How Titan America Decreased Unplanned Maintenance by 30% with MaintainX
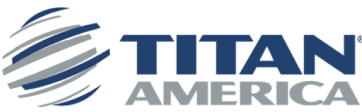
Interroll is a global leader in material handling solutions, with more than 20 manufacturing facilities worldwide. They run a production system steeped in lean principles with several key pillars. “One of those key pillars for us is digitization,” says Scott Quesenberry, Lean Engineer at Interroll’s facility in Wilmington, North Carolina.
As part of the digitization efforts, Interroll adopted a legacy maintenance management system. While the system helped reduce paper use, the team soon found it came with challenges. “It was paperless because it was all online,” says Scott. “But it still took up a lot of time.”
In addition, the team found it difficult to use, which impacted adoption—a fact echoed by Interroll’s Global IPS Director, Elisabetta Brunetti. “I needed a simple and user-friendly tool,” Elisabetta says.
After continually losing valuable time, encountering usability issues, and experiencing low adoption, Interroll decided that it was time for a change.
One of the main challenges Interroll faced with its previous maintenance system was its lack of usability. While it had helped the company go paperless, the platform didn’t provide the flexibility or ease of use the Interroll Production System prioritizes. “We look for tools that have a lot of flexibility, adaptability, and a user-friendly interface,” says Scott. Unfortunately, their previous system fell short. At the time, it didn’t even have a mobile app, which created further obstacles for the team when managing maintenance tasks on the production floor. Without a quick and efficient way to submit requests or updates, the system became more of a burden than a benefit.
Another major hurdle was the system’s low adoption rate among employees. Because the platform lacked native mobile functionality, team members found it cumbersome to use since they had to access it on computers. “It didn’t have the functionality of an app, which is obviously key,” Scott points out. This disconnect between the system’s design and the team’s day-to-day needs led to low engagement.
Team members avoided the software, opting for faster, though less efficient, alternatives. “They were using the intercom system to make requests because it was so much quicker than finding a computer and navigating through the system.”
Because their previous maintenance management tool lacked the functionality to cover all their needs, the team relied on additional platforms to handle specific tasks. “We had another system in which we were keeping all our quality gauges for calibration,” recalls Scott. They also used a different system for audits.
Reliance on separate systems for different functions made processes more complex. Plus, the lack of integration between systems meant data wasn’t centralized, making it harder to access critical information quickly. This fragmented approach highlighted the need for a more comprehensive solution that could streamline all maintenance-related tasks into a single, easy-to-use platform.
To handle all of these issues, Interroll implemented MaintainX across multiple locations to consolidate their systems, improve their response times, and take their maintenance management to the next level.
Given the challenges they faced with their previous system, the Interroll team prioritized ease of use when searching for a new platform. With a workforce reluctant to engage with complicated systems, they knew that a user-friendly interface was essential to successful adoption.
MaintainX’s intuitive design, which, in some cases, required no training at all, quickly won them over. “Ease of understanding and use played a crucial role in my decision-making process,” says Elisabetta, Global IPS Director. Features like the ability to easily attach photos to work orders further streamlined communication and improved day-to-day operations, making it clear that this was the right choice for their team.
MaintainX’s scalability was a key factor in their decision, as it offered flexibility for both large and small teams, ensuring it could grow with their needs. Scott and his team required a tool that could adapt to the varied demands of its global operations. From large-scale manufacturing facilities to smaller production lines, they needed a platform capable of supporting diverse processes without compromising on functionality. “As an IPS Director, I needed a simple and user-friendly tool with an intuitive interface that could be applied to different types of production, whether large or small—essentially, a scalable solution,” explains Elisabetta.
For Interroll, a seamless implementation process was critical, and the strength of MaintainX’s customer support played a key role in their decision. Having overseen several implementations over the years, Scott knew that strong support could make or break the transition to a new system. “I've implemented a lot of digital tools over the last three years, and to me, it's about customer support,” Scott emphasizes.
The ability to customize the tool to fit their specific processes was important, and MaintainX’s team was ready to assist. “We had training, and we were able to go through all the functionalities,” says Scott. “Within 24 hours, we would have everything populated.” Whether it was providing templates or offering quick responses to requests, the MaintainX team made sure the transition was smooth and efficient, with implementation at the Wilmington facility taking just around 4 weeks.
Beyond its current capabilities, the team also sought to purchase a solution that would continue to evolve alongside its business. MaintainX’s commitment to continuous development and regular feature updates was a major draw. Based on our previous experiences, we wanted to work with a provider that was committed to continuous development of its platform,” Elisabetta shares. “We wanted a partner that would grow with us and, over the months or years of our partnership, provide continuous improvements and new features that would help us optimize maintenance operations.”
She also highlights the platform’s versatility, noting that MaintainX isn’t just limited to maintenance. “Some productions have used it to manage improvement proposals, quality control, and more,” said Elisabetta. This flexibility and forward-thinking approach ensured that MaintainX would continue to meet Interroll’s needs well into the future.
One of the most significant outcomes of Interroll’s implementation of MaintainX has been the time saved on admin work. Scott estimates that the team is saving over five hours a week just in terms of time to upload information into the system.
The streamlined process has also improved their handling of work orders, reducing downtime and increasing reaction time significantly. “Now, requests are submitted within less than two or three minutes, get approved, and are assigned to a maintenance team,” Scott explains. “The response time’s quicker, and I’d say we’ve improved downtime and reaction time by 15 to 20%.”
The transition to MaintainX has also bolstered Interroll’s preventive maintenance efforts, providing the team with a thorough and transparent way to track their work. “It has made the entire process accurate and transparent, from reporting an issue to its resolution,” Elisabetta says.
Regular checklists and work orders have ensured that inspections are timely and thorough, which has increased both machine operational efficiency and overall production. Scott points out that MaintainX can be seamlessly linked as a hyperlink on production boards and other interfaces, simplifying the request process. “Now, operators and team leads can easily track requests and timestamps,” Scott says. This feature has enhanced communication and accountability, allowing for real-time updates and better tracking of requests.
MaintainX has improved Interroll’s ability to record and address problems with features that allow users to document issues in greater detail. Being able to add pictures and videos to work orders, for example, enhances a team’s ability to respond properly. As Scott says, “With the app, you can take pictures of the actual issue, like a leak in a hydraulic hose, and document it in detail.” This capability has allowed the team to capture issues more precisely and address them more effectively. This also adds a visual dimension that enhances the clarity and depth of their maintenance records.
Because MaintainX offers features for a broad range of processes, Interroll has been able to deploy the solution in multiple areas beyond work order management. “We use MaintainX for audits, including process audits, TPM audits, and quality gauge management,” says Scott. As a result, Scott’s team has consolidated several different processes and systems into MaintainX. “We've been able to eliminate two other tools by using MaintainX,” Scott says, estimating that the team is saving between $8,000 and $10,000 as a result.
As Interroll continues its journey with MaintainX, the team aims to implement the software across even more locations. The goal, Scott says, is to deepen the organization’s commitment to lean principles while enhancing operational efficiency to eliminate downtime.
"From a lean perspective, MaintainX is only going to add more value,” Scott says, explaining that he aims to go from identifying issues to understanding their underlying causes. “It’s going to be about root cause analysis, improving on the high runners, and eliminating downtime.”
With MaintainX's user-friendly interface and robust reporting capabilities, Interroll is poised to drive significant improvements toward making downtime a thing of the past.
Get more done with MaintainX