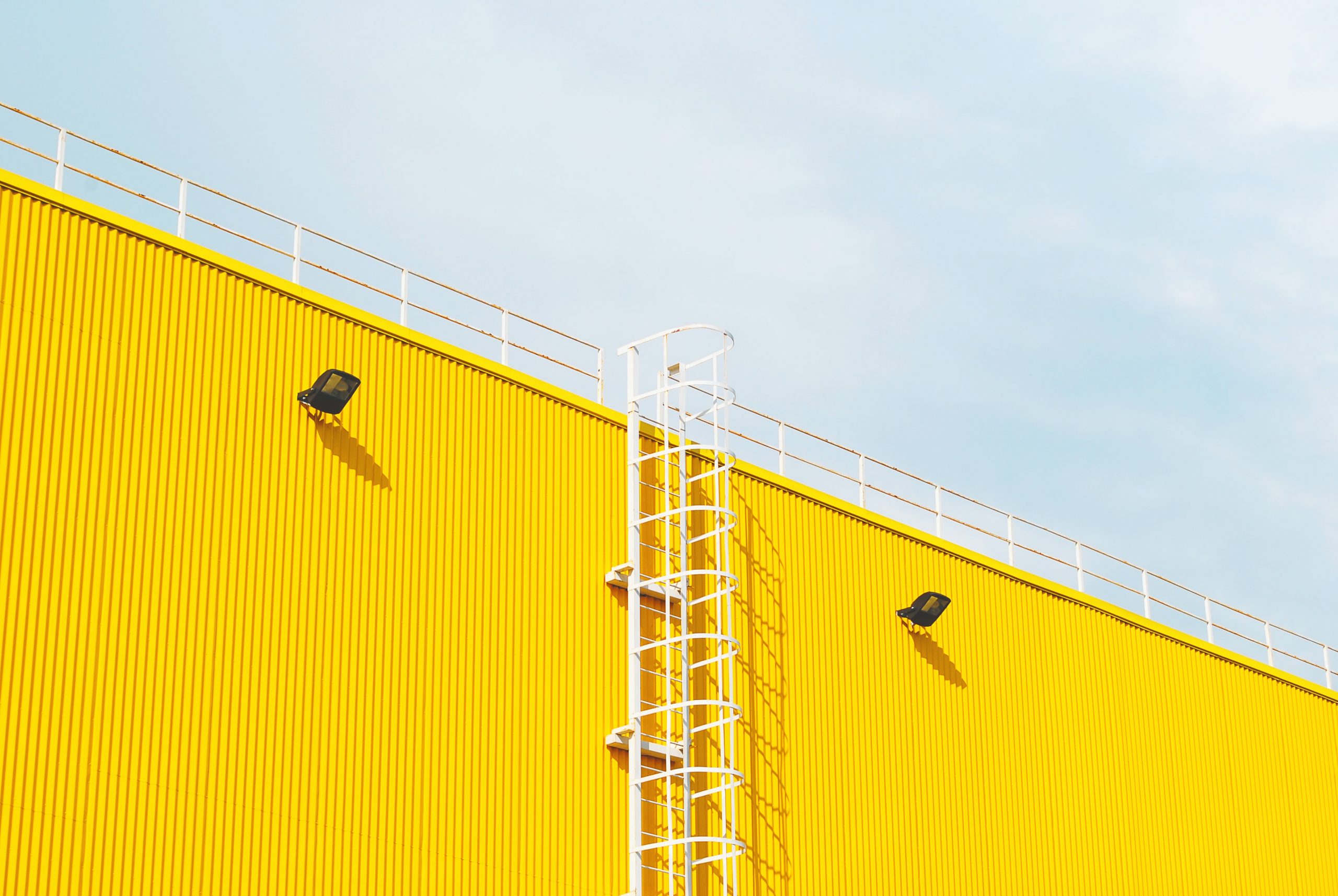
Deadlines are important within every industry.
Journalists publish newsworthy articles, construction workers complete project milestones, and educators develop lesson plans—all according to daily timelines.
Missed deadlines cause chain reactions that affect others. And nowhere is that impact felt more strongly than in manufacturing facilities. As recently demonstrated, everyone depends on manufacturers to sustain global supply chains with food products, vital equipment, and other important items.
However, both personal and corporate expectations of manufacturers have recently increased due to speedy delivery services like Amazon Prime. According to the 2020 MHI Annual Industry Report, four of the six most commonly cited manufacturing challenges relate to delivery requirements.
Nearly half of the 1,000 manufacturing and supply chain professionals surveyed listed “customer demands on response times”, and “rising customer service expectations” as significant concerns for the year ahead.
Poor On-Time Delivery (OTD) performance can happen for a variety of reasons, including material shortages, poor material handling procedures, and inefficient production methods. Some of those factors are within your control, while others are not. In this article, we’ll focus on something you can do to increase OTD, and that is organizing an effective manufacturing preventive maintenance (PM) program.
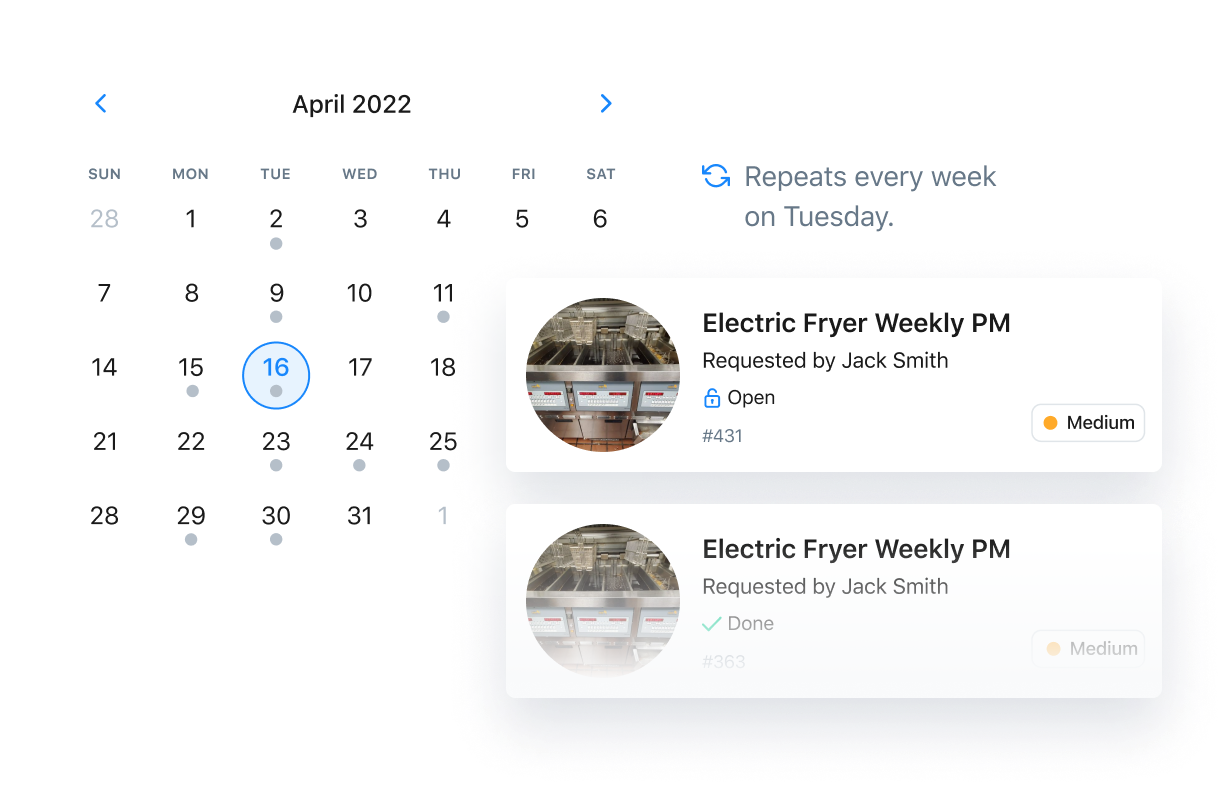
7 Manufacturing Preventive Maintenance Tips for Facility Operational Managers
Performing routine maintenance on manufacturing equipment may sound like a lofty goal in the midst of competing priorities. However, studies show that effective preventive maintenance programs can save companies money by reducing downtime. Predictive maintenance systems (that track machine historical data) can save even more.
Considering that 10 percent of industrial equipment ever completely wears out, and downtime costs some facilities as much as $22K a minute, practicing strategic preventive maintenance is wise. Increase your overall equipment effectiveness with planned maintenance.
Most facility and maintenance directors already understand the value of preventive maintenance. Many of them even invest in Computerized Maintenance Management Systems (CMMS) to digitize, assign, and organize work orders. The larger the manufacturing facility, the more difficult using paper clipboards becomes. Unfortunately, choosing the right CMMS platform can be tricky. According to Reliable Plant, a whopping 80 percent of managers fail to use purchased CMMS solutions.
We believe this happens for a simple reason: The software is too complicated.
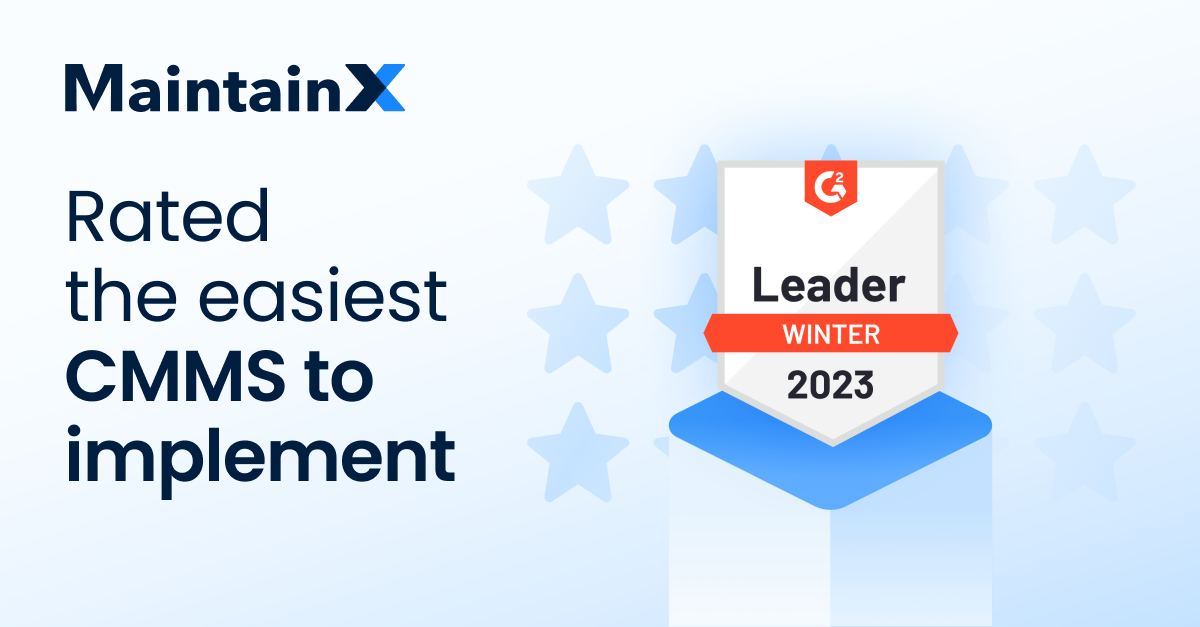
1. Choose a user-friendly CMMS
Put simply, you shouldn’t need a Ph.D. to understand how to use a piece of software that promises to make life easier. Everyone on your maintenance team should have no problem figuring out how to create work orders, how to complete them, and how to track assets. Manufacturing preventive maintenance programs depend on the consistent use of CMMS platforms.
As mentioned by Jeff Owens, CEO of Advanced Technology Services and Plant Engineering Maintenance Survey partner:
“It’s clear, from my perspective and the majority of survey respondents, that the number one barrier to improved maintenance is the lack of staff resources, which lends itself to the need for experienced talent and technology providers.”
Fortunately, new SaaS providers have entered the CMMS market, making the software more user-friendly than ever before. MaintainX offers a freemium maintenance management app that is comprehensive, elegant, and robust: Maintenance workers can learn how to access work order assignments, upload equipment photographs, chat with managers, and complete work orders in just a few minutes. The best part? They can do it from their smartphones.
Managers will also appreciate how MaintainX makes it easier to create repeatable work orders, cut equipment purchases, reduce equipment failure, streamline safety inspections, and ensure compliance with digital audit trails.
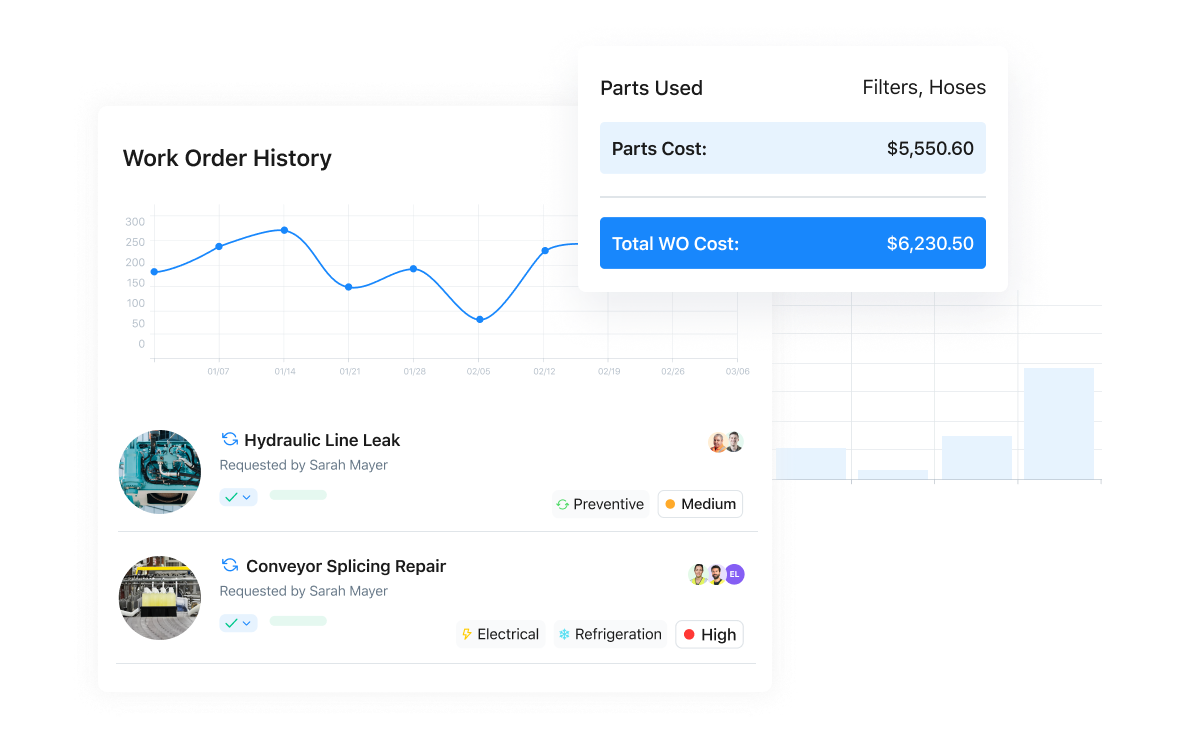
2. Track costs for savings opportunities
Want to know a secret? Making preventive maintenance schedules based on your own equipment, vendor, and worker data is what really drives cost savings.
The best CMMS solutions cross-reference work order components by the assigned technician, asset type, priority status, time to complete, and several other categories. These pieces of information are then combined to create powerful reports that illustrate previously unseen savings opportunities.
A user-friendly CMMS will make data collection a breeze so that maintenance doesn’t feel burdened with cumbersome data entry steps. The more equipment data you have, the less likely your facility will experience downtime, and the faster it will meet customer deadlines.
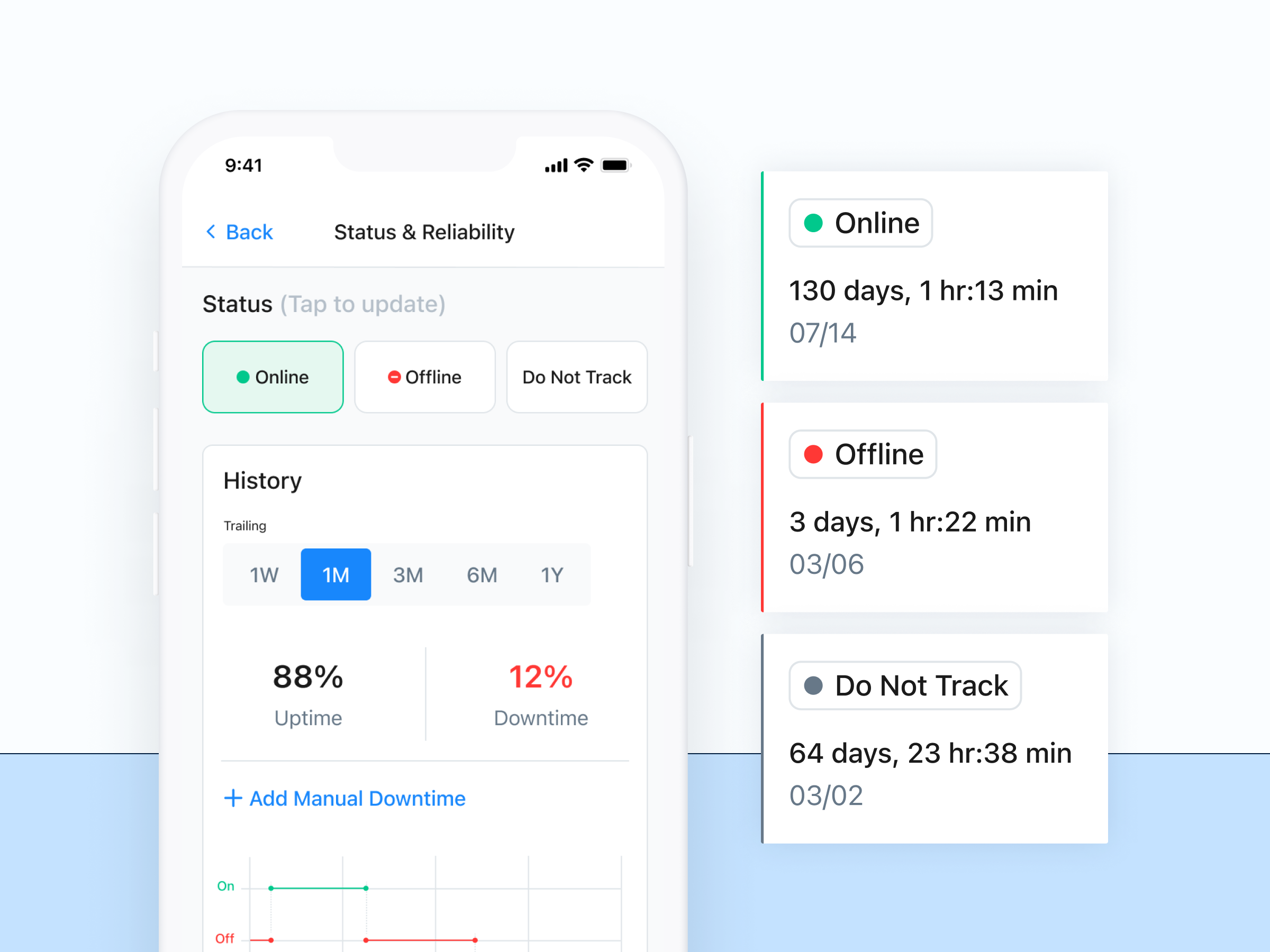
3. Enhance team communication
One overlooked way to increase OTD is to strengthen communication between maintenance technicians and operators. How many times have your team members missed an important deadline or lost downtime because of a minor miscommunication?
While nothing beats face-to-face conversations, the enormous size of many manufacturing facilities means that it isn’t always convenient. Conversations are often limited to walkie-talkies, email, and text messages–if they happen at all. However, these methods aren’t helpful when trying to organize complex instructions regarding separate projects. The most efficient way to effectively communicate is via business messaging platforms.
Software companies like Slack, Lua, and HipChat all provide smartphone apps that allow companies to organize communication threads by department, project, and task. The MaintainX platform takes things a step further. Our CMMS allows manufacturing team members to upload PDFs, take equipment photos, and chat directly within the comments section of digital work orders.
Receive some last-minute instructions regarding some parts to be ordered? Just update the information within the work order and ping the assigned technician with a comment. Containing important discussions within respective work order categories helps manufacturing teams decrease the likelihood of equipment setbacks, downtime, and shipment delays.
4. Negotiate preventive maintenance arrangements with equipment providers
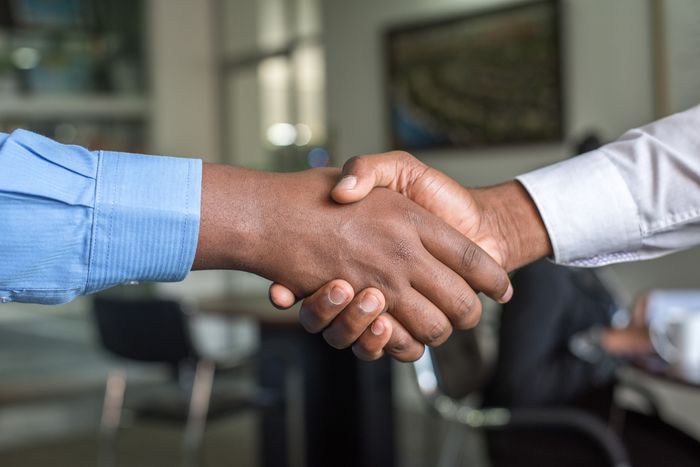
Many machinery manufacturers offer preventive maintenance service visits for flat annual rates or discounted labor costs. If an equipment provider doesn’t offer such agreements, make sure you receive recommended PM instructions for your team to work with.
Not only do service contracts ensure necessary PM gets performed, but they also help managers improve their cases for annual budgets. While you should strive to complete most maintenance in-house, partnering with an experienced equipment service provider on important assets can be beneficial.
5. Shadow equipment providers
Anytime an outside technician visits, consider assigning an in-house technician to shadow his work. This is a great time for maintenance team members to observe complex maintenance tasks up close, ask questions, and take notes. The shadowing worker should also request a copy of the inspection report so that parts are checked, and the date of service can be recorded in your CMMS calendar and on your Asset history.
The next time that specific machine is due for preventive maintenance, your in-house technician might feel confident enough to accomplish the task. Taking advantage of every training opportunity is key to establishing an effective manufacturing preventive maintenance program.
6. Stock frequently replaced parts
Next, consider asking outsourced providers for spare parts lists. Your equipment’s most frequently needed parts can often be purchased at a cheaper price. While you shouldn’t feel obligated to buy every part, stocking the most commonly replaced parts can reduce potential downtime and save money in the long run.
7. Plan PM around seasonal variables
Finally, schedule preventive maintenance tasks that require downtime during slower seasons. Comprehensive PM for larger assets requires an average of four to eight hours for completion. Get ready for a marathon maintenance session! However, these preventive measures can help your team avoid days' worth of reactive maintenance when an important machine breaks and causes costly downtime.
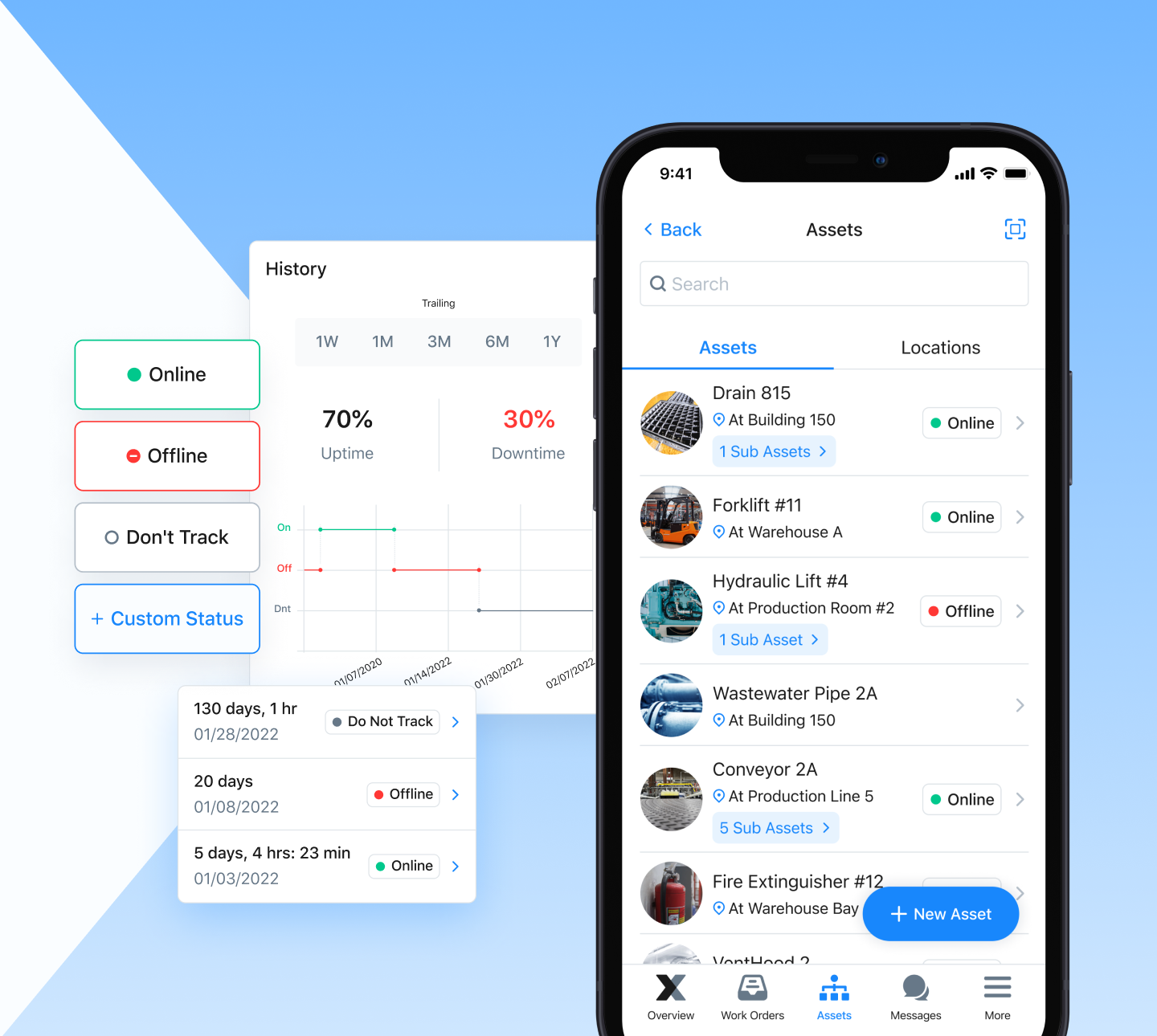
Simplify Maintenance with MaintainX
Manufacturing facilities are the heart of our global supply chain. Shipping important items that are heavily relied upon by technology providers, medical professionals, small businesses, and consumers–without delay–is no small task.
Maintenance teams that choose user-friendly CMMS solutions to support preventive maintenance programs can reduce downtime, increase OTD, and increase organizational profits. In-house technicians who take the time to shadow outsourced equipment service providers also contribute to facility efficiency.
Has your organization abandoned a CMMS solution because it was overly complicated, time-consuming, and unenjoyable? If so, we invite you to download our app for free. Find out why companies like Hilton, Marriott, and McDonald’s are streamlining operations with MaintainX.
FAQs
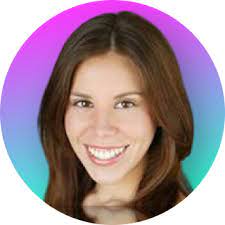