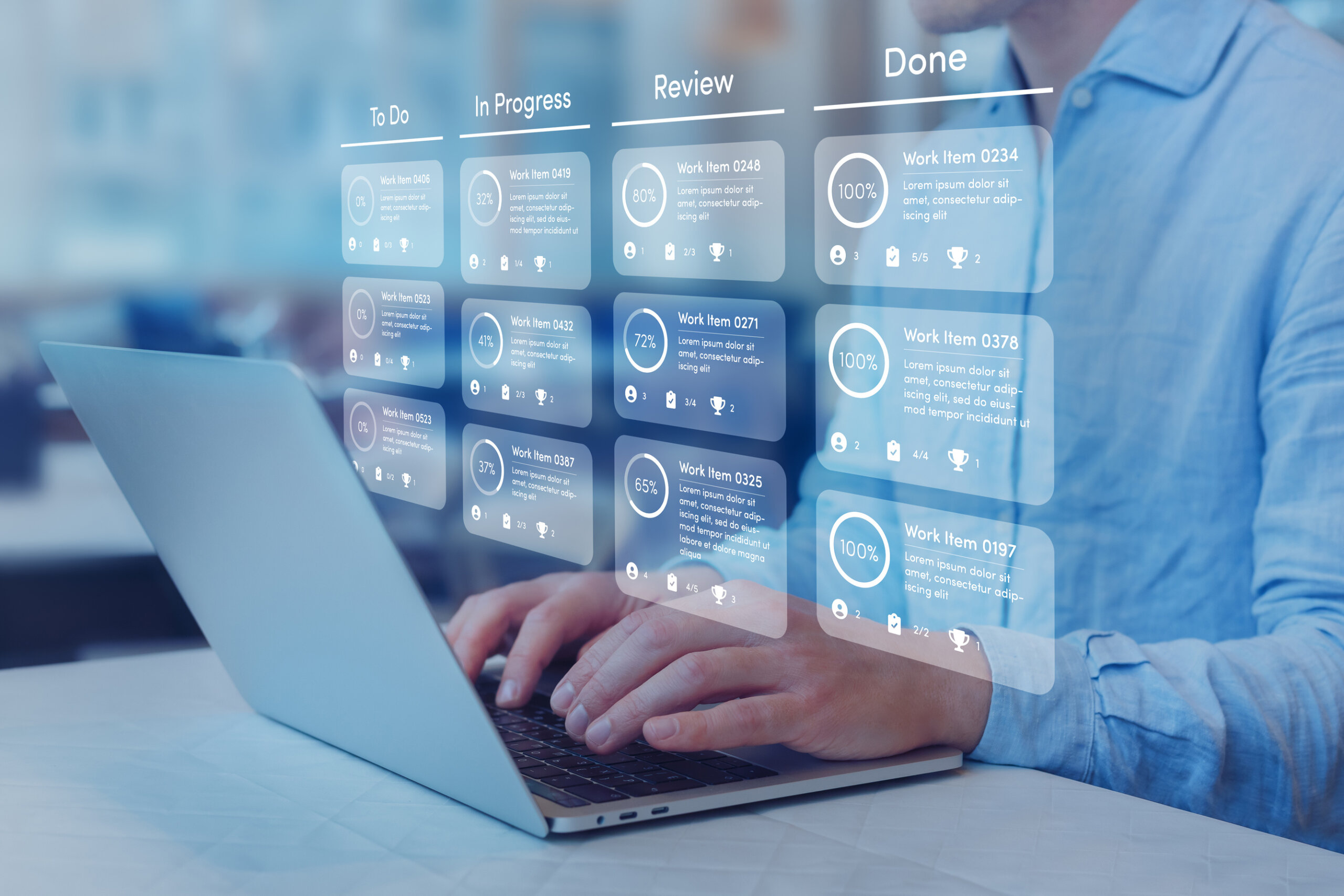
Kanban in lean manufacturing is a management methodology that uses visual cues to help teams manage and communicate the process of tasks through a workflow.
The system signals a need for action via a shared work board, allowing everyone involved in the process to understand what needs to happen next. Kanban systems help control production rates, allowing manufacturers to reduce wasted time, effort, and money while still meeting customer demand.
By only completing the next step when the Kanban signal indicates it’s time to do so, companies can reduce inventories, quickly identify quality defects, and work more efficiently and effectively.
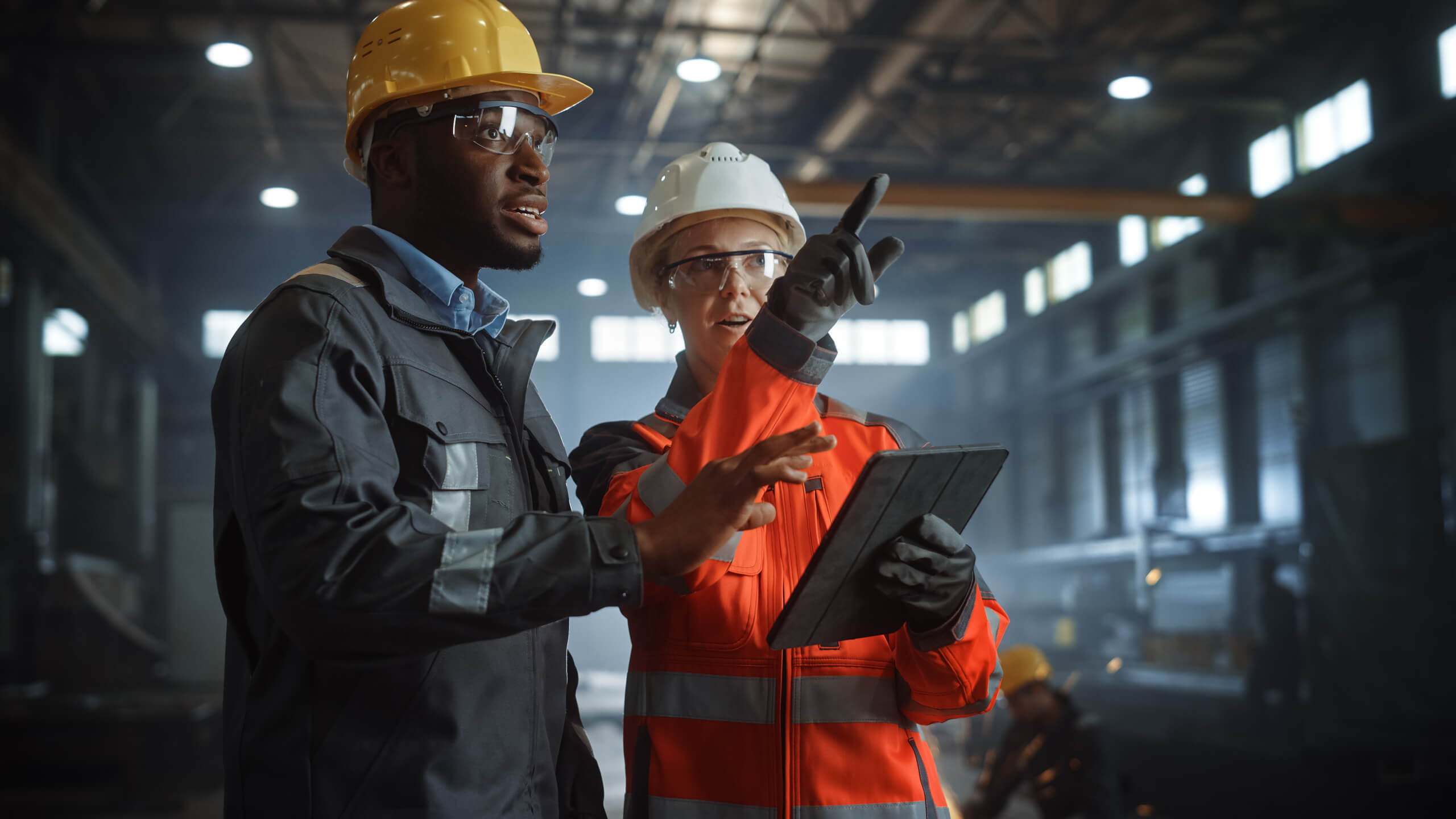
Where Did Kanban Originate?
Kanban is a Japanese word that translates to “signal card” or “card you can see.” First coined in the context of manufacturing processes in the 1950s, it has its roots in the Toyota Production System, as do many other lean concepts we use today.
The Japanese engineer Taiichi Ohno is credited with first developing and refining a visual scheduling system. He successfully implemented it for just-in-time (JIT) manufacturing. This JIT method relies heavily on kanban concepts to filter steps or tasks through a production line in a neat, optimized way.
Toyota’s dedication to adding value while reducing waste using lean production techniques like kanban has enabled it to remain at the forefront of manufacturing best practices. As a result, business use tools like Kanban in project management, software development, and a range of other sectors. Kanban provides an accessible way for teams across industries to stay on top of day-to-day tasks.
“Kanban strives to save companies time, money, and other resources by ensuring there is minimal downtime between tasks. In addition, kanban attempts to target bottlenecks before they occur, ensuring that you take steps in advance to avoid having work in process sit idly back while problems are fixed.”
Investopedia
What Is the Kanban Management System?
To achieve a successful Kanban implementation, you should follow six essential practices:
- Visualize the workflow. Represent the workflow visually to identify bottlenecks, make the work more transparent, and understand the flow of work.
- Limit work in progress. Restrict the amount of work in progress to improve focus, prevent multitasking, reduce lead time, and increase efficiency.
- Manage flow. Optimize flow by monitoring metrics, identifying bottlenecks, and continuously improving the workflow.
- Make process policies explicit. Clearly define and communicate process policies to help ensure consistency. Reduce any misunderstandings about how you want your teams to do work.
- Implement feedback loops. Get feedback from customers, stakeholders, and team members to help identify areas for improvement.
- Improve collaboratively. Kanban is a continuous improvement process. It encourages collaboration and experimentation to identify and solve problems, improve continuously, and evolve processes to better meet customer needs.
“As with implementing any other lean manufacturing tools you will need to do it as part of an overall philosophy within your business. . . Kanban is not something that is going to work overnight, nor is it something that can be just dropped into place without explanation or training. There is also no one size fits all solution that is going to be right for you.”
Lean Manufacturing Tools
How a Kanban System Benefits Your Manufacturing Business
Recognize Improvement Opportunities
When used correctly, kanban can lead to improvements across all areas of your business, including people, processes, management, and facilities.
With the Kanban management system handling process flow, each iteration is an opportunity for continuous improvement. In addition, Kanban systems quickly reveal bottlenecks and sticking points in real time. This allows departments like inventory management to more precisely manage stock levels and minimum order quantities determined by their supply chains.
Closing the gap with feedback loops after implementing system improvements means your team can further optimize the process based on its practical assessment.
Reduce Waste
Kanban focuses on visualizing the value stream. This allows you more detailed insight into where “Muda” or “uselessness”–one of the eight wastes–is in your production process.
Opting for a “pull” value stream, overlaid with Kanban management principles, means you will only be producing products based on customer orders. This approach eliminates overproduction and inventory waste.
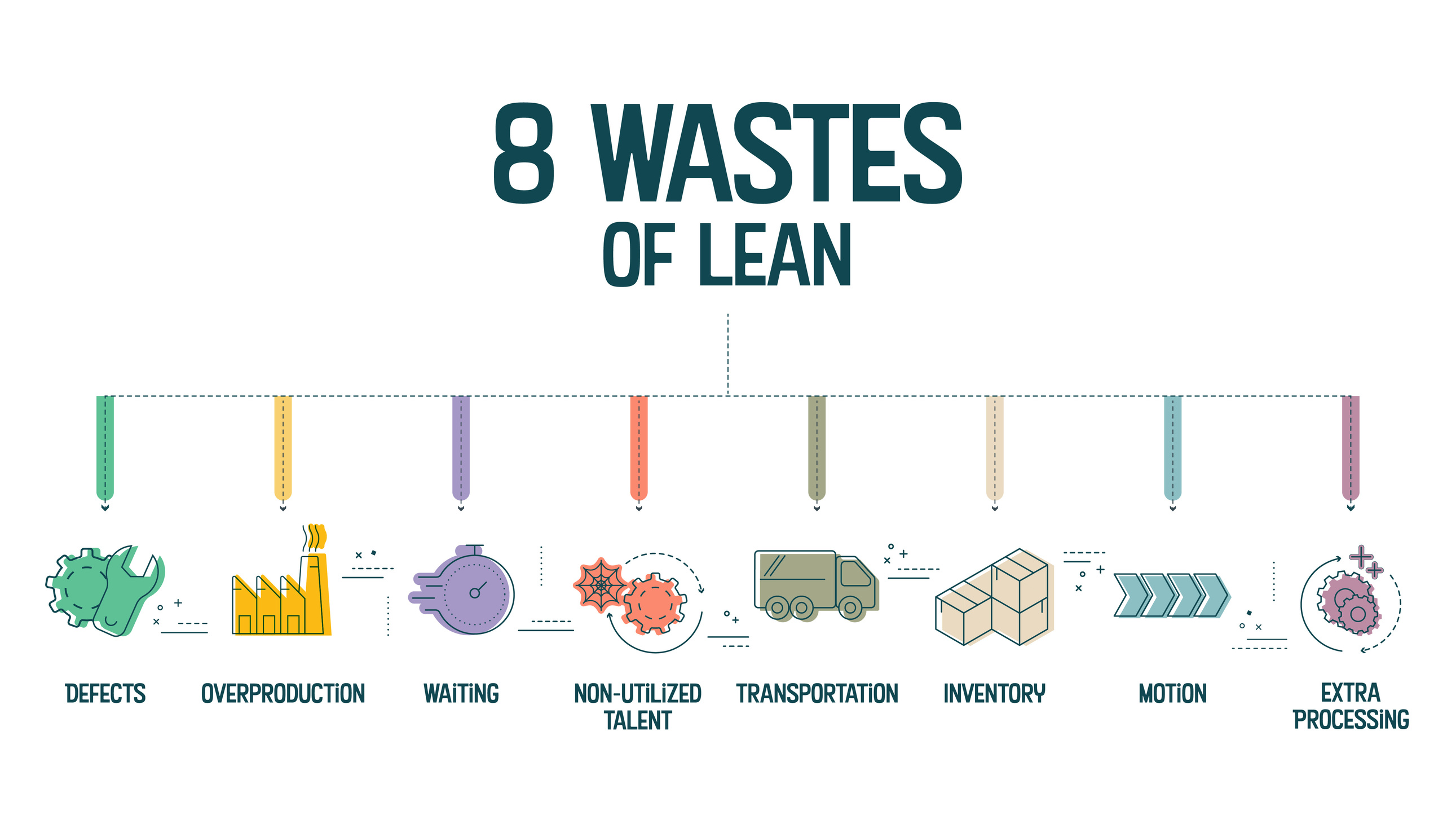
Reduce Bottlenecks
Kanban is a type of pull system that requests products or components as needed. As a result, businesses can drastically reduce unnecessary wait time. In addition, using Kanban to manage “what needs to be done next” keeps each team member aligned on a common goal in a way that is communicated for all to see.
Now everyone knows what needs to be done and what stock needs to be replenished. Eliminating bottlenecks from the work process is much easier.
Make Better Use of Idle Resources
Likewise, once we reduce bottlenecks, staff and machinery no longer sit idle waiting for their part in the process. They no longer need to wait on work in progress to arrive at their workstation. Idle time negatively affects staff engagement.
Utilizing information from sources such as your Kanban board, your ERP system, and WIP cycle time reports helps you locate inefficiencies in your current process. Once you know where there is excess idle time, you can adjust the manufacturing process to even out the utilization of resources.
Improve Business Agility
Lean tools like Kanban systems offer clear visual data to help your business become more agile. In addition, regularly reviewing how items move through the process reveals actionable insights.
Data from Kanban systems can highlight times of increased customer demand. Variance in lead times can be tracked and improved for a better customer experience. In addition, patterns and themes from your Kanban data can help you increase throughput and reduce cycle times.
Physical vs. Digital Kanban Systems
The traditional use of kanban cards begins with a kanban board, divided into columns that represent different stages in a process. For example, you might manufacture components that teams cut, fabricate, galvanize, and assemble. Each of these stages is represented on your board.
Of course, your board doesn’t have to be a traditional whiteboard or physical board in your factory. These days, digital kanban methods can be more effective. For example, they can automatically send out reminders when the next work item is ready to be moved down the line.
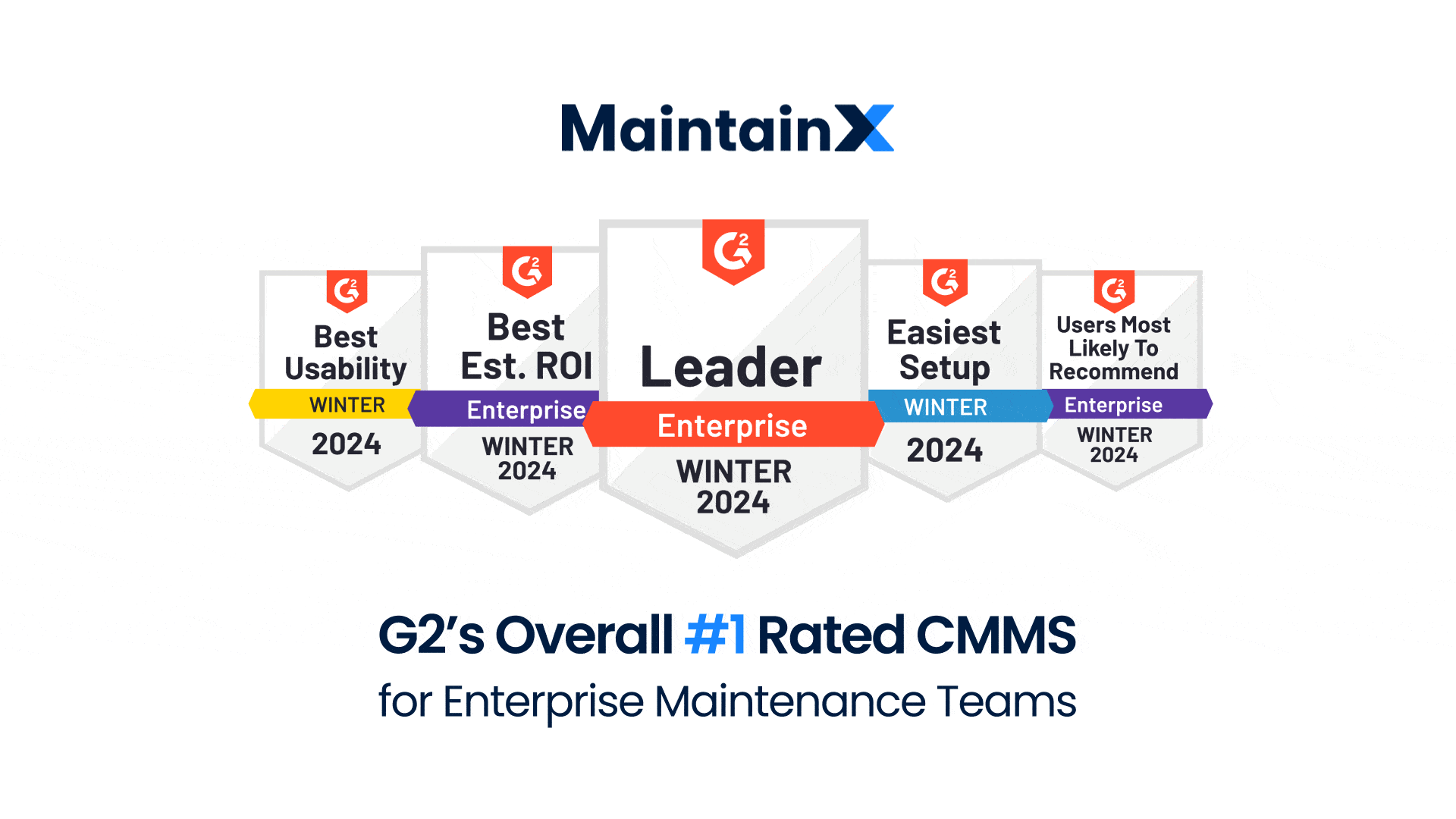
Let MaintainX Manage Your Kanban
Many ERP systems, like MaintainX, allow minimum and maximum stock levels to be set, along with mapping out average demand for a product, lead time for components, and other critical information. MaintainX also includes work order management and reporting features for deeper insights into WIP times, MTTR, asset utilization, and more.
MaintainX makes light work of managing manufacturing essentials like SOPs, templates, checklists, inventory management, and work orders, bringing increased depth to your Kanban planning. Learn how other manufacturers use MaintainX.
FAQs
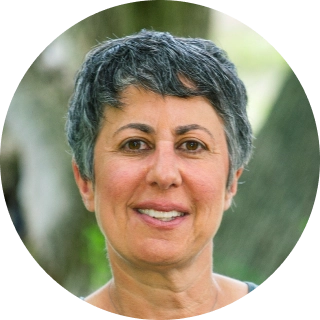
Caroline Eisner is a writer and editor with experience across the profit and nonprofit sectors, government, education, and financial organizations. She has held leadership positions in K16 institutions and has led large-scale digital projects, interactive websites, and a business writing consultancy.