Construction companies waste time and money when they can't track equipment effectively. Missing tools, breakdowns, and poor resource allocation hurt project timelines and profits. Effective construction asset management gives you the structure to overcome these obstacles.
Key Takeaways
- Construction asset management tracks, maintains, and optimizes physical assets throughout their lifecycles.
- Implementation reduces downtime, extends equipment lifespan, and improves regulatory compliance.
- Best practices include centralized tracking systems, preventive maintenance schedules, and regular inventory audits.
- Digital solutions streamline workflows and provide real-time data for informed decision-making.
What is construction asset management?
Construction asset management is a strategic approach to tracking, maintaining, and optimizing physical assets throughout their lifecycle while aligning with broader business objectives. This comprehensive system manages everything from procurement to replacement of equipment, tools, vehicles, and resources.
Construction asset management maximizes value and cuts costs. It goes beyond basic record-keeping to include:
- Setting and tracking key performance indicators (KPIs) tied to business goals
- Developing strategic maintenance approaches based on asset criticality
- Making data-driven decisions about resource allocation and capital investments
- Analyzing lifecycle costs to optimize replacement timing
Robust asset management systems give construction firms complete inventory visibility across all sites. This visibility supports long-term growth and profitability.
Effective construction asset management relies on several key components:
- Asset tracking capabilities to monitor location and usage
- Maintenance scheduling to prevent unexpected breakdowns
- Inventory management to ensure availability of necessary equipment
- Compliance tracking to meet safety standards and regulatory requirements
- Performance monitoring to identify inefficiencies and improvement opportunities
- Strategic planning to align asset decisions with organizational objectives
The benefits of construction asset management
Construction asset management delivers tangible value to construction businesses through operational improvements and cost reductions. Implementing a structured system produces several immediate benefits.
Regular maintenance based on usage data and maintenance history dramatically reduces unexpected breakdowns. This preventive approach keeps projects moving forward without costly interruptions.
Proper maintenance scheduling extends the lifespan of assets. Construction equipment represents a substantial investment, and maximizing its useful life directly impacts the bottom line. Tracking maintenance activities ensures assets receive timely service, preventing both expensive emergency repairs and premature replacement costs.
Real-time asset tracking improves resource allocation. Construction managers gain visibility into equipment availability across multiple construction sites, enabling them to make informed decisions about resource deployment and eliminate redundant purchases and rental costs.
Well-maintained equipment improves safety for workers and reduces accident risks. Detailed maintenance records help companies prove regulatory compliance during inspections. This documentation is especially valuable for equipment that must meet strict safety standards.
Digital asset management systems streamline workflows and boost operational efficiency. These systems eliminate manual processes and deliver real-time data, enabling construction teams to respond more quickly and adapt to changing project requirements.
Construction asset management best practices
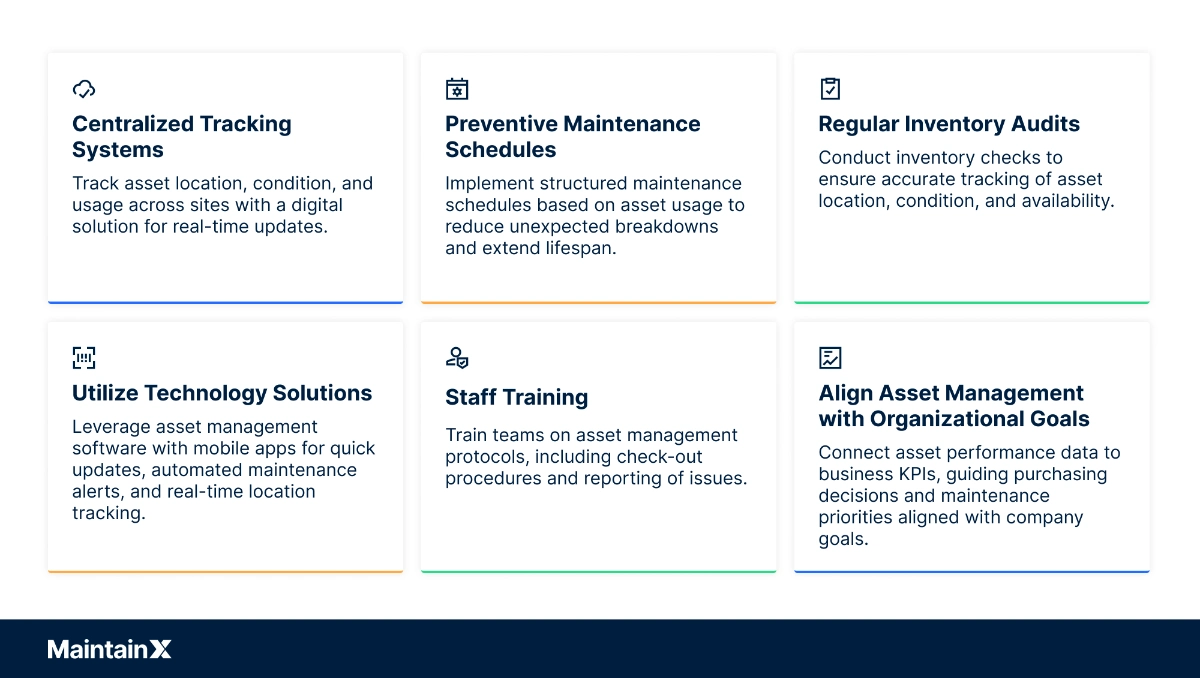
Implement centralized tracking systems
A centralized asset tracking system forms the foundation of effective construction asset management by providing visibility into all physical assets across locations. The system should track essential information, including:
- Current asset location
- Asset condition status
- Complete maintenance history
- Purchase date and warranty information
- Usage metrics and performance data
Choose tracking solutions that work across all of your sites and integrate with existing workflows. Mobile apps let field teams update asset information instantly, keeping your inventory database accurate.
Establish preventive maintenance schedules
Create and follow structured maintenance schedules based on manufacturer recommendations and usage patterns to significantly reduce equipment breakdowns and repair costs.
The process requires:
- Documenting manufacturer maintenance guidelines for each asset
- Scheduling routine maintenance based on calendar time or usage metrics
- Recording all maintenance activities with sufficient detail
- Analyzing repair history to identify recurring issues
- Adjusting maintenance intervals based on performance data
Construction equipment management software can automate these schedules, sending notifications when maintenance is due and tracking completion. This proactive approach extends asset lifespan while minimizing project disruptions.
Conduct regular inventory audits
Perform regular inventory audits to ensure accuracy between physical assets and tracking records. Construction companies should establish a consistent audit schedule to verify asset location, condition, and operational status. These audits serve multiple purposes:
- Confirming the location of all tracked assets
- Identifying missing or damaged equipment
- Updating asset condition assessments
- Verifying that all assets have proper identification tags
- Reconciling discrepancies between physical inventory and system records
The frequency of audits depends on project scale and equipment value, but quarterly checks are the minimum standard for effective asset management. Construction sites with high-value equipment may require monthly verification.
Utilize technology solutions
Construction asset management software provides purpose-built tools to streamline operations and improve decision-making. These technological solutions offer significant advantages over manual tracking methods:
- Barcode or RFID scanning for quick asset identification
- Mobile applications for field data gathering and updates
- Automated maintenance alerts based on usage metrics
- Real-time location tracking of valuable assets
- Detailed reporting capabilities for analysis and planning
When selecting a construction asset management solution, prioritize user adoption by choosing software with intuitive interfaces and mobile accessibility. The system should integrate with existing construction management software to create a unified workflow.
Train staff on protocols
Construction asset management succeeds only when all team members follow established protocols. Comprehensive training ensures consistent implementation across the organization, covering:
- Proper check-out and check-in procedures
- Documentation requirements for maintenance activities
- Reporting processes for damaged or malfunctioning equipment
- Correct usage of tracking tools and software
- Importance of timely updates to asset information
Construction companies should designate asset management champions at each job site responsible for ensuring compliance with established procedures. Regular refresher training maintains awareness and addresses common issues.
Align asset management with organizational goals
Effective asset management extends beyond day-to-day operations to support strategic business objectives. Construction companies should:
- Connect asset performance metrics to overall business KPIs.
- Use asset data to inform capital investment decisions.
- Align maintenance priorities with project deadlines and business cycles.
- Analyze equipment ROI to improve future purchasing decisions.
- Review asset management strategies quarterly with leadership.
This strategic approach transforms asset management from a maintenance function into a competitive advantage that supports growth and profitability targets.
FAQs on Construction Asset Management
Selecting the right construction asset management system requires evaluating several key factors. The solution must align with your operational scale, integrate with existing systems, and provide mobile accessibility for on-site use. Prioritize systems offering:
- User-friendly interfaces that minimize training requirements
- Mobile capabilities for on-site data access and updates
- Flexible tracking options, including barcode and RFID capabilities
- Robust reporting tools for compliance documentation
- Cloud-based access for multi-site visibility
- Scalability to accommodate business growth
Request demonstrations from multiple providers to evaluate real-world functionality before making your decision.
Construction asset management systems deliver measurable improvements across multiple operational areas. These platforms help construction businesses:
- Reduce equipment downtime through preventive maintenance
- Decrease operating costs through optimized resource allocation
- Extend asset lifespan through proper maintenance scheduling
- Improve regulatory compliance through detailed documentation
- Enhance decision-making through real-time asset information
These improvements give you significant competitive advantages in project efficiency and profitability.
Construction asset management directly impacts project efficiency through several mechanisms. These systems eliminate time wasted searching for tools and equipment-transfer delays by showing real-time availability and location.
Preventive maintenance scheduling reduces unexpected breakdowns that cause project delays. Resource allocation improves as construction managers gain access to accurate utilization data across the entire equipment inventory.
With better operational workflows, your teams can focus on building—not hunting for equipment. This directly boosts productivity and helps projects stay on schedule.
See MaintainX in action