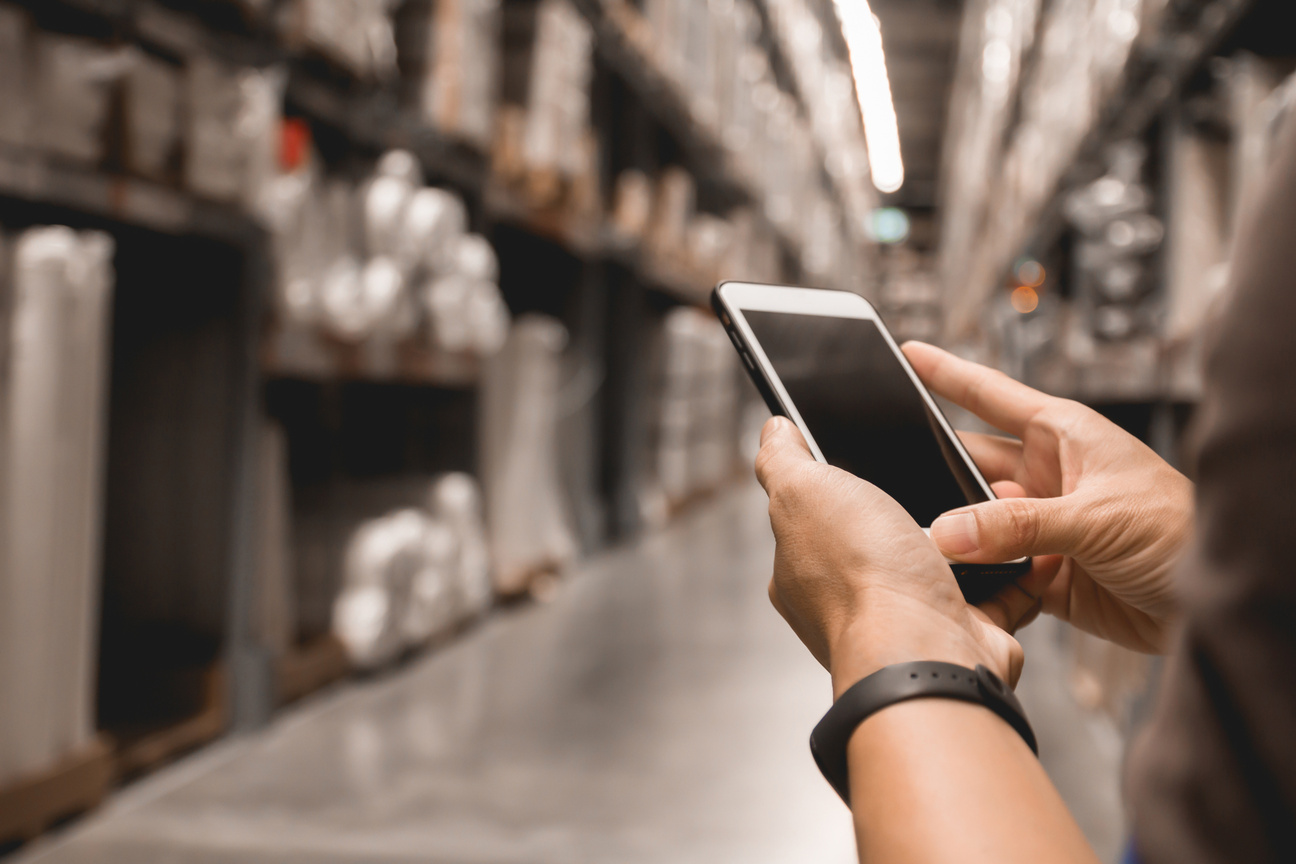
Buying, organizing, and using inventory is something that almost every business deals with. But manufacturing and facilities management companies face additional challenges with parts, supplies, and tools needed daily by maintenance technicians.
Companies with maintenance teams spread far and wide can struggle to keep up with multiple stock locations, allocating parts used for manufacturing products vs. making repairs and coordinating access to the right parts available when maintenance teams are on site.
Optimizing Inventory and Streamlining Operations
One way to streamline this complex workflow is to take advantage of work order management software with robust parts inventory management capabilities.
Instead of battling with siloed inventory and work order management systems that are perpetually out-of-sync, it’s possible to integrate both functions within one platform, ensuring purchasing teams and technicians can always access accurate spare parts inventory in real time.
"Given the current state of global competition, manufacturing industries are almost always on the lookout for an inventory management system that would help curtail costs and reduce time required to supply raw materials and goods to carry out production quickly and efficiently."
e-Prime
What Is Parts Inventory Software?
Inventory software is designed to help organizations easily track parts, maintain an accurate inventory, and manage supplies and tools.
Parts inventory management software typically offers functionality to help businesses stay abreast of inventory counts, inventory costs, stockouts, stock on hand, and reorder requirements.
Some types of software for work orders also incorporate inventory management capabilities. This means that many businesses dealing with work order management and repetitive maintenance and repair tasks can often invest in a single software solution that handles their stock and maintenance requirements.
Using Work Order Software for Parts Inventory
Apps that combine work order management capabilities with an inventory management system are known as a computerized maintenance management system, or CMMS software.
A CMMS solves two problems, providing businesses of all sizes with a cost-effective way to streamline their maintenance and work order management systems.
So what can a CMMS do?
The best work order software and CMMS programs transform Excel spreadsheets, paper-based stock management, and disconnected inventory control processes into a “single source of truth.”
This means you can confidently allocate stock and quote pricing, making tasks easier for maintenance crews and speeding up mean time to repair (MTTR).
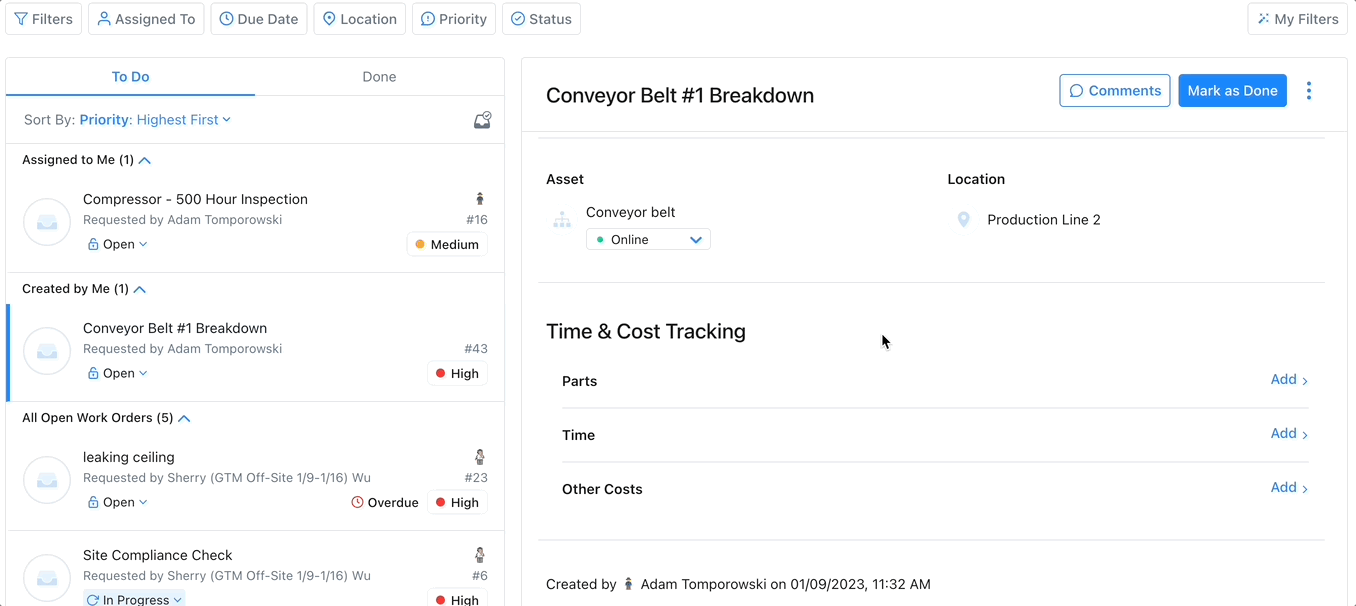
Get Accurate Parts Quantities to Reduce Downtime
Most standalone inventory tracking systems allow you to set min/max quantities. But incorporating this functionality into your works order software creates better organizational transparency.
Technicians can avoid calls to HQ to check stock and, instead, can see directly on their app if the part is available for the job. Purchasing teams can assign a minimum quantity to every part and easily reorder parts in advance to prevent costly downtime costs.
Simplify Purchase Orders
Purchase orders can quickly become complex and unwieldy as your business grows. CMMS or work order software can help you simplify the entire process, including raising, approving, and sending purchase orders to vendors.
Update Work Orders
When parts and maintenance systems are separate, work orders may not be automatically updated if a crucial spare part is delayed. However, integrating these essential functions lets you streamline maintenance management and update work orders in real time.
Linking work orders software directly with your stock levels means you can get critical repairs done faster and avoid unnecessary downtime.
Automate Inventory
Stock reorder points can also be automated so that purchase orders are always raised when inventory levels dip below allocated minimum quantities. Automation frees up your time from time-consuming manual tasks and ensures precision by reducing human error.
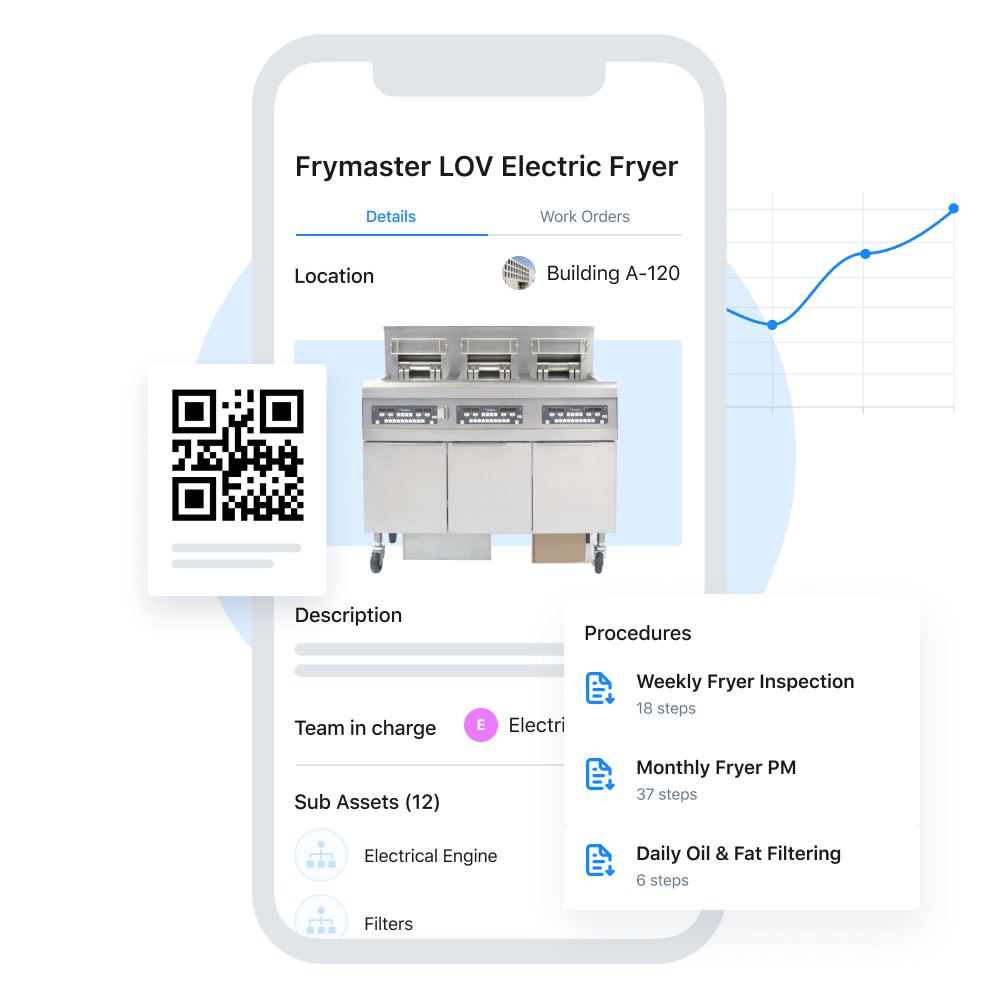
Always Get the Right Part with QR Codes and Barcodes
Each part should have a unique barcode, but technicians often have to guess whether they need part A or B to complete the job. Maintenance work order software can help technicians get their work done faster by using barcode scanning to populate work orders with precise part numbers.
Maintenance technicians will always know the exact parts required to complete the job by creating a bill of materials attached to an individual asset.
Review Usage Reports to Optimize Stock Holdings
First in, first out (FIFO) can be difficult to manage in practice, which is where barcode and serial number tracking can help. A robust work order app can help you minimize obsolete stock by prioritizing older parts and allocating FIFO inventory items to repair requests.
Access Forecasting Tools to Reduce Costs
The best work order programs include practical dashboards, which can help you see historical parts usage and get a real-time snapshot of your current inventory position. This ultimately helps you make confident decisions about which parts to order and when, reducing stockouts and keeping your overall SOH value in check.
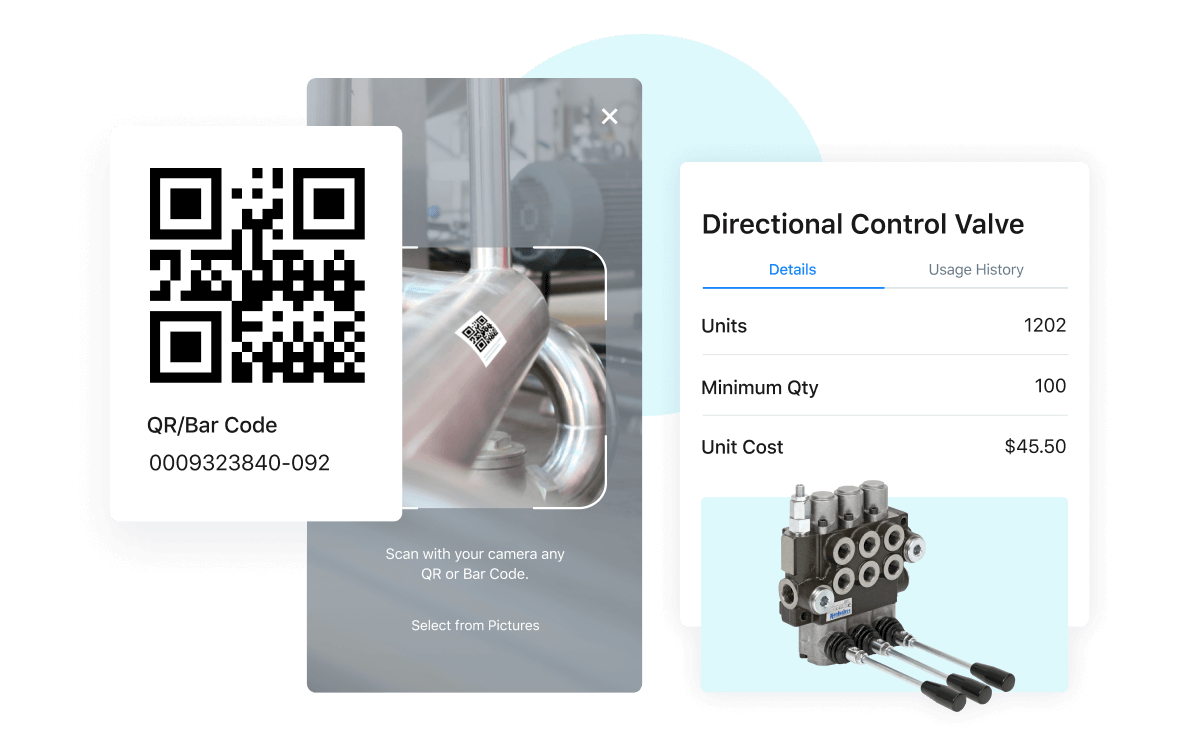
Try MaintainX, the Best Work Order Management Software
MaintainX is free work order software that helps you manage inventory, schedule work orders, handle asset management, and stay on top of preventive maintenance.
Integrations with common ERP systems make it easy to implement a better inventory and maintenance workflow in your organization. And with a user-friendly mobile app, instant messaging functionality, and some of the best reviews in its class, MaintainX can help you automate manual tasks and clarify complex business operations.
FAQs
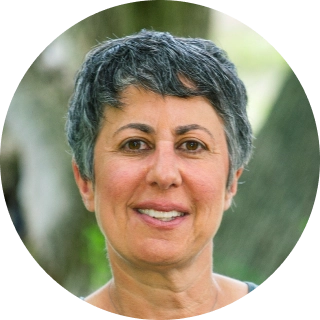
Caroline Eisner is a writer and editor with experience across the profit and nonprofit sectors, government, education, and financial organizations. She has held leadership positions in K16 institutions and has led large-scale digital projects, interactive websites, and a business writing consultancy.