Redimix Cuts Year-Over-Year Maintenance Costs by 53% With MaintainX
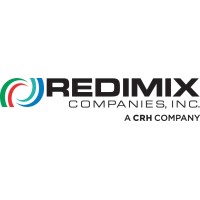
LUV Car Wash is a national express car wash service with over 75 locations across America. Headquartered in Gilbert, Arizona, LUV aims to give customers a superior car wash experience through a combination of technology, best-trained employees, and well-maintained facilities.
Prior to MaintainX, LUV Car Wash relied primarily on a reactive maintenance strategy to manage its facilities. And while it seemed to be doing a good enough job, Linda Linaweaver, Facilities Maintenance Manager at LUV Car Wash, knew from personal experience that a proactive approach would help further streamline operations and deliver best-in-class customer experience.
“Like I told my guys this week in training,” Linda says, “I bought my house 27 years ago. I still have my original air conditioner. Because my husband is fanatical about maintenance. Every summer, each fall, the maintenance is done. And I haven't had to replace it. I'm still there 27 years later with the same air conditioner because maintenance is key.”
Linda had been brought on to spearhead the transformation of maintenance and operations for LUV Car Wash. “I was originally hired as the Purchasing Manager to set up and develop an online work order program so we could move away from spreadsheets.” However, with their previous maintenance management system, that was a challenge.
To manage maintenance at LUV, the team relied on a simple spreadsheet system. As Linda puts it, “We kept everything on a spreadsheet and just went down the line working the jobs that were listed.” These spreadsheets didn’t contain all the necessary information, or the necessary data was spread across multiple different spreadsheets. The lack of ready access to data meant that each team member had to rely on their memory to inform how they approached maintenance work. “In its infancy we were reactive to the site locations maintenance needs because there was no continuity to the data.”
This method of maintenance management also meant that the LUV team couldn’t always stay on top of who did what, where, and when. Just as the technicians relied on memory to know what tasks to perform, managers had to rely on verbal status updates to know that the team had completed the work. “With paper, you don't really know who's doing it and who isn’t,” Linda says. “You're not sure, there's no accountability, and you can't find the data that you need to double-check.”
Without a centralized system to collect, record, and store data, Linda and the LUV Car Wash team struggled to get visibility into important operational insights. “Let's say you have a top brush, and the air cylinder breaks,” Linda says. “Well, that's normal wear and tear. Next month, if it breaks again, you're going to stop and think, 'oh I just did this, let me keep an eye on it.'” The team had no consistent or reliable way of tracking their maintenance and operational data and could have missed crucial opportunities to improve their operations.
"I loved how much sense MaintainX made even to those who aren't used to working with technology. I knew that the user-friendly interface would make it easy for the team to transition onto MaintainX."
In order to modernize the maintenance program at LUV Car Wash, Linda knew that she would need the help of a modern CMMS.
After extensive competitive research, Linda enlisted the help of MaintainX. She found that MaintainX offered better and more relevant features than the other platforms in the market. “I researched and checked a couple of different ones,” Linda says. “But MaintainX just had all the bells and whistles and all the little things that we wanted.”
Given the team’s challenges with access to data and accountability, MaintainX’s data management and history tracking features stood out to Linda. “We wanted to be able to track history and data, and MaintainX helped us to do exactly that with ease.”
”In MaintainX, you can clearly see work orders that still need to be worked on and what needs to be done,” Linda explains. “If we are on-site and something has not been greased, we can search the site's work orders and know who is accountable for it. If we notice an air compressor is breaking down, we can look and see that it's because the site is not maintaining it. We're able to track better.”
Now, instead of relying solely on memory, Linda and her team gained complete visibility into the work that had been performed and the work that needed to be done next.
Functionality was only one part of the equation for Linda. Having used a maintenance management system that saw little adoption at a previous company, Linda knew it was important to implement a CMMS the team would fully embrace and adopt. “I knew going into LUV that I wanted to have more access for the people that were going to use it.”
MaintainX’s mobile-first, intuitive design made it easy for her team to learn and start using it from day 1. "I loved how much sense MaintainX made even to those who aren't used to working with technology," Linda explains. “I knew that the user-friendly interface would make it easy for the team to transition onto MaintainX."
“I walked the team through it, showing them how it creates the corrective action work orders. It was kind of one of those aha moments where now they're like, 'okay, this makes a lot of sense.'"
MaintainX helped to immediately improve visibility and accountability into the work that had been done and the work that needed to be done next. ”In MaintainX, you can clearly see work orders that still needs to be worked on and what needs to be done,” Linda explains. “If I go in and something has not been greased, I know who's accountable for it. If I notice an air compressor is breaking down, I can look and see, oh, it's because you're not draining it. We're able to track better.”
What’s more, standardized procedures within MaintainX have helped improve the quality of the work output, ensuring that the work is done correctly every time.
“The pass or fail option within a procedure? I loved it,” Linda says. “I walked the team through it, showing them how it creates the corrective action work orders. It was kind of one of those aha moments where now they're like, 'okay, this makes a lot of sense.'"
Relying on spreadsheets and memory meant that Linda and her team couldn’t always plan properly for maintenance work. Now, with MaintainX, the team can create optimized maintenance work schedules and ensure they have the right parts in stock to complete the necessary work orders.
“Our pit pumping, for example, is scheduled on the first of every year for the entire year,” Linda says. “When GMs see the work orders, they can go into them and tag me in a comment saying, 'I'm going to need this before next month.'”
With labor shortages affecting new talent recruitment, it was important for Linda to train and up-level her existing team. ”Car Wash maintenance is one of the hardest to learn and one of the hardest to train,” Linda says. “And it’s crucial for us to provide continued opportunities to learn and grow in our team.”
“Our Maintenance Leads are going to go through the wash, spend 10 hours a week on every piece of equipment. They are getting to know the wash inside and out and become experts in the industry. And MaintainX is helping to enable all of this for our team.”
With MaintainX, LUV has been able to create and assign procedures for employees to perform, through which they carry out regular preventive maintenance and gain the practical experience required to step into leadership roles. In Linda’s own words, “ Our Maintenance Leads are going to go through the wash, spend 10 hours a week on every piece of equipment. They are getting to know the wash inside and out and become experts in the industry. And MaintainX is helping to enable all of this for our team.”
In partnership with MaintainX, LUV Car Wash has laid the foundation for robust parts management. For example, technicians are already taking advantage of MaintainX parts inventory to easily track and locate necessary parts. Linda elaborates, “A district manager needed to find bearings for a piece of equipment that had broken down. And despite being miles away from her, I was able to help her locate the required parts by directing her to MaintainX. And in less than a minute, she was able to find the required part by simply knowing how to use the system.”
Having tackled parts inventory management, Linda is looking to bring purchase order management back in-house with the help of MaintainX. “Over the next year, we're going to take back the ordering process,” Linda says. “And we'll be doing it all through MaintainX.”
On the roadmap, next for Linda is further optimizing their inventory practices with MaintainX, especially taking advantage of QR code scanning. “My perfect world would be taking a QR code and getting a visual printout for each location containing exactly what pieces of equipment they have and all the parts associated with the equipment.” This streamlined approach promises to further enhance LUV Car Wash's commitment to operational excellence, driven by the continuous innovation made possible through its partnership with MaintainX.
Get more done with MaintainX