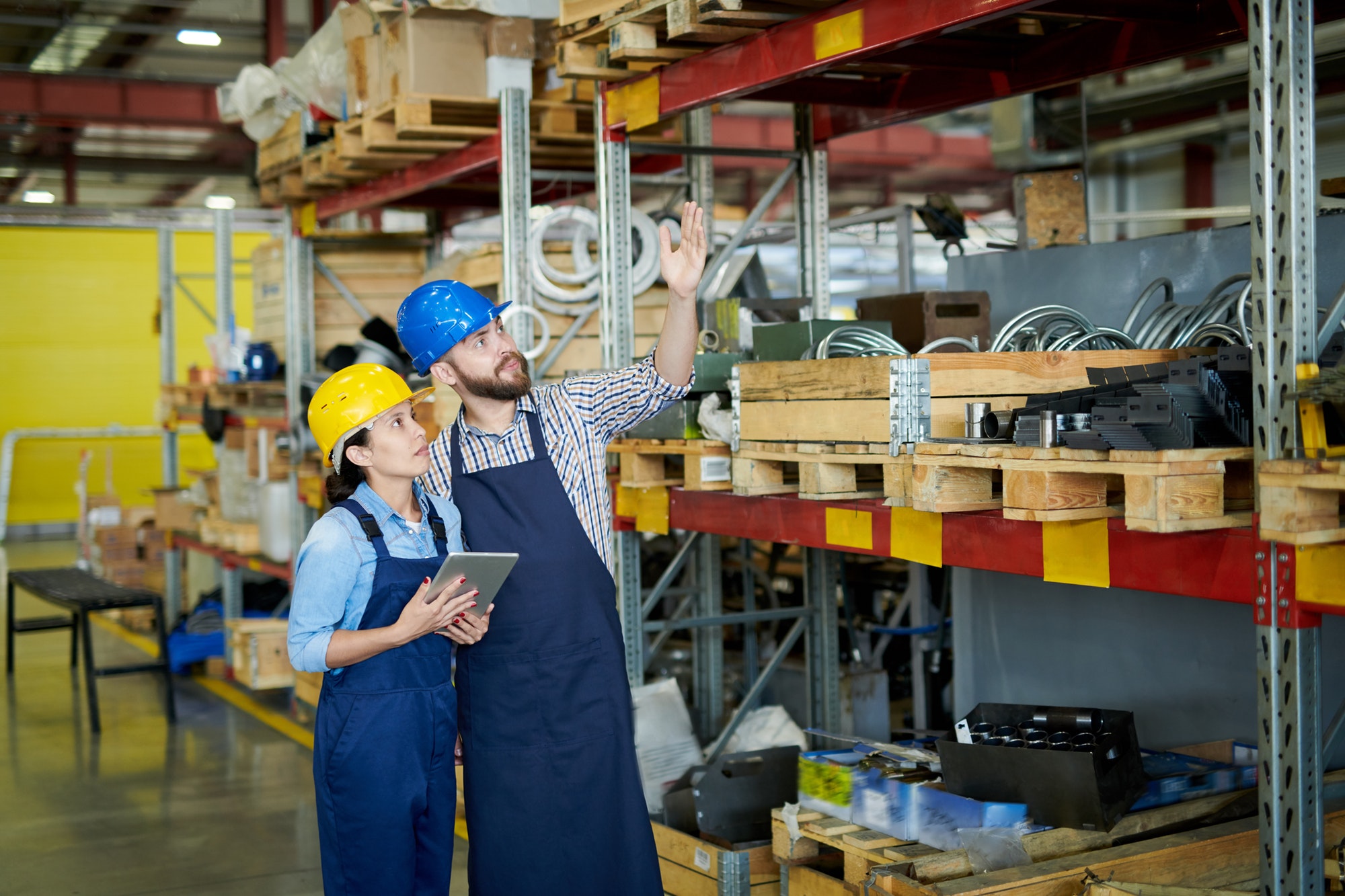
Now more than ever, parts inventory software is a fundamental part of a robust production strategy. First of all, proper parts management is essential for smooth production and meeting customer demand. Whether you’re thinking about raw materials for goods or spare parts for assets, you want to ensure you have everything in stock when needed.
Second, minimizing unplanned downtime will already be a serious enough challenge if an asset breaks down. The last thing you want is to prolong it because the necessary repair tools or parts are unavailable for the maintenance team. To avoid stockouts, you can use inventory management software.
For example, a robust computerized maintenance management system (CMMS) can allow you to trigger purchase orders at particular reorder points.
In addition to this, proper asset management is necessary to ensure cost-effectiveness. While you want to ensure you always have the necessary materials and parts on hand, you don’t want to overstock your items and increase your inventory costs.
Finding the right balance to optimize profitability is at the heart of functional inventory planning. But before we take a closer look at how to build an inventory management system, let’s start by looking at what makes up your inventory.
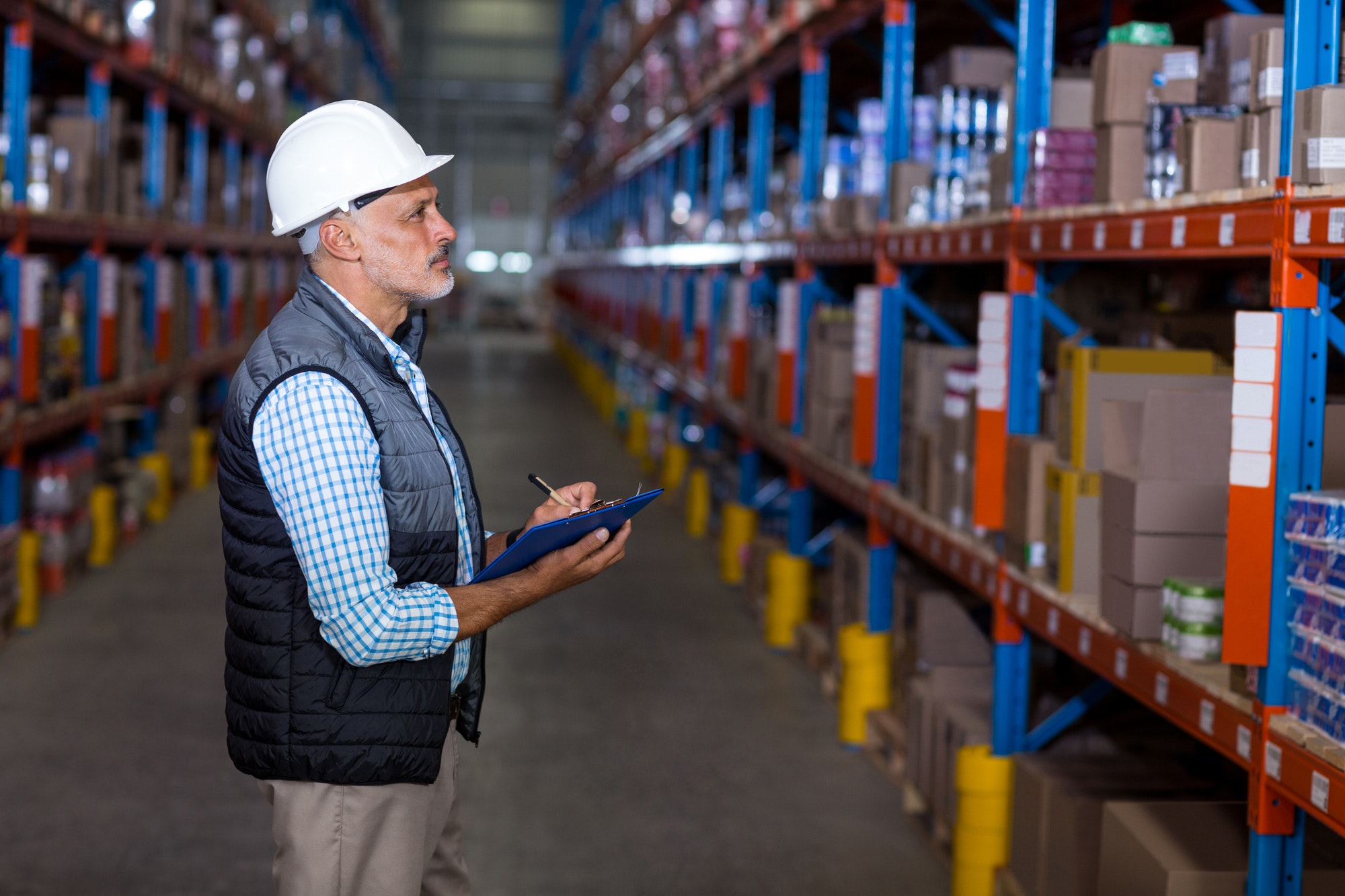
Types of Inventory
Specifically, your inventory will depend on factors unique to your industry and business. However, inventory will broadly fall into one of these categories. Understanding these categories is vital for inventory optimization, with or without software.
- Raw Material: This is the foundation for finished goods. It refers to any material turned into a finished good, whether alone or in parts. Examples include everything from steel welded into machines or tools to cotton processed into clothing.
- Works-in-Progress: You can look at this in two ways: As raw materials that you are turning into finished goods or as goods that you need to finish processing. These could be goods themselves in the middle of processing or parts that complete a finished product—for example, cartons and other forms of packaging for a cooking stove. The packaging is not the actual good sold by the cooking stove manufacturer, but the stove is not complete as a product without the packaging.
- Finished Goods: As the name suggests, goods that have reached the final production and/or assembly stage. They are ready for sale to consumers or wholesalers.
- Overhaul Inventory: These items are not part of the product but are necessary for production. They include parts and other operating assets that take up inventory space, as well as maintenance and repair tools and items. Examples include spare parts, lubricating fluid, and personal protective equipment (PPE) like coveralls.
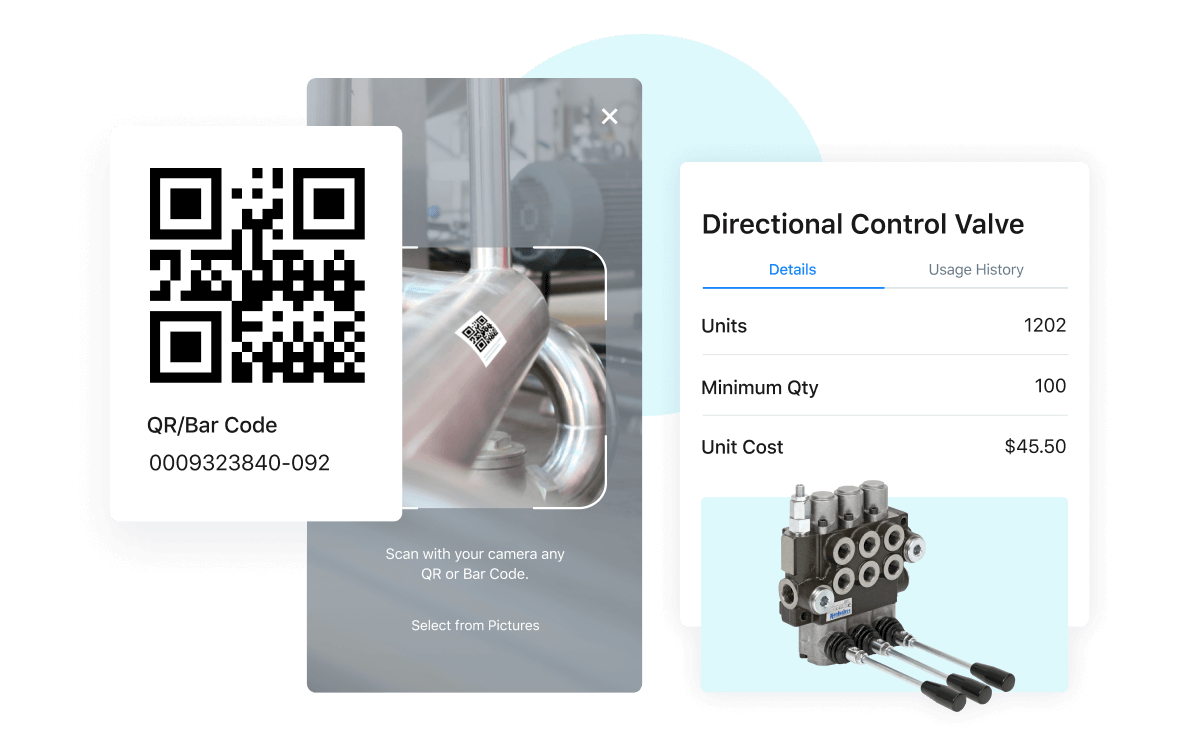
Creating an Inventory Management System
To create a robust inventory system that works for you, consider the following steps:
Organize Your Locations
No matter the size of your inventory, you want to ensure you maintain easy access to the items you need. To ensure this, label your storage locations properly. Use signs, labels, and directional symbols to ensure people know where they are and when to find things. You can also color-code areas for more straightforward navigation.
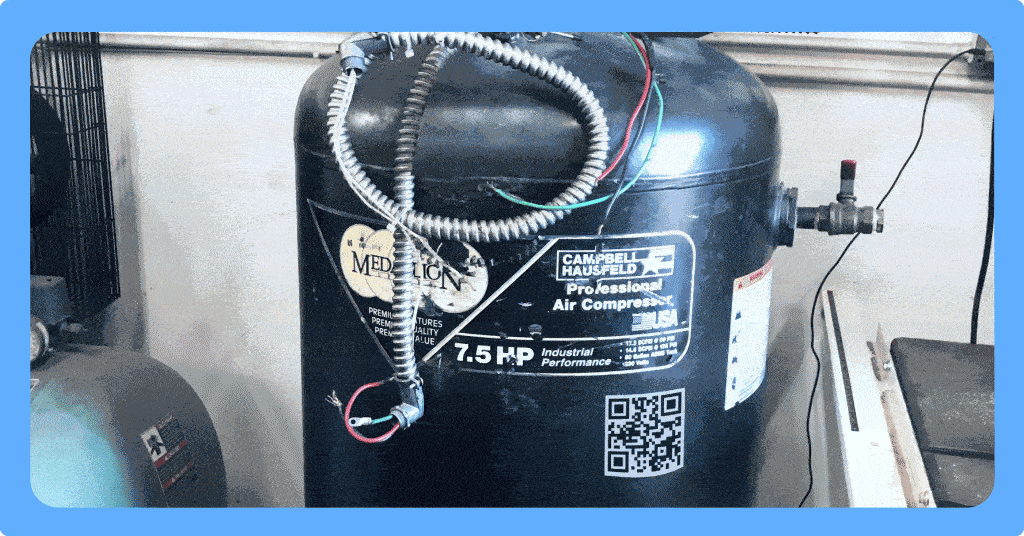
Label Your Products
Make it clear what is in every storage container. Written signs and labels are one way to do this. Alternatively, you can use barcodes, which you can scan for information. This way, you can get information about the inventory items, such as detailed measurements, parts numbers, serial numbers, stock-keeping units (SKUs), etc.
Maintain Proper Records
You can do this via pen-and-paper methods or spreadsheets. Ensure that staff members record every new item they add to inventory. Same for anything taken out. However, it’s much easier to use parts inventory software. You can create barcodes or QR codes that workers scan once items are taken in or out of inventory.
This process ensures you have real-time, up-to-date information about your inventory counts and stock levels. You know when you need to reorder raw materials to avoid rushing during production while avoiding excess inventory.
Your historical data also helps with demand forecasting, so you can simplify your procurement, avoid supply chain issues, and mitigate long lead times and slow order fulfillment by placing orders well in advance.
This approach also applies to spare parts inventory. Software solutions can also help you track parts and identify when you need replacements.
Let’s take a closer look now at what software can do for your inventory control.
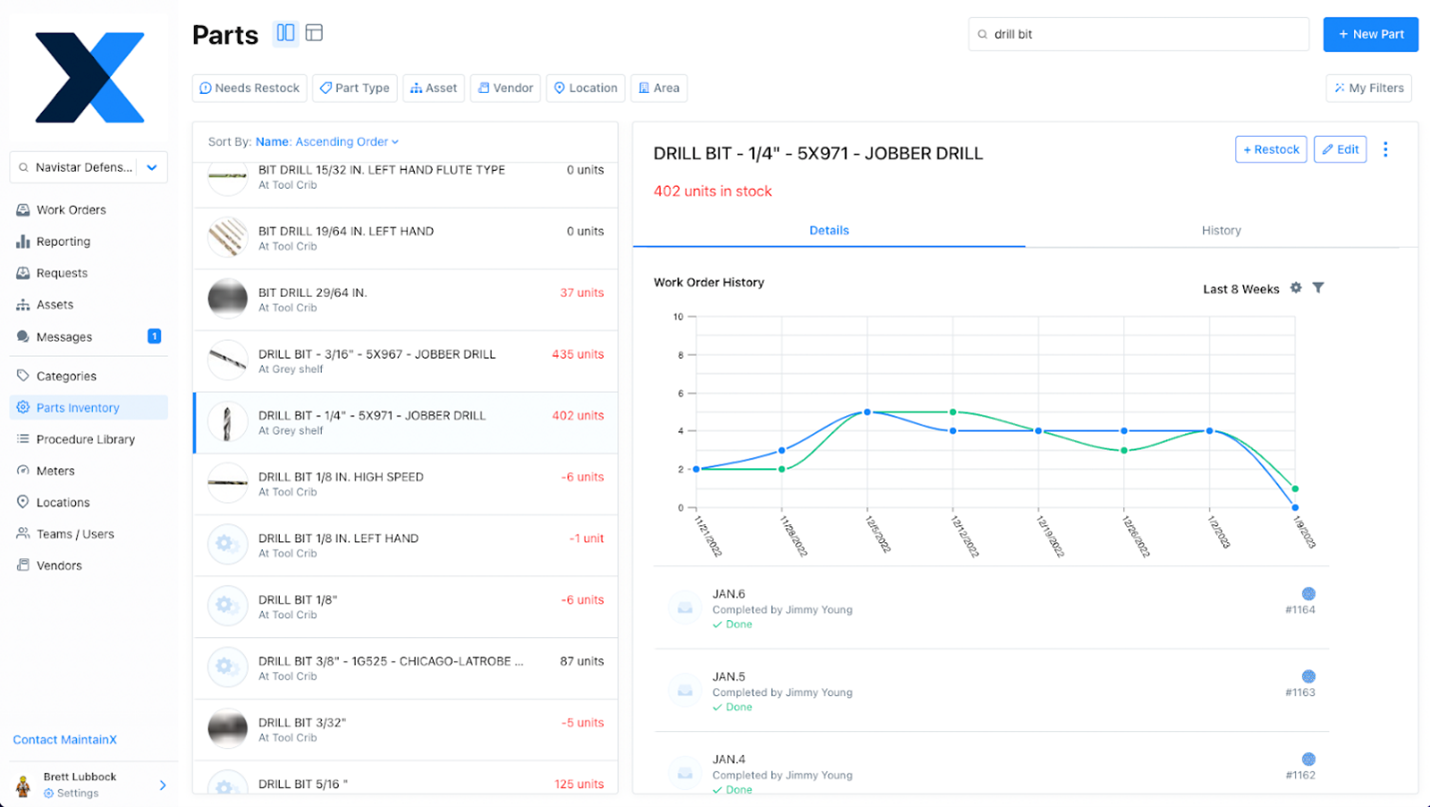
How Can Software Manage Inventory Control?
Helps Facilitate Preventive Maintenance
Preventive maintenance is one of the best ways to ensure good parts management and cost savings. Preventive maintenance will help you avoid unplanned downtime and breakdowns. You can plan for replacement parts because you carry out your maintenance primarily according to a schedule.
You’ll know when to order parts and when inventory levels will likely reduce. A good CMMS can help you automate your preventive maintenance work orders and track your past activities. The software can also help you with predictive maintenance, which functions by forecasting breakdowns. Knowing this lets you ensure you get what you need on time.
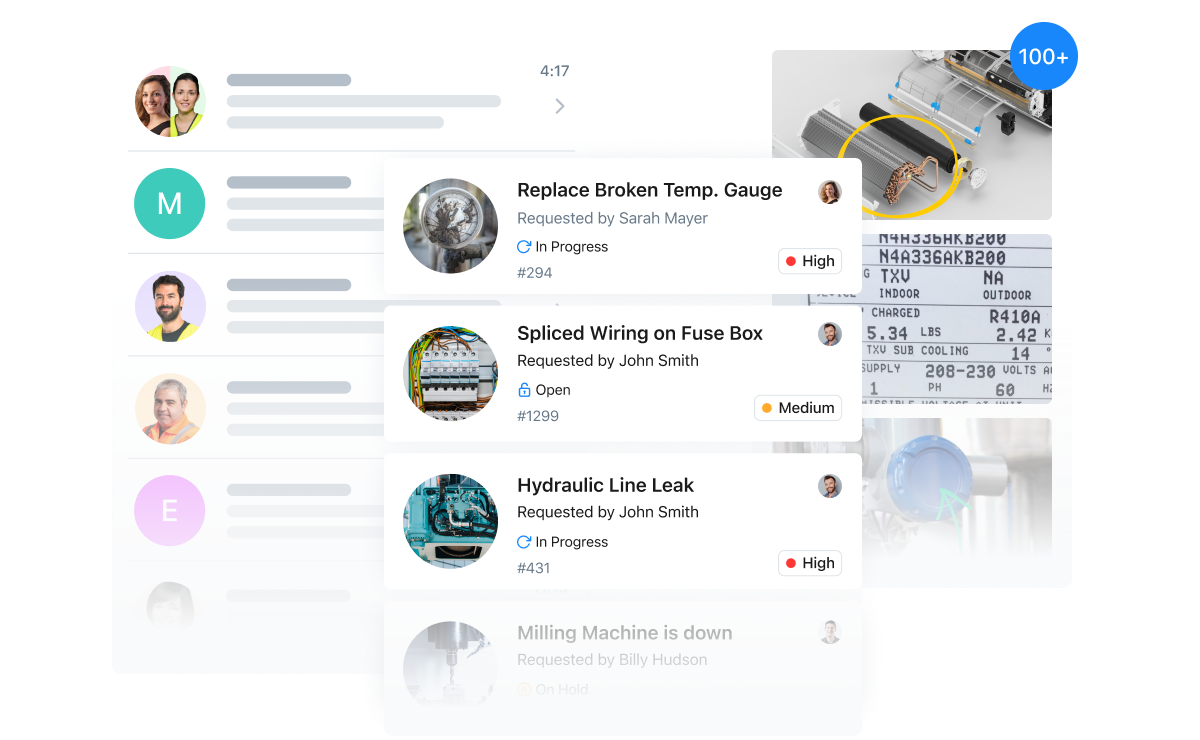
Helps Develop Standard Operating Procedures
Good maintenance software ensures that your workers carry out all maintenance activities according to set rules and guidelines. You can also apply these SOPs to your inventory management system. You can create proper protocols for storing and logging items to ensure your entire facility is on the same page. This system makes it easier to track inventory.
Helps Anticipate Failure
While you can’t eliminate all breakdowns, you can ensure you prepare adequately for them. Good CMMS apps can help you track past performance, analyze specific metrics, and generate valuable insights. For example, if you know that you have low MTTR and MTBF for certain assets, you can deem these assets high risk to ensure you always have the necessary parts for their repairs.
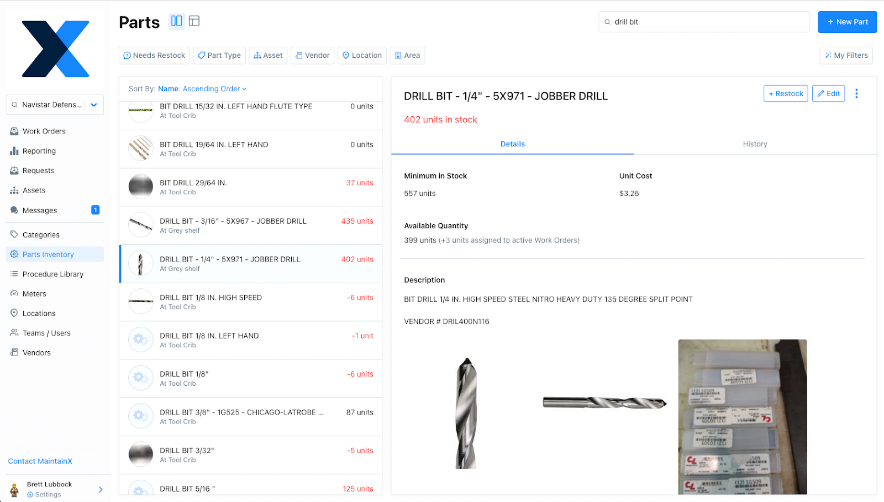
Streamline Your Parts Management Workflow with MaintainX
Ready to take your parts management to the next level? MaintainX CMMS seeks to help you streamline your inventory workflow and optimize your asset management.
As the first work order management software with chat, MaintainX facilitates collaboration by helping your staff stay connected through their mobile devices. MaintainX’s user-friendly web and mobile app provide several parts management features, including:
- Purchase orders module with automated low inventory alerts
- Reporting dashboards with cost-tracking functionality to enable data-driven decision-making
- Cloud-based management system
- Work order automation
- Vendor data management
- Timestamps and digital audit trails
- Barcode scanning
- Asset data management
FAQs
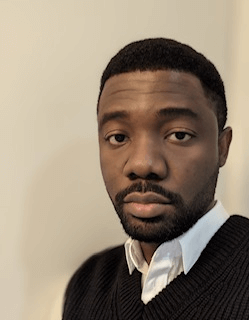
Lekan Olanrewaju is a content writer with years of experience in media and content creation. He has held positions at various media organizations, working with and leading teams at print magazines, digital publications, and television productions.