Breeze Thru Car Wash Empowers Employees by Revolutionizing Work Order Management
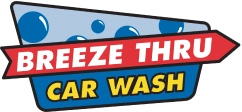
PharmaNZ is a family-owned nutraceutical company that manufactures health supplements for the world’s leading brands. The company produces over 250 tonnes of powder blend products, 10 million tablets, and 70 million hard-shell capsules annually for clients worldwide. The 30+ person company founded by Director and Owner Peter Lehrke is led by Scotty Death, Chief Operations Officer, and his wife, Katrina, the Chief Executive Officer.
With increased regulatory oversight and the slowdown of the global economy, Scotty knew that the company’s reliance on manual record-keeping and reactive maintenance would cost them valuable time, resources, and money in the long run. He knew he had to be proactive and get ahead of the problem before it materially impacted the business.
“Being audit-ready at every moment is PharmaNZ’s approach to the myriad of requirements we need to meet, as we could be audited with no notice. Managing the documentation requirements was labor intensive and opened the door to human error. Paper-based systems also did not enable easy trending and analysis to support good decision-making on capital expenditure.”
As a pharmaceutical manufacturing company, PharmaNZ is subject to extensive regulatory oversight, including inspections from the Food and Drug Administration (FDA), a quarterly MPI audit, a Medsafe Good Manufacturing Practice (GMP) inspection every two years along with a variety of other external audits
In order to complete these inspections and demonstrate compliance to the auditors, PharmaNZ needed to sort through massive amounts of records to find and share the necessary paperwork. “Paperwork was our biggest hamstring,” Scotty says. “We would have to bring out binders and binders of paperwork, and the auditor would have to sit there looking through each record.”
This manual process created multiple challenges for Scotty and the PharmaNZ team: First, the sheer amount of labor required to prepare the paperwork for each audit put a lot of pressure on the team.
After sorting through all the records, there was the question of whether they were comprehensive: “Even with all the records on hand, we weren’t always sure if the information would be enough for the auditor as paper-based systems have their limitations.”
And more often than not, the records on hand risked inaccuracy. As Scotty says, “You have more human error with paperwork, obviously.”
With the economic slowdown, Scotty was also focused on reducing unnecessary maintenance costs. “Times are definitely tough over on this side of the world,” Scotty says. “The cost of living and interest rates are definitely making things difficult, and we needed to find ways to reduce costs across the entire organization.”
Up to this point, PharmaNZ had relied almost exclusively on a reactive maintenance strategy. Regular preventive maintenance was a challenge to coordinate and manage in a standardized way. “We were doing some critical preventative maintenance work,” Scotty says, “but not in a manner that was best in class, as scheduling on paper does not enable the best resource planning.”
Depending mainly on a reactive maintenance strategy meant PharmaNZ spent close to NZ$100,000 each year on fixing assets when they eventually broke down. Unreliable inventory management made matters worse—the team often found that critical parts were not readily available when needed and had to either wait for weeks for the part to arrive or pay a hefty fee for express shipping. This meant longer downtimes, decreased production capacity, and higher maintenance costs for PharmaNZ.
To tackle these challenges, Scotty and PharmaNZ brought on MaintainX to streamline regulatory compliance and level up their maintenance program from a reactive to a proactive approach.
MaintainX stood out from the rest of the pack because of its best-in-class features that directly addressed PharmaNZ’s business challenges, and the constant stream of product improvements released by the team. “Even during the trial and the early stages, you guys were releasing feature updates,” Scotty says. “If I can see you guys are continuously releasing updates, it gives me hope that you're listening to me and other users.”
In addition, Scotty was convinced by MaintainX’s intuitive user experience. “I trialed MaintainX and other platforms to see how intuitive the platform was and how easy it was to use on PC, laptop, tablet, and mobile. MaintainX took home the prize by a wide margin” This first-hand experience with the product, coupled with glowing third-party reviews from other MaintainX users helped to seal the deal for Scotty.
Before MaintainX, it took Scotty and his team significant time to pull out all the binders and ensure the paperwork was available for the auditors. Now, with MaintainX, Scotty and his team don’t have to do much at all. Instead of spending days sorting through stacks of paper to find the necessary documentation, they can easily find the requested maintenance data right in the CMMS—complete with notes, pictures, and videos—with a simple click of a button.
Now, for most audits, Scotty simply opens up MaintainX for the auditor and lets them go through the platform to find the required documentation for the audit. “With MaintainX and the audit log, we've got procedures in there, we've got signatures at the bottom of the procedure, we've got due dates in there, we can put comments in there, we can put photos in there. Hence why, when the auditor looks at it, they barely ask me any questions.”
The PharmaNZ team can now save hours of valuable time when completing audits. “We easily save 3 to 4 hours during our GMP audits now,” Scotty says.
“In previous years, we spent nearly NZ$100,000 on reactive maintenance. Since then, it's down to around NZ$30,000.”
Through the partnership with MaintainX, PharmaNZ has transitioned from a reactive maintenance strategy to a proactive one. They increased their preventive maintenance work by what Scotty estimates to be around 200%, eliminating the team’s reliance on external contractors to fix their equipment. “You're able to fix something small earlier on before becoming huge and reduce the amount spent on fixing big problems,” Scotty says.
As a result, PharmaNZ has reduced maintenance spending by over 70%. “In previous years, we spent nearly NZ$100,000 on reactive maintenance. Since then, it's down to around NZ$30,000.”
Improved parts inventory with MaintainX has also driven further cost savings for PharmaNZ. In the past, PharmaNZ would need to order parts after a breakdown. “The parts we need aren’t just a bearing down the road,” Scotty says, explaining that these parts often required precision engineering, a process that was not only expensive but also prolonged downtime. “We'd be waiting a week for that part to come back to go back onto the machine.” Now, with MaintainX, PharmaNZ can ensure they maintain optimal inventory levels on critical parts to ensure they never stock out. With the right parts in stock, technicians can get assets back up and running much quicker, eliminating the downtime and production losses that would otherwise occur.
In addition to solving its core problems of compliance and maintenance spending, PharmaNZ has also seen a positive impact on its quality and engineering processes. Calibration has been a critical issue for PharmaNZ, with the maintenance team previously relying on the quality assurance team and a paper-based system to manage it.
With MaintainX, Scotty has absorbed calibration as part of the maintenance function, freeing up the quality team to focus on other critical work. “Purely because of being able to utilize MaintainX’s procedures and load calibration reports, we were able to lighten the load off of the quality team so that they could focus on other critical matters,” Scotty says.
Scotty is confident that his team is far from achieving all they can with MaintainX. “We are definitely far from hitting the peak with our savings from MaintainX—It’s only going to get better.” He sees integrations with PLCs to implement predictive maintenance as the next step in PharmaNZ’s evolution. “MaintainX will definitely get us to predictive maintenance rather than just preventive maintenance,” Scotty says. “I'm looking forward to the integrations.”
Looking further down the horizon, Scotty and the PharmNZ team are looking to use MaintainX to improve financial oversight, further optimize inventory parts management, and move PharmaNZ closer to a culture of total productive maintenance. This all aligns with PharamNZ’s mission of Creating a Healthier World, and with their values of Operational Excellence.
“MaintainX has unlocked our ability to level up our maintenance operations. I’m excited to continue working with the MaintainX team to build a world-class maintenance team and program at PharmaNZ.”
Get more done with MaintainX