Maintenance work order software helps you and your team manage, organize, schedule, and review all the tasks that flow through your organization.
Developed primarily for maintenance teams in the manufacturing and facilities management sectors, cloud-based work order software helps your business keep track of essential data on expenses, parts, and labor.
What are the Advantages of Using Work Order Management Software?
Work order management software is also called CMMS software (Computerized Maintenance Management System). It’s a brilliant tool that can help automate and streamline workflows across your organization.
- Maintenance managers and supervisors can easily assign tasks to maintenance personnel and see real-time data, including job status.
- Maintenance personnel can then easily see what needs to be done and when–and know which tasks are most critical.
- Predictive maintenance schedules can be set up, eliminating repetitive manual scheduling.
- Inventory management functionality helps ensure the necessary spare parts are always allocated to each job.
- A CMMS encourages and amplifies team collaboration, particularly if the work order software has instant messaging functionality.
- Historical reporting allows supervisors to see how resources are used across the organization and identify where improvements can be made.
- Technicians can action work orders and respond to breakdowns faster, reducing equipment downtime.
- Customer experience improves as machine uptime increases, reducing order wait times and speeding up the shipping of goods.
- Maintenance costs can be reduced thanks to better team and resource utilization, improving your bottom line.
Integrating a work order management system into your business can be easy, with many types of free work order software available on the market.
However, finding the best work order software for your business requires a solid understanding of what you want from the program. A good approach is to select people from different departments or teams and trial several work order management systems to see which works best for your company.
How to Choose the Best Work Order Management Software
Is It User-Friendly?
Ease of use should always be at the top of your list. Your team won’t widely accept a work order system that is hard to navigate. Look for work software that is easy for technicians, supervisors, and management teams to operate.
Is It Cross-Platform Compatible?
You need your work order software to function where your employees spend their time. For field service technicians, that means a mobile app that operates reliably in remote areas, whereas, for managers, a desktop work order app is typically most appropriate. Whether the software is on a PC or a mobile device, the critical factor is that it should be intuitive to use.
Does It Have the Features You Need?
The maintenance work order system you choose impacts how different teams do their day-to-day work. Before settling on a particular provider, take some time to make a list of all the features you’d like to manage within your work order program.
Your list could include:
- Automating and prioritizing work requests/maintenance requests
- Preventive maintenance scheduling
- Work order tracking
- Inventory management / spare parts inventory
- Checklists and templates for routine maintenance tasks, safety checks, etc.
- Instant messaging and notifications
- Measuring KPIs and reporting dashboards
- Historical reporting capabilities
- Asset tracking and asset management functionality–if this is your top priority, you may like to explore Enterprise Asset Management software (EAM)
What Support Is Available?
Even work order tracking software that is designed for simplicity has a slight learning curve. Suppose your team has become accustomed to spreadsheets or is entirely new to work order tracking systems.
In this case, they will need some support when you first implement the system across your organization. Look for maintenance management software with a robust onboarding and support program to set you up for success.
Challenges to Choosing the Right Maintenance Work Order Software
Choosing the best maintenance work order software for your organization can come with challenges.
Integration with Existing Systems
The new software might not be fully compatible with the existing systems, leading to integration issues and challenges. Additionally, migrating data from old systems to the new one can be time-consuming and may result in data loss or errors if not handled carefully. Check out how well your new software will integrate with legacy systems and software used by other departments. The work order software you use should not create another information silo.
User Friendliness and Learning Curve
Some work order software solutions have complex user interfaces, leading to a steep learning curve and potential resistance from your maintenance teams. The lack of adequate training resources and materials can intensify the uptake, making it difficult for users to adapt to and efficiently use the new system. The best work order software platforms offer free training and robust support. Don’t settle until you know your technicians will be in good hands. Check out G2 and Capterra for user reviews.
Cost and Budget Constraints
The initial costs of purchasing and implementing work order software can be high, which does not always guarantee a good return on investment. Additionally, organizations need to be mindful of ongoing costs, such as maintenance, updates, and customer support, all of which add to the total cost of ownership. Compare pricing and features, including the cost of training and CMMS ROI, to be sure you will get the best bang for your buck.
Specific Features and Customization Options
The software might not have all the necessary functionalities required for your organization’s unique needs, and limited customization options can constrain how much the software can be tailored to fit specific business processes and workflows. Be sure that the software you choose offers customizable features, such as low-inventory triggers, conditional work order logic, and customizable work order fields and feature labels, to name a few.
It’s crucial to conduct thorough research, engage in trials, seek end-user feedback, and evaluate the total cost of ownership. Ensuring the software is scalable and flexible enough to accommodate future changes and growth is also vital. By taking these steps, organizations can make a more informed decision and select a maintenance work order software that best aligns with their needs and constraints.
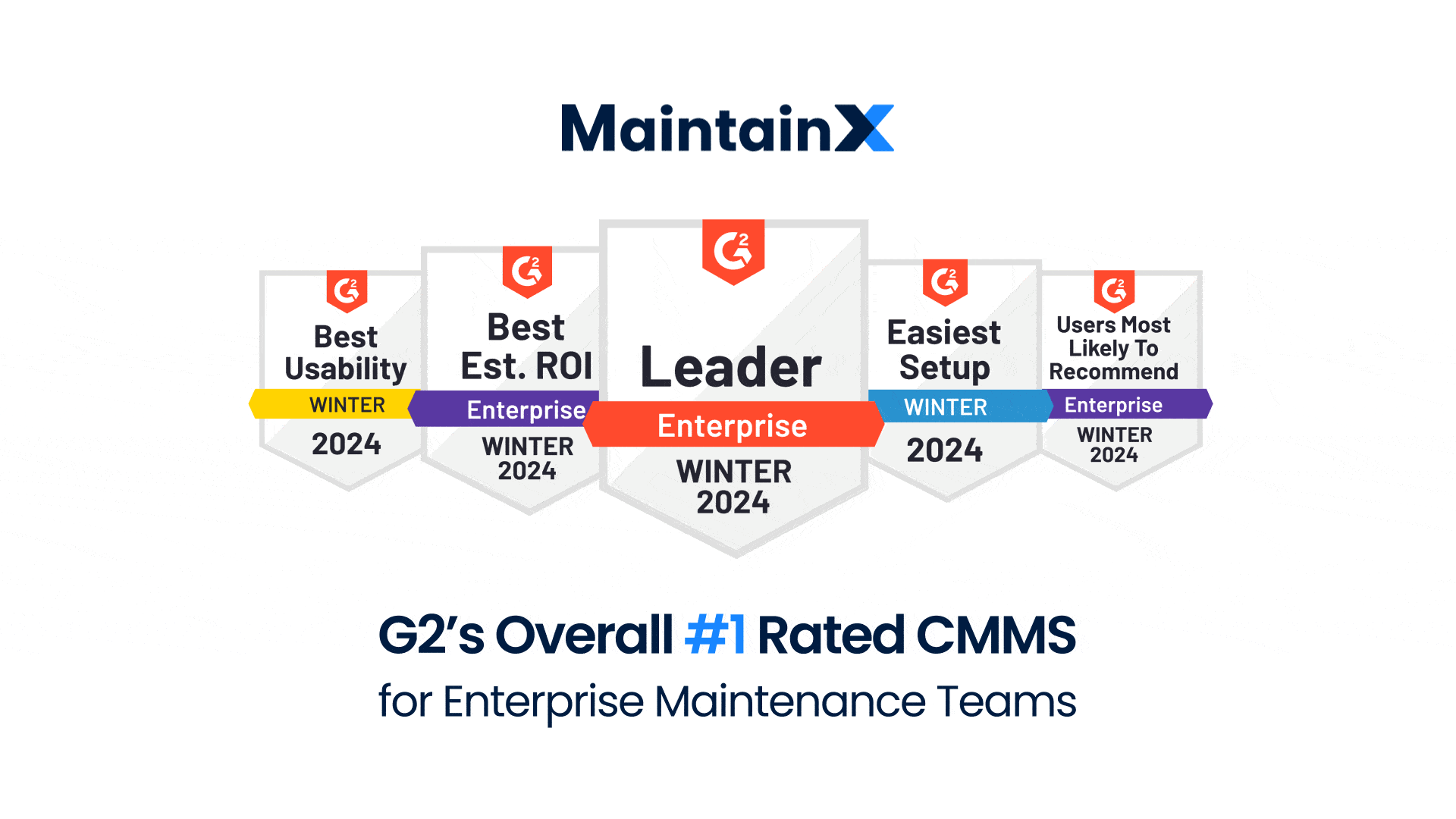
Choosing an Online Work Order System: Next Steps
The choice of work order systems can be overwhelming–but we encourage you to test out several software solutions and read independent reviews to find the best CMMS software for your organization.
With MaintainX, you can deliver better operational efficiency to your maintenance operations. The mobile-first platform offers an excellent collection of common-sense features without unnecessary complexity to slow down your workflows.
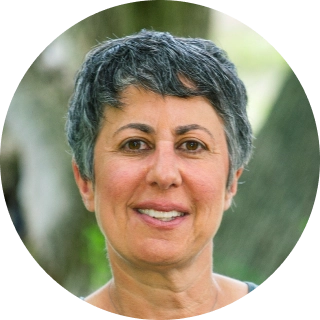
Caroline Eisner
Caroline Eisner is a writer and editor with experience across the profit and nonprofit sectors, government, education, and financial organizations. She has held leadership positions in K16 institutions and has led large-scale digital projects, interactive websites, and a business writing consultancy.
See MaintainX in action