The two most advanced proactive maintenance strategies used by organizations today are Predictive Maintenance (PdM) and Condition-Based Maintenance (CBM). When considering condition-based vs. predictive maintenance, both approaches share the same overarching goals: a) reducing equipment downtime and b) optimizing resources by performing maintenance work only when needed.
Additionally, both strategies are forms of preventive maintenance (PM) that often rely on condition-based diagnostic sensors to measure vibration, temperature, and ultrasound intervals to predict equipment failure. With these similarities, there is often confusion within the maintenance community on the differences between PdM and CBM.
Condition-Based vs. Predictive Maintenance
The primary difference between condition-based vs. predictive maintenance is the latter combines sensor measurements with precise algorithmic formulas to predict the exact moment when maintenance actions should be taken.
Comparatively, CBM can only provide information when given perimeters reach an unacceptable level, and action needs to be taken in the present moment to avoid equipment failure. Thus, PdM is a more advanced form of preventive maintenance than CBM.
Condition-Based Maintenance Workflow
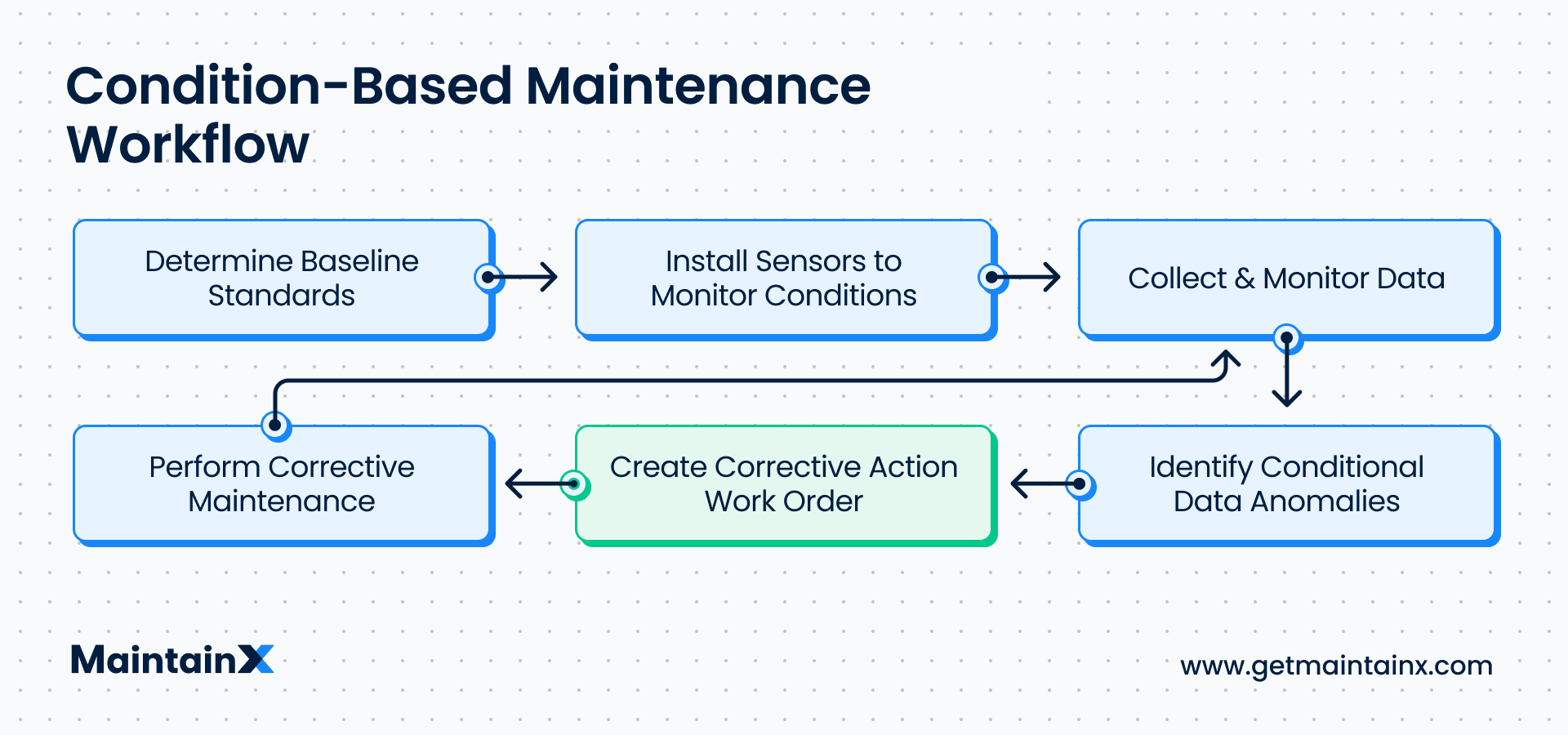
Example of Condition-Based Maintenance
If you manage a fleet of vehicles, such as in the transport or construction industry, you may be used to scheduling an oil change based on a calendar schedule (such as every three months) or mileage (such as every 5,000 miles driven). But if you use CBM, your maintenance schedule may be informed by reading a gauge that monitors oil particles. This may mean changing the oil every 8,000 miles instead of 5,000 miles or after four months instead of three months. The advanced monitoring would save costs on engine oil.
Predictive Maintenance Workflow
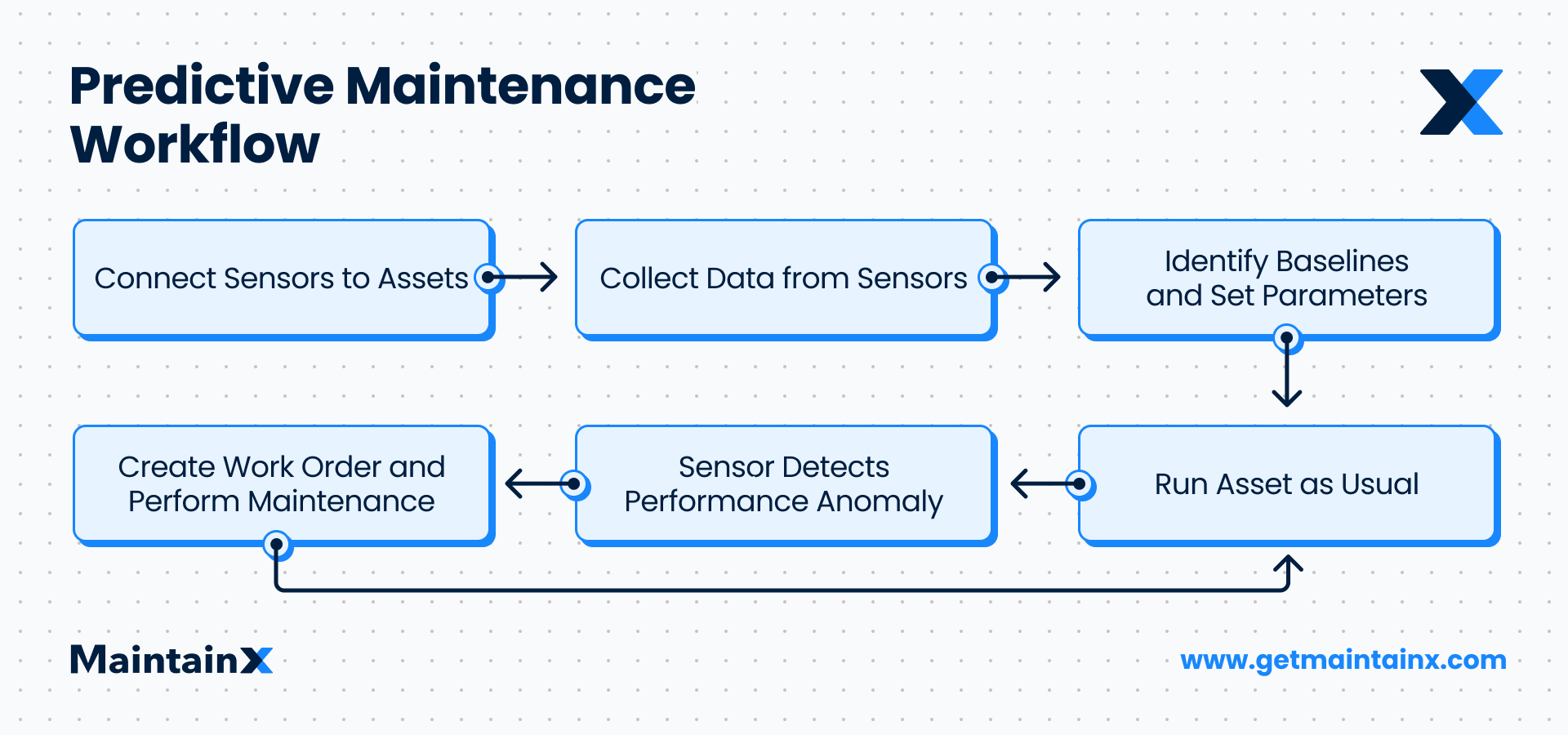
Example of Predictive Maintenance
The railway industry commonly uses PdM by installing IoT-based sensors on trains to identify problems long before failure occurs. Over time, as more asset behavioral data is accumulated, the algorithm becomes increasingly accurate at recommending ideal times for scheduled maintenance to avoid future train breakdowns.
How Does Predictive Maintenance Work?
PdM is implemented in four basic steps:
- Establish baseline acceptable condition limits for critical assets.
- Install sensor devices and the Internet of Things (IoT) to monitor the condition of equipment and send data in real time.
- Connect sensor devices and IoT to a Computerized Maintenance Management System (CMMS) for data collection and analysis.
- Monitor CMMS reports for increasingly accurate insights on decreasing downtime, reducing unnecessary costs, and increasing efficiency.
It’s worth mentioning that some CMMS platforms can automatically create and schedule work orders when maintenance protocols are triggered. However, operational managers can also do this manually.
What Are the Types of Predictive Maintenance Technologies?
PdM technologies can be divided into four different categories, including:
- Vibrational Analysis: This type of PdM is used to detect imbalance, bearing wear, misalignment, or looseness in high-rotating equipment monitoring vibrations.
- Sonic Acoustical Analysis: Manufacturing plants use sonic acoustical analysis proactively to tell when low-and high-rotating pieces of equipment need lubrication.
- Ultrasonic Acoustical Analysis: Commonly used in mechanical and electrical equipment, this type of PdM relies on ultrasonic friction and stress sounds to predict imminent breakdowns.
- Infrared Analysis: Infrared analysis predicts the need for maintenance by measuring the temperatures. It’s mostly used to identify motor stress, cooling, and airflow-related issues in equipment.
Industries That Use Condition-Based vs. Predictive Maintenance
Due to the current high cost of sensor-based technology, both CBM and PdM programs are only within reach for large organizations with high maintenance budgets. Some of the industries that commonly use CBM and PdM include:
- Manufacturing
- Utility Companies
- Transportation
- Mining
- Healthcare
Alternatively, SMBs looking to optimize their existing maintenance programs should strive for an 80/20 ratio of preventive maintenance to reactive maintenance with the support of a user-friendly CMMS, as opposed to utilizing condition-based maintenance vs. predictive maintenance strategies.
What Are the Advantages of Condition-Based vs. Predictive Maintenance?
Both PdM and CBM can improve equipment reliability, increase workplace safety, streamline maintenance costs, and increase productivity. According to survey data compiled by Industrial AI and Analytics, implementing maintenance programs with advanced technologies may:
- Deliver 10 x ROI
- Reduce maintenance costs by 25% to 30%
- Eliminate breakdowns by 70% to 75%
- Reduce downtime by 35% to 45%
- Increase production by 20% to 25%
Additionally, PdM can increase asset uptime by as much as 30 percent. This not only improves maintenance team productivity but the output and functionality of the entire organization.
Quick Glance: Predictive Maintenance vs. Condition-Based Maintenance
The table below summarizes the differences between predictive and condition-based maintenance.
Implement a CMMS for CBM and PdM
Determining the differences between condition-based vs. predictive maintenance might not be evident at first glance. Both advanced maintenance practices use sensors to measure changes in equipment vibration, temperature, ultrasounds, and more. And both PdM and CBM programs can help reduce costly equipment failures. Their high setup and operational costs make the maintenance strategies most suitable for large organizations with extensive resources. However, PdM technology takes efficiency a step further by combining real-time monitoring with predictive algorithms that help determine the precisely ideal times for asset maintenance.
User-friendly automation platforms are crucial to running efficient work environments, staying on top of preventive maintenance, and providing a dependable range of services. MaintainX is a modern CMMS system that streamlines maintenance services by providing maintenance schedule digitization, team messaging, and asset cataloging. The best part? It’s compatible with both desktops and mobile devices!
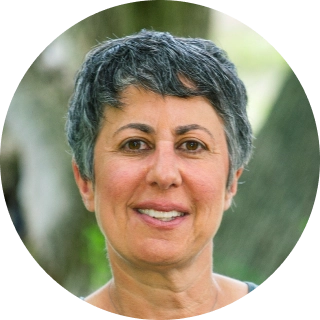
Caroline Eisner
Caroline Eisner is a writer and editor with experience across the profit and nonprofit sectors, government, education, and financial organizations. She has held leadership positions in K16 institutions and has led large-scale digital projects, interactive websites, and a business writing consultancy.
See MaintainX in action