MaintainX vs The Rest: Find a better rated software, we dare you
The future of maintenance, today
Compare CMMS Solutions: Top MaintainX Alternatives
Leading enterprises rely on MaintainX
Award-winning software you can trust
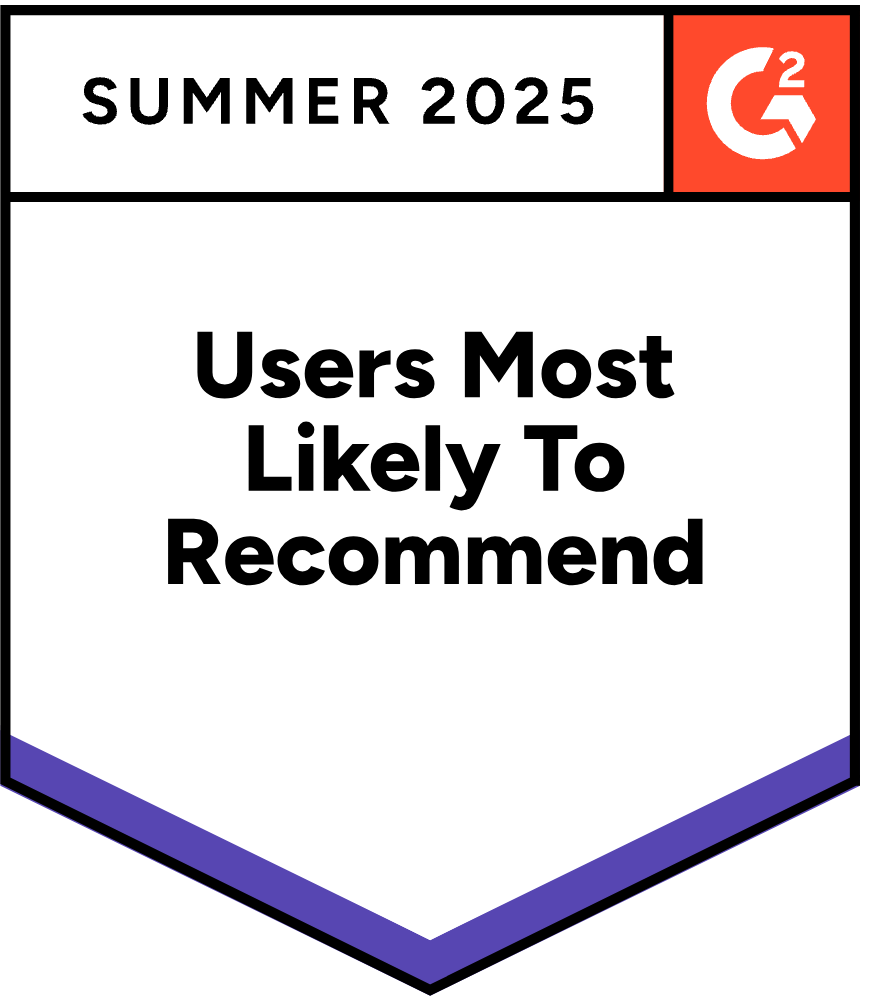
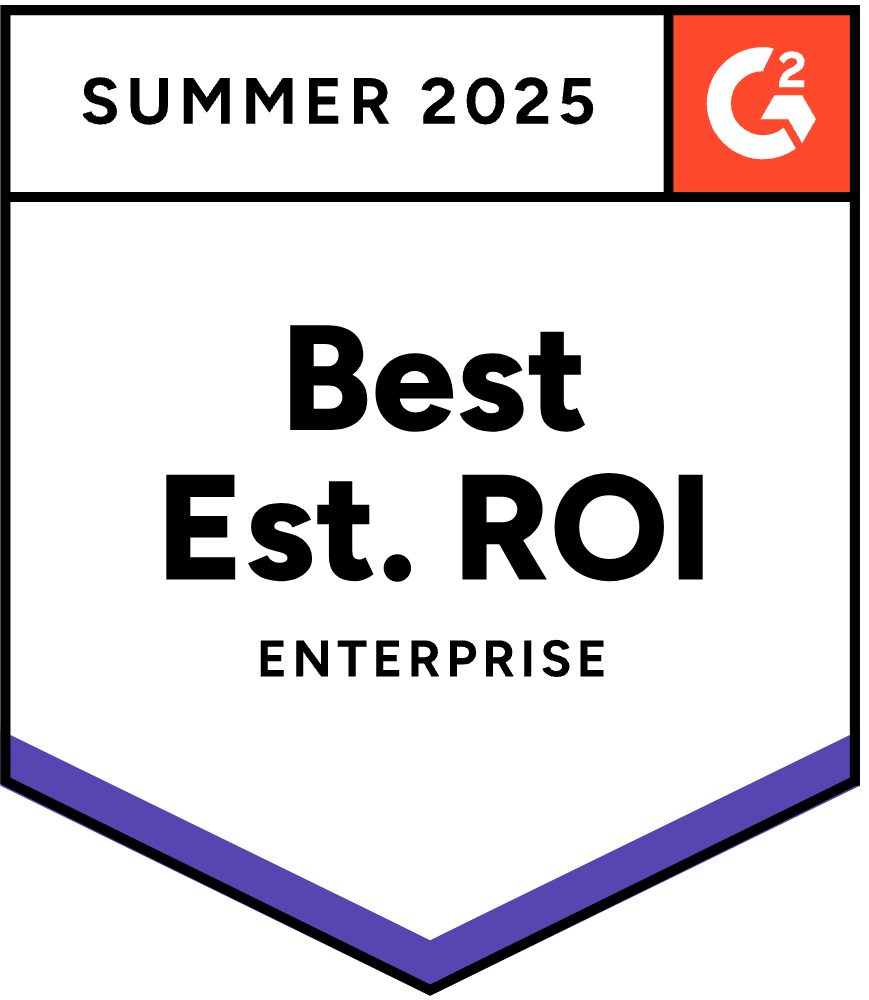
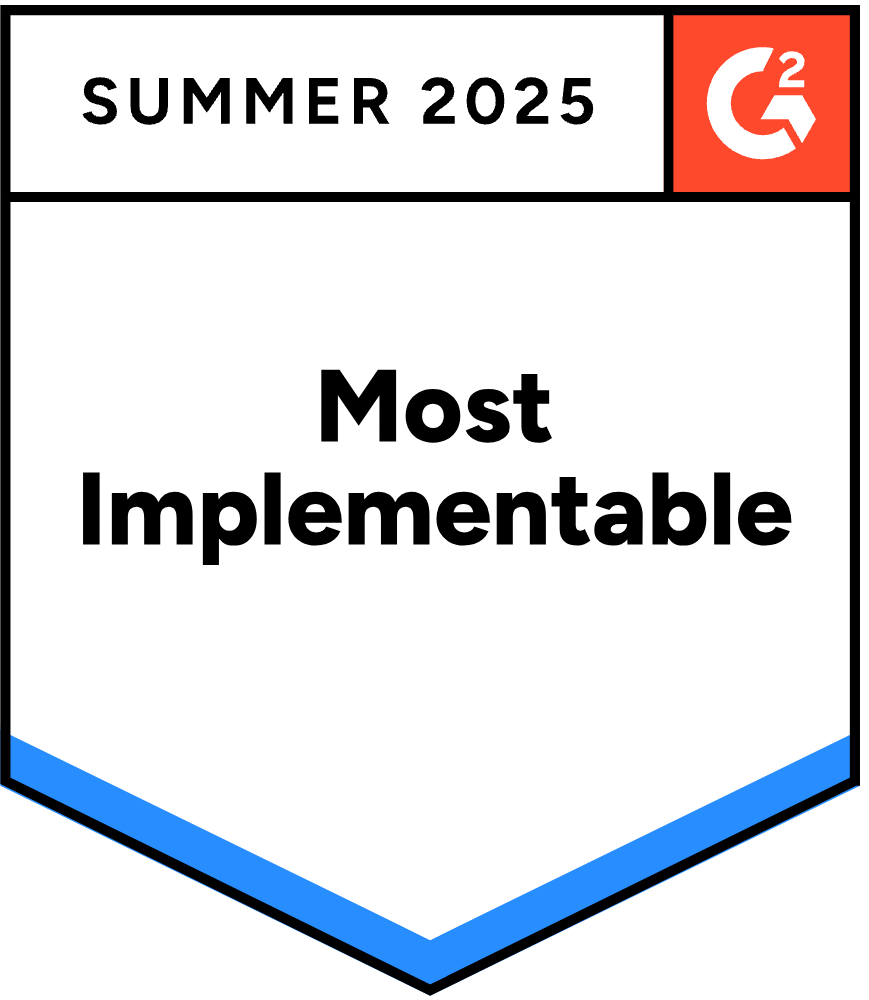
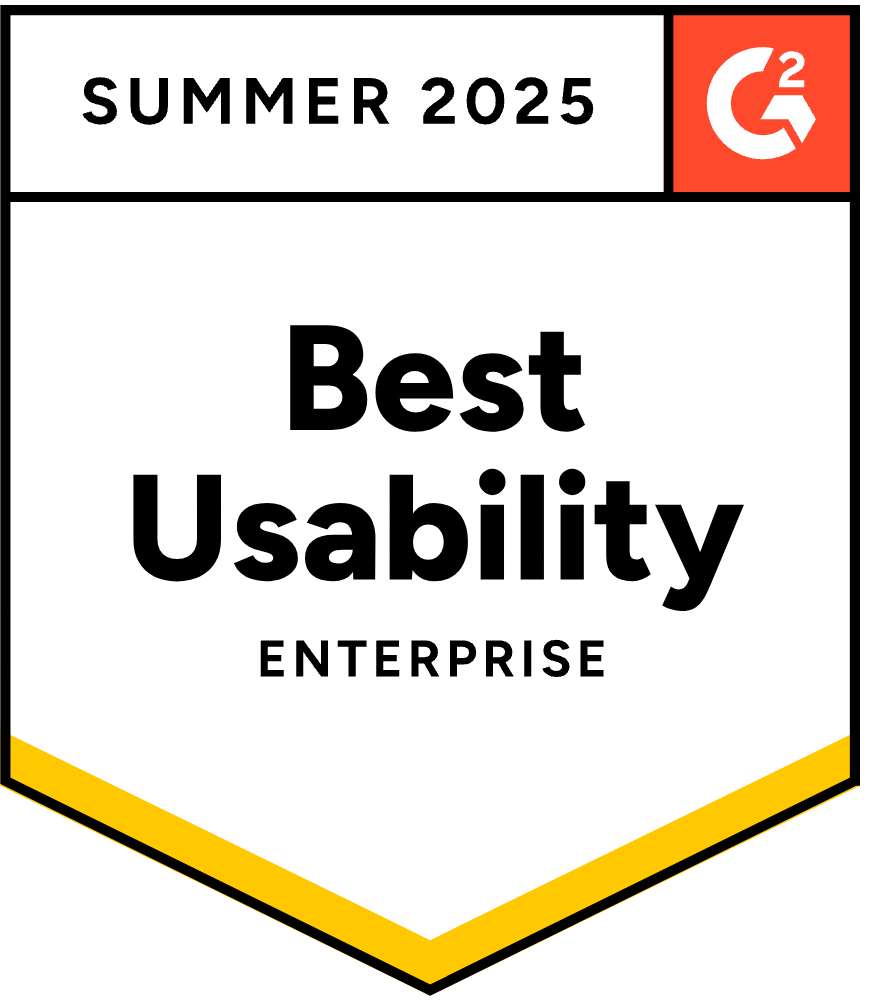
See what customers have to say
Frequently Asked Questions
A CMMS improves maintenance operations by streamlining and automating maintenance tasks, enhancing workload management, managing parts inventory, and analyzing maintenance data. A CMMS provides a comprehensive suite of maintenance solutions to help you schedule preventive maintenance, track work orders, generate insights, make data-driven decisions, and ensure you always have parts available This leads to increased operational efficiency, reduced equipment downtime, and better resource management.
When selecting asset management solutions for your maintenance teams, look out for features including:
Work order management: Features to allow you to create, assign, and track work orders, as well as address one-off maintenance requests, all in one place.
Enterprise asset management: Tools to help manage, track, and analyze your assets for efficient performance and maximized return on investment.
Maintenance scheduling: Robust scheduling tools for planning and scheduling preventive maintenance tasks.
Resource planning: Optimize your preventive maintenance schedules with labor insights so you can assign tasks based on capacity.
Asset tracking: The ability to track asset performance, status, location, and history.
Inventory management: Modules for managing spare parts and supplies, generating alerts to restock, creating purchase orders, and managing vendor information.
Reporting and analytics: Comprehensive reporting capabilities to analyze data and performance, generate insights, identify areas of improvement, and drive operational excellence.
Mobile access: Support for mobile devices to facilitate on-the-go access.
Real-time communication: The ability to communicate via instant messaging and share real-time feedback.
Integration: Flexibility and compatibility with other systems like ERPs, sensors, and IoT devices.
Preventive maintenance helps reduce maintenance costs by addressing issues before they become major problems. You’ll be able to get ahead of failures and breakdowns, minimize downtime, and avoid costly repairs. By keeping assets in good working condition with preventive maintenance procedures, you can also ensure they run efficiently and prevent premature wear and tear. This process will extend equipment life, leading to a better return on investment, and reduced spending on replacing equipment.
MaintainX allows you to track critical parts usage, manage parts suppliers, and calculate parts spend to help you minimize downtime and reduce costs.
Low-stock alerts: MaintainX notifies you when stocks run low to avoid breakdowns and emergency shipping fees. You can trigger new orders automatically to restock parts when they fall below a certain level.
Multi-facility visibility and sharing: Global Parts Management in MaintainX allows you to access and share parts across your facilities. This keeps assets up and running while maintaining a leaner inventory across the organization.
Integrated purchasing: With MaintainX, you can control costs with customizable approval workflows and sync POs with your ERP system to reduce duplicate data entry.
Cost tracking: Robust reporting in MaintainX allows you to track your parts costs over time, see which assets cost you the most, and make smarter decisions about which parts to keep in stock.
Inventory management software helps maintain accurate inventory records by providing real-time tracking of inventory levels, locations, and usage. It automates the process of recording inventory transactions, such as receipts, issues, and transfers, reducing the likelihood of human errors. The software also generates alerts for low stock levels and reorder points, ensuring that necessary parts and supplies are always available. Better inventory control helps in better planning and budgeting, reducing excess stock and stockouts.
The advantages of using a web-based maintenance software include:
Accessibility: You can access the system from anywhere with an internet connection.
Efficient management: Using a cloud-based cmms software means maintenance managers can monitor their maintenance operations from one central location.
Real-time updates: Your team can share and receive instant updates across all users.
Cost-effectiveness: Because these systems don’t require extensive hardware or setup, you’ll have lower upfront costs.
Scalability: Easily scalable to accommodate growing maintenance needs.
Enhanced collaboration: Web-based software, particularly systems with mobile access, facilitates collaboration among team members across different locations.
Maintenance and operations professionals across multiple industries use CMMS solutions to manage maintenance, streamline operations, reduce equipment downtime, manage resources, and more. Examples of these industries include manufacturing, property management, facilities management, healthcare, education, and more.
Get more done with MaintainX
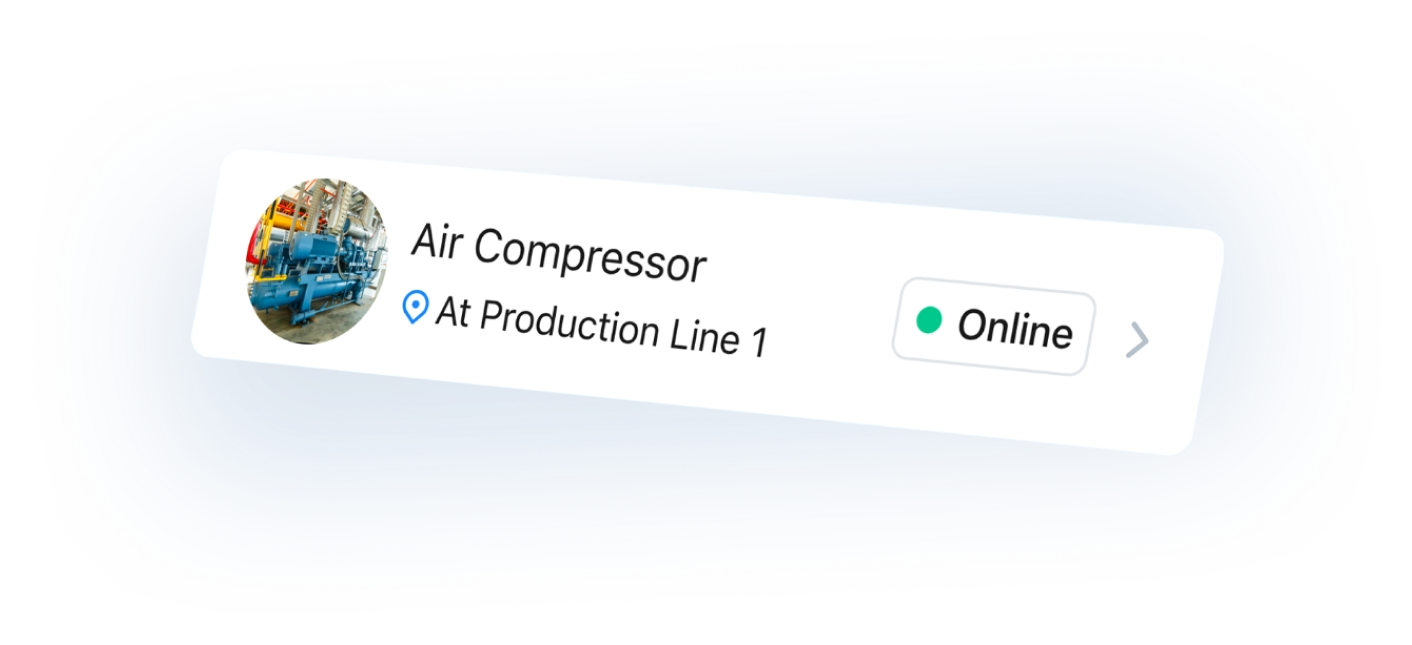
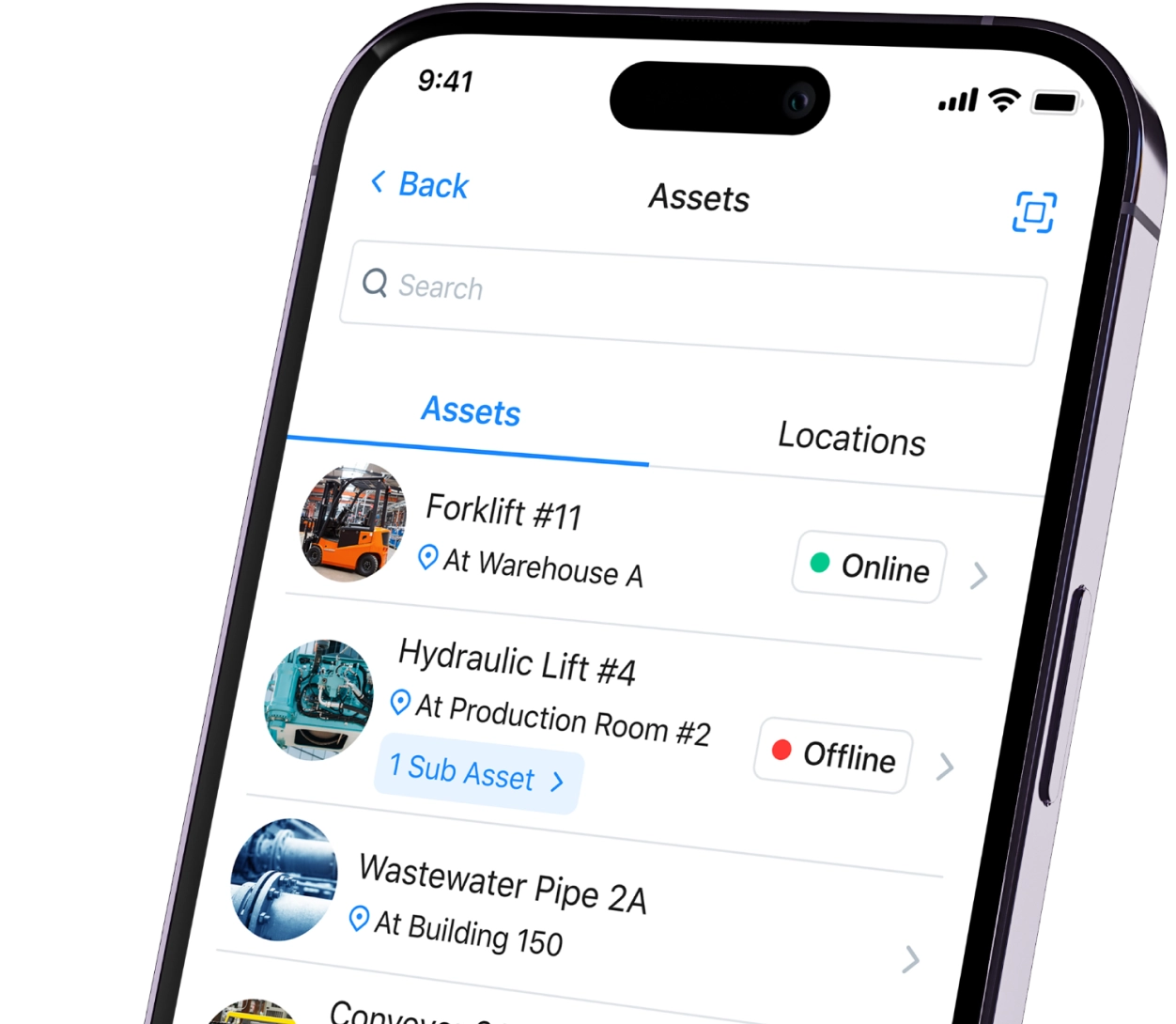