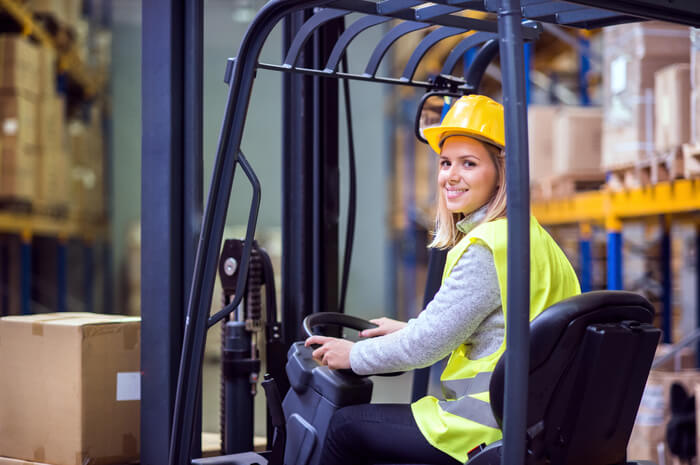
Forklifts are the backbone of the equipment industry.
Production facilities, construction sites, and warehouses use the large vehicles for handling heavy materials. Forklifts have a wide range of uses, from transporting pallets to plowing snow. The vehicles allow workers to transport large and heavy loads without throwing their backs out.
In addition to their utilitarian benefits, forklifts also have a fun side! Each year, hundreds of skilled forklift operators get together to compete in forklift rodeos. Contestants navigate courses, pick up basketballs from safety cones, and drop them through hoops using forklifts.
How to Operate a Forklift Safely (and Avoid Common Safety Hazards)
Considering the weight of the forklift comes in at a whopping 9,000 pounds, on average, operators must know how to operate a forklift safely—in both work and play settings.
In this article, we’ll answer the most common questions about forklift safety and operator training. We’ll also review the seven types of forklifts, types of hazards, and safety procedures for operating. Let’s begin by discussing exactly why knowing how to operate a forklift safely is essential.
Why Is Operating a Forklift Safely Important?
The good news is forklift accidents are uncommon. The large vehicles cause about one percent of accidents in warehouses and factories. The bad news is forklift accidents tend to be serious because of their massive weight. To put things in perspective, the average forklift weighs three times that of an average automobile!
Here are recent statistics on forklift accidents:
- 79 workers lost their lives in forklift-related accidents.
- 8,140 workers suffered nonfatal injuries and took leaves of absence.
- 19 percent of forklift accidents resulted in bone fractures.
- 20 percent of forklift incidents resulted in soreness, pain, sprains, strains, tears, bruises, and contusions.
Furthermore, organizations stand to lose productivity due to forklift accidents. Such accidents resulted in an average of 16 days away from work. Comparatively, the average time out for other workplace hazards is eight days. Trade, transportation and utilities, and service-providing industries report the highest number of forklift accidents.
What Is a Forklift?
A forklift is a powerful industrial tool used to move materials over short distances. The Merriam-Webster Dictionary defines a forklift as “a self-propelled machine used to hoist and transport heavy objects by using steel fingers inserted under the load.” Forklifts are also referred to as forklift trucks, fork hoists, fork trucks, jitneys, and lift trucks. They are most recognizable by their front-facing mast assemblies.

Fun fact: forklift usage is rising. A record 260,180 forklifts were sold in North America from 2014 to 2018. That’s great news for anyone wanting to find work as a forklift operator.
The 7 Classes of Forklifts
Operators must complete unique certifications for each class of forklift they drive. The classification system is organized according to forklift features, applications, and fuel options, among other factors. The Occupational Safety and Health Association (OSHA) categorizes forklifts into seven different classes:
- Class I-Electric Motor Forklifts: These forklifts have pneumatic tires, whereas other forklifts are fitted with cushion tires. Pneumatic tires are suited for dry, outdoor environments, while cushion tires are ideal for smooth, indoor floors. Industrial batteries and transistor motor controllers power Class I forklifts. The vehicles are best suited for facilities that prioritize air quality, such as storage facilities.
- Class II-Narrow-Aisle Electric Motor Forklifts: Facilities wanting narrow aisle operation to maximize their storage space prefer this class of forklifts. Electric motor trucks also have special features designed to optimize speed and efficiency.
- Class III-Hand-Rider Forklifts: Class III forklifts usually are usually by hand. The operator, in front of the truck, uses a steering tiller to control the lift. Side-to-side movement of the tiller steers the forklift. The truck’s controls are mounted on the tiller. Most Class III forklifts are battery-powered.
- Class IV-Internal Combustion Engine Forklifts: These forklifts are best suited for smooth, dry floors. They’re usually lower to the ground and are handy for low-clearance applications. Class IV forklifts have solid or cushion tires.
- Class V-Internal Combustion Engine Forklifts: Similar to Class IV forklifts, Class V forklifts share the same features with the exception of pneumatic tires. Class V forklifts are common in warehouses because they can be used for a variety of applications, both inside and outside. They have large capacities and can handle up to 40-foot loaded containers.
- Class VI-Internal Combustion and Electric Engine Forklifts: Class VI forklifts are versatile and suitable for a number of applications. They’re usually equipped with battery-powered electric motors for indoor use. For outdoor applications, they rely on internal combustion engines.
- Class VII-Rough Terrain Forklifts: Driving on large floatation tires, operators can easily drive class VI forklifts on difficult, outdoor surfaces. For this reason, they’re commonly found in construction sites, auto recyclers, and lumberyards.
The 5 Most Common Forklift Hazards
Modern-day forklifts boast enhanced features, making them safer than earlier versions. However, taking precautions when operating heavy machinery is always important. Forklift safety starts before the vehicle is even turned on!
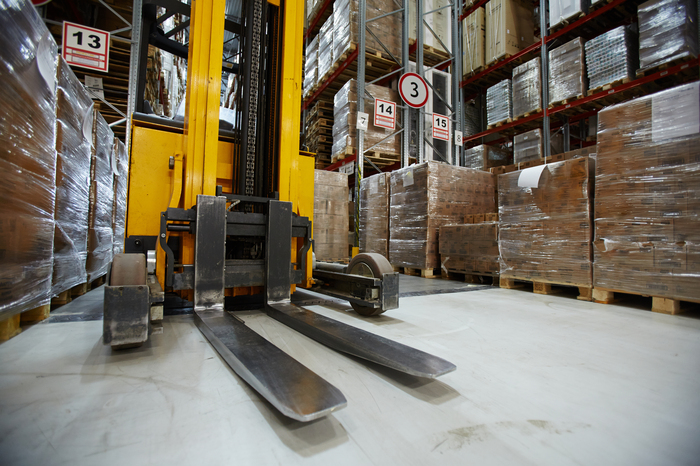
According to OSHA, more than half of forklift accidents were preventable. It’s important to know how accidents can happen to be prepared. Here are the most common forklift hazards:
1. Overturning Forklifts
According to the National Institute for Occupational Safety and Health (NIOSH), overturning forklifts are responsible for about 25 percent of forklift fatalities. Uneven weight distribution is the most common cause of overturning forklifts. Excess loads, unusual loads, high heights for heavy loads, and obstructed operator view also can cause forklifts to overturn.
Proper training can reduce the likelihood of overturns. Forklift operators should never jump off trucks when they are overturning. Instead, they should remain seated, lean in the opposite direction, and hold on tight to avoid serious injuries.
2. Crushing, Striking, and Pinning
Other workers in a facility are also at risk of getting crushed, struck, or pinned by forklifts. This usually happens when they’re in the path of an overturning forklift or in the operator’s blind spots. Overcrowded or poorly laid out facilities expose workers to such dangers.
Facilities should develop traffic management plans. Plans should outline clearly defined paths for pedestrians and forklifts. Physical barriers such as railed walkways and bollards can help with this effort.
3. Falling Loads
Falling loads also expose workers to the risk of getting injured. This event usually occurs when lifting loads without properly attached pallets. Out-of-balance loads can fall when lifted too high. Forklift operators and loaders should ensure materials are balanced and secured properly before lifting.
4. Blind Spots
Unfortunately, forklift loads can create blind spots for operators. Visual blockages can cause drivers to run into other workers and facility assets. When carrying huge loads, operators should drive in reverse to maintain clear sight of their path.
Similarly, forklifts require plenty of clearance area as the front end usually has a tight turn while the back end tends to swing wide when making a turn. Facility workers should stay away from the operator’s blind spots.
5. Speed
Forklift speeds and weights can create strong momentum. Even at low speeds, trucks can cause as much damage as a car driving 15 miles per hour. Operators should drive within indicated speed limits. They should also slow down and sound the horn when approaching intersections. Forklifts should be driven at speeds that allow the operator to stop safely within the stability triangle. Attachments, emission poisoning, refueling and recharging, floor conditions, and mechanical failures are other common forklift hazards.
The Most Important Forklift Procedures for Operating a Forklift Safely
Disclaimer: the operating procedures and safety guidelines below are NOT intended to substitute for proper forklift training. Operating a forklift requires an operator to be fully alert. At no time should someone operate a forklift when overtired, drowsy, or medicated. If a manager or supervisor suspects any of these factors are at play, he should not permit operation.
The National Institute for Occupational Safety and Health (NIOSH) details several case studies that clearly show the importance of OSHA requirements for forklift safety training programs. Now, onto the most important forklift safety procedures and commonly enforced worksite rules:
1. Conducting Pre-Operation Inspections
At the beginning of each shift, an operator must carry out a pre-operation inspection. Forklifts are sturdy machines, but they experience wear and tear over time. Just as a pilot will personally inspect an aircraft before taking flight, a forklift operator must ensure his or her vehicle is in shape to perform tasks. Below is an example of the tasks included on a general safety checklist for pre-operational inspections. Keep in mind that one type of forklift won’t have exactly the same checklist items as another.
Safety Checklist for Pre-Operation Inspections:
- Controls
- Fuel, engine oil, and radiator water levels
- Battery plug connections
- Battery is fully charged
- Wheels and tires
- Electrolyte levels and cells
- Chain anchor pins
- No damp spots beneath forklift (could indicate a leak)
- Hydraulic hose reels
- Control levers
- Forks
- Immediate area clear (on floor and overhead)
- Horn
- Brakes
- Clutch and gear shifts
- All lights and gauges
- Steering
- Lift and tilt mechanisms
- Seat belt
- Reverse beeper and warning lights
Ensuring forklifts function as they should is vital for employee safety. These steps, while lengthy, can be the difference between an on-site accident happening or not.
If your company requires a logged inspection for liability reasons, use an app like MaintainX.
2. Handling Pallets
Operators must confirm forks are level and correctly positioned as they enter a pallet. Level forks ensure the proper distribution of weight (if uneven, the forklift can tip over). Be aware of pallet sizes and load center calculations to move pallet loads safely. Once a load is positioned on the forks, do not attempt to reposition anything. Never use a pallet stationed on a forklift as a work platform.
3. Loading
Each forklift has a data plate indicating a recommended load limit for its specific model. These limits aren’t intended to be soft guidelines—overloading a forklift can cause serious injury.
However, knowing the capacity isn’t enough. Correct weight distribution prevents forklift tip-overs. Learning to arrange and balance materials is a crucial element of forklift training. To keep the lift stable, place the load as close to the front wheels as possible to maintain balance. Never counterbalance an overload by adding more weight.
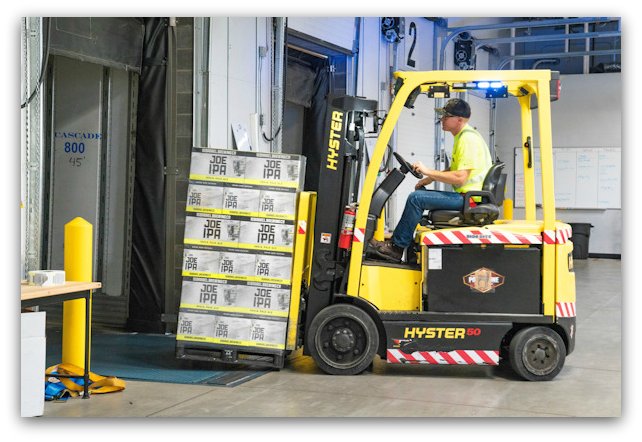
Before inserting the fork into a pallet, ensure the fork is level. The vehicle’s mast must remain in an upright position. Finally, also pay attention to loading dock safety guidelines. Loading docks are high-traffic zones that require vigilance. Operational managers should take precautions such as creating safety patches, ensuring docks are free of debris, and securing trailers with rig obstructions.
4. Raising the Load
Never raise or lower the fork until the truck is fully stopped and the brake is engaged. When lifting, bring the load straight up, and then tilt it back slightly. Once a load is lifted, the forklift loses some of its stability, and tilting the weight compensates for this.
Depending on the truck, be sure to avoid lifting a load that extends past the load’s backrest. It is extremely unsafe if any or all of the load can shift back toward the driver. Before raising a load, check for enough overhead clearance, and if outdoors, always maintain a safe distance from power lines. Once a load is lifted, the operator must remain on the truck. Additionally, whether or not a lift is loaded, never let anyone walk or stand under an elevated fork.
5. Loading/Unloading Tractor Trailers and Railway Cars
Before loading or unloading, engage the brakes and chock the wheels. When unloading a semi-trailer that isn’t coupled to its tractor, install fixed jacks to support and prevent upending it. Be sure that you have at least 2 inches (5 cm) clearance between the forklift height and the trailer door. Also, determine that the bed of the trailer can support both the weight of the load and forklift.
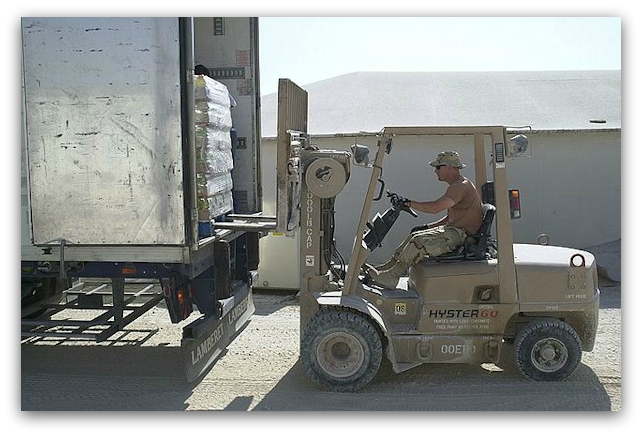
When loading or unloading rail cars always cross the tracks diagonally. Don’t park within approximately 10 ft (3 meters) of the tracks and never attempt to open railcar doors with the forks. Never operate a forklift for an extended time within a trailer or boxcar without proper ventilation.
6. Traveling
A moving forklift is a dangerous forklift. At all times, an operator’s hands, arms, feet, legs, and head must remain within the forklift truck. Forks, whether loaded or not, should be kept as low to the ground as possible and tilted back.
When approaching corners, always slow down and sound the horn. Be sure to watch for swing in the load and the rear of the truck. If possible, avoid sudden stops. If the line of vision is obscured by the load, drive slowly in reverse. Always look in the direction of travel. Learn the forklift’s blind spots, whether loaded or not. If traveling on an incline, the forks should be pointed uphill when carrying a load and downhill without a load.
7. Steering
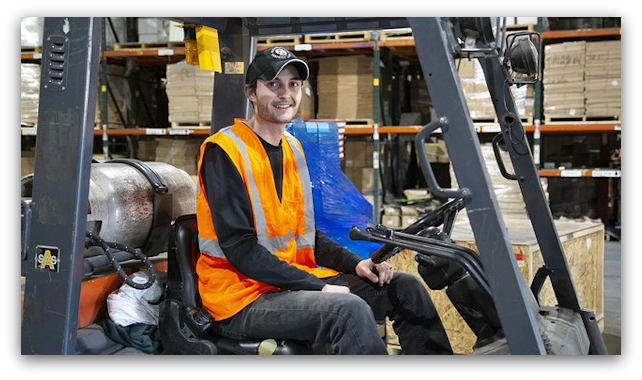
Steering a forklift is nothing like steering a car because lifts are significantly more top-heavy—and even more top-heavy when the forks are at the top of the mast. S forklift is a rear-wheel-drive, making it very hard to make quick stops, so never drive fast or round corners too quickly. Never give the steering wheel a sharp crank when driving at any speed. Before changing directions, come to a full stop, and before executing any turns, slow down first. Never attempt to turn a forklift around when on uneven ground.
8. Entering Elevators
Never enter an elevator without having specific authorization. Before entering an elevator, be sure that the combined weight of the load, the driver, and the forklift doesn’t exceed the maximum weight capacity of the elevator. Ensure you have ample clearance and then enter the elevator slowly and squarely. Once inside, brake and turn off the motor.
9. Parking
A parked forklift is still a dangerous forklift. Only park a forklift in approved locations. Before leaving it unattended, ensure that the brakes are secured, all controls are set to the neutral position, and the forks are lowered to ground level.
Make sure you turn off the motor and remove the key. Follow these steps regardless of how long an operator plans to be away from the vehicle. Ready to see forklift truck operation in action? Check out the video in the next section for a quick glimpse into what it’s like to drive one of these massive vehicles.
10. Wear Personal Protective Equipment (PPE)
OSHA requires employers to provide their workers with safety equipment that protects their eyes, ears, head, and extremities. Personal Protective Equipment (PPE) must be maintained and worn on the job whenever necessary.
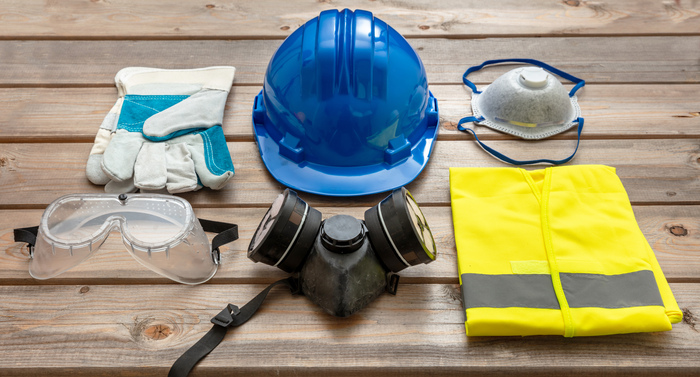
Should workers supply their own PPE, employers must verify that their gear meets OSHA’s minimum standards. Additionally, employers must either confirm that employees know how to correctly use PPE or provide them with OSHA-approved retraining. Forklift operators should wear:
- Safety Shoes: Prevent or mitigate crushing injuries that could result from a worker’s foot being run over by a forklift. Usually, steel-capped boots are worn.
- Safety Gloves: Protects hands from residues, harsh chemicals, and bruising from lifting heavy pallets. Also, provides a better grip when handling grimy controls.
- Reflective Clothing: Allows workers to be easily seen when entering and exiting vehicles.
- Hard Hats: Provides a safe barrier between potential dangers and operators’ heads.
- Safety Goggles/Shields: Worn when working around concrete, harmful chemicals, or other foreign matter.
After completing forklift safety training and familiarizing themselves with important safety procedures, individuals are finally ready to drive. Below is a quick glance at what that entails.
How Do You Operate a Forklift?
Different types of forklifts have different modes of operation. Operators should be certified for the particular class of forklift they will be driving. While different types of forklifts are operated differently, this video provides a general explanation of how to operate a forklift.
After watching the video above, you may be wondering: is operating a forklift easy?
With proper training and experience, forklifts are fairly simple to operate. Most folks can learn how to operate a forklift within a short period with enough practice. However, maximum attention is always required when operating a forklift. Operators should never let their guard down at any time, no matter how experienced they may be.
Additional Resources for Operating a Forklift Safely
Here are additional resources on how to safely operate a forklift:
- Convergence Training: How to Operate a Forklift
- OSHA: Traveling & Maneuvering
- Atlantic Training: Forklift Safety Tips A Comprehensive Resource
- OSHA: Powered Industrial Trucks – Forklifts
Want to access your team’s procedural checklists from your smartphone?
FAQs
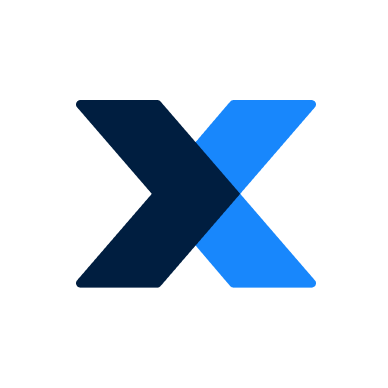
The MaintainX team is made up of maintenance and manufacturing experts. They’re here to share industry knowledge, explain product features, and help workers get more done with MaintainX!