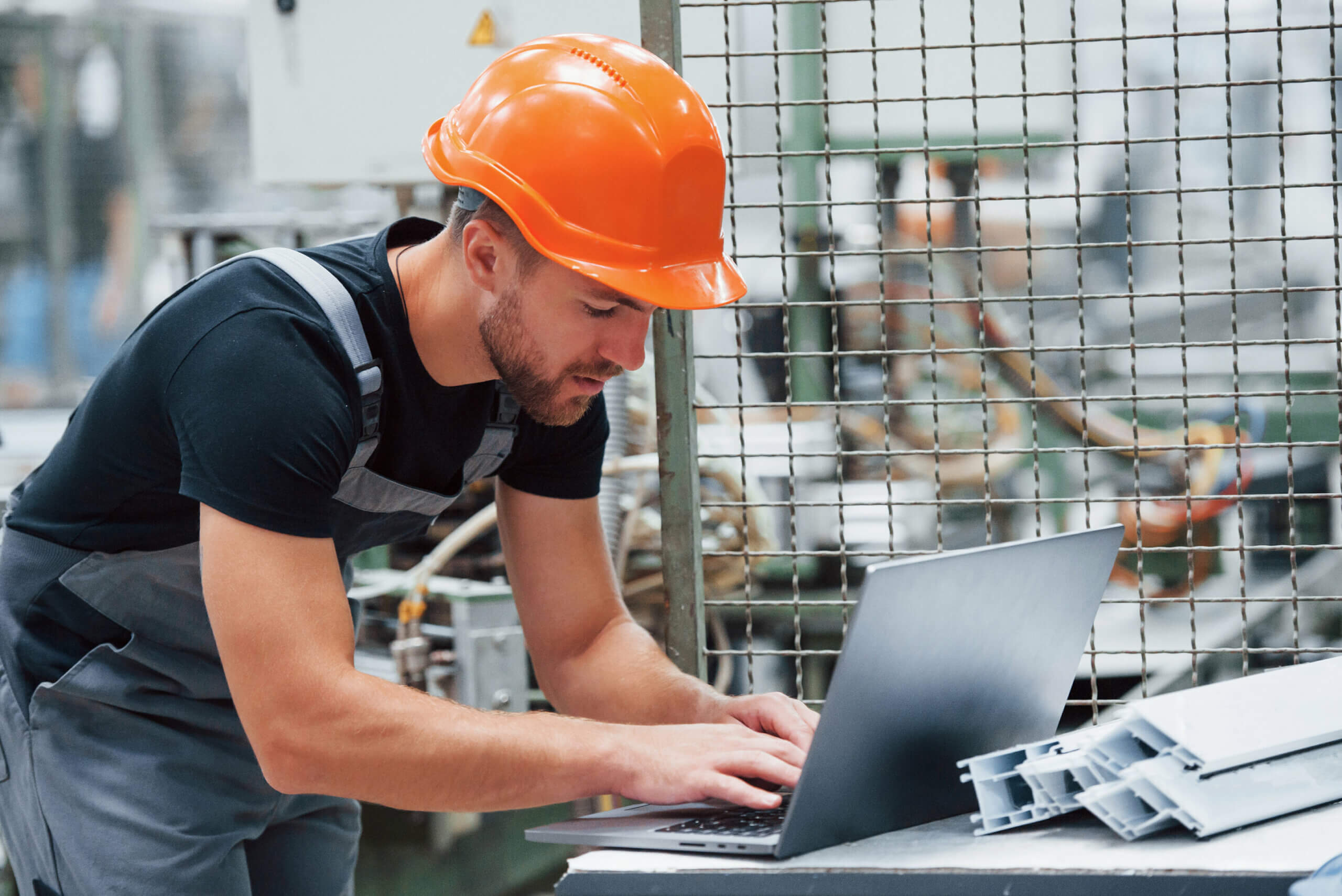
Human error—it’s one of the most common causes of production and quality losses. Well-executed SOPs help complex organizations achieve consistent results across departments regardless of who is working which shift. They also serve to keep employees safe, ensure compliance, and enhance operational efficiency. This article will look at why standard operating procedure programs sometimes fail and how to mitigate such undesirable occurrences.
It’s no surprise that we’re big fans of process standardization at MaintainX. We recently launched an open-source library, which houses hundreds of free SOP templates available for download. MaintainX users can conveniently digitize SOPs with our mobile work order software.
At MaintainX, we recognize that as transformative as process development can be, standard operating procedure implementations don’t always go as planned.
Why Standard Operating Procedure Programs Fail (and How to Fix Them)
This isn’t new information: standardizing your team’s core processes is crucial to consistently meet production goals, maintaining quality control, and keeping costs down. Essentially, SOPs could be the key to unlocking the kind of growth you’ve been striving toward.
So, why is your team still making unnecessary errors? Before we get into some of the surprising reasons why standard operating procedure programs fail, let’s review some indicators of both unsuccessful and successful SOP program launches:
Indicators of SOP Program Setbacks
- Lackluster Adoption: Employees failing to use work instructions is the most obvious indication of program ineffectiveness. There are many potential reasons for poor cooperation when it comes to SOPs, including the points below.
- Inaccessibility: According to Plant Engineering, 39 percent of organizations still rely on paper records. Storing paper records in filing cabinets or even in notebooks presents employees with an unnecessary hurdle. If your team uses multiple systems to create, manage, and store SOPs, it’s time to upgrade to a digital system.
- Inefficient SOP Reviews: Was Jay Leno still hosting the Tonight Show the last time your procedures were updated? If so, you need a faster system for reviewing and revising SOPs. Tedious processes make it easy to procrastinate updating procedures. If you want your SOPs to be successful, it’s crucial to create a step-by-step process for them to succeed.
Organizations should regularly review and update SOPs, or even write new SOPS, for accuracy, cost-effectiveness, and regulatory compliance. Now, let’s look at what you should be experiencing in the next section.
Indicators of SOP Program Success
The benefits of a well-written SOP include:
- Measurability: You have a benchmark for measuring process improvements. Your SOP fulfillment rates and employee feedback shed light on how to become even more efficient.
- Minimized Errors: Employees know exactly what to do, how to do it, and how long each task should take. They rarely make errors because you’ve left no room for confusion.
- Improved Training: New employee onboarding is a breeze. Experienced employees can quickly relay their knowledge to new members of the team.
- Innovation: You find yourself thinking of new ways to innovate, automate, and streamline existing SOPs. Not only did your early process research lead to the discovery of wasted steps, but it also prompted new questions about how to overcome operational challenges.
- Peace of Mind: You feel more relaxed knowing you have eliminated the possibility of workers misinterpreting the execution of processes. In turn, your coworkers feel more confident when fulfilling their assignments.
Again, if you aren’t yet experiencing these benefits, you may have succumbed to common SOP pitfalls. Ineffective SOPs often foster a false sense of security. Managers assume everything is under control because they gave employees a checklist.
However, a closer look can reveal potential issues. Managers often write SOPs that are difficult to understand. It’s also common to come across SOPs that fail to outline all potential work scenarios. But these aren’t the only reasons programs sometimes fail. Keep reading to identify where your organization may have dropped the ball.
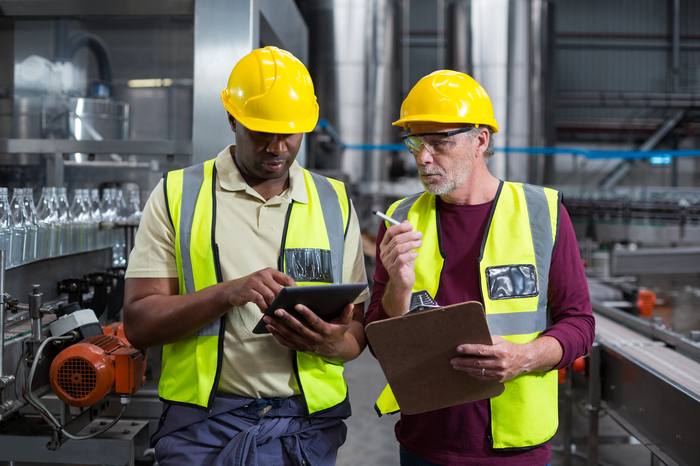
5 Reasons Standard Operating Procedure Programs Fail
1. Fragmented Data
It’s difficult to standardize processes without reliable data. Unfortunately, many organizations fragment data by business function, department, and role.
Informational tidbits kept in separate silos aren’t easily accessible and jeopardize standardization initiatives. Avoid this problem by organizing the data you need before beginning the SOP development process.
2. Developed by Executives/Consultants
Your employees are the ones on the ground day in and day out. For this reason, you should consult them when writing standard operating procedures. Many managers make the mistake of allowing business executives and third-party consultants to direct the SOP development process.
While enlisting non-biased support isn’t a bad idea, don’t allow outsiders to completely run the show. This strategy often leads to lengthy SOP documents filled with unnecessarily advanced vocabulary. Leaders and other stakeholders who aren’t directly involved in procedures are more likely to miss important details. They’re simply too far removed from the daily reality of executing the task at hand!
3. Lack of Purpose
Clear SOPs have five elements: purpose, procedures, scope, responsibilities, and accountability measures. Sometimes, SOPs tend to focus too much on procedures without paying attention to their purpose. The result is a team following the process to solve problems that no longer exist. Regularly review and update your SOPs to purge redundant processes.
4. Poor SOP Formatting
An incorrect SOP format or template can make it difficult to understand or just plain dull. No one wants to read a document that has them yawning within seconds—even if their job depends on it! Common SOP formats include checklists, flowchart formats, hierarchical steps, and use common acronyms.
However, you also can include attached infographics, work instructions, and manuals. Eighty-three percent of human learning.) occurs visually. For this reason, we recommend making your forms as attractive as possible. Add a table of contents, bulleted lists, and flowcharts to increase clarity. MaintainX’s digital checklists are simple, colorful, and feature-rich.
5. Negative Tone
SOPs should be clear, concise, and easy to follow. Additionally, they should direct employees on what they are expected to do—not about what you don’t want them to do. For example, instead of writing “don’t run,” you should write “walk slowly.” SOPs that use negative language can be off-putting.
Read “How to Write Work Instructions That Are Easy to Follow” to learn more about best writing practices.

How to Fix Your SOPs
Don’t worry—you don’t have to throw your SOPs out and start over! Make the following tweaks, and you will be back on track in no time:
- Acquire Employee Feedback: Let someone outside of your original development team review your documents to provide feedback. They can point out any oversights you may have made or steps that are confusing to comprehend.
- Review The Five Elements: Review your SOPs for purpose, scope, procedures, responsibilities, and accountability metrics. Ask yourself: what problem are we trying to solve, and why is this process necessary? Restructure steps as needed. Remember, new hires need to understand the routine tasks in order to save time and not get lost in the weeds. Use simple steps to break down more complex tasks.
- Conduct a Trial Run: Put yourself in your employee’s shoes. Execute the procedures to determine if the step-by-step instructions are practical in real-life situations. Trial runs also eliminate miscommunication by making sure those doing the work understand the procedure. Troubleshooting the accuracy of specific steps provides a level of quality management that both your new hires and experienced techs will appreciate.
- Automate with MaintainX: Download our mobile-friendly software to use our free SOP templates. Our Global Procedure Library includes hundreds of high-quality SOPs for safety inspections, quality control, and other specific tasks for major industries. Not to mention, the MaintainX reporting feature provides real-time data on how effective standard operating procedures increase uptime and decrease downtime.
We hope this guide has provided you with ideas to strengthen your SOP program. Ready to experience greater quality assurance, safety compliance, and operational efficiency? Your project management team will thank you!
Ready for a MaintainX tour? Why not? MaintainX is free!
FAQs
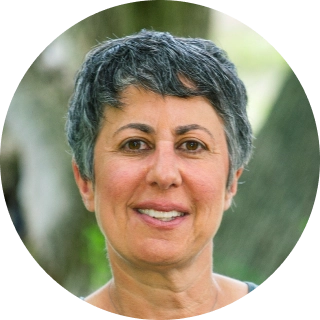
Caroline Eisner is a writer and editor with experience across the profit and nonprofit sectors, government, education, and financial organizations. She has held leadership positions in K16 institutions and has led large-scale digital projects, interactive websites, and a business writing consultancy.