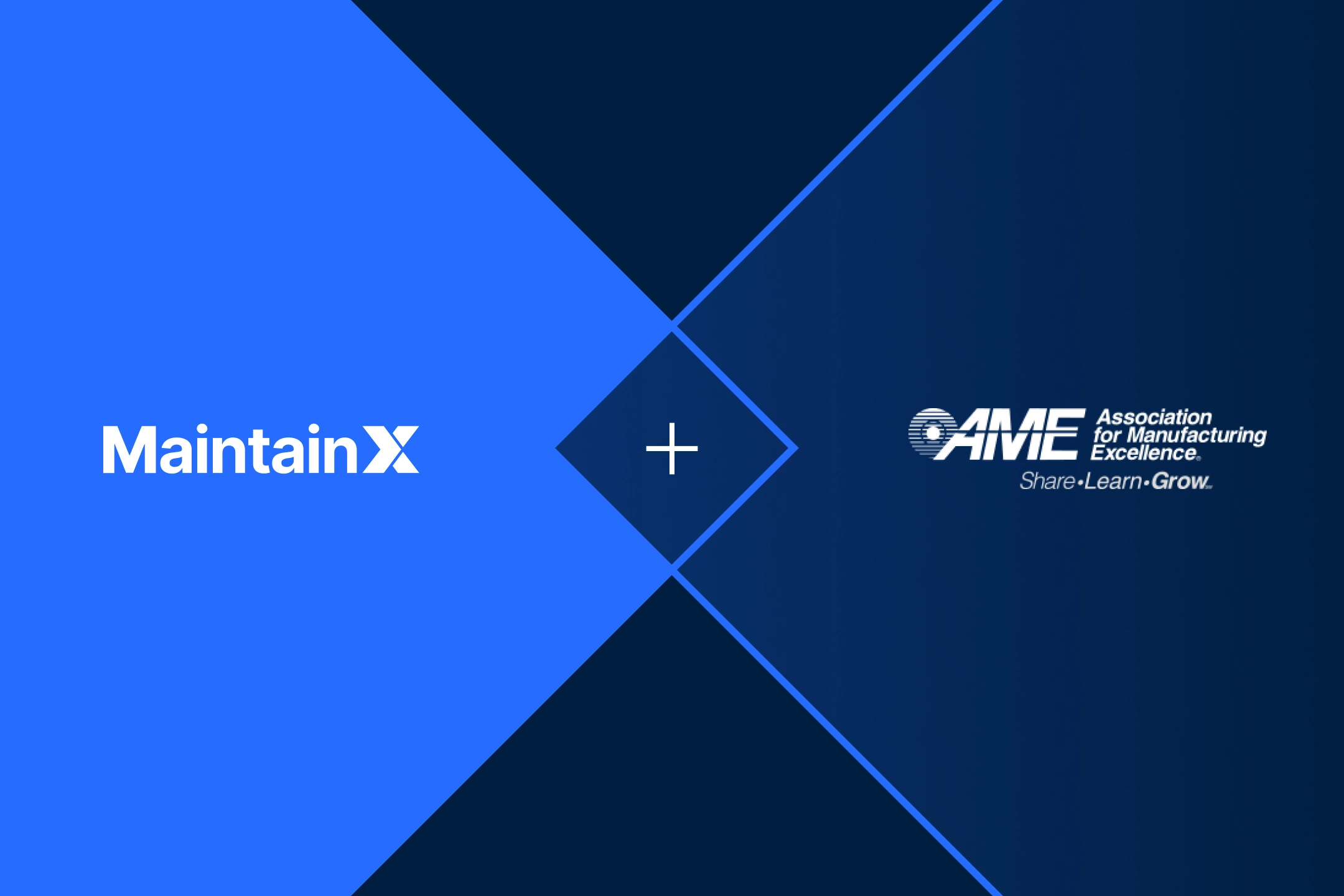
The MaintainX team joined lean manufacturing leaders in Atlanta last week to share best practices and industry trends.
The Association for Manufacturing Excellence (AME) International Conference welcomed more than 1,000 attendees seeking ways to empower their workforce and operate more efficiently.
Standardization, workforce development, and AI, were among the topics covered throughout the four-day event.
We also hosted MaintainX customers at a special event—the MaintainX Power Hour—where they shared best practices and gave input on our 2025 roadmap.
Here are some key takeaways from AME to help inspire your planning for the coming year.
Appetite for AI is high, but current adoption is low
If you’re feeling behind on AI, you’re not alone.
A presentation on the role of AI in reducing unplanned downtime attracted hundreds of attendees at AME. But very few of them were able to say that they are using AI today.
Data quality challenges were highlighted as barriers to adopting AI in the session.
Speakers urged companies to digitize and start building a robust data foundation to ready themselves for AI-powered predictive maintenance.
Some of the AI use cases highlighted at the conference included the ability to improve schedule compliance and upskill workers by streamlining their training.
Visitors to MaintainX’s booth were shown how quickly they could adopt AI to generate procedures, plan work more intelligently, and catch anomalies using MaintainX.
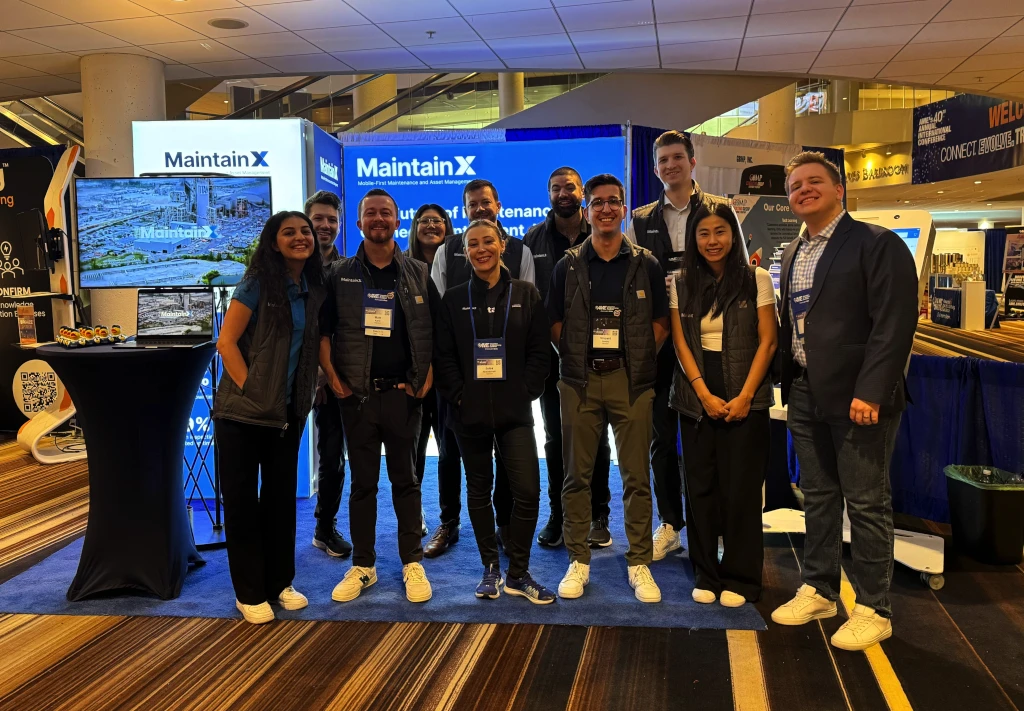
Innovation is critical to help upskill and retain workers
The operations leaders we spoke with at the conference were focused on providing technology and training to help nurture and empower their workforce.
Retaining and upskilling talented employees, and capturing knowledge from people that are soon to retire, were among people’s biggest concerns.
One of the keynote speakers addressed the labor shortage head-on. He called upon manufacturing leaders to walk the shop floor and identify innovation gaps affecting frontline teams.
The importance of adopting more automation and AI, both for developing talent and maximizing productivity, was also stressed during the presentation. Manufacturers were advised to work on providing the skills and tools workers need to evolve into roles that offer greater safety and long-term career growth.
The people that stopped by our booth were excited to see how MaintainX could streamline training using digital procedures and in-app communication.
Communicate often to inspire positive change
Practitioners also led workshops to help industrial companies improve their processes and overcome resistance to change.
We spoke with attendees leading a range of change initiatives, from eliminating paper to introducing total productive maintenance (TPM).
Change management strategies shared at the conference included:
- Presenting successes to leadership. Attendees were urged to celebrate wins early in their initiatives, however small they might seem, and communicate them to leadership on a consistent basis.
- Communicating purpose frequently. Team members should always understand their role in the project, how they are making an impact, and what’s in it for them.
- Consistent messaging. Several speakers explained the importance of preparing team leaders and supervisors to answer questions about change initiatives in the same way, to increase trust and avoid confusion.
At our Power Hour event, new MaintainX customers were inspired with change management tips from others that had rolled out MaintainX across multiple locations.
Customers then discussed how they’ve been using the system to drive standardization at scale, reduce costs, and put their data to work.
We’re hugely thankful to all customers who attended and gave valuable input for our 2025 roadmap.
If you’re not yet a MaintainX customer, book a tour today.
Learn more about MaintainX for lean manufacturing
Are companies using AI for predictive maintenance of industrial equipment?
Many companies are increasingly leveraging Artificial Intelligence (AI) for predictive maintenance of industrial equipment. AI algorithms analyze vast amounts of sensor data to detect patterns and anomalies that may indicate potential equipment failures. This proactive approach allows businesses to predict maintenance needs before issues arise, minimizing downtime and optimizing the performance of critical assets.
How can maintenance teams use historical data to improve maintenance processes in manufacturing facilities?
Historical maintenance data allows teams to analyze past performance, identify recurring issues, and pinpoint inefficiencies. Using this data, teams can adjust maintenance strategies, optimize schedules, and implement predictive maintenance to reduce failures and improve operational performance over time.
How does asset management software aid in the management of critical equipment in manufacturing facilities?
Asset management software provides real-time monitoring and detailed insights into the health and performance of critical manufacturing equipment. It helps identify wear patterns, optimize maintenance schedules, and ensure that vital machines remain in top working condition, reducing the risk of failure and increasing the lifespan of assets.
How does MaintainX support multi-location maintenance operations?
MaintainX simplifies maintenance for multiple locations by using a centralized platform. You can manage work orders, assets, and schedules across all sites from one dashboard, keeping your team consistent and compliant. The platform also allows you to share resources like templates and checklists so all locations follow the same best practices. This improves efficiency and reduces downtime, no matter how many sites you manage.
How do the reporting capabilities of MaintainX help improve maintenance management?
MaintainX offers robust reporting features that allow you to measure and improve your preventive maintenance program. Create custom dashboards to track critical metrics and generate at-a-glance insights to identify areas of improvement, improve resource planning, and drive operational excellence.
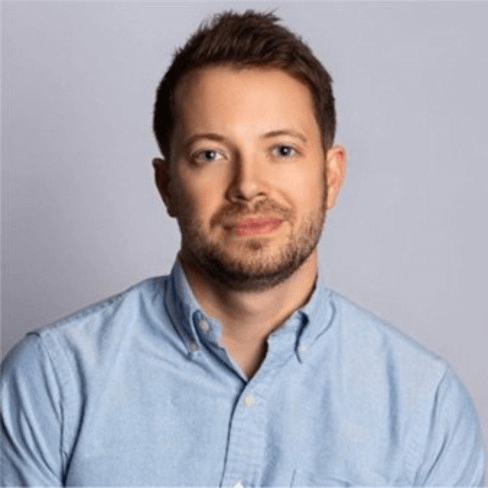
Colin Strachan is a Senior Product Marketing Manager at MaintainX, with a background in journalism and almost a decade of experience in SaaS marketing. In the past few years, he has worked with some of the world’s largest enterprises to adopt software that empowers their employees to work more effectively.