Karn Custom Woodwork Built a Successful Preventive Maintenance Program in under a Year
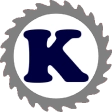
Wauseon Machine, founded in 1983 and headquartered in Wauseon, Ohio, has established itself as a leader in precision machining, custom robotic automation, and tube end-forming equipment. With 300 different pieces of equipment in their Ohio-based factory, the company faced growing challenges, including aging machinery, which they maintained using largely paper-based systems. “How we handled maintenance was to write stuff down on paper and store it in file cabinets,” says Bill Johnson, Wauseon’s Vice President of Precision Machining.
As part of their lean journey, Wauseon sought to improve Overall Equipment Effectiveness (OEE) and transform their maintenance operations. “What we want, from a department level on the maintenance side, is to be an invisible supplier so that nobody has to talk about maintenance,” explains Bill. “It just happens in the background.”
To realize this vision, Wauseon began searching for a simple yet powerful CMMS that could streamline their processes and boost efficiency.
In the past, Wauseon Machine’s maintenance process was bogged down by a slow, paper-based system that delayed repairs. Technicians would fill out maintenance repair forms and wait for approval. Maintenance managers often couldn’t review these forms immediately, especially if they were in meetings or offsite, and without approvals, technicians couldn’t act. This led to critical delays, with the team losing valuable time and urgent repairs often stalling.
In addition to an inefficient repair process, Wauseon Machine struggled to properly track the team’s maintenance work and history. With no centralized platform to assess work orders or review maintenance history, the team depended on a combination of spreadsheets. Because of this siloed information, they had a limited view of their operations. That meant spotting recurring issues and taking proactive steps to optimize processes was difficult.
Another significant challenge Wauseon faced was the lack of an organized parts inventory, resulting in frequent misorders and inflated costs. Without a centralized system, the team often ordered the wrong parts, leading to unnecessary delays and extra expenses.
When the team ordered the wrong part, they often ended up keeping—and storing—it to avoid hefty restocking fees, leading to strained storage space. Moreover, because there was no vendor tracking system, the team sometimes had to source parts from resellers, which were more expensive than they should be. “They buy it from somebody else who buys it from somebody else, and everybody marks it up,” Bill explains. This lack of control over inventory management created inefficiencies that impacted both time and budget.
To tackle these challenges and further its lean initiatives, Wauseon Machine brought on MaintainX to streamline its maintenance management, improve its record-keeping, and make maintenance “invisible.”
Going into the market for a CMMS, the Wauseon Machine team had a list of essential features they knew they couldn’t compromise on. These features included:
In MaintainX, the team found a comprehensive solution that met—and exceeded—their requirements, offering features the team wasn’t even thinking about initially. “Meters was one of them,” says Bill, highlighting MaintainX’s meter-based maintenance scheduling as a key feature that stood out.
Additionally, MaintainX’s continuous updates kept expanding its functionality, providing Wauseon with more value than they anticipated. “It looks like every month or so there's something new being added that can be used. You're broadening the MaintainX capability,” Bill adds. Because the software continued to evolve, Wauseon Machine could be confident that MaintainX would continue to meet its growing needs.
Having used CMMS solutions before, Bill understood the importance of choosing an option his team would adopt. A system with a steep learning curve would discourage adoption and defeat the entire purpose of the implementation.
MaintainX’s simple, easy-to-use workflows—for everything from recording parts to managing work orders—convinced Bill this wouldn’t be a concern. “A new maintenance technician joined the team, probably a month and a half ago,” Bill says, “and he caught right on with this.”
Since adopting MaintainX, Wauseon Machine has completely transformed its approach to maintenance, shifting from a reactive model to a proactive system where 85% of maintenance tasks are now planned. This shift has led to significant improvements, with PM completion rates rising from 60% to 100% and all critical assets now being under preventive maintenance schedules.
The impact on efficiency has been profound. As Bill notes: “I think it saved our maintenance team a good 45 to 50% of work time from what our old system was.” This newfound efficiency has allowed the maintenance team to focus more on strategic initiatives, improving overall productivity across the facility.
Wauseon Machine has seen tangible improvements in its operational efficiency since implementing MaintainX. Bill estimates that the company’s Overall Equipment Effectiveness (OEE) increased by six percentage points directly because of MaintainX. He explains that “we didn’t have a lot of the lean metrics before, and OEE was one of the important ones. Over a 16-month period before and after implementing MaintainX, we saw a six percentage point improvement.”
Preventive maintenance has also seen major progress. Before, the team struggled with on-time PM completion rates, hovering around 60%. But thanks to better communication and tracking through MaintainX, that rate has now reached 100%.
The switch from paper to digital has also significantly improved response times for managing work orders. Bill shares that MaintainX’s mobile app has transformed how his team handles requests: “Our maintenance guys have the app on their phones, so managers just approve the work order, they get a notification immediately, and it’s on their schedule.” This seamless process has reduced delays, making the team more efficient in tackling tasks.
Beyond just managing equipment, the team has started using the system to track vehicle maintenance and automate work orders based on mileage or hours used. This automation ensures that nothing slips through the cracks, keeping both vehicles and machinery running smoothly without manual intervention.
Wauseon Machine has also seen considerable improvements in parts management thanks to a proactive approach enabled by MaintainX. With MaintainX’s robust record-keeping, the team can accurately forecast their parts needs and get ahead of any emergencies. “If you have a bearing that you know is going to last eight months, you can plan to replace it by the seventh month,” says Bill. This planning minimizes downtime, as the part is already on hand and available for the team to use immediately.
In addition to reducing downtime, optimizing parts inventory management with MaintainX has led to substantial cost savings when purchasing these parts. Ordering in advance means the team can avoid expensive rush orders and can research the market for the most cost-effective options. Bill explains, “We can go out and research where we can get the same product for the best price and then put it in our parts inventory, so our guys know to use that part.” This diligent cost control strategy has resulted in a 14.5% reduction in parts costs, saving the company ~$60,000 annually.
Wauseon Machine is looking to build on the success they've already achieved with MaintainX by expanding its use into new areas. As part of their strategic plan, they intend to integrate SOPs from other departments into the platform, streamlining operations and reducing the need for multiple software systems.
In addition, Wauseon aims to take better advantage of MaintainX’s asset tracking features. “When a machine goes down on the floor, we can record it as offline,” Bill says. “Then, when we get the machine up and running, we can toggle it back online and track how long that machine was down.”
Fleet tracking and downtime monitoring by asset are also on the horizon, allowing for even greater visibility into equipment performance. As Bill explains, “If we can pull everything into one easy-to-use platform, it makes things so much easier for people.”
With these goals in mind, Wauseon is confident that MaintainX will continue to be a critical tool for their future growth and operational excellence.
Get more done with MaintainX