Mean Time to Repair (MTTR) refers to the average time maintenance teams spend diagnosing, fixing, and recovering failed pieces of equipment. MTTR is a baseline that maintenance departments use to improve asset efficiency, minimize unplanned downtimes, boost bottom lines, and assess equipment value.
Mean Time to Repair (MTTR) provides a useful productivity benchmark for organizations seeking to reduce prolonged repair times and their associated expenses.
MTTR Analysis
Conducting an MTTR analysis allows organizations to evaluate the quality and effectiveness of their maintenance strategies, processes, and practices. For many industries, organizational effectiveness is dependent on asset reliability. Critical equipment breakdowns often translate to extended repair times, technician overtime, outsourced contractor fees, and lost production schedules.
Maintenance experts recommend striving for an ideal MTTR below 5 hours. However, the metric can vary substantially based on asset type and importance, for example. Savvy department leaders routinely monitor MTTR for both individual pieces of equipment and the organization as a whole.
The metric provides insights into maintenance scheduling, replacement parts purchases, and maintenance task completion. Ultimately, delving deeper into “the whys” behind extensive MTTR metrics helps maintenance teams increase uptime, enhance efficiency, and decrease unnecessary costs.
How to Conduct MTTR Analysis
MTTR includes the time taken to:
- Notify maintenance technicians of a failure
- Diagnose the cause of the failure
- Fix the problem at hand
- Wait for overheated equipment to cool down
- Reassemble, align, and calibrate equipment
- Set up, test, and restart equipment for average production targets
It’s worth mentioning that hunting down replacement parts can significantly impact MTTR. Lack of inventory optimization leads to out-of-stock parts, expedited shipping costs, and serious maintenance delays.

How Is MTTR Used?
MTTR is a powerful tool for predicting the impact of equipment failure on an organization’s bottom line. The higher the MTTR, the costlier the downtime. Applications of MTTR include:
- Maintenance Decision-Making: MTTR can help leaders make decisions about whether to repair or replace aging assets. Consider that up to 40 percent of unplanned downtime is due to aging equipment. MTTR indicates how long it takes to repair an asset as it ages. In such cases, it can be more economical to replace an asset than to fix it. Furthermore, MTTR can predict the lifecycle costs of a new system to inform its purchasing and design process.
- Preventive Maintenance Scheduling: Tracking MTTR helps organizations ensure that their preventive maintenance (PM) programs and activities are efficient and effective. MTTR primarily measures reactive maintenance, but it can help determine how to schedule maintenance activities to minimize unplanned breakdowns. For example, longer MTTR may mean that PM activities aren’t standardized and optimized for maximum efficiency.
- Maintenance Planning and Inventory Purchasing: Disorganized inventory management of replacement parts can significantly impact asset maintenance. It leads to delayed completion of maintenance activities. According to Chemical Processing, about 50 percent of unplanned downtimes are caused by a lack of replacement parts. Additionally, organizations spend up to 25 percent of maintenance time sourcing replacement parts. Ensuring that replacement parts aren’t defective, understocked, or mislabeled can reduce MTTR. Forecasting maintenance needs allows organizations to stock necessary replacement parts for upcoming activities, including reactive maintenance.
While machine failure is inevitable, MTTR helps organizations quickly and efficiently respond to equipment breakdowns. This strategic key performance indicator can help minimize disruption to production, revenue loss, and customer dissatisfaction by establishing a baseline for improvement.
How to Calculate MTTR
Mean Time to Repair (MTTR) is calculated by tracking the total amount of time an asset undergoes recovery after downtime, then dividing by the number of times the asset in question has failed within a given time.
MTTR Formula:
MTTR = Total Maintenance TIme ÷ # of Repairs
For example, if an organization spends 50 hours total on unplanned maintenance for an asset that broke down eight times in one year, the asset’s MTTR is 6.25 hours. The calculation would be:
50 hours ÷ 8 = 6.25
Notably, MTTR doesn’t depend on an asset’s uptime. It only factors in how long each unplanned stoppage lasts. The MTTR formula assumes all maintenance tasks are performed sequentially and by well-trained maintenance personnel.
How to Improve MTTR
The first step to improving MTTR is to understand the four stages of MTTR: problem identification, diagnosis, repair, and verification that the asset is operational again. The primary goal is to reduce the time spent in each stage. Of course, preventive maintenance is crucial to reducing significant equipment breakdowns. However, asset data collection, analysis, and problem solving ultimately reduce MTTR.
The most important ways to reduce MTTR include:
- Anticipating breakdowns and organizing resources needed for corrective maintenance
- Providing maintenance personnel and third-party contractors with detailed standard operating procedures to avoid miscommunication while performing tasks
- Ensuring that maintenance personnel are adequately trained and equipped with the necessary skill sets
- Leveraging technology, such as computerized maintenance management systems (CMMS), to streamline maintenance activities
- Implementing well-managed spare parts and tools inventory system
Calculate MTTR with a CMMS
MTTR is one of several metrics that operational managers use to track time spent on equipment failure and repairs. Lower MTTR translates to less downtime, reduced maintenance costs, stable production, and improved customer satisfaction. A Computerized Maintenance Management System (CMMS) platform is the easiest way to collect, store, and analyze MTTR.
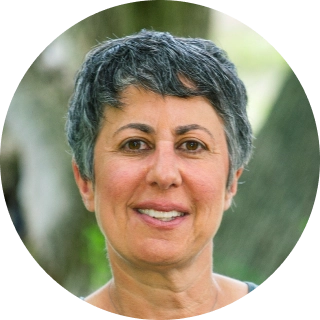
Caroline Eisner
Caroline Eisner is a writer and editor with experience across the profit and nonprofit sectors, government, education, and financial organizations. She has held leadership positions in K16 institutions and has led large-scale digital projects, interactive websites, and a business writing consultancy.
See MaintainX in action