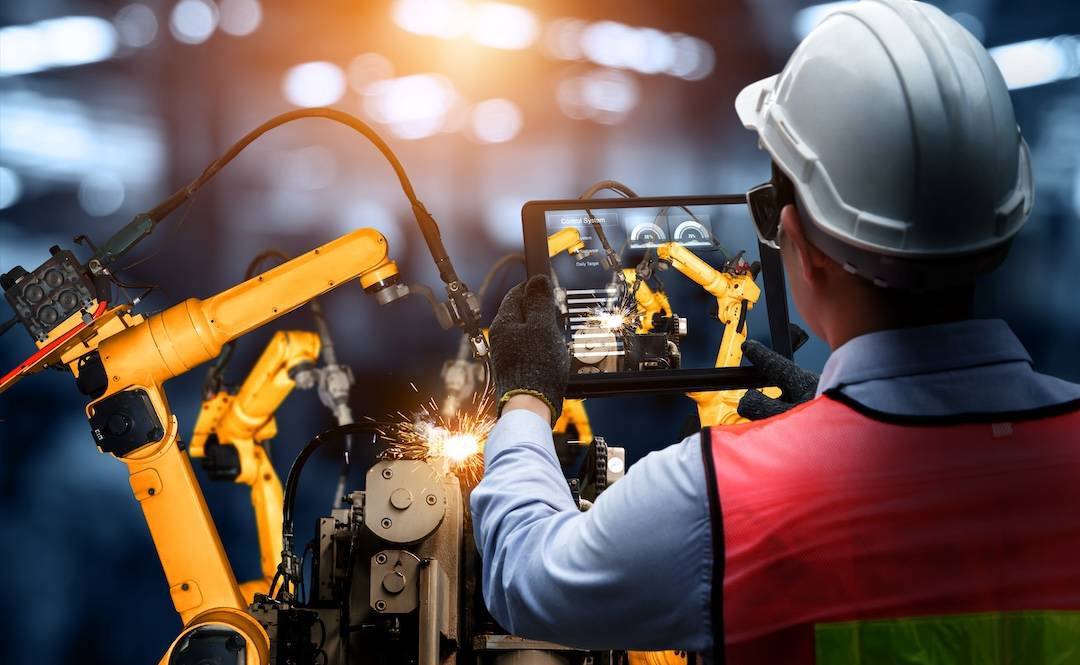
After spending years working alongside frontline manufacturing teams, I’ve come to see one thing clearly: preventing incidents isn’t just a legal requirement—it’s the heartbeat of a healthy operation. With workplace safety making headlines daily—and often with tragic details—it’s time to highlight how emerging tech is changing this narrative.
If you’re like most maintenance and operations managers, keeping your team safe is a top priority. In fact, “number of safety incidents” is one the top five metrics maintenance, repair, and operations professionals track.
Everyone deserves to go home safely after work every day, and even one injury is one too many. Plus, workplace accidents damage employees’ trust and hurt your company’s ability to attract and keep top talent. Safety incidents also take a heavy financial toll—on average, a workplace injury can cost an organization more than $100,000.
Fortunately, tech innovations are rising to the challenge of helping operations professionals minimize accidents and stay compliant with OSHA regulations. Here are a few examples of how new technologies—including AI, automation, and mobile-first software tools—can make it easier than ever to create a safe environment for your team.
New tools to manage workplace safety
Predictive AI
In many ways, AI is the next frontier of safety: proactively addressing hazards instead of reacting after incidents occur. On the safety front, when combined with IoT sensors, AI tools can predict problems before they emerge. This allows teams to complete repairs early—before equipment issues become dangerous or cause a shutdown.
→ Get AI for Industrial Manufacturing
Machine vision
From my conversations with operations managers, I often hear concerns about “human error”—and machine vision is a direct answer to that. It provides constant oversight where no single human could possibly maintain focus.
Did you know a human scanning security footage loses half their ability to spot problems within just 18 minutes? Human focus naturally fades with time. AI tools, on the other hand, never get bored or tired. They can analyze camera footage to track workers entering restricted areas, spot safety violations, and monitor personal protective equipment compliance.
Drone inspections
Recently, I visited a chemical plant where drones drastically cut down inspection times—no more scaffolding or harnesses for hours on end. And that’s a safety win across the board.
Drones are revolutionizing inspections, making it easier to monitor gantries or check inventory without workers clambering to unsafe heights. In chemical factories, thermal imaging and gas sensors enable drones to conduct detailed safety inspections in risky environments, minimizing downtime while keeping humans out of harm’s way.
Intelligent LOTO
Any maintenance supervisor will tell you: lockout-tagout (LOTO) mistakes lead to some of the scariest near-miss incidents. Digitizing these processes not only reduces those errors but also fosters trust within teams—the sense that the organization truly values their well-being.
When your organization digitizes LOTO, your team gains visibility into which tasks are underway. If protocols aren’t properly followed, these tools can trigger automatic alerts or a shutdown. They also offer digital audit trails, plus full documentation to support training and improvement.
Centralized knowledge bases
I’ve watched teams struggle with scattered SOPs or outdated binder checklists. No matter how committed you are to safety, if you can’t quickly reference the right procedure or flag a problem in real-time, it leads to needless risk.
Modern computerized maintenance management systems (CMMS) put critical information at employees’ fingertips. With a central workflow management hub, teams can track maintenance tasks, communicate quickly, access up-to-date documentation, and make sure they’re complying with standard operating procedures.
This ultimately helps teams break down hazardous silos. From maintenance techs to leadership, a CMMS gives all parties the real-time information they need to act quickly on issues.
Mobile-first systems
With a mobile-friendly maintenance system, frontline team members can simply flag concerns on their phone or tablet—attaching a quick photo or video to illustrate an issue—and let the right person on the team take it from there. Or, they can access digital SOPs for a step-by-step guide to fixing the problem.
There’s no need for a flurry of phone calls, emails, and radio messages to coordinate a response. Everyone on the team gets updated automatically so they can carry out safety measures efficiently.
AI for standardization
Reliable equipment translates to a safer environment—and one key to keeping your equipment reliable is ensuring every technician consistently follows the same procedures. But operations managers know this is easier said than done. Digitizing procedures can be a tedious and excessively time-consuming process.
This is where AI changes the game. In minutes instead of hours, AI assistant tools can take thousands of pages of asset manuals or work orders and transform them into standardized digital procedures that keep techs in sync.
Accurate data monitoring and reporting
Modern reporting tools offer leaders a clearer picture of their safety KPIs. With the ability to accurately monitor performance in real-time, managers can think more strategically about how to improve safety measures.
Leaders can keep an eye on equipment data, analyze failure patterns, and flag indicators of possible safety issues. The software makes it simple to generate reports and provide audit trails for safety-related maintenance activities. High quality, accurate frontline data is also the lifeblood for future AI-related safety and reliability improvements.
Safety is a competitive advantage
In every plant I visit, the teams who treat safety as a strategic pillar—rather than an obligation—are the ones who see stronger morale, better retention, and higher productivity. They’re also the ones leading their industries into the next era of manufacturing.
You may have noticed that preventive maintenance support is a major theme when it comes to safety innovations. As Woody Rogers, maintenance supervisor at Cintas, puts it, “The longer you go without completing the PMs on an asset, the more wear and tear you will see on it, and the more likely you are to run into unexpected equipment failures, downtime, or accidents.”
For operations leaders, setting higher safety standards by embracing technology that optimizes preventive maintenance activities is practically a requirement for success. Because safety isn’t just about complying with state and federal rules—it’s a competitive advantage for organizations that want to support their teams, operate more intelligently, and maximize profits.If you haven’t started adopting these technologies—whether it’s AI-driven LOTO, drone inspections, or mobile-first SOPs—pick one area and pilot it. You’ll be amazed how quickly small changes can transform your entire safety culture.
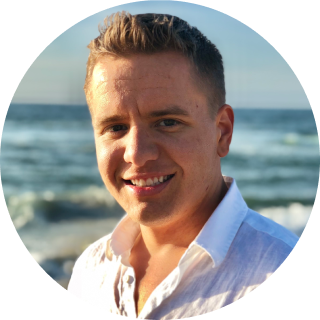
Nick Haase is a co-founder for MaintainX and is responsible for designing and leading the go-to-market strategies. He is a subject-matter expert in emerging CMMS technologies.