Western’s Smokehouse Increases On-Time Delivery with MaintainX
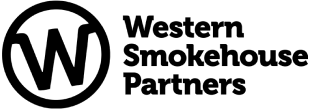
Ahlstrom is a global leader in producing sustainable and technically advanced fiber-based specialty materials. The company specializes in paper technologies, fiber refining, surface treatment, and converting techniques. The five end markets it serves form the basis of its five divisions: Filtration, Food & Consumer Packaging, Healthcare, Building Materials, and Technical Materials. With over 6,800 employees and 38 plants across 13 countries, Ahlstrom is dedicated to creating sustainable, innovative, and high-quality products, from compostable food and beverage processing and packaging materials to liquid and air filtration media, diagnostic materials, and protective medical fabrics.
When Chris Burns arrived at Ahlstrom in 2021 as the newly appointed Engineering Manager, he was determined to make a difference. He wanted to automate maintenance workflows and “set each day’s business and maintenance workflows in the morning” to prioritize work more effectively. However, Chris soon ran into a problem: not only was the company losing necessary information spread across multiple sources—from whiteboards to Excel spreadsheets—but it was losing tribal knowledge due to retiring technicians. There had been previous attempts to centralize the maintenance tribal knowledge to power automated maintenance workflows, but they had failed to gain full adoption.
Without clear visibility into maintenance history, data, and performance, Chris struggled to effectively plan maintenance tasks ahead of time and implement a more robust maintenance strategy. In fact, before implementing MaintainX, Ahlstrom’s maintenance strategy was almost entirely reactive. “We were 90% firefighting,” Chris recalled. “There was no categorization or prioritization of work [and we were simply reacting to any breakdowns that occurred that day].”
Further complicating his maintenance management plans was the loss of critical maintenance knowledge as older technicians retired. “Older technicians knew that certain things needed to be done on certain days,” Chris said. “But [that knowledge] was just in people's heads, and the tribal knowledge of what needed to be done on certain days was leaving with them.”
Chris recalled, “One of the first things I wanted to do when I arrived was to put a CMMS in place. One here in the UK had a fairly good reputation. But I had been looking at options, and MaintainX kept popping up.” He thought he’d better take a look. It was easy to use, especially on mobile. It’s been MaintainX ever since.
With more technicians planning to retire in the foreseeable future, Chris had to move quickly to stop the loss of tribal knowledge and get visibility into the data. Chris recalled, “One of the first things I wanted to do when I arrived was to put a CMMS in place. One here in the UK had a fairly good reputation. But I had been looking at options, and MaintainX kept popping up.” After careful evaluation, Chris decided to choose MaintainX as Ahlstrom’s preferred CMMS provider due to its robust capabilities and easy-to-use platform.
With the CMMS in hand, Chris first consolidated all maintenance data spread across multiple sources and uploaded them onto MaintainX. He then brought back retired technicians to capture the lost tribal knowledge of how maintenance had been performed in the past. With all knowledge and data consolidated in one central platform, technicians could now access the information they need, when and wherever they need it, to complete work orders better and faster. Chris noted, “[Our teams] have been using MaintainX to record their tribal knowledge, making this information more easily accessible to the new frontline teams.”
To keep the information in MaintainX up-to-date and refreshed, Ahlstrom technicians record what they know as they complete their work directly in MaintainX. Chris explained, “They're filling everything out as they do the jobs. Right away, it increases the history of the asset.”
Alan Foster, mechanical maintenance engineer responsible for scheduling and handling work orders at Ahlstrom, elaborated further, “Now, our work orders tell a story. You have your documentation right in the work order. Each shift can see what was done by the previous shift. When we work a shift system, a lot of information is lost through work and shift handovers. MaintainX captures even the simplest thing of one of our guys drawing an arrow to a part to show what’s not working. It’s all right there on mobile.”
MaintainX’s native mobile application provides Ahlstrom technicians immediate access to the necessary information wherever they are in the plant, allowing them to respond better and faster. “Electrical drawings and schematics are all there in the palm of their hands. And as you start to build up the history of the assets, they're finding it easier to go to breakdowns, have a look, and say, ‘Oh, this is a repeat.’”
MaintainX has also improved communication and collaboration between technicians. Its chat and comments features allow technicians to work together on solving problems no matter where they are on the shop floor. Chris says, “[The flexible messaging functionality with emojis and reactions] helps to get the guys using it, especially the younger guys. It’s adding fun.”
“If it’s not in MaintainX, it’s not happening. If you’ve got a problem, it goes into MaintainX.”
—Chris Burns, Ahlstrom Engineering Manager
As Chris initially hoped, work planning has become easier and more effective. He uses MaintainX reporting to make data-driven decisions around the maintenance work that needs to be done for the day. He can also easily track and forecast the time required to complete a specific task/job. “Prioritization has become a lot better,” Chris recalled. “Having everything in one place has helped. Our meetings are shorter. We end the meeting and go do the work.”
In addition to prioritization, MaintainX has improved the culture around record-keeping and sharing information. In fact, since February 2023, Ahlstrom has created 3,200+ work orders, including 170+ procedures, 440+ locations, and more than 3,000+ assets in MaintainX. Technicians understand that “the more work you put in MaintainX, the better it gets.” The techs have a mantra, Chris said: “If it’s not in MaintainX, it’s not happening. If you’ve got a problem, it goes into MaintainX.”
In just the first year since implementing MaintainX, Ahlstrom has captured 80% of the tribal knowledge, decreased downtime significantly, and reduced MTTR by 90%. Chris affirms, “Since adoption, our Mean Time to Repair has decreased from 580 to 60 hours a month.”
“MaintainX has, for sure, surpassed my expectations. We've been really happy to see all these different functions and take them at our own speed.”
—Chris Burns, Ahlstrom Engineering Manager
At Ahlstrom, implementing MaintainX took just one month, much faster than Chris expected. Adoption of the platform—which is often a challenge with CMMS platforms—is widespread at Ahlstrom.
Alex remarked, “[After just a few days, I knew MaintainX was] definitely different. It’s fresh, clean, simple. It was plug-and-play on a multitude of devices. With the exact same display and the exact same functionality. A big game changer for these guys because we already had good Wi-Fi coverage throughout the site.”
These days, Chris uses MaintainX Reporting dashboards and filters to drive adoption of more robust features. “We've been learning as we go on and are happy we have access to these tools.” Chris noted that his technicians like using mobile devices on the job. “We can bring in other forms of online training.”
As part of the next step in Ahlstrom’s journey to level up its maintenance program, Chris plans to onboard MaintainX’s parts management features to reduce the over-ordering of parts. “We can’t just assume there’s no part on the shelf, place an order, only to find we’ve got the part and double spend,” Chris explained. And with MaintainX’s responsive and effective support team, Chris is confident that they will continue to see success with MaintainX at Ahlstrom and is excited by the opportunity to further expand the platform's usage at the company.
Get more done with MaintainX