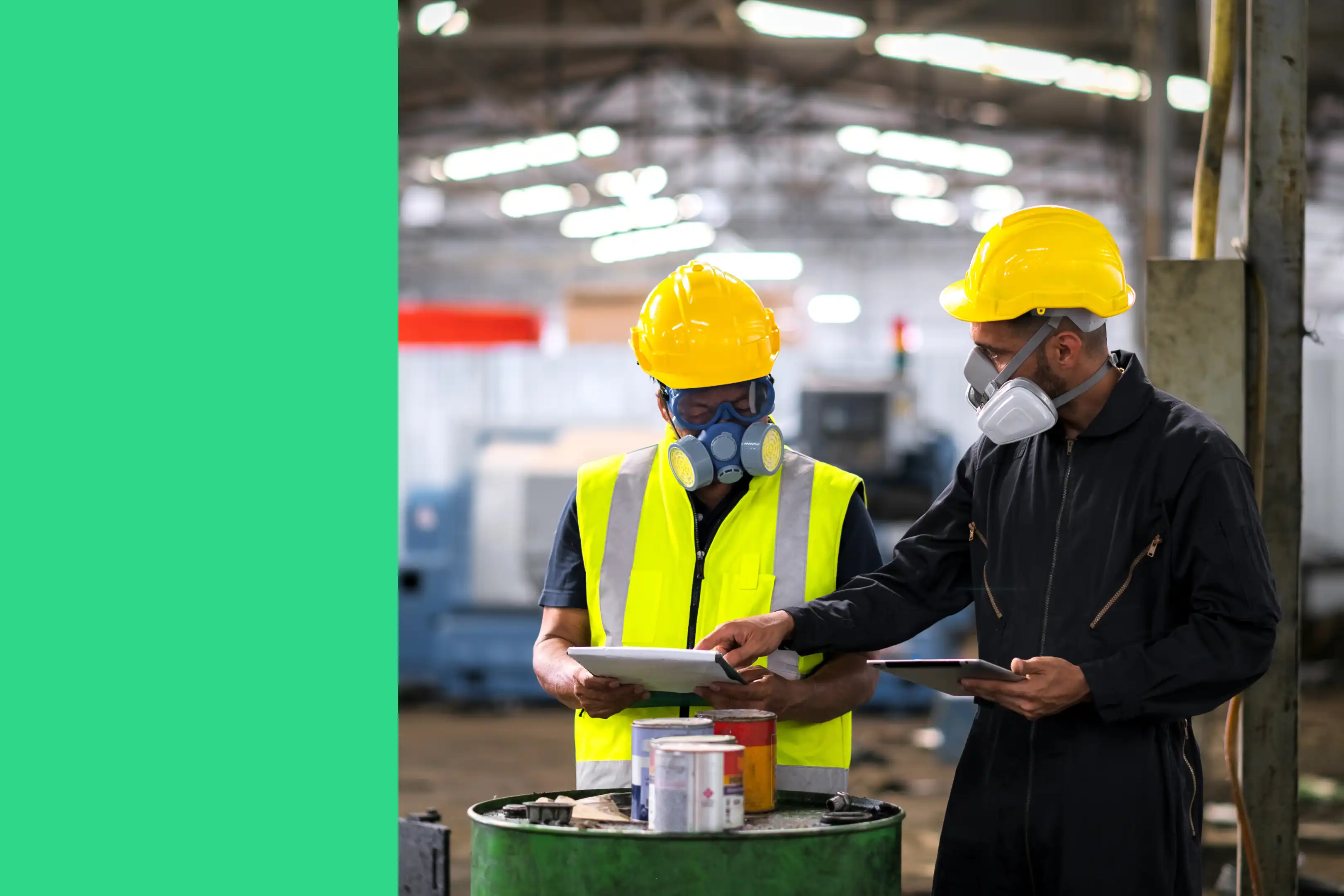
According to the U.S. Bureau of Labor Statistics, a worker died every 99 minutes from a work-related injury in the United States in 2023. There were also 5,283 fatal work injuries recorded nationwide. And while this is a 3.7-percent decrease from 5,486 in 2022, you know safety concerns persist across industries where proper safety procedures could prevent countless accidents.
When organizations fail to implement and enforce effective safety procedures, the consequences can be devastating. As a safety, plant, or general manager, you’re responsible for adhering to standard operating procedures (SOPs) that protect workers from harm and minimize exposure to unsafe conditions. Comprehensive workplace safety rules serve as the foundation for creating a safe working environment where personal safety becomes everyone's job.
In high-pressure situations at a facility, safety procedures can sometimes take a backseat when workplace demands increase. Even the best teams occasionally find themselves with safety equipment that needs inspection, electrical hazards that require attention, or personal protective equipment requirements that gets overlooked during busy periods.
Simply establishing safety protocols isn't enough. You need to continuously enforce them within robust safety training programs that empower your employees to identify potential hazards and make safe choices that protect both themselves and their co-workers.
In this post, we'll examine the most common industrial and office workplace safety hazards along with standardized procedures for preventing workplace injuries. You’ll get guidance on conducting thorough risk assessments and implementing proper safety inspections. We’ll also show you how to use digital tools to enhance compliance with safety regulations while maintaining comprehensive documentation of your safety program.
Key takeaways
- Implementing consistent safety procedures across your facility prevents accidents and protects your team from preventable hazards.
- The top OSHA violations for 2024 include fall protection, hazard communication, and lockout/tagout procedures. Prioritizing these areas can significantly reduce workplace injuries.
- Industrial environments face unique safety challenges, including ergonomic injuries, indoor air quality issues, and psychological hazards that require specific prevention strategies.
- When you digitize safety procedures through CMMS platforms, you’ll improve compliance rates, streamline reporting, and create accountability while preserving organizational safety knowledge.
What are workplace safety procedures?
As a maintenance professional, you know workplace safety procedures protect your team from hazards, prevent accidents, and ensure regulatory compliance. These procedures go beyond basic compliance to establish a proactive safety culture that integrates occupational safety into every aspect of your daily operations.
According to OSHA (Occupational Safety and Health Administration), employers must "keep their workplace free of serious recognized hazards" under the General Duty Clause of the OSH Act. Effective safety procedures help organizations fulfill this obligation by identifying, evaluating, and controlling workplace safety concerns before accidents occur.
A robust workplace safety program in your facility should include these interconnected elements:
- Hazard identification and risk assessment: Systematically evaluating your workplace to identify potential safety hazards, including physical, chemical, electrical, ergonomic, and psychological risks
- Written safety policies and SOPs: Developing clear, accessible documentation that outlines specific protocols for safely operating equipment, handling hazardous materials, and responding to emergencies
- Safety training programs: Providing comprehensive instruction to your team on recognizing hazards, using personal protective equipment properly, and following established safety rules
- Regular safety inspections: Conducting periodic safety inspections to verify compliance with safety procedures and identify areas needing improvement
- Incident reporting and investigation: Establishing clear protocols for reporting accidents, near-misses, and unsafe conditions, followed by thorough investigations to prevent recurrence
- Emergency response planning: Creating detailed procedures for handling fires, chemical spills, natural disasters, medical emergencies, and other crisis situations
OSHA is increasingly emphasizing strengthened enforcement efforts with increased inspections, particularly in high-risk industries like construction and manufacturing. The agency has also focused on enhanced data collection to identify patterns in workplace injuries, with employers in certain industries now required to submit more detailed injury and illness information electronically.
Six types of safety procedures
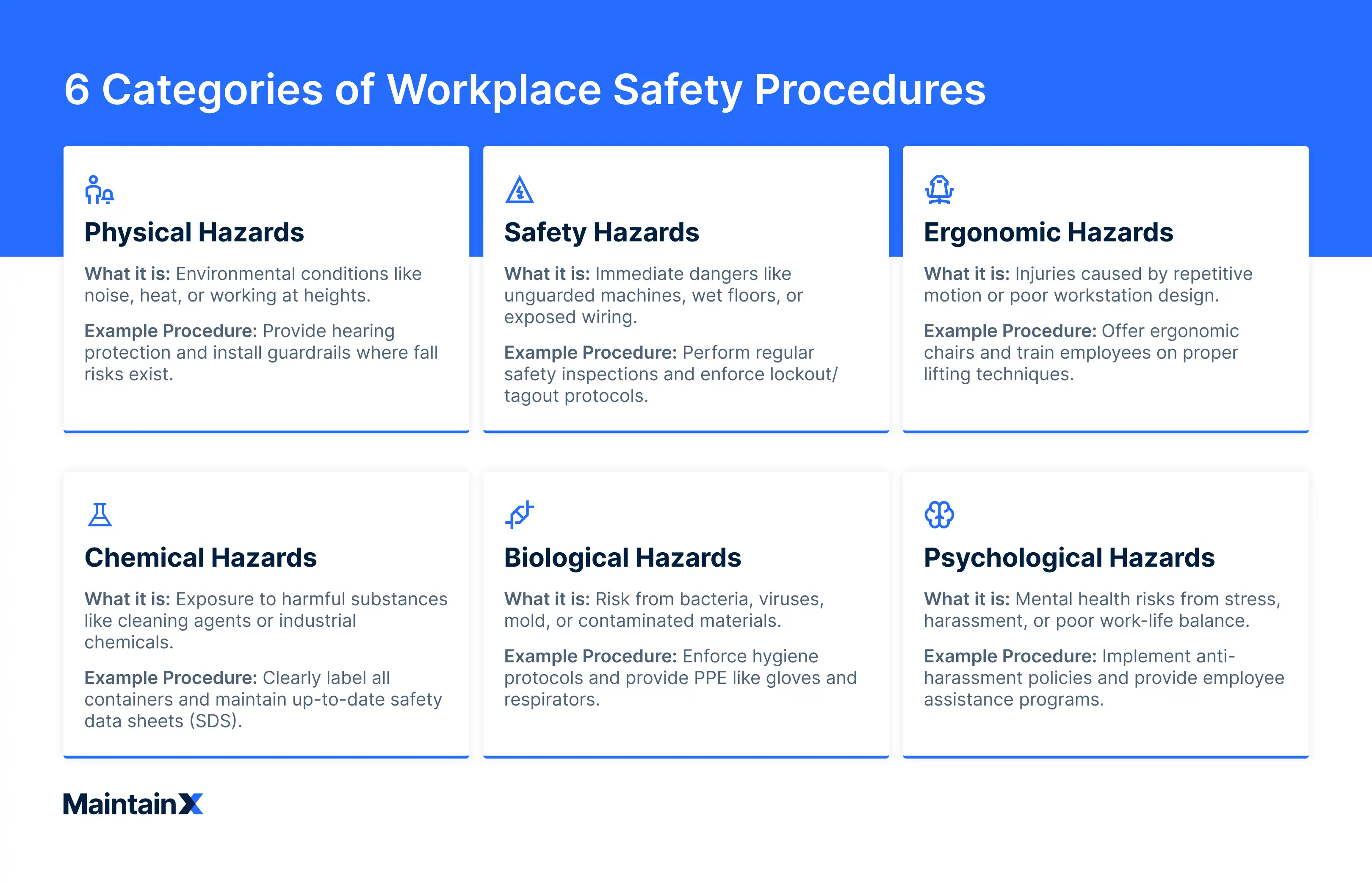
Unsafe conditions in your workplace fall into several categories, each requiring specific safety procedures to effectively protect your team and prevent accidents.
- Physical hazards: These environmental factors can harm your employees without necessarily making direct contact. Examples include excessive noise that can damage hearing, radiation exposure, extreme temperatures that can cause heat stress or cold injuries, and working at heights without proper fall protection. Safety procedures for physical hazards typically involve engineering controls, administrative controls, and providing appropriate personal protective equipment.
- Safety hazards: These include conditions that can cause immediate accidents and injuries through direct contact. Common safety hazards in your facility might include exposed electrical wiring that creates electrical hazards, unguarded machinery with moving parts, wet floors that contribute to slip and fall incidents, and improperly stored materials that could fall and strike workers. Proper safety procedures include regular safety inspections, implementing lockout/tagout protocols for electrical equipment, and ensuring proper housekeeping practices.
- Ergonomic hazards: These factors damage an employee's musculoskeletal system through repetitive motions, improper lifting techniques, or poorly designed workstations. Safety procedures addressing ergonomic hazards include workstation adjustments, task rotation to prevent repetitive strain, proper training on lifting techniques, and providing ergonomic equipment designed to minimize physical strain.
- Chemical hazards: These pose threats through hazardous substances that can cause severe injury or health risks upon exposure. Chemical exposure may result in skin irritation, respiratory problems, blindness, corrosion damage, or, in severe cases, explosions and fires. Your safety procedures for handling chemicals should include proper labeling, maintaining detailed safety data sheets, providing ventilation systems, implementing chemical storage protocols, and requiring appropriate personal protective equipment such as gloves, goggles, and respirators.
- Biological hazards: These include exposure to harmful organisms like bacteria, viruses, insects, animals, or plants that can adversely affect employee health. They often result from contact with mold, blood, sewage, contaminated materials, or harmful plants in the working environment. Effective safety procedures include vaccination programs, hygiene protocols, proper waste disposal systems, containment measures, and personal protective equipment appropriate for the specific biological risk.
- Psychological hazards: These hazards impact your employees' mental health and overall well-being. Examples include workplace violence, excessive stress, harassment, victimization, and poor work-life balance. Safety procedures addressing psychological hazards include violence prevention programs, stress management training, clear anti-harassment policies, employee assistance programs, and creating a positive workplace culture that supports mental health.
Neglecting any category can jeopardize your team’s health and well-being while potentially exposing your organization to liability, regulatory fines, and increased workers' compensation costs.
Five most common industrial safety hazards and procedures for prevention
Every year, OSHA publishes a list of the Top 10 Most Frequently Cited Standards. Here’s the top five from that list for fiscal year 2024:
1. Fall protection
Falls remain the leading cause of serious workplace injuries and deaths. In 2024, OSHA issued 7,036 violations related to fall protection requirements.
Prevention procedures you can implement:
- Conduct thorough risk assessments to identify potential fall hazards.
- Install proper guardrails, safety nets, or personal fall arrest systems when working at heights.
- Keep your floors clean, dry, and free from trip hazards.
- Implement comprehensive fall protection training programs.
- Regularly inspect fall protection equipment for damage or wear.
2. Hazard communication
With 3,277 violations in 2024, hazard communication remains a critical safety concern. Your facility likely uses different chemicals, with workers potentially exposed to hazardous substances.
Prevention procedures you can implement:
- Label all chemical containers clearly with product identifiers and hazard warnings.
- Maintain detailed safety data sheets (SDS) for all hazardous chemicals.
- Develop a written hazard communication program for your team.
- Train your employees on chemical hazards and protective measures.
- Implement proper ventilation and storage protocols for hazardous materials.
3. Control of hazardous energy (lockout/tagout)
OSHA issued 2,967 citations for lockout/tagout violations in 2024. Accidental machine startups during maintenance or servicing can result in serious injuries or fatalities.
Prevention procedures you can implement:
- Develop comprehensive lockout/tagout procedures for all equipment.
- Train authorized employees on proper lockout/tagout techniques.
- Use standardized locks and tags that identify the employee performing the work.
- Conduct periodic inspections of your lockout/tagout procedures.
- Ensure all energy sources in your equipment (electrical, hydraulic, pneumatic, etc.) are properly controlled.
4. Ladder safety
With 2,897 violations in 2024, ladder safety continues to be a significant concern across industries.
Prevention procedures you can implement:
- Select the right ladder for the job (correct type and height).
- Inspect ladders for damage or defects before use.
- Set up ladders on stable, level surfaces away from doorways or heavy traffic areas.
- Maintain three points of contact when climbing (two hands and one foot, or two feet and one hand).
- Ensure your employees understand proper ladder usage and safety procedures.
5. Respiratory protection
With 2,835 violations, respiratory protection rounds out the top five most-cited standards.
Prevention procedures you can implement:
- Conduct workplace assessments to identify respiratory hazards.
- Develop a written respiratory protection program for your team.
- Select appropriate respirators based on specific workplace hazards.
- Provide medical evaluations and fit testing for your employees using respirators.
- Train employees on proper respirator use, maintenance, and limitations.
By prioritizing these areas of workplace safety, organizations can address the most common causes of industrial accidents and injuries. Digital safety management systems can help streamline compliance with these critical safety procedures while maintaining comprehensive documentation for regulatory requirements.
Eight most common office safety hazards
Your office spaces don't present the same obvious dangers as industrial environments, but they harbor their own set of safety hazards that can lead to injuries, illness, and lost productivity when overlooked.
- Slips, trips, and falls. The most common office accidents involve slips, trips, and falls, often resulting from wet floors, loose carpeting, poor lighting, or cluttered walkways. Prevention measures include maintaining clear pathways, promptly addressing spills, securing loose cabling, providing adequate lighting, and posting warning signs for potential hazards.
- Ergonomic injuries. Prolonged computer use, improper workstation setup, and repetitive tasks can lead to musculoskeletal disorders like carpal tunnel syndrome, neck strain, and back pain. Implement ergonomic assessments, provide adjustable furniture and equipment, encourage regular breaks, and train employees on proper posture and workstation setup.
- Indoor air quality issues. Poor ventilation, chemical contaminants from cleaning products, and biological pollutants like mold can affect employee health and productivity. Regular HVAC maintenance, proper cleaning protocols, prompt addressing of water damage, and adequate ventilation help maintain healthy indoor air quality.
- Fire hazards. Overloaded power outlets, damaged electrical cords, improper storage of flammable materials, and blocked emergency exits create serious fire risks. Prevent office fires through regular electrical system inspections, proper storage practices, clear emergency exit pathways, functioning fire extinguishers, and comprehensive fire drill procedures.
- Electrical hazards. Frayed cords, overloaded circuits, and improper use of extension cords can cause electrical shocks, burns, or fires. Implement regular electrical inspections, avoid daisy-chaining power strips, replace damaged cords immediately, and train employees on electrical safety practices.
- Eye strain and vision issues. Computer vision syndrome affects many office workers who spend hours looking at screens. Prevention strategies include implementing the 20-20-20 rule (looking at something 20 feet away for 20 seconds every 20 minutes), proper monitor positioning, adequate lighting, and regular vision check-ups.
- Workplace violence and security concerns. Office environments are not immune to workplace violence or security breaches. Develop comprehensive security protocols, secure entry points, provide emergency response training, implement visitor management systems, and establish clear reporting procedures for concerning behavior.
- Mental health and stress-related hazards. Workplace stress, excessive workloads, harassment, and poor work-life balance can severely impact employee mental health. Address these issues through reasonable workload management, anti-harassment policies, employee assistance programs, stress management resources, and creating a supportive workplace culture.
By identifying and addressing these common office hazards, you can create a safer working environment that promotes employee well-being and productivity. Regular safety training, clear communication, and proper documentation of safety procedures are essential for maintaining a culture where safety is prioritized in all your workplace activities.
Enhance compliance with safety procedure digitization
As you work to implement comprehensive safety procedures, the challenge often lies in consistent execution, documentation, and tracking. Digital solutions have transformed how your team can manage workplace safety programs, making compliance more accessible while providing valuable data insights that drive continuous improvement.
Modern digital safety management systems like computerized maintenance management systems (CMMS) offer significant advantages over traditional paper-based approaches. These platforms centralize safety protocols, streamline inspections, and create digital audit trails that demonstrate regulatory compliance while identifying potential safety gaps.
The benefits of digitizing workplace safety procedures include:
- Real-time monitoring and alerts: Digital systems provide immediate visibility into safety compliance status and can automatically notify responsible parties when inspections are due or issues need addressing.
- Improved accountability: Electronic workflows track task completion, creating clear responsibility chains and ensuring safety procedures aren't overlooked during busy periods.
- Enhanced data collection: Digital tools capture comprehensive safety information that can be analyzed to identify trends, recurring issues, and opportunities for improvement.
- Streamlined reporting: Generate compliance reports instantly, saving your team hours of administrative work while providing better documentation for regulatory inspections.
- Mobile accessibility: Your field workers can access safety procedures, report issues, and complete inspections from smartphones or tablets, enabling real-time safety management across distributed worksites.
- Knowledge retention: Digital systems preserve organizational safety knowledge even through employee turnover, ensuring consistent application of safety protocols.
By implementing digital safety management tools, your team can transform safety from a compliance obligation into a strategic advantage. These systems not only help prevent workplace injuries but also improve operational efficiency by reducing downtime, lowering workers' compensation costs, and creating a culture where safety becomes an integrated part of daily operations rather than a separate administrative burden.
When selecting a digital safety management solution, prioritize user-friendly interfaces, mobile capabilities, customizable workflows, robust reporting features, and integration potential with existing systems. The right digital platform should adapt to your organization's specific safety needs while scaling to accommodate growth and evolving regulatory requirements.
Safety procedure resources
OSHA provides several resources to help organizations improve their workplace safety. Below are some of their most useful publications and a couple of other noteworthy guides:
- OSHA Recommended Practices for Safety and Health Programs
- OSHA Safety and Health Resources for Small Businesses
- OSHA Other Safety and Health Training Resources
- OSHA Recommended Practices for Safety & Health Programs in Construction
- U.S. Department of Labor Workplace Safety and Health
- The National Institute for Occupational Safety and Health (NIOSH) Small Business Resource Guide
Building a safer workplace
Creating and maintaining a safe workplace requires more than just establishing protocols; it demands ongoing commitment, leadership engagement, and a culture where safety becomes everyone's responsibility. Effective safety programs are never static but evolve through continuous improvement cycles that respond to changing workplace conditions, emerging hazards, and lessons learned from incidents and near-misses.
Organizations that excel in workplace safety recognize that prevention is always more effective than reaction. By implementing risk assessments, clear procedures, thorough training, and regular inspections, your team creates environments where accidents become increasingly rare. Digital tools like MaintainX help teams stay proactive by streamlining safety procedures, automating inspection schedules, and providing real-time visibility into compliance status across facilities.
FAQs on Workplace Safety Procedures
What are safety procedures?
Safety procedures are documented protocols designed to prevent accidents and protect employees from workplace hazards. They include step-by-step instructions for performing tasks safely, guidelines for handling equipment and materials, emergency response plans, and preventive measures to identify and control risks before incidents occur. Effective safety procedures incorporate regulatory requirements, industry best practices, and organization-specific hazards.
What is the Take 5 safety procedure?
The Take 5 safety procedure is a simple five-step risk assessment process that workers perform before starting a task. It encourages employees to: (1) Stop and think about the work to be done, (2) Look for hazards, (3) Assess the risks these hazards present, (4) Control the hazards by implementing safety measures, and (5) Monitor the effectiveness of controls while working. This quick mental checklist helps workers develop situational awareness and proactively identify potential dangers.
What are the 5 steps of safety?
The 5 steps of safety form a comprehensive framework for workplace safety management:
- Identify hazards through workplace inspections, task analysis, and employee feedback.
- Assess risks by evaluating the severity and likelihood of potential harm.
- Control risks using the hierarchy of controls (elimination, substitution, engineering controls, administrative controls, PPE).
- Implement and communicate safety measures through training, procedures, and visual cues.
- Review and update by continuously monitoring effectiveness and making improvements based on performance data and incident investigations.
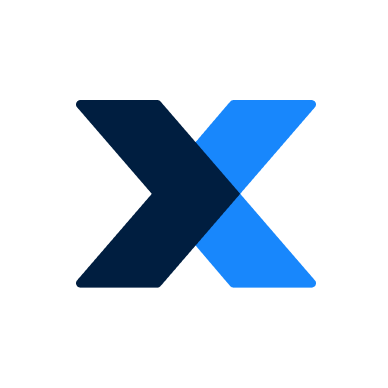
The MaintainX team is made up of maintenance and manufacturing experts. They’re here to share industry knowledge, explain product features, and help workers get more done with MaintainX!