Kamishibai boards are a visual audit management tool used by companies that have adopted a Lean manufacturing approach.
Using highly visual, color-coded “pass or fail” flags on a wall-mounted board, the entire production team can see at a glance whether a procedure has been completed successfully or whether it has failed a quality audit and needs further attention.
The Kamishibai system provides a simple way to look after the daily management of quality control throughout your facility, encouraging everyone involved to do their part to ensure each process runs smoothly.
The Ancient Origins of Kamishibai
Those familiar with the Toyota Production System and other Lean Six Sigma approaches, like Kaizen, might assume that the Kamishibai process was developed alongside other Lean concepts in the mid-twentieth century. However, its origins go as far back as 12th-century Japan. Gemba Academy explains that Buddhist monks originally used kamishibai–literally “paper theater”–to create visual stories for citizens who could not read.
A visual management tool, Kamishibai is still common both in Japanese culture and elsewhere worldwide, offering a way to pose moral problems and stories through simple actors in a paper drama.
So how does this relate to running a Lean workplace?
Just like the poka-yoke approach, which aims to reduce mistakes by simplifying complex actions and ideas, Kamishibai offers a way to simplify your auditing and quality processes without losing any impact or urgency required to keep your organization running smoothly.
Using visual cues, this system simplifies communicating the status of your business’s auditing procedures. It ensures problems or errors are caught early.
Kamishibai as Part of Total Productive Maintenance
These days, managers and quality professionals use Kamishibai boards as auditing and process confirmation tool. They also use them to oversee total productive maintenance (TPM).
TPM covers all the elements of the business, from employees to safety to equipment. The strategy ensures that each system within the organization’s ecosystem runs efficiently and effectively. In addition, TPM aims to remove roadblocks to ensure each sector of your operation can carry out its assigned processes without unnecessary waste, downtime, or accidents.
However, once a TPM system is in place, it’s not hands-off. Quality personnel need to continue checking, auditing, and reviewing each moving part in the production machine is where the Kamishibai board comes into its own.
Once started, Kamishibai can work as an autonomous system. The person responsible for each process has the power to improve processes. Likewise, the system can prevent issues before they happen. For example, a manager might create preventive maintenance workflows instead of a reactive maintenance plan that results in unsafe and unplanned downtime.
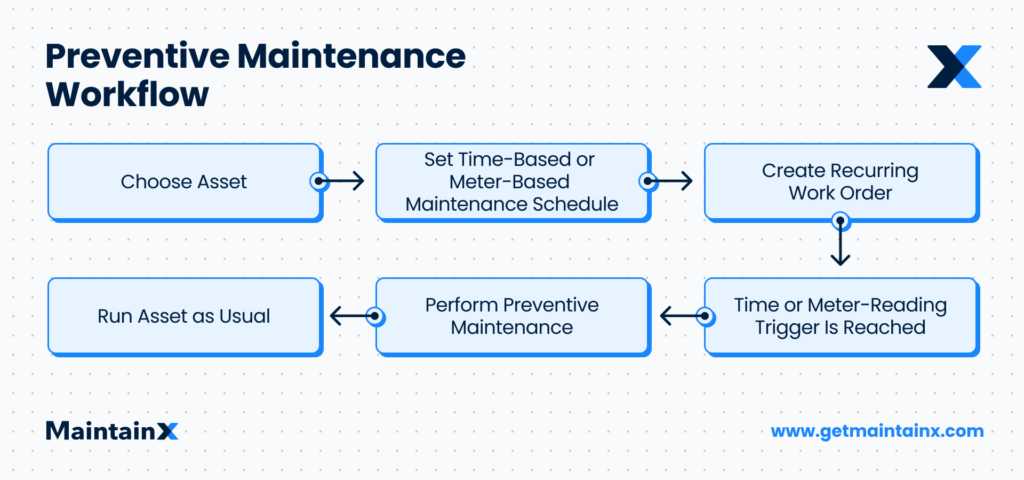
Getting this kind of intricate, autonomous system up and running is no small feat, but the payoff is a self-sustaining production system.
Using this easy-to-manage audit system, management can display Kamishibai cards on the wall of your facility. The display offers simple visual control of how maintenance is running.
Let’s look at how to set up and use a Kamishibai board.
How to Create a Kamishibai Board
Decide Where to Put Your Board
Kamishibai boards are most effective when they are wall-mounted right near the work area: at the entry to a production area or somewhere easily visible to anyone in the zone being audited. A whiteboard, pinboard, or a purpose-designed system to hold Kamishibai cards will all work well.
Delineate Types of Audits and Their Frequency
Whichever system you choose, you’ll need to break your board into sections for each audit process or department. For example, you could add columns for safety, quality, and overall cleanliness of your facility.
Note the main audit categories you use when you inspect each process. A daily Gemba walk might fall into a cleanliness column, while a weekly quality control audit might be another.
Leadership can use Kamishibai to conduct weekly, monthly, or quarterly audits effectively. You can arrange your board to display these periodic checks.
Create Your Card System
Kamishibai cards are simply double-sided cards that indicate a successful pass on one side (often color-coded green). The other side represents a fail on the other (typically red). A popular way of maintaining a Kamishibai board is to use T-cards–simple index-style cards that fit into purpose-built slots. Another is simply using a hanging card (similar to an open/closed sign that you would see in a shop window).
The core purpose of a Kamishibai is to train staff to immediately recognize deviations from the standard output and take corrective action in real time. This is why color coding is so effective. Once failures are obvious and visible to everyone involved in the production process, staff can conduct self-audits to correct any errors.
Is Kamishibai Different from Kanban?
At times, there is an overlap between various lean tools and methodologies. Kamishibai and Kanban boards are both parts of a lean management system. But, while they look similar, they serve entirely different purposes.
A Kamishibai is most effective for audit processes, standard procedures, and operating methods. On the other hand, a Kanban system effectively tracks process flow. For example, managers can track motor assemblies across a factory floor or parts consumed for routine maintenance.
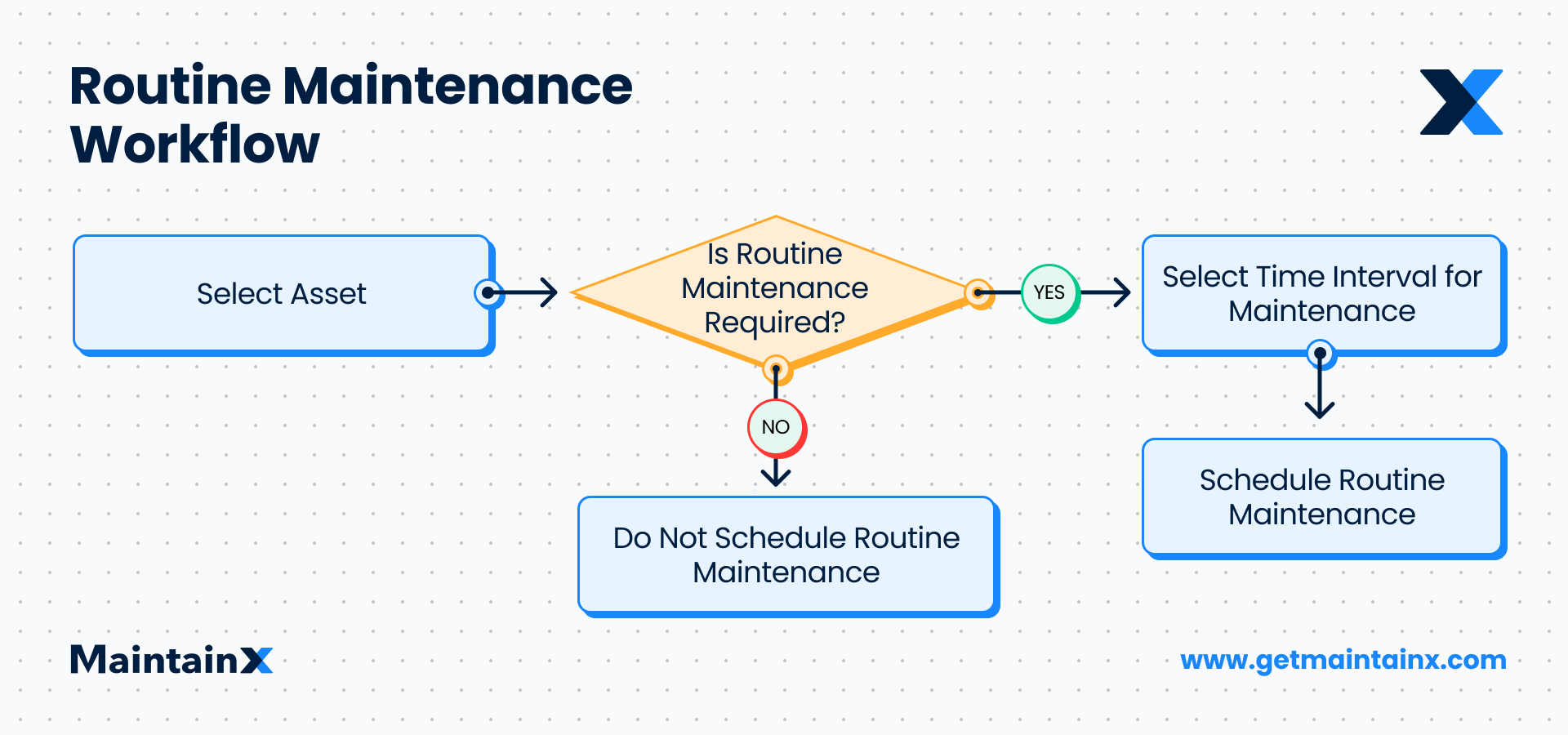
Both use graphic cards as cues. However, the purpose of a Kamishibai is to monitor cyclical processes and systems. A Kanban, on the other hand, monitors linear progress through a pipeline.
Audit the Effectiveness of Your SOPs and Checklists
The purpose of a Kamishibai is not to audit the person responsible for the process. It’s to figure out why the process is not working as planned. For this approach to continuous improvement to succeed, your entire team needs to be on board. Everyone, admin and technicians, needs to strive for operational excellence.
A manufacturing process regularly failing an audit shouldn’t be a reflection of the person responsible. Instead, quality control managers should review standard operating procedures to pinpoint weak points in the process as they work through each audit cycle.
Of course, to audit anything effectively, you need a documented standard work procedure to use as a benchmark. This is where maintenance management software like MaintainX provides real value.
You can create SOP templates for everything from preventative maintenance to breakdown maintenance and checklists for daily cleanliness checks. You can build a library of auditing benchmark documents that will form the foundation of your Kamishibai system.
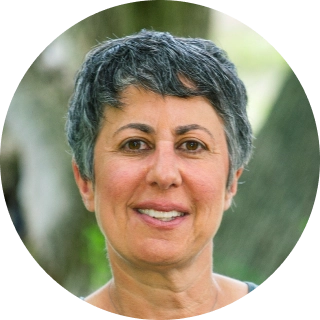
Caroline Eisner
Caroline Eisner is a writer and editor with experience across the profit and nonprofit sectors, government, education, and financial organizations. She has held leadership positions in K16 institutions and has led large-scale digital projects, interactive websites, and a business writing consultancy.
See MaintainX in action