resource who can go into any pertinent details.
6. Have Your Records Available
If you are using software like MaintainX, your organization’s records will be available at your fingertips and easily exportable. With MaintainX, you can create digital versions of your inspections and checklists that can be completed by your team.
Be sure to have your records on leading indicators, workers’ compensation, safety, insurance, and general liability easily accessible and available. It helps to show your readiness and compliance.
OSHA Inspection Checklists
There’s a vast number of OSHA inspection checklists and regulations covering a variety of issues. To give an example of what they look like, we have shared one below.
We’ll just cover one here but note that MaintainX is a great way to create your own custom checklists using the exact OSHA rules and regulations.
OSHA Forklift Inspection Requirements
Safety and Operational Checks for Gas/LPG/DieselTrucks & Forklifts (Prior to Each Shift)
Engine-Off Checks
- Leaks: Fuel, Hydraulic Oil, Engine Oil, or Radiator Coolant
- Tires: Condition and Pressure
- Forks, Top Clip Retaining Pin, and Heel: Check Condition
- Load Backrest: Securely Attached
- Hydraulic Hoses, Mast Chains, Cables, and Stops: Check Visually
- Overhead Guard: Attached
- Finger Guards: Attached
- Propane Tank (LP Gas Truck): Rust Corrosion, Damage
- Safety Warnings: Attached (Refer to Parts Manual for Location)
- Battery: Check Water/Electrolyte Level and Charge
- All Engine Belts: Check Visually
- Hydraulic Fluid Level: Check Level
- Engine Oil Level: Dipstick
- Transmission Fluid Level: Dipstick
- Engine Air Cleaner: Squeeze Rubber Dirt Trap or Check the Restriction Alarm (if equipped)
- Fuel Sedimentor (Diesel)
- Radiator Coolant: Check Level
- Operator’s Manual: In Container
- Nameplate: Attached and Information Matches Model, Serial Number, and Attachments
- Seat Belt: Functioning Smoothly
- Hood Latch: Adjusted and Securely Fastened
- Brake Fluid: Check Level
Engine-On Checks: Unusual Noises Must Be Investigated Immediately
- Accelerator or Direction Control Pedal: Functioning Smoothly
- Service Brake: Functioning Smoothly
- Parking Brake: Functioning Smoothly
- Steering Operation: Functioning Smoothly
- Drive Control–Forward/Reverse: Functioning Smoothly
- Tilt Control–Forward and Back: Functioning Smoothly
- Hoist and Lowering Control: Functioning Smoothly
- Attachment Control: Operation
- Horn and Lights: Functioning
- Cab (if equipped)–Heater, Defroster, Wipers: Functioning
- Gauges–Ammeter, Engine Oil Pressure, Hour Meter, Fuel Level, Temperature, Instrument Monitors: Functioning
OSHA also provides brochures and fact sheets on nearly every type of equipment. For example, if you need info on an OSHA crane inspection, let Google be your friend. A quick Google search will bring up pages like this with fact sheets, flow charts, safety tip sheets, cards, and more.
Be Prepared to Put Employee Safety First
While the focus of this article has centered around preparing your business to comply with federal regulations and inspections, it is important to remember why this exists. OSHA was put in place to stem the increasing rates of workplace injuries and fatalities that surged in the 1960s. Since its inception, the U.S. occupational injury rate is 40 percent lower, and deaths from occupational injuries are at an all-time low—60 percent lower than 30 years ago.
These well-intentioned rules can help keep your employees safe and productive to enable long-term business success. And, if you end up with a list of alleged violations and abatement dates, follow up with your OSHA compliance officer.
Download MaintainX safety audit software for iOs, Android, or desktop.
FAQs
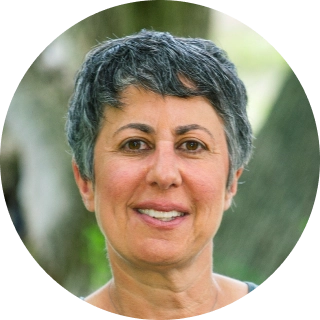
Caroline Eisner
Caroline Eisner is a writer and editor with experience across the profit and nonprofit sectors, government, education, and financial organizations. She has held leadership positions in K16 institutions and has led large-scale digital projects, interactive websites, and a business writing consultancy.