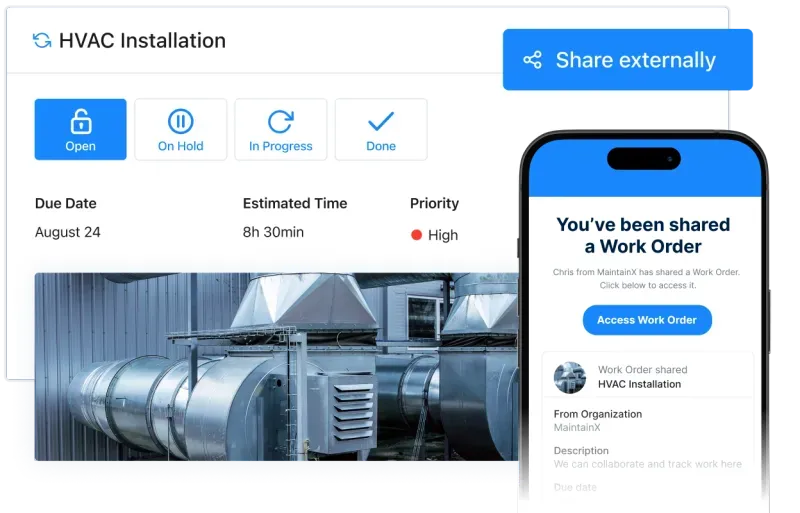
Imagine juggling multiple maintenance requests, tracking work orders manually, and constantly chasing updates—chaos builds, and small details slip through the cracks. Now, picture a streamlined system where tasks flow seamlessly, and every work order is created, assigned, and completed with minimal human intervention.
A good work order automation system transforms work order management by automating specific actions—like assigning tasks based on availability, tracking real-time progress, and flagging urgent requests. This minimizes manual intervention, ensuring critical tasks are handled quickly and routine tasks stay on schedule. Adopting a computerized maintenance management system (CMMS) can automate those types of administrative tasks and give your maintenance team a real-time view of task completion, ensuring accuracy and timely results.
What is work order automation?
Work order automation is a feature in some work order management systems that streamlines work order management. Instead of relying on manual processes, automation simplifies tasks like creating work orders, assigning them to teams, tracking progress, and reporting results.
For example, in a manufacturing facility, predetermined conditions can automatically generate a work order when equipment sensors detect unusual vibrations or temperatures. This triggers a maintenance task, which is instantly assigned to the appropriate technician based on their skill level and availability. The system then tracks the technician’s progress in real-time and updates the maintenance records once the work is completed. Functions like these boost efficiency, reduce errors, and free up maintenance teams to focus on more critical responsibilities.
Automation throughout the work order management process
With automated work order management, you can reduce the manual workload and let the software handle the rest. For example, a technician completing a routine inspection of an HVAC unit might notice a part that shows signs of wear. Instead of manually filling out a work order request, the system automatically generates one based on the technician’s input, schedules the repair, and assigns it to the appropriate team. A reliable automation system can manage many work order-related tasks, including:
Automated work order creation
You can integrate digital meters and Internet of Things (IoT) sensors into your CMMS system. With their input and your software's data analytics abilities, the system can automatically trigger work orders based on a range of criteria, such as:
- Equipment conditions (e.g., temperature, vibration, etc.)
- Continuous runtime thresholds
- Scheduled time intervals for specific tasks
Many systems, like MaintainX, offer customizable work order templates that make it easier for you to:
- Fine-tune specifications for repeating tasks
- Tighten up the process of work order generation for preventive maintenance tasks
Automated work order planning
Automation simplifies work order planning by taking advantage of real-time data and analytics, letting you prioritize tasks strategically. Here are some helpful planning features you can expect with a robust automated work order system:
- Real-time data collection: Systems can automatically gather critical information from equipment and sensors to identify maintenance needs.
- Task prioritization: Reliable work order software can flag and assign urgent tasks quickly.
- Automated technician assignment: Work order platforms can assign tasks based on technician availability, expertise, or location.
- Proactive scheduling: Predictive analytics can perform maintenance task planning to address potential issues before they arise.
Automated work order execution
With automation, putting work orders into action takes minimal effort. Once an automated tool or maintenance manager assigns a task, many software systems alert technicians, immediately informing them of what they need to do. Some key automated work order execution capabilities include:
- Real-time notifications: Technicians receive alerts for assigned work orders, priority changes, and upcoming deadlines.
- Instant access to information: A good work order management software system can relay maintenance history, work procedures, and asset details directly to the technician.
- Automated updates: Technicians can update the status of work orders as they progress, keeping everyone informed.
Automated work order tracking
With automation, maintenance managers can set up alerts to notify them when a team is running behind or when other issues pop up that might delay completion. This proactive approach lets managers act quickly to prevent equipment downtime or operational disruptions.
Users can also configure automation to send customers an email, text alert, or push notification, keeping them updated on the progress of work orders they're waiting on. This enhances customer satisfaction by giving them real-time communication without the need for manual follow-ups.
Take a busy hotel, for instance. When a technician faces delays fixing a faulty HVAC system, the automated system will send an alert to the maintenance manager. The manager can then assign extra help or move the task to another team to make sure the repair gets done quickly. Users can configure the automation to send the guest an email, text alert, or push notification to keep them updated on the progress of the repair. This enhances customer satisfaction by providing real-time communication without the need for manual follow-ups.
Automated tracking systems can also generate reports on work order completion times and identify recurring delays, giving you helpful insights for improving future workflows.
Automated asset inventory management
Automation in maintenance work order software makes tracking materials, spare parts, and supplies much easier and more accurate. An automated asset management system helps you track key inventory levels. You’ll know when supplies are running low, so you can keep what you need on hand and avoid running out of stock. This reduces downtime and keeps operations running smoothly.
Automation does all this by giving you:
- Automated alerts: Receive notifications when inventory levels dip below set thresholds, enabling you to focus on core operational duties.
- Automatic reordering: The system can automatically place orders for critical parts and materials, instilling confidence that you'll never run out of stock at a critical time.
- Inventory tracking: Easily track the usage and availability of parts across multiple locations or sites so you know what you have and what you need at a glance.
Automated work order documentation
Manually documenting service requests and work orders can be a time sink and open the door for mistakes. Automation simplifies work order documentation by generating records for each work order as it's completed.
You can enjoy a ton of benefits from automated documentation, including:
- Data capture: Automatically record key details such as assigned technician information, materials used, and time spent on the task.
- Issue tracking: Analytics helps users identify repeating issues and offer insights to help come up with long-term solutions to problems that happen over and over.
- Comprehensive maintenance history: Automatically store work order records, making it easy to review past maintenance activities and trends.
- Regulatory compliance: Ensure proper documentation to meet regulatory requirements without the risk of missing information.
Automated work order KPI tracking
Key performance indicators (KPIs) touch every corner of every industry these days. Common KPIs for maintenance teams include work order completion time, equipment downtime, and maintenance costs. Tracking these metrics helps you understand how efficiently your team operates and where improvements can be made with minimal manual effort. Automated systems collect and analyze data in real-time, offering dashboards and reports to highlight areas that need attention. This helps improve maintenance processes and strengthens the overall performance.
Work order management software systems can track many key metrics, including:
- Work order completion times: Measure how quickly your teams complete work orders to identify bottlenecks and improve response times.
- Technician performance: Analyze the productivity of individual technicians, ensuring tasks go to the right person for the job.
- Asset downtime: Track equipment downtime and use this data to improve preventive maintenance scheduling.
- Cost tracking: Automatically record and evaluate costs associated with each work order, helping to manage your budgets and reduce expenses.
Automated work order systems are easier to use than they sound
Automating work orders may seem complex or difficult to implement. However, an intuitive CMMS like MaintainX simplifies work order processes and greatly improves efficiency. This intuitive platform integrates nicely with existing systems, making it easy to get up and running. MaintainX offers an array of tools that make it the right choice for organizations.
- Seamless integration: MaintainX plays well with most existing work order management systems and other platforms, allowing you to get started quickly without overhauling your entire workflow.
- Mobile accessibility: Technicians can receive work orders and mobile push notifications that update them in real-time, even while in the field, enabling quick responses to maintenance tasks.
- Automated workflows: Easily set up and manage preventive maintenance, asset tracking, and inventory management workflows with just a few clicks.
- User-friendly interface: MaintainX’s platform is designed to be intuitive, so your team can start using it with minimal training and technical expertise.
With these features, automating your work order processes becomes much more manageable, helping your team tighten up operations and reduce manual work.
Automate your work orders with MaintainX
MaintainX empowers businesses to fully automate their work order processes, providing an all-in-one solution to simplify every aspect of work order management. You can rest assured knowing that tasks will be completed efficiently and on time. Here’s how MaintainX helps automate your work orders:
- Work from any mobile device, no matter where you are, to access full work order management functionality.
- Create work orders automatically based on equipment conditions, preventive maintenance schedules, or manual triggers.
- Assign tasks to the right personnel using automated workflows that consider technician availability and expertise.
- Track real-time work order progress through the dashboard, allowing managers to monitor tasks and updates from anywhere.
- Send automated notifications to technicians when tasks are assigned or when priorities change.
- Automate preventive maintenance scheduling to ensure that routine inspections and repairs are conducted on time.
- Manage inventory automatically by tracking parts usage and reordering materials when stock runs low.
- Generate work order reports automatically, providing data-driven insights for continuous improvement and compliance.
Take the next step in optimizing your maintenance practices by automating your work orders with MaintainX. Visit our work order management page to discover how MaintainX can help your team improve efficiency, reduce downtime, and streamline maintenance tasks.
Work order automation FAQs
What are the benefits of automating work orders?
Automating work orders reduces manual labor, improves efficiency, and decreases the chance of errors. It also allows real-time task tracking, automated notifications, and streamlined communication, helping maintenance teams complete tasks more quickly and effectively.
What are common challenges in work order automation?
Some common obstacles that facilities face with automation include properly integrating with older legacy systems, training staff to use new tools, and selecting the right features to meet your specific needs. However, a user-friendly CMMS like MaintainX reduces many of these challenges.
What are the best work order automation tools?
Every work order management system has its own strengths and challenges. The best tools for work order automation should offer real-time tracking, mobile accessibility, customizable workflows, and easy integration with existing systems. MaintainX provides all of these features, making it an ideal solution for businesses looking to achieve operational excellence.
How do automated work order systems integrate with other tools?
Automated work order platforms like MaintainX integrate easily with many other systems, such as enterprise resource planning (ERP) software and asset management systems. This allows for smooth data flow and reduces redundant entries, making it easier to manage several facilities operations across various systems from a centralized platform.
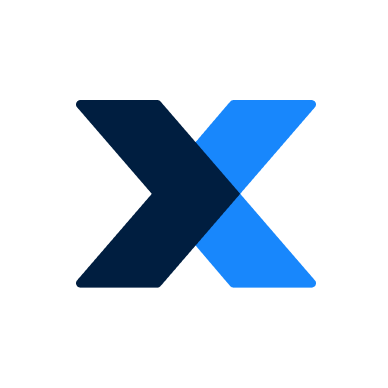
The MaintainX team is made up of maintenance and manufacturing experts. They’re here to share industry knowledge, explain product features, and help workers get more done with MaintainX!