Lean Six Sigma Definition
Lean Six Sigma is a holistic approach to industrial management focused on improving performance by eliminating “process waste.” Common examples of operational and maintenance (O&M) waste include extra-processing, inventory mismanagement, transportation mismanagement, non-utilized talent, overproduction, and equipment downtime. Lean Six Sigma is a team-oriented approach that maximizes efficiency and improves business profitability. It’s based on the tools and methods of Sigma Six and the philosophy of lean manufacturing.
Lean Six Sigma Approach
The Lean Six Sigma approach helps operational managers optimize talent, resources, effort, and time. The O&M framework combines the tools and methods of the popular Sigma Six approach with Lean manufacturing philosophy. This results in the prioritization of three key elements:
- Tools and Techniques: Organizations rely on a set of tools and analytical techniques to identify and solve problems.
- Process and Methodology: Using problem-solving tools, root causes of problems are identified through a series of phases, and then solutions are fully implemented.
- Mindset and Culture: Teams rely on data and processes to achieve operational performance goals while ensuring continuous improvement.
The three Lean Six Sigma elements reinforce one another, cutting unnecessary O&M costs. Without a mindset of continuous improvement, the first two elements are ineffective.
Processes also only produce results if tools and techniques are implemented, and the organization has a culture of a data-based problem-solving approach. Lastly, an improvement mindset is only useful when there are analysis tools, techniques, and processes in place to achieve the desired results. Lean Six Sigma takes an approach to business improvement that includes all three elements.
What is Lean Manufacturing?
Lean manufacturing focuses on waste elimination. The concept was originally developed as part of the Toyota Production System, founded on Walter Shewhart and Edward Deming’s management principles of process control and continuous improvement. The principles focused on Quality Assurance and Quality Control are widely used in many organizations today.
Lean manufacturing is premised on five principles:
- Value: Organizations define their value based on customer needs. The value of products and services doesn’t depend on business needs and goals.
- Value Stream: Value stream refers to the activities and processes of product development and delivery to the customer. This principle argues that processes should be considered as connected instead of in isolation.
- Flow: A smooth and uninterrupted flow of activities adds value for customers. Waste and inefficiencies that impede the flow should be eliminated.
- Pull: Value streams only process products that are in demand. Organizations shouldn’t create products and hope there will be demand.
- Perfection: Organizations should continually assess their value stream’s performance to improve the value they deliver to customers. They shouldn’t resist changes that improve value creation and delivery.
According to Lean philosophy, organizations should strive to eliminate three types of waste.
- Muda: This refers to processes that are a complete waste of time, resources, and finances. The seven primary types of muda include transport, inventory, motion, waiting, overproduction, over-processing, and defects.
- Mura: Mura is the unpredictable variations of waste that cause unevenness in the production flow. Mura often force organizations to find resources elsewhere in the system to compensate for the unevenness.
- Muri: This refers to overburdening employees and processes so that normal workloads cannot be performed. Examples of mura failures include lack of training, unclear standard operating procedures, and inadequate tools on hand.
Furthermore, the principles of Lean Manufacturing can be applied to any business process and function across all industries.
What Is Six Sigma?
Interestingly, Motorola developed Six Sigma in the 1980s. The approach focuses on eliminating errors that cause process variations. It enables organizations to predict the results of a process with precision. Six Sigma is organized into five phases that ensure processes address the root cause of a problem:
- Define: The organization analyzes and sets the boundaries for a process. The process’s expectations are informed by value creation for the customer to ensure that the process enhances customer experience.
- Measure: The performance of a process or product is measured to determine whether the customers are getting any value. This phase seeks to ensure that solutions are based on actual performance.
- Analyze: In this phase, the organization performs a data-based analysis of the process or products to determine the root cause of production upsets.
- Improve: The organization assesses, designs, and tests possible changes to a process or product to achieve the desired results. Variations that cause problems are either eliminated or reduced.
- Control: In this phase, the organization implements the approved changes. The organization also updates the supporting systems and puts the process or product under control. This ensures that the solution is fully implemented and declining performance can be identified.
Six Sigma relies heavily on data and can be applied to any business process or product as long as it has measurable characteristics and definable goals.
Principles of Lean Six Sigma
Several principles enhance the effectiveness of Lean Six Sigma. They include:
- Address Real-World Problems: Lean Six Sigma takes a top-down and bottom-up approach to problem-solving. The organization focuses on problems that impact both business processes and customer experience. An analysis of a problem determines the root cause of a problem instead of letting the management dictate the problem and its solution.
- Uses a Cross-Functional Team to Perform Analysis: The organization involves a cross-functional team to analyze the different aspects of the process or product under scrutiny. This helps to ensure that all the steps are improved, and none is neglected.
- Focus Analysis on the Process: Lean Six Sigma is best applied to processes of achieving production objectives. The analysis looks to improve actions that are always informed by processes.
- Adopt a Data-Driven Analysis: The analysis must be based on data collected during the Measure phase. The data is used to determine the actual state of the process being analyzed. After developing a solution, the team still needs to collect data to measure its effectiveness.
- Understand the Impact of the Process: The process determines the amount of variation that occurs. Processes or products that have the same attributes won’t have any variations. Variations lead to defects and impact the customer experience.
- Create Solutions That Address the Root Cause: Lean Six Sigma identifies and addresses the root cause of a problem instead of dealing with the symptoms.
- Control System to Make the Solution Sustainable: Organizations are naturally resistant to change. Lean Six Sigma emphasizes implementing a solution and sticking to it. The support systems should be updated to reflect the changes, and staff needs to be trained on the new processes. The solution should be monitored to help determine its sustainability.
Benefits of Lean Six Sigma
Organizations benefit greatly from implementing Lean Six Sigma principles for their operations. It adopts a continuous improvement approach to business processes. Some of the benefits include:
- Simplifies Business Processes: Lean Six Sigma simplifies all business processes by eliminating wastages and inefficiencies. It, therefore, makes business processes move much faster.
- Reduces Mistakes and Errors: Lean Six Sigma starts by defining the acceptable quality for customer value. It prioritizes continuous improvement and, with time, results in fewer errors and mistakes. It also looks to address the root cause of a problem instead of just treating the symptoms.
- Predicts Performance: The approach minimizes variations in a process. This makes the cycle time, quality of output, and costs more predictable. In the long run, it improves the business's bottom line and customer satisfaction.
- Provides Active Control: With improvements to processes, it becomes easier for the organization to be in control and on top of things. People will start taking ownership of processes instead of feeling like they are victims of the process.
Lean Six Sigma also improves employee morale and effectiveness. By taking charge of projects, they develop leadership qualities and have better promotion and higher pay prospects.
Similarities between Lean Manufacturing and Six Sigma
The principles of Lean Manufacturing and Six Sigma are usually combined because they complement each other. They both provide analysis that can be performed on a process or product simultaneously. Both base their definitions of value on the customer experience and map out the process flow in a way that understands the process.
Other similarities between the two principles include reliance on data, emphasis on continual improvement, and extensive use across different industries. Both Lean Manufacturing and Six Sigma can be applied across several business processes, functions, and products. On the other hand, their differences provide analytical tools and solution options to improve business processes and products.
Using MaintainX to help run your Lean Six Sigma makes it easier for continuous improvement, better document control, and sustained lean management. If that sounds interesting, try MaintainX today. Our goal is to make work smarter, not harder.
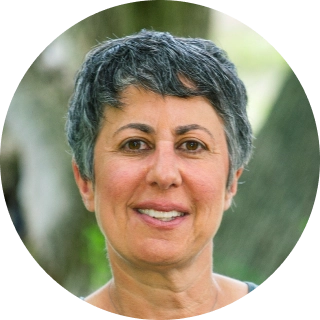
Caroline Eisner
Caroline Eisner is a writer and editor with experience across the profit and nonprofit sectors, government, education, and financial organizations. She has held leadership positions in K16 institutions and has led large-scale digital projects, interactive websites, and a business writing consultancy.
See MaintainX in action