A calibration management software solution is a critical component in a modern manufacturer’s toolkit. The reason? Equipment in an out-of-tolerance condition can produce defective products, leading to non-compliance.
Calibration management software helps reduce the risk of non-compliance. CMS helps you effectively create and monitor calibration management schedules. This post explains why calibration and calibration management software (CMS) is essential for quality management and certification.
Calibration: What It Is and Why It’s Important
Calibration is the process of checking equipment’s accuracy against a benchmark. The values measured during calibration are compared to the OWM Laboratory Metrology Program’s standard. If the measured value isn’t within the expected test limit, it’s called out of tolerance.
Failure to recalibrate can result in recalls and legal penalties. For example, Toyota’s $2 billion global safety recall affected the company’s earnings and reputation.
Inspecting and calibrating equipment regularly is critical and requires careful planning. You need a strategy where you create a schedule, manage calibration tasks. and track equipment maintenance activity.
What Is Calibration Management Software?
Companies use calibration management systems to schedule equipment calibration and maintenance tasks as needed.
Equipment managers and technicians exchange and manage a substantial amount of calibration data. Manually logging data can quickly become overwhelming for everyone involved in the process. This is where a CMS can be a great resource.
However, a computerized maintenance management system (CMMS) offers even more functionality. For example, a CMMS helps you schedule comprehensive preventive maintenance (PM) and precision maintenance programs that can include calibration tasks.
Along with calibration-related tasks, a robust CMMS offers features for all maintenance-related tasks, including cloud-based notifications, traceability, and equipment maintenance logging.
Why You Need Digital Calibration Management Software
Calibration is required to ensure compliance and customer satisfaction. We know that creating calibration schedules, tracking calibration procedures, and storing calibration records manually can be a hassle. And that’s why you need a digital tool for calibration management. Here are more reasons to use a digital tool for calibration management:
Ensures Compliance
Both the International Organization for Standardization (ISO) and U.S. Food and Drugs Administration (FDA) require manufacturers to comply with various standards. For example, ISO 17025 ensures laboratories operate competently and generate valid results. This requires due diligence regarding regular equipment calibration.
Other standards requiring compliance include:
ISO 9001 is a set of five quality management systems standards. It ensures organizations meet customer and other stakeholder needs within statutory and regulatory requirements related to a product or service.
21 CFR Part 11 of Title 21 of the Code of Federal Regulations. It establishes the United States Food and Drug Administration regulations on electronic records and electronic signatures.
A CMMS helps execute a calibration schedule consistently. The CMMS automatically creates a calibration history, so you always have the information needed during an audit. You can also track calibration activity and store calibration certificates.
Streamlines Calibration
A CMMS can help automate tasks and streamline the calibration workflow. You can complete all collaboration procedures on schedule without overwhelming your team. For example, you can set up a schedule in the CMMS that automatically notifies the appropriate technician to test calibration.
CMMS like MaintainX use barcodes (and QR codes) to track parts and equipment. Using such tracking makes calibration workflows even more efficient. Not to mention that the attached barcodes help streamline your asset management.
You can start small with your calibration tracking. Then, set up a scalable compliance management system for calibration validation as you integrate the CMMS and your company grows.
As technicians complete calibration, they can use the CMMS on their mobile phones to check the tasks, creating real-time calibration logs for inspections. Likewise, you can monitor the progress of calibration tasks from the CMMS. This way, everyone involved can track the tasks from a single dashboard.
Reduces Costs
A CMMS helps reduce costs in multiple ways. For example, it saves your team time because all the information is in a single app. The calibration software solution also automatically logs the data generated during the process.
Using a CMMS also eliminates expensive errors that manual processes are prone to. Now, with all the data on the CMMS, you can make real-time, data-driven decisions to control other cost drivers.
Why You Shouldn’t Overlook Calibration
It’s impossible to meet the accuracy and ISO-quality requirements without adequately calibrated equipment. “Nearly there” isn’t a great approach to calibration—precision is vital. Here are more reasons not to overlook calibration:
Cost Overruns
The higher the number of rejected parts, the more you’ll need to spend reprocessing them. So, in addition to the direct costs of reprocessing, you’ll incur the opportunity cost of not producing new units.
Reduced Productivity
Your teams will need to spend time bringing the defective parts back into production, which can mess with the production schedule. Defective production is bad news if you’re trying to achieve production efficiency or build a reputation for high-quality standards.
Damage to Reputation
This is the most expensive consequence of defective production resulting from improper calibration. As noted in HBR:
“In an economy where . . . market value comes from hard-to-assess intangible assets such as brand equity, intellectual capital, and goodwill, organizations are especially vulnerable to anything that damages their reputations.”
MaintainX: Your Best Bet for Calibration Management
MaintainX is a web-based CMMS with everything you need for calibration management and asset maintenance all in one app. For example, you can create a checklist for emergency calibration or a scheduled work order for regular calibration.
You can upload pictures for added context. Or, if your team has questions, it can use the built-in chat option (only available in MaintainX) to get questions answered faster. MaintainX comes with built-in checklists creating calibration records such as:
If you’re trying to create and implement a calibration management schedule, give MaintainX a try today!
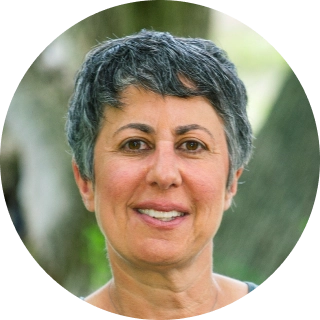
Caroline Eisner
Caroline Eisner is a writer and editor with experience across the profit and nonprofit sectors, government, education, and financial organizations. She has held leadership positions in K16 institutions and has led large-scale digital projects, interactive websites, and a business writing consultancy.
See MaintainX in action