Redimix Cuts Year-Over-Year Maintenance Costs by 53% With MaintainX
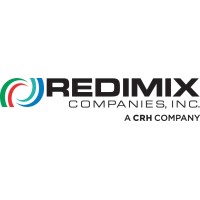
If you’ve ever visited the Golden Arches, you may have wondered: Why does Coke always taste better here than elsewhere? The answer is standard operating procedures (SOPs). Coca-Cola delivers Coke syrup to McDonald’s restaurants in stainless steel tanks.
Everything from the soda water filtration process to the wide-set straws creates the restaurant’s signature beverage experience. Additionally, every menu item, employee task, and piece of machinery has its own SOP.
Take the McRib, for example. The company provides franchise owners with an entire book’s worth of SOPs to make one sandwich. This ensures all locations are refrigerating patties at the same temperature, maintaining grills the same way, and providing customers with similar tasting experiences.
With that said, McDonald’s gives franchise owners complete control over how they organize, execute, and oversee SOPs—that’s where our story begins.
Steve began organizing the restaurants’ SOPs using Google Tasks. He used the familiar platform to create checklists before printing and distributing them to store supervisors. Initially, the Nisbets only had one maintenance technician splitting his time between three stores. However, as the couple slowly took on more locations, the Nisbets made some crucial adjustments.
The Nisbets became franchise owners to experience more freedom. So, why were they spending half their workweek editing checklists, distributing them, and visiting store locations to oversee quality control?
"This is the program I was dreaming of. If I could create something this would be it."
“Before, I would have to make lots of phone calls assigning maintenance tasks,” Steve said. “Now, I wake up, check the alerts, and review the status of each of my store’s assigned work orders. The technicians are happy because they’re getting fewer phone calls, fewer text messages, and can plan their days around assigned app priorities. It’s a life-saving application—it has saved me at least 20 hours a week.”
Now Steve has a full-blown Operations and Maintenance communication system. Steve invited his store supervisors, managers, maintenance technicians, training supervisor, and business partners to join his MaintainX organization. Now, everyone can conveniently communicate from one place regarding O&M issues.
Once COVID hit, Steve immediately turned to his MaintainX app for support. He assigns store managers recurring digital sanitation checklists to enforce COVID-19 safety guidelines. Steve also now has a digital audit trail of who completed which checklists and when. MaintainX allowed the Nisbets to social distance and conduct business completely remotely during the onset of COVID lockdowns.
Creating a central point of truth has been a major benefit. Every question and answer regarding an assignment is communicated within a work order comment thread. “With regular texts, you can’t remember who responded or where,” Steve said. “In comments, I love that I can say, ‘Hey, did you order this part?’”
"It’s a life-saving application—it saves me at least 20-30 hours a week."
Steve’s maintenance-management search initially led him to three platforms, all of which proved too difficult to use. Eventually, he stumbled upon MaintainX and quite literally found the app of his dreams.
“This is the program I was dreaming of. If I could create something this would be it” Steve said. “It’s the simplicity of it. MaintainX has a lot of features, but not overwhelming ones I would never use.”
Over the next several weeks, Steve dove headfirst into digitizing McDonald’s SOPs, developing new workflows, and granting more autonomy to store supervisors and maintenance workers.
Result
McDonald’s Corporation has taken notice of how smoothly Steve’s seven restaurants are running. The company is so impressed that they are now encouraging new Florida franchise owners to visit Steve to learn more about how he streamlines O&M with MaintainX.
Though Steve and his wife always enjoy training new owners in person, they plan to travel more soon. Their goal is to continue automating business processes, so they can run their restaurants from anywhere on the road.
Steve can now track:
Steve’s training manager also is enjoying how much faster it now is to explain how McDonald’s produces “the world’s greatest Coke” with digitized SOPs!
"I think a lot of people are hesitant to change old systems, but it’s worth it. The app is extremely simple to use. My team picked it up quickly."
Get more done with MaintainX