Manufacturing Maintenance Software
Maintenance software for manufacturing plants
The most trusted manufacturing software for maintenance and asset management. Streamline manufacturing operations and manage your assets in one easy to use platform. Drive key metrics like asset availability, MTTR, and MTBF by adopting a modern approach to work planning and execution.
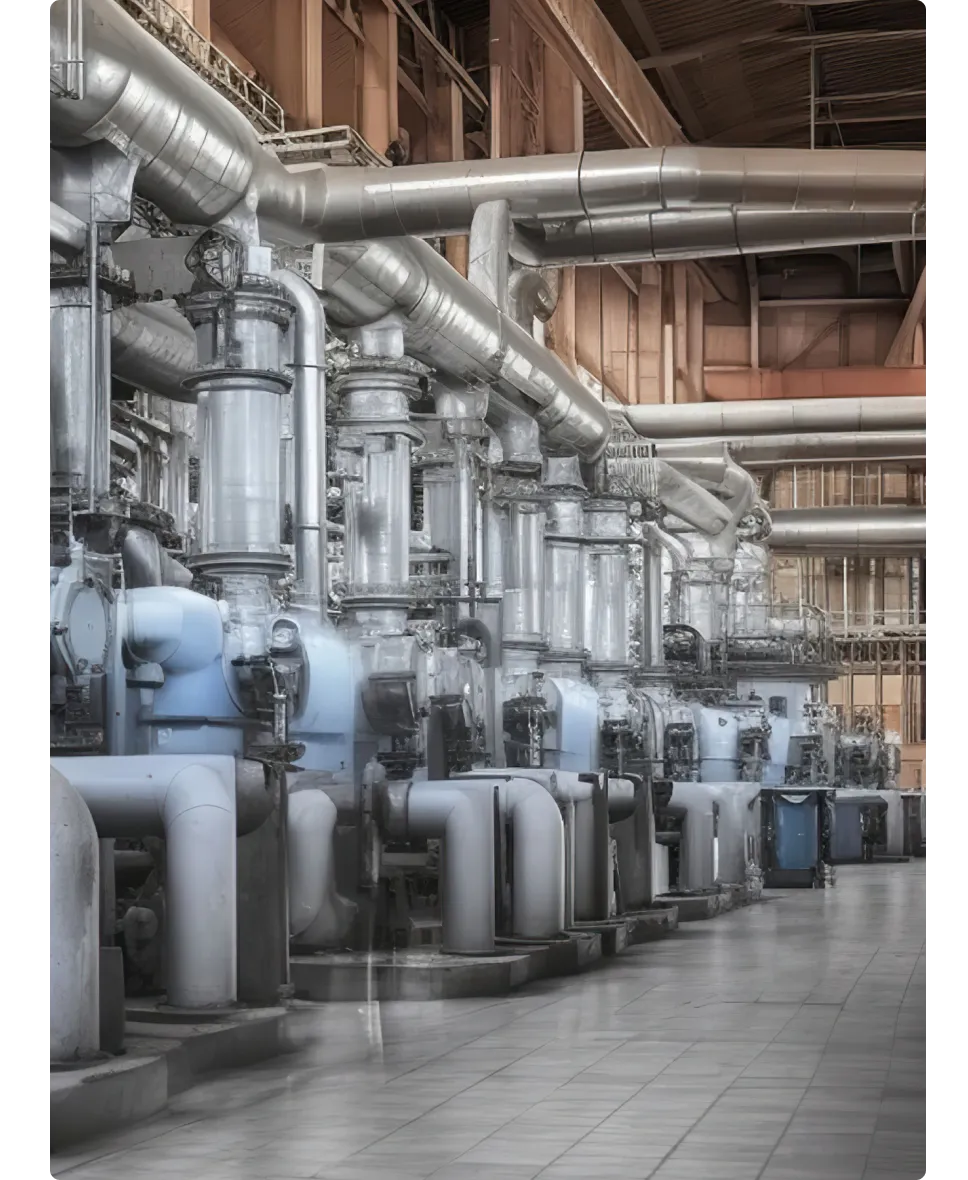
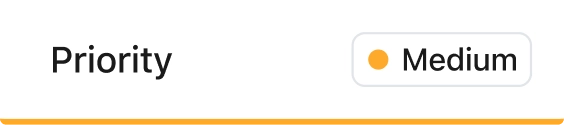
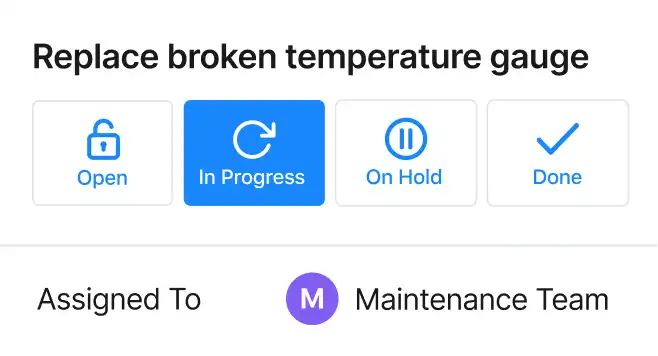
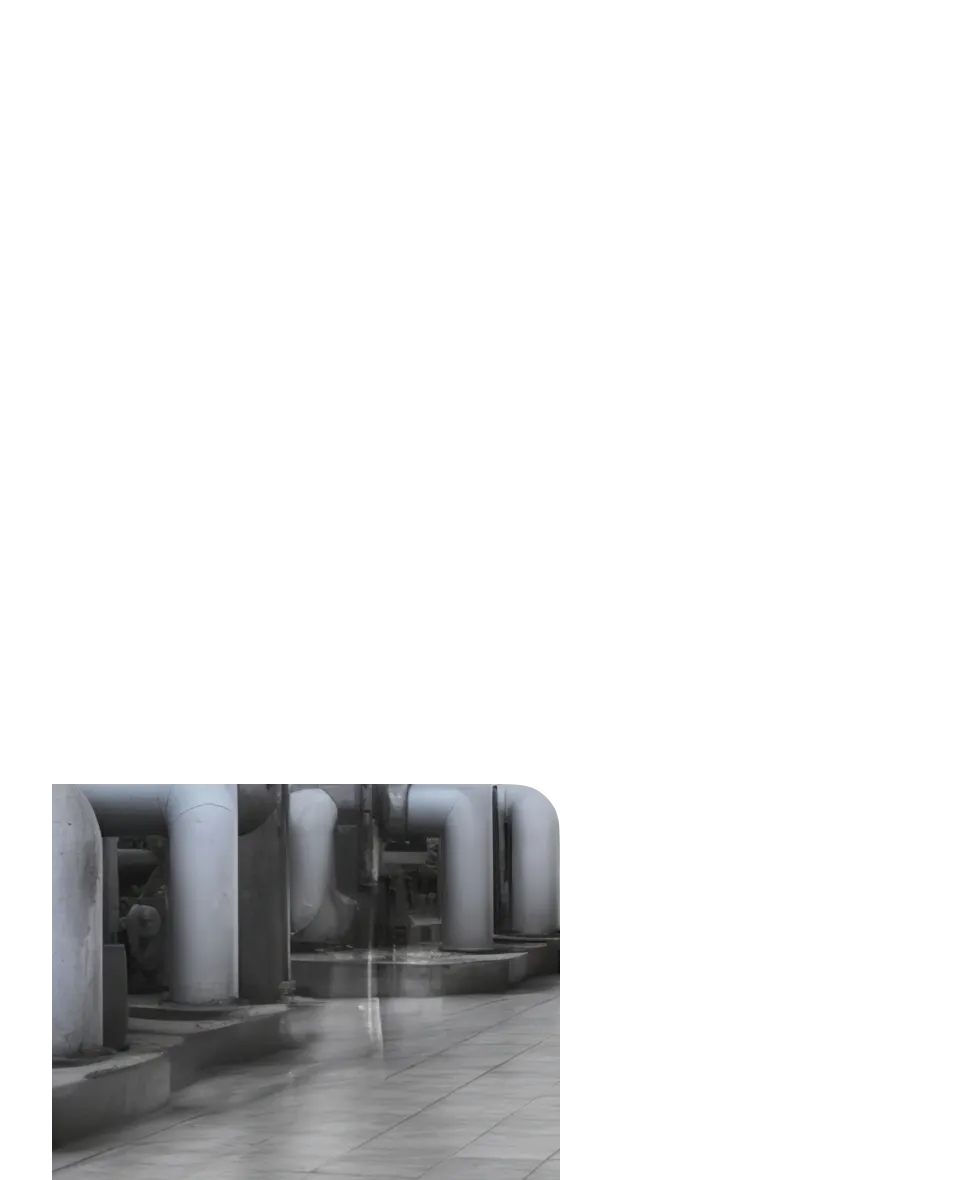
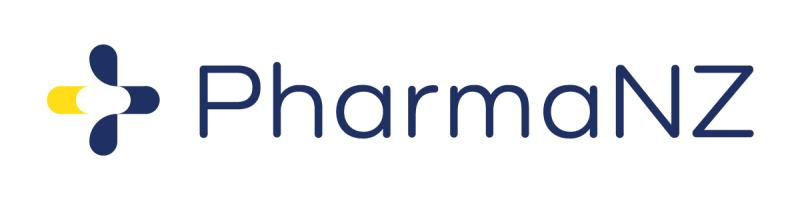
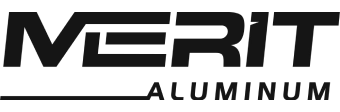
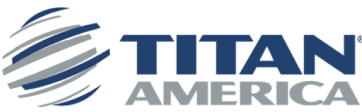
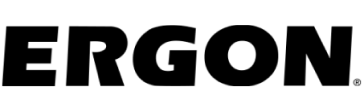
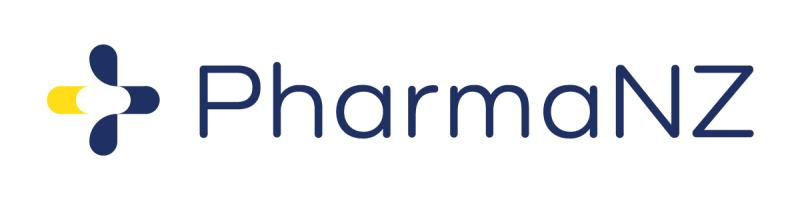
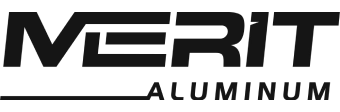
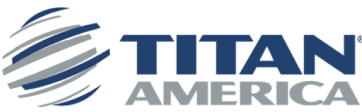
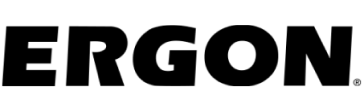
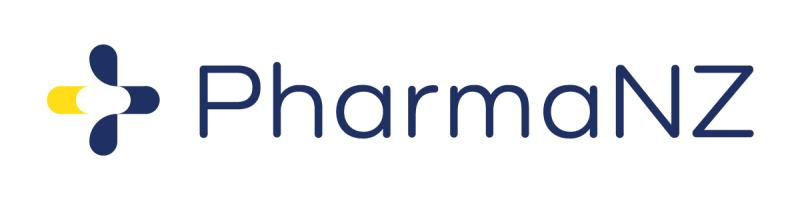
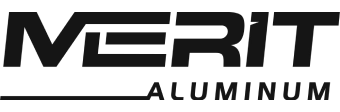
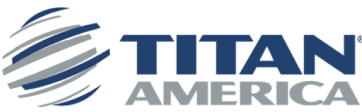
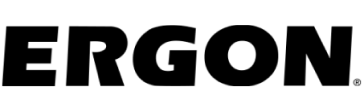
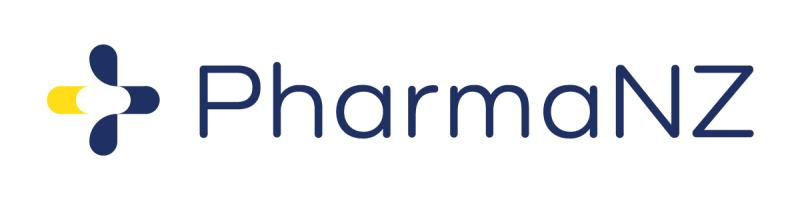
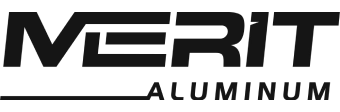
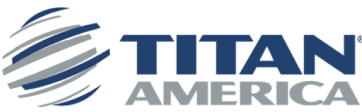
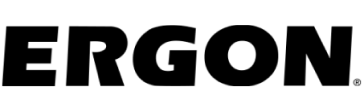
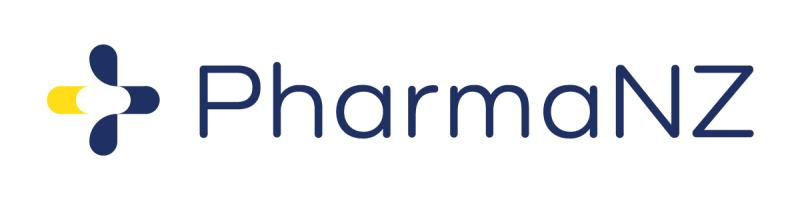
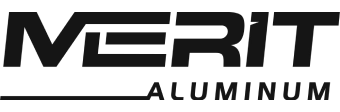
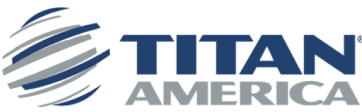
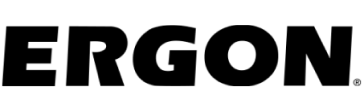
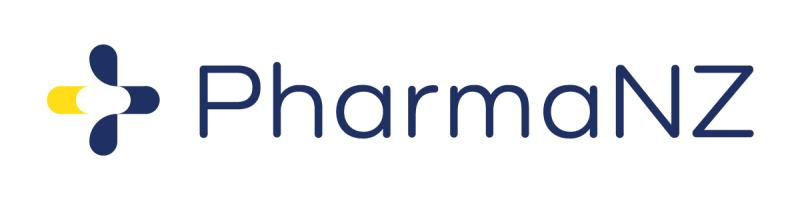
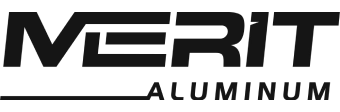
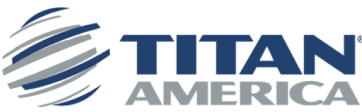
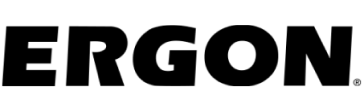
MaintainX is the #1 CMMS for manufacturers
Increase workforce productivity
Empower manufacturing teams with a modern, all-in-one app. Make data-driven decisions to prioritize work, allocate budget, and more.
Improve asset reliability
Save time and control costs by making repairs faster, avoiding last minute parts restocks, and consolidating technology systems.
(mean time to repair)
Boost operational efficiency
Maximize plant production capacity by reducing downtime and unexpected breakdowns.
Frost & Sullivan ‘25 tech innovation recognition
MaintainX recognized for leading AI-powered maintenance and asset optimization in North America.
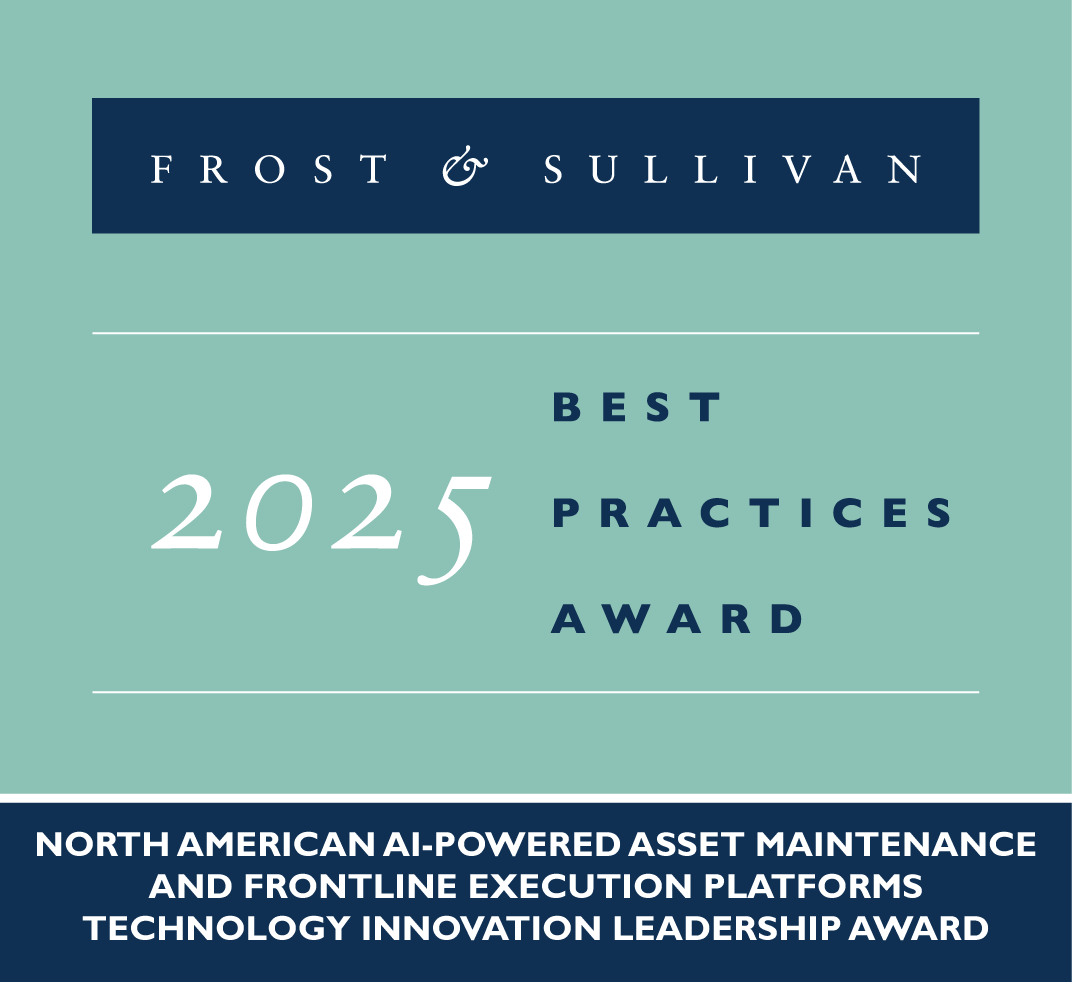
Maximize production capacity with preventive maintenance
Get ahead of costly equipment breakdowns with preventive maintenance plans. Build custom procedures, schedule PMs, and trigger Work Orders automatically based on meter readings, IoT data, and more. Track PM compliance to ensure maintenance is being completed on time.
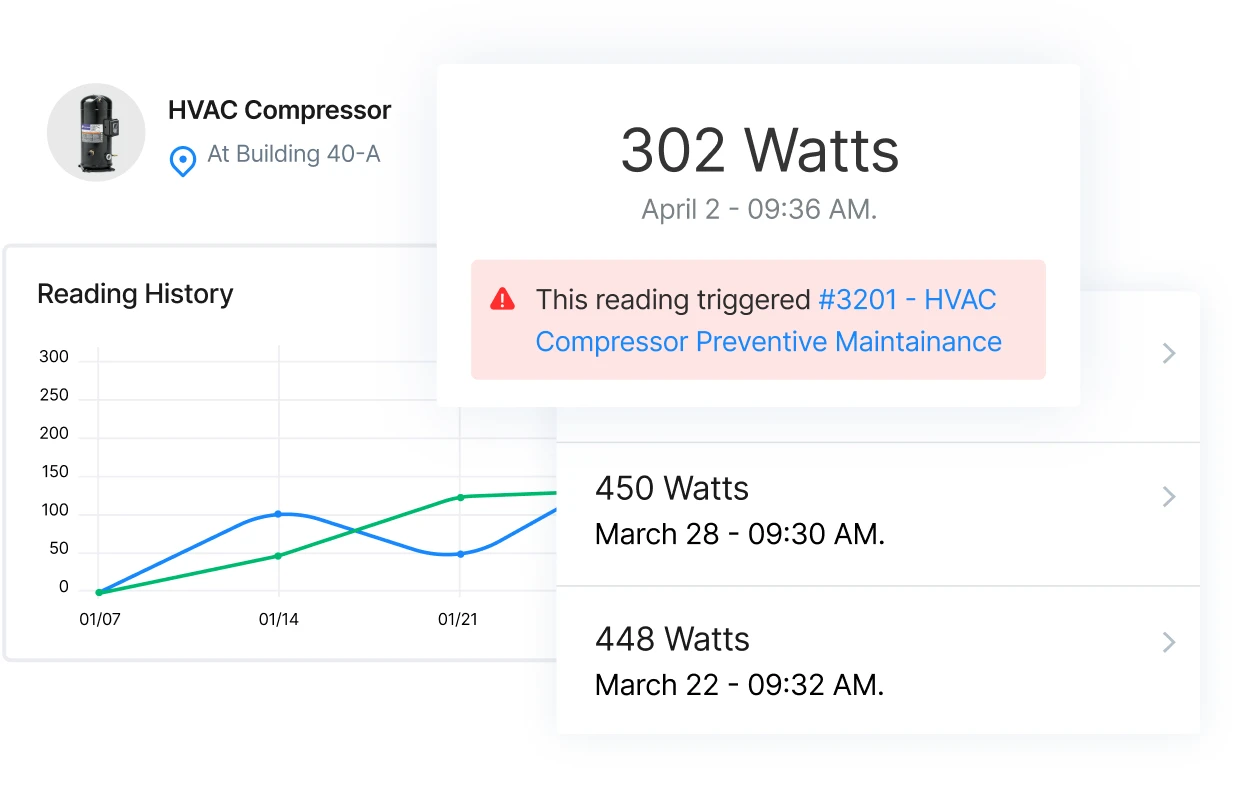
Minimize downtime with reactive work order management
When a machine goes down, your team needs to react quickly. Get a full picture of asset status across all your plants. Quickly understand assets that need maintenance work and assign Work Orders to your field technicians. Track progress in real-time as the maintenance work is started, paused, or completed.
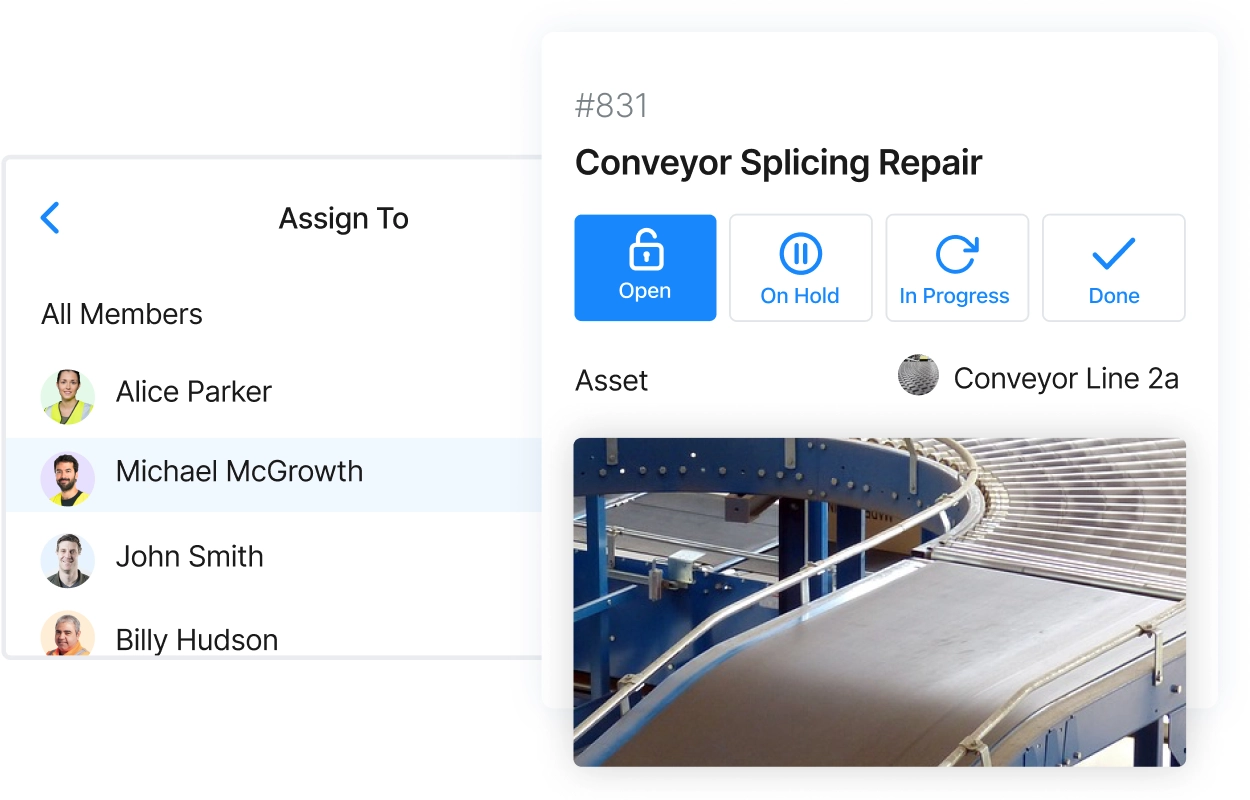
Get ahead of audits with work history you can see and search
Never get caught unprepared for another audit. Easily build, maintain, and access a full maintenance log and audit trail. Sort work history by location, assets, teams or users to quickly drill down to specific records.
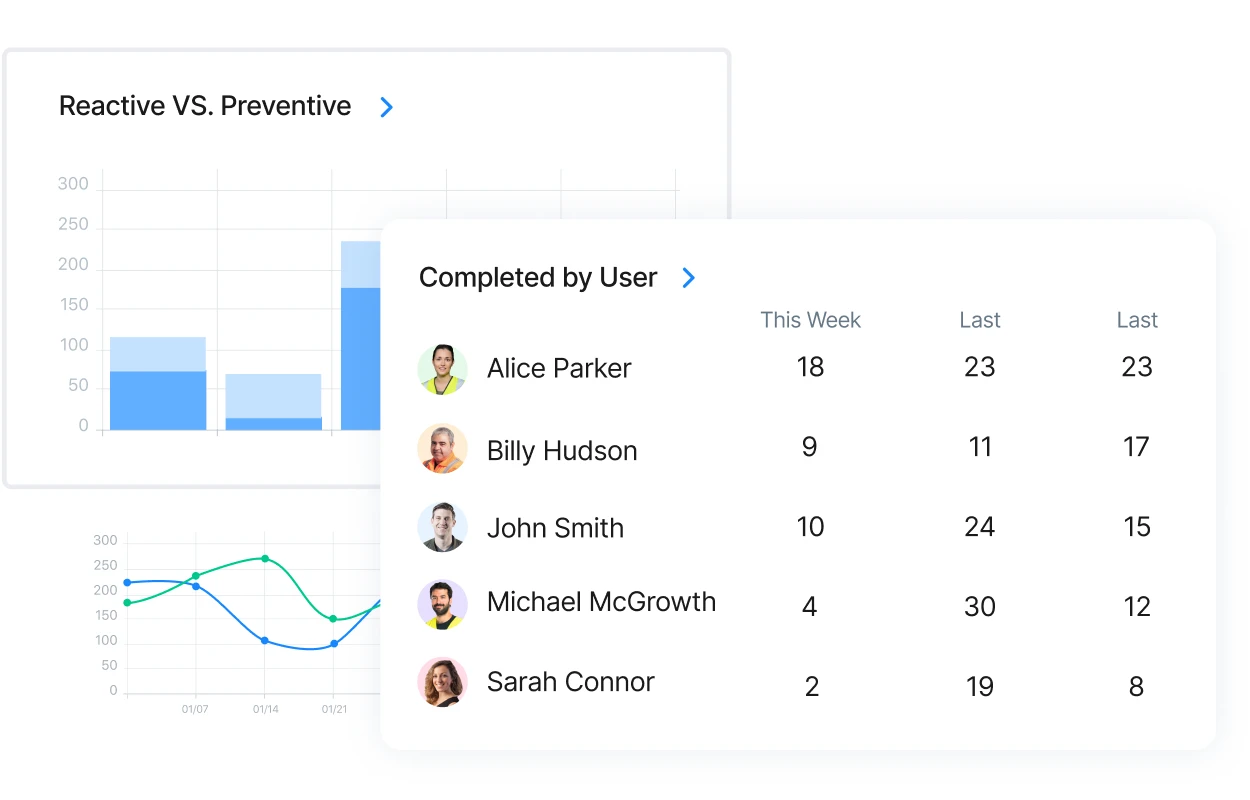
Limit costs with seamless parts inventory management
Keep the right inventory in stock at all times. Perform cycle counts to keep physical and digital inventory in-sync, manage parts inventory in one central location, get alerts when stocks run low, and streamline the purchasing process to keep critical parts on the shelf.
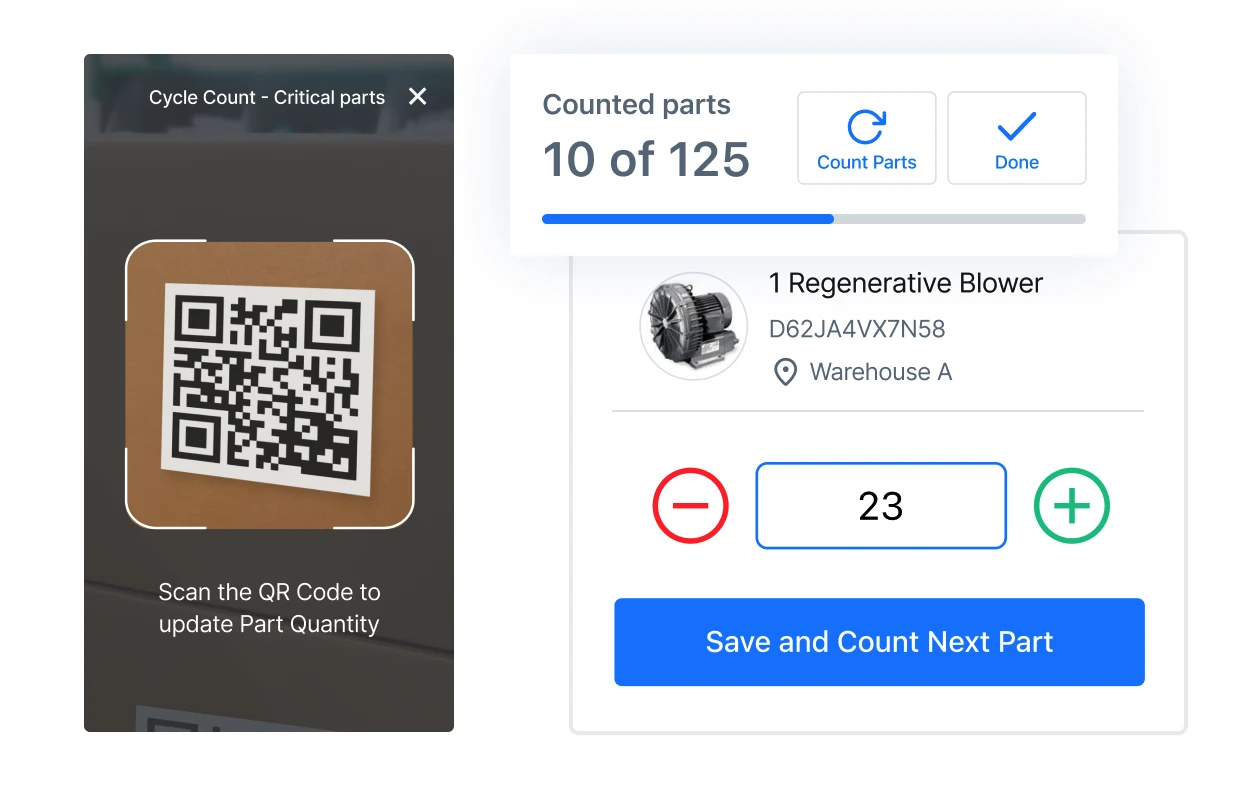
Reduce guesswork with data-driven insights
All your business critical information in one place. Quickly generate and export reports, such as asset maintenance history or MTBF, to make informed decisions. Track work across all assets and easily filter by technician, location, and more.
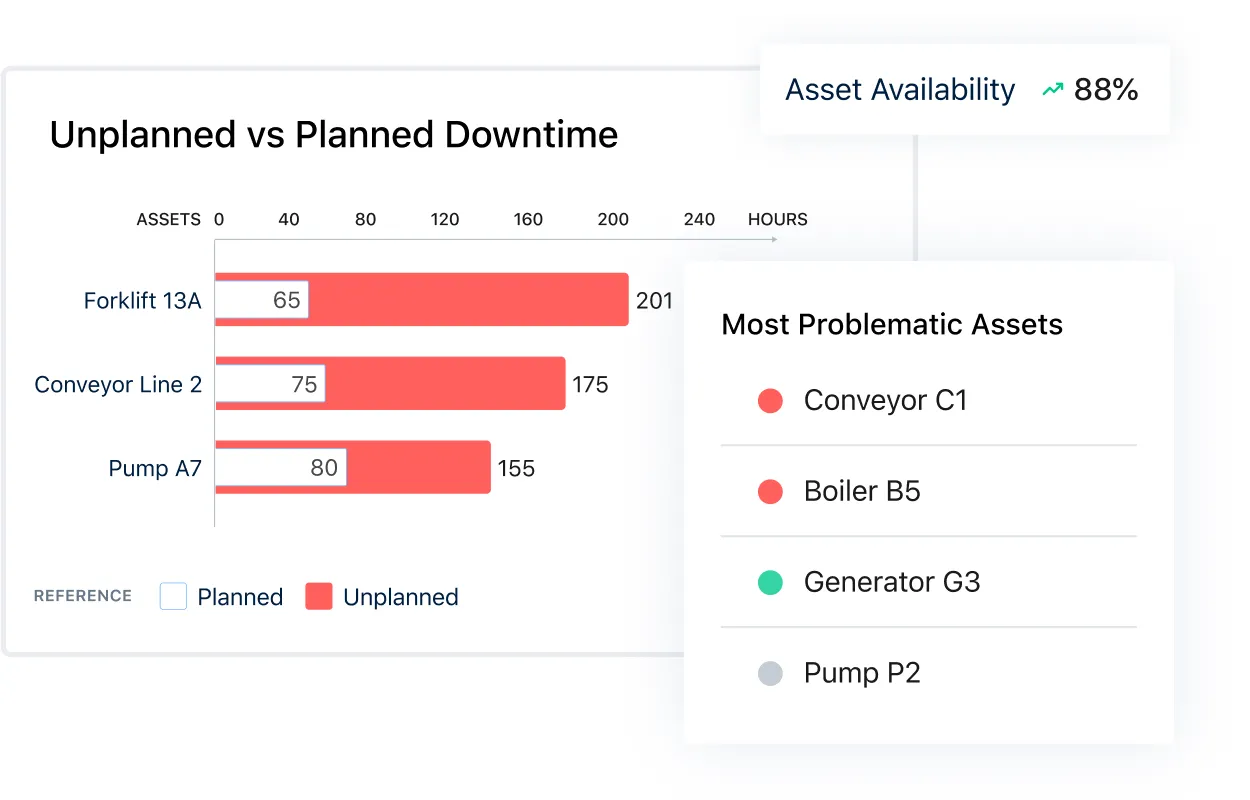
Leading enterprises rely on MaintainX
Award-winning software you can trust
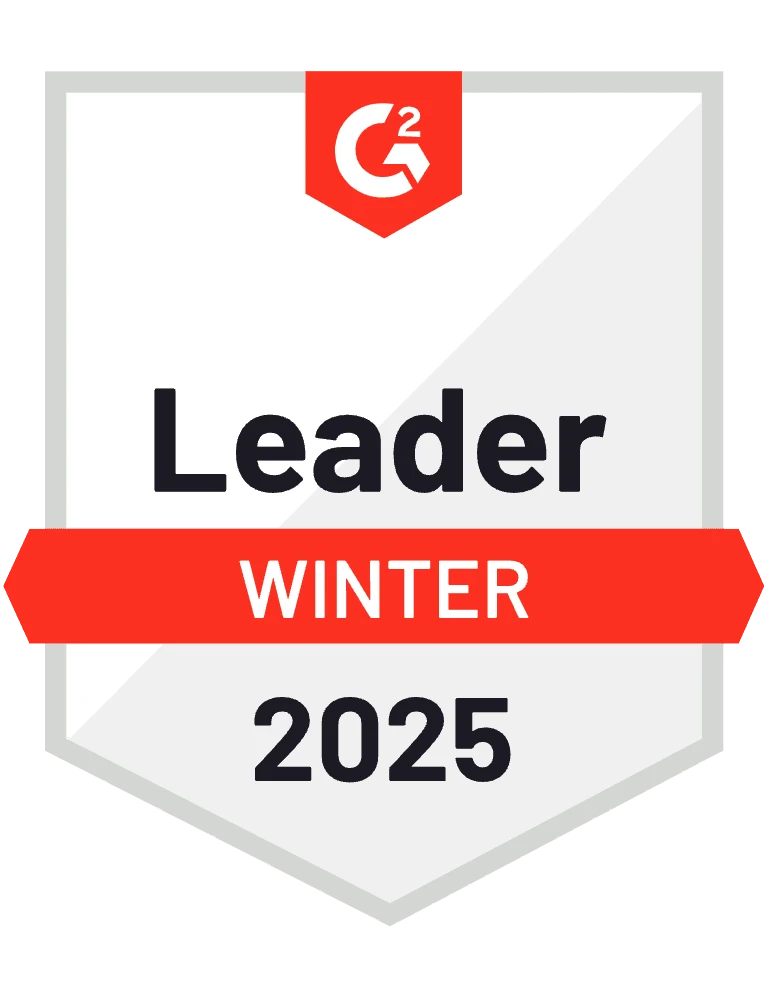
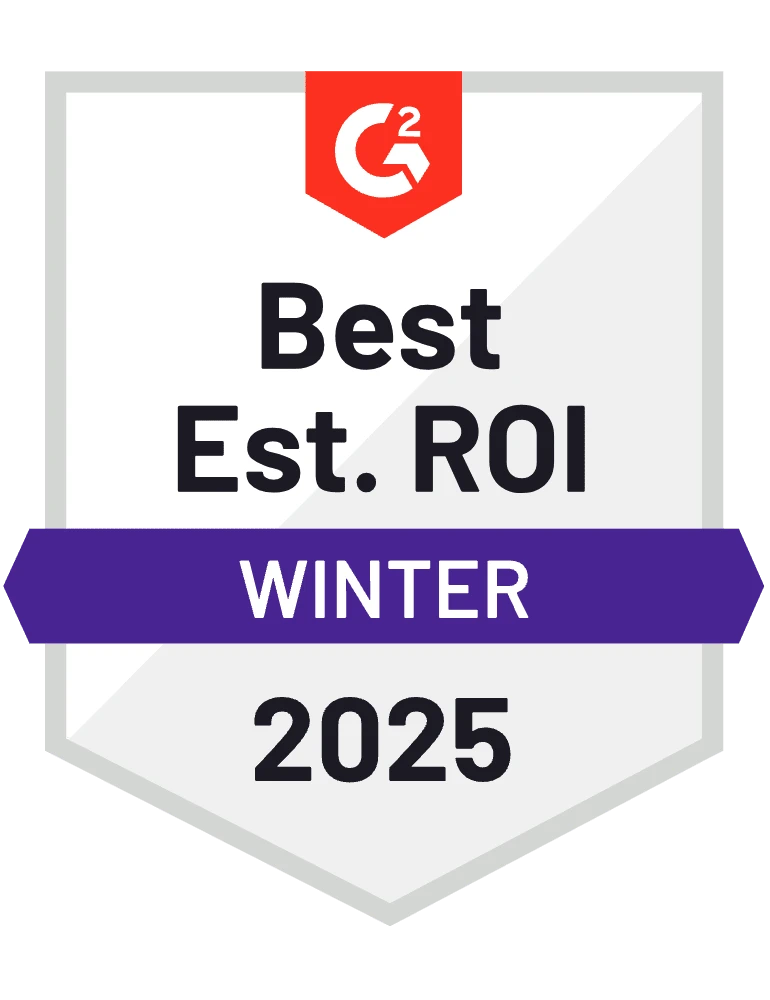
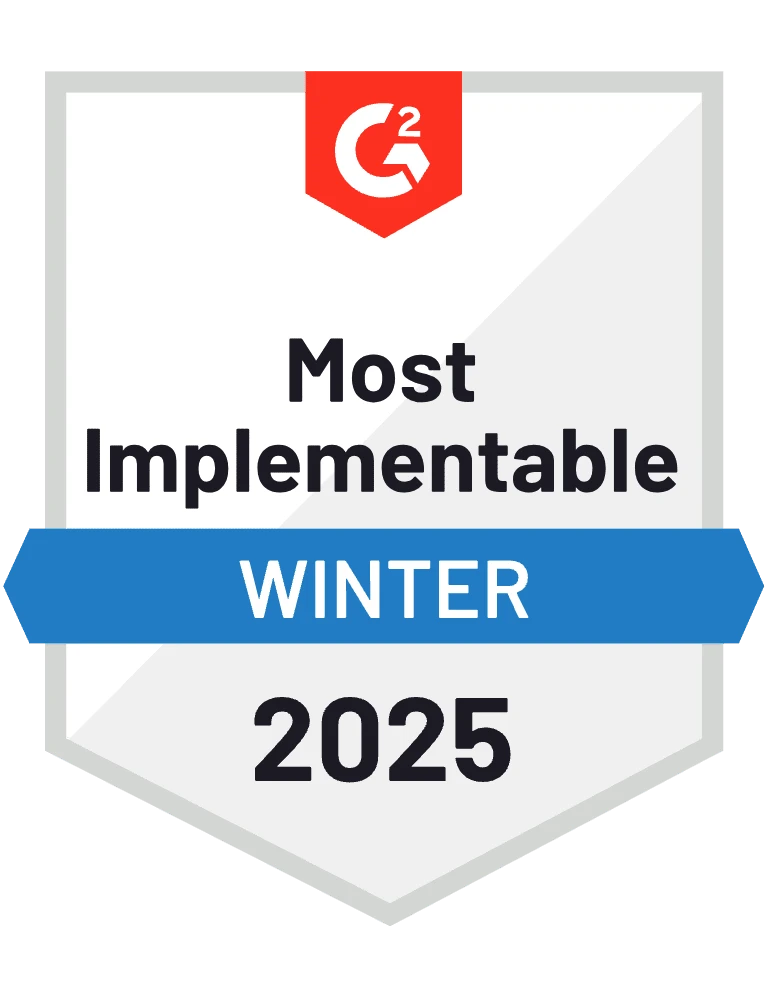
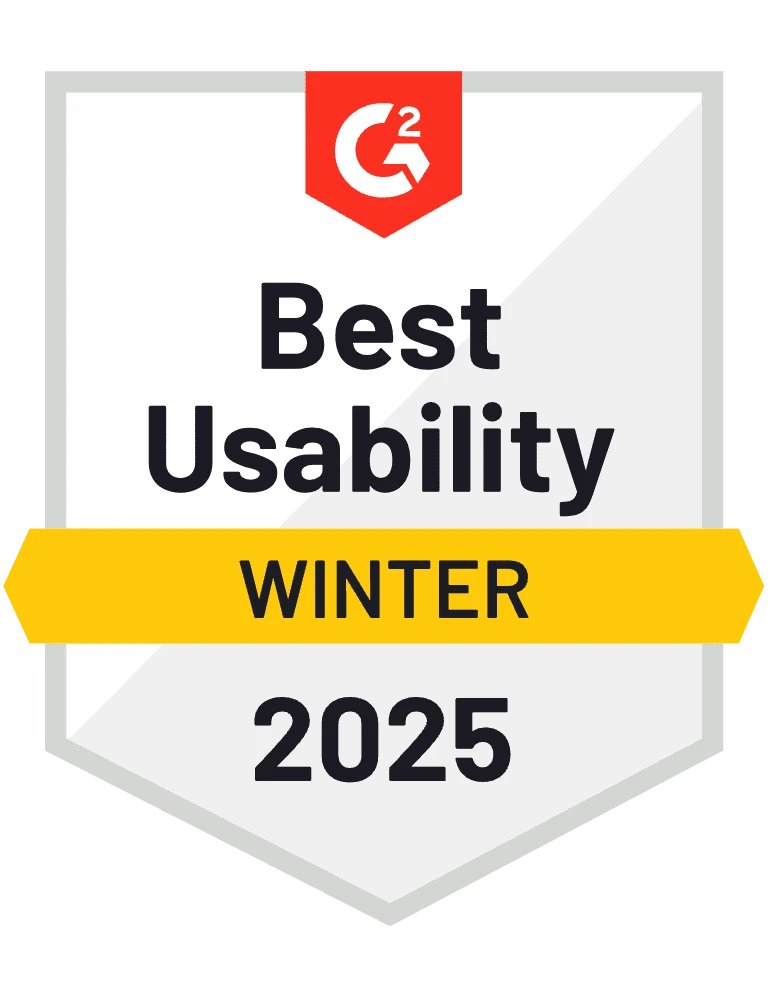
MaintainX FAQs
A CMMS (Computerized Maintenance Management System) in manufacturing is software that helps manufacturers plan, track, and manage all maintenance tasks for equipment and machinery. It provides a centralized platform to monitor asset performance, schedule preventive maintenance, and manage work orders to improve uptime and reduce equipment failures.
Manufacturing maintenance software, such as CMMS, reduces unplanned downtime by enabling preventive maintenance and allowing maintenance managers to schedule and track regular inspections. It also enables communication between team members, streamlines parts inventory management, and provides real-time insights into equipment health.
A CMMS offers centralized and automated tracking of maintenance logs, allowing manufacturing teams to:
- Access historical maintenance data for each piece of equipment.
- Ensure compliance with industry standards.
- Track spare parts usage.
- Improve asset reliability by recording all inspections, repairs, and replacements.
Preventive maintenance scheduling ensures that critical equipment receives regular attention before breakdowns occur. CMMS tools help manufacturing companies optimize maintenance operations by:
- Automating task scheduling.
- Streamlining parts inventory management to ensure necessary parts are always available.
- Preventing delays in service.
- Reducing reliance on reactive maintenance. This leads to smoother workflows and improved overall productivity.
Inventory management ensures that the necessary spare parts and tools are available when needed, preventing maintenance delays due to stock shortages. In a manufacturing environment, integrated inventory systems within a CMMS allow for efficient tracking of parts, automatic reordering, and cost control, contributing to reduced downtime and smoother maintenance operations.
Preventive maintenance reduces the likelihood of equipment failure, ensuring that machines operate at peak performance. This minimizes breakdowns, extends asset life, and optimizes production uptime, leading to higher throughput, fewer delays, and a reduction in costly repairs.
A CMMS system automates the scheduling of recurring maintenance tasks by setting up maintenance cycles based on time intervals or equipment usage. It sends reminders, assigns tasks to technicians, and generates reports on task completion, ensuring that recurring maintenance is consistent and efficient.
Asset management software provides real-time monitoring and detailed insights into the health and performance of critical manufacturing equipment. It helps identify wear patterns, optimize maintenance schedules, and ensure that vital machines remain in top working condition, reducing the risk of failure and increasing the lifespan of assets.
Historical maintenance data allows teams to analyze past performance, identify recurring issues, and pinpoint inefficiencies. Using this data, teams can adjust maintenance strategies, optimize schedules, and implement predictive maintenance to reduce failures and improve operational performance over time.
Historical maintenance data allows teams to analyze past performance, identify recurring issues, and pinpoint inefficiencies. Using this data, teams can adjust maintenance strategies, optimize schedules, and implement predictive maintenance to reduce failures and improve operational performance over time.
Integrating maintenance software with ERP, asset management, or inventory systems streamlines workflows, enabling better communication between departments and automating data sharing. This improves the visibility of equipment status, enhances reporting, and reduces manual data entry, leading to higher operational efficiency and smoother maintenance processes.
Get more done with MaintainX
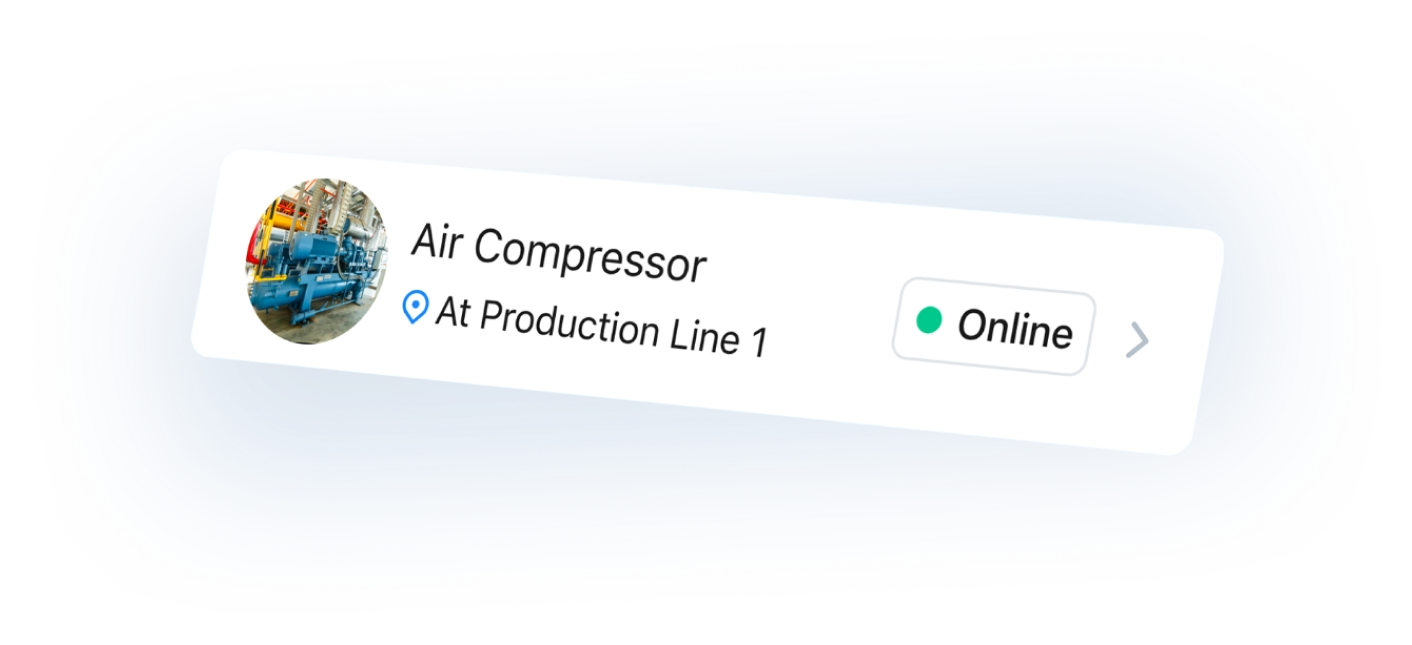
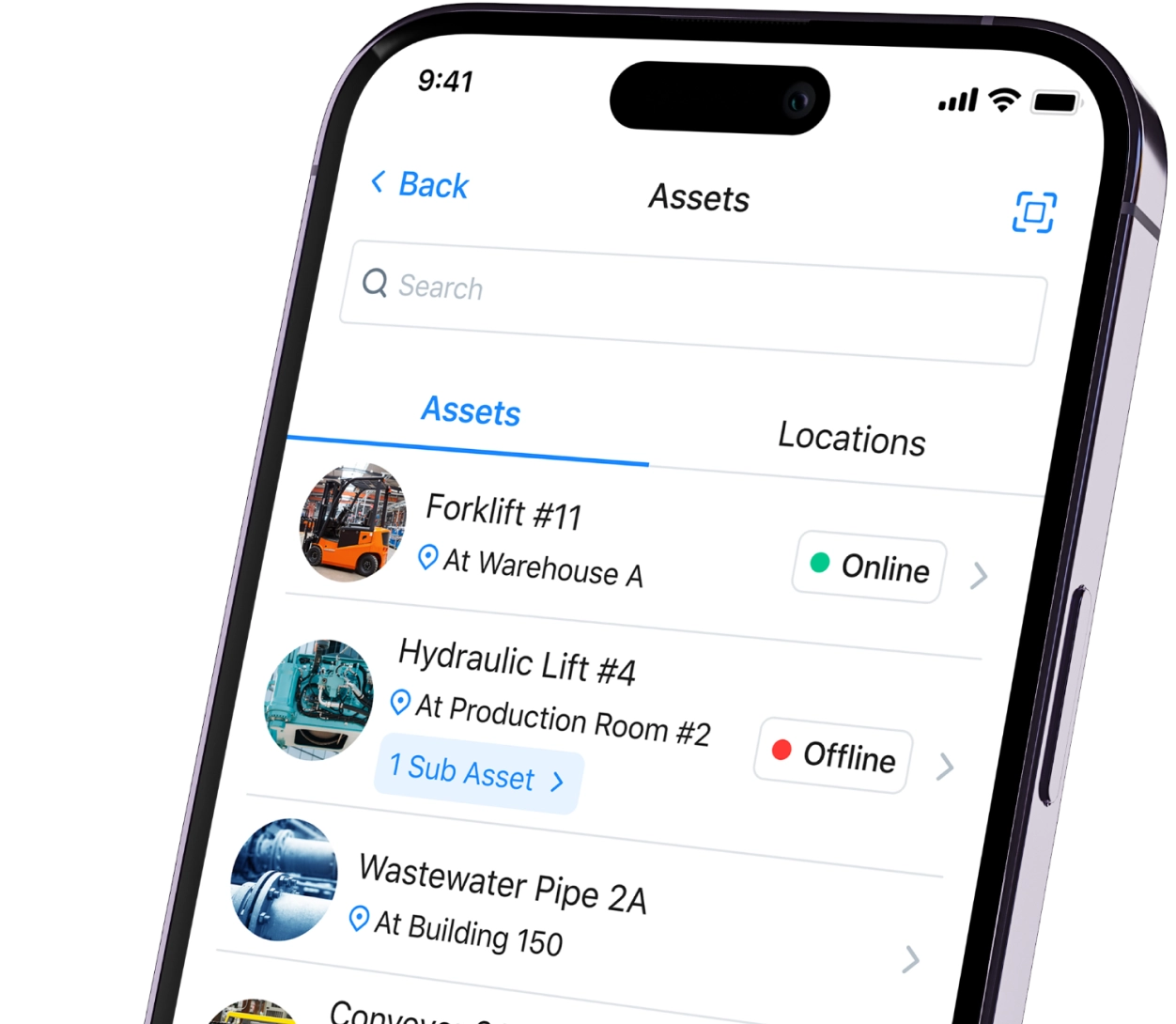