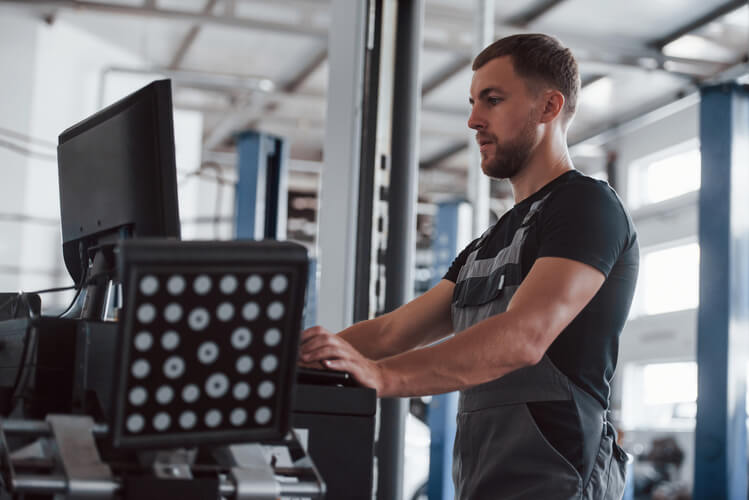
At MaintainX, we often write about the power of digitizing work orders and standard operating procedures. Here, we will review best practices for writing maintenance procedures for maximum efficiency and effectiveness.
Writing Maintenance Procedures
Although the terms “work order” and “procedures” are often used interchangeably, they are not the same. In general, a work order includes the procedure necessary to complete the work order. A procedure, though, isn’t always a work order. Below we outline how to write maintenance procedures for maximum maintenance efficiency.
For example, a work order may be titled “Change lightbulb” and include who is assigning the work order, who is completing the work order, and the location of the lightbulb to be changed. However, the procedure in the work order will explain in simple step-by-step instructions HOW to change the lightbulb.
In this case, we don’t need specific step-by-step work instructions to change a lightbulb. But, we do need detailed and carefully written instructions for other maintenance tasks. In other words, the work order includes the administrative and necessary information and the procedural and technical information for exactly how to get the maintenance work done.
Maintenance Procedure Essentials
Detailed and carefully written procedure steps are essential to:
- Protecting the health and safety of your employees, including listing the personal protective equipment (PPE) necessary to carry out the standard maintenance procedure
- Ensuring that everyone performs the routine maintenance procedure as required
- Making it easier for standards and regulations to be followed
- Increasing asset and equipment reliability
- Training new employees
- Providing accident investigation information
- Making sure process safety rules are followed.
And, remember, poorly written procedures are generally less effective, can be unsafe, and can cause equipment downtime. They can also affect an organization’s profitability.
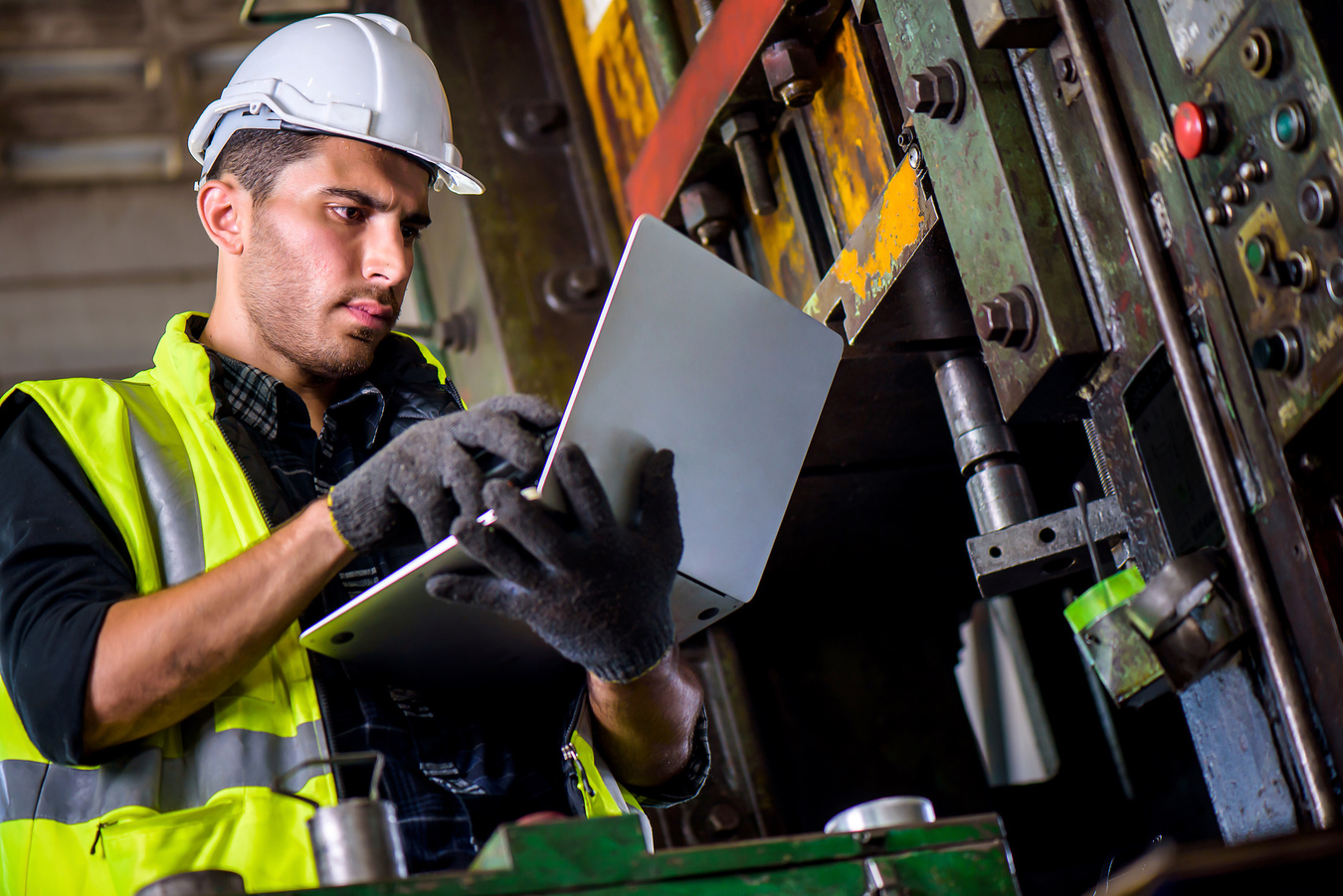
There is no one formula for writing the perfect procedure. Just like there is no one procedure, team member, maintenance team, or management plan that will prevent asset breakdowns all the time. However, as we’ve written elsewhere, there are best practices. We recommend following a PDCA (Plan, Do, Check, and Act) workflow or process flowchart format to write a standard procedure. The process relies on teamwork to ensure that no substeps or safety warnings are left out.
Plan, Do, Check, and Act
Likewise, by troubleshooting how the SOP is written, the PDCA cycle makes sure that, in real time, new hires and even team members with prior knowledge and know-how can follow the docs to ensure both quality assurance and quality control.
To start the PDCA workflow, the employee who knows and regularly performs a specific procedure should be the one to plan, develop, and write the first draft of that procedure. We call this person the “subject-matter expert” (SME), the one most familiar with the procedure. Likewise, that employee should be familiar with any safety, environmental, and regulatory cautions and guidelines.
The same employee who writes the procedure should then work through (do) the procedure as written to make any necessary changes. The writer also will clarify the text and add graphics to increase clarity and ensure compliance.
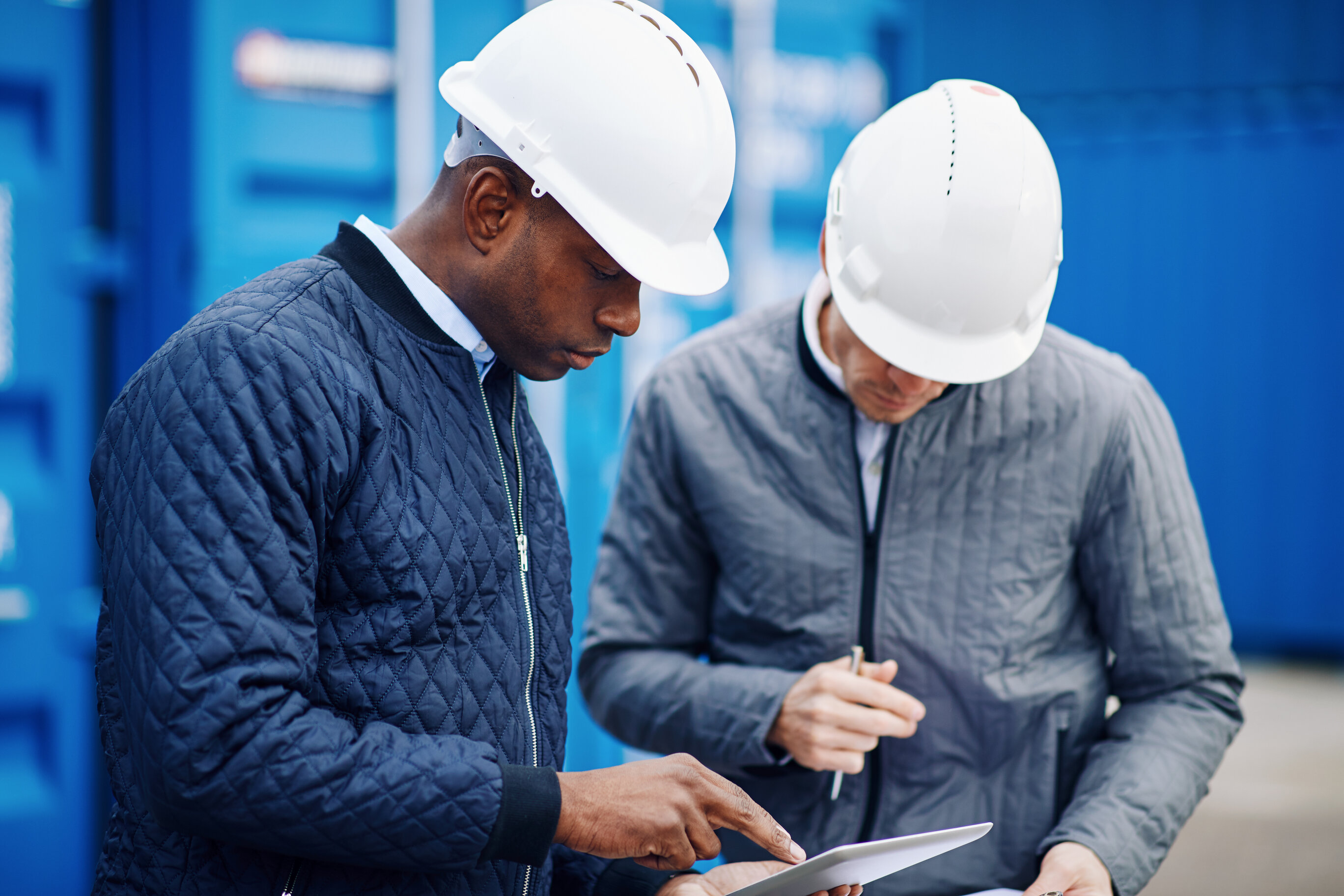
Once clear, the procedure is bumped up to other employees and managers who are familiar with the procedure. As they work through the procedure, they check to ensure it includes all the steps and details and is easy to follow. Again, this step can include adding additional steps to break down specific tasks into smaller pieces and add more graphics for clarity.
When the procedure is in final draft form, an equipment or process manager should follow the procedure. Again, as with the other steps, additional changes to increase clarity should be made now.
After this quality-control review, finalize any necessary changes. Then, if necessary, run the procedure through your company’s approval process identified in company policy. Also, check to make sure the procedure adheres to any industry and governmental guidelines.
At this point, the procedure is ready to be added to the workflow. Employees can now act on it and report back when the procedure is complete.
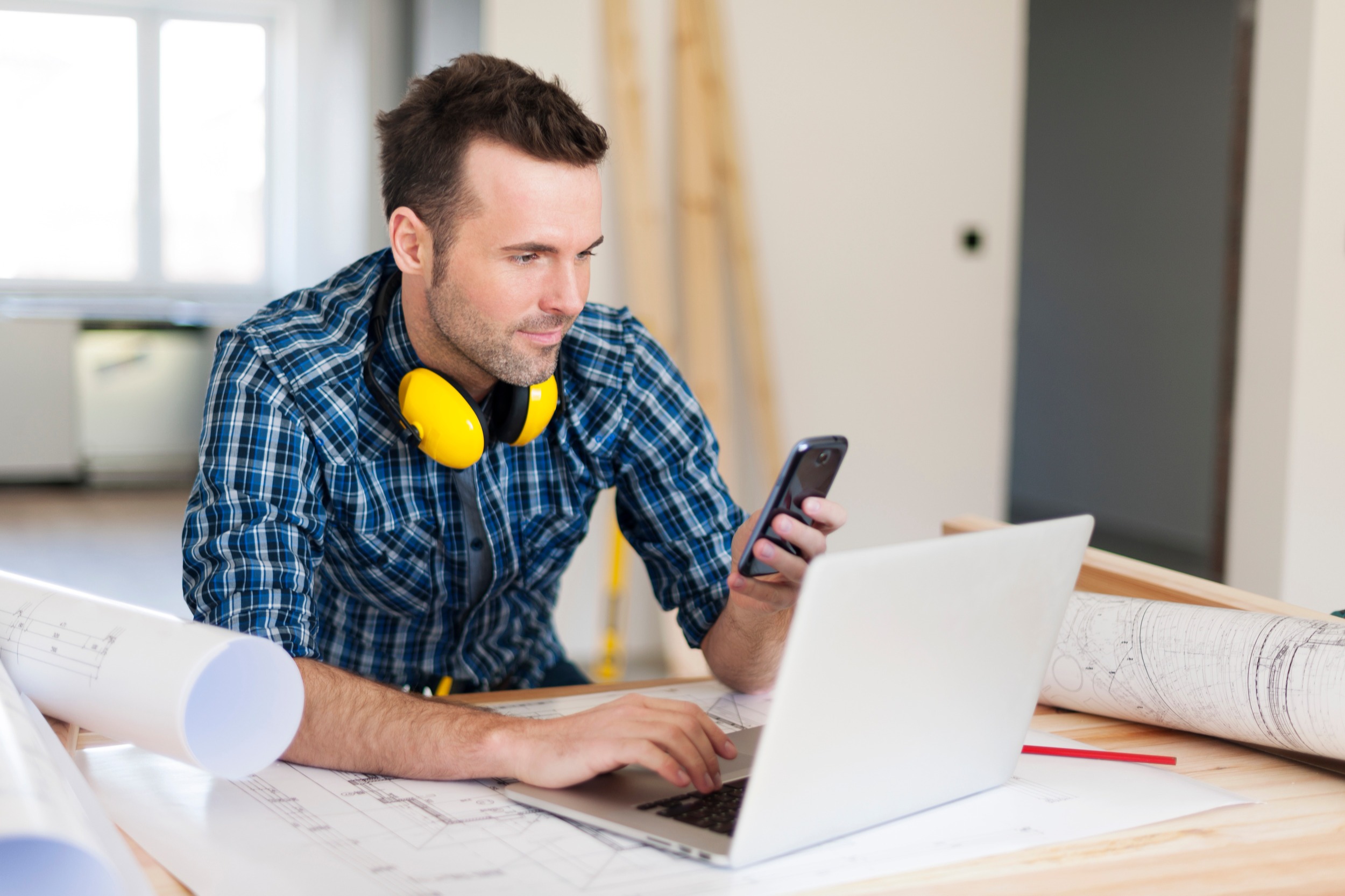
Writing Down Procedures
We recommend that you name procedures so that employees can figure out the procedure based on the name you give it. We also recommend that your procedure naming conventions work as your company grows and can be scaled up as needed.
Therefore, create and organize procedures knowing that you will be adding and revising procedures in the future. Make sure that any system you devise now can be scaled up as your organization grows. For example, a predictive maintenance (PdM) or preventive maintenance (PM) procedure on a conveyor belt will be different than a reactive maintenance (RM) procedure on a conveyor belt. Using this logic, a PM procedure on a conveyor belt may be named PMConveyor.
Likewise, the RM procedure may be named RMConveyor, knowing that steps regarding safety may be different depending on how and why the conveyor needs reactive and/or emergency maintenance. Also, ensure that the procedure name defines the categories you want grouped together. Computerized maintenance management systems (CMMS), like MaintainX, sort records by name. For example, preventive maintenance procedures for conveyors will begin with PMCON02. Here, the PM denotes preventive maintenance, and CON02 is conveyor #2, which you named according to your asset naming conventions.
If you want the asset name to be listed first, rather than the maintenance plan or maintenance program, label the procedure CON02PM.
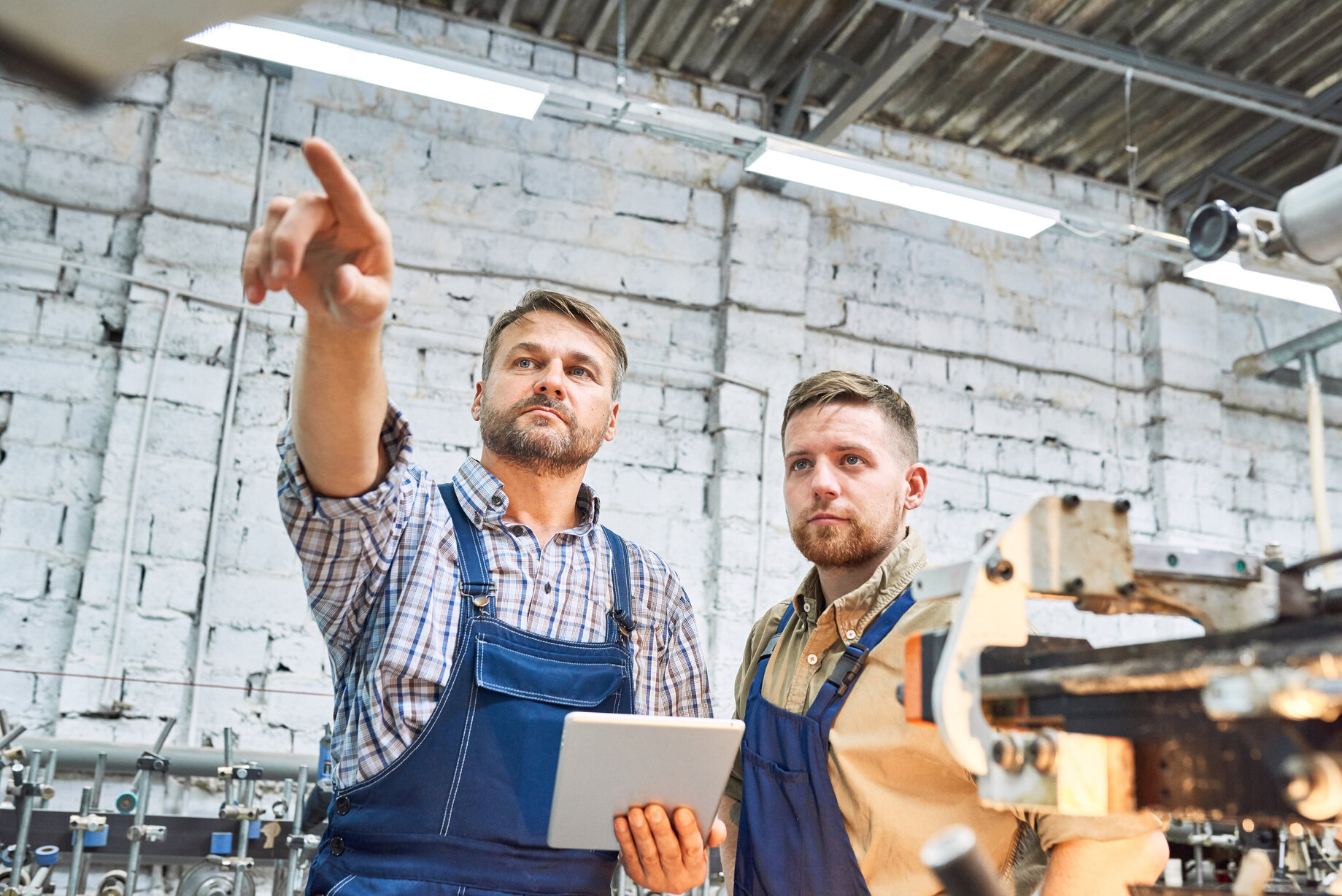
Naming Procedures
The following asset-naming conventions also apply to naming procedures:
- In the number portion, leave enough room for future expansion.
- Include “gaps” in your identification method so that you can easily insert new records or record groups in the future.
- Create an identification method that is meaningful, easy to use, and easy to remember.
- Use consistent terminology, especially with abbreviations and acronyms. For example, consistently use either “BLDG” or “BUILD” as an abbreviation for BUILDING so that a query or search finds all occurrences of “building.”
- Don’t only use numbers. Numbers are not easily remembered, especially those that may change based on a manufacturer’s part number.
Creating Procedures
Essential elements to creating standard maintenance procedures in a CMMS include:
- Carefully lay out the precise hierarchical steps in the correct order with the right level of detail and
- Purposefully select how the maintenance staff member or technician indicates that each step has been performed correctly.
The Precise Steps in Maintenance Procedures
In addition to writing SOPs as clearly and logically as possible, use the following tips to ensure clarity and to take the decision-making process out of it:
- Use headers to separate different stages of the procedure. For ex., “Turn the Compressor Off” and then follow with the steps to turn the compressor off.
- Use a parallel structure for each instruction.For ex., “Press stop. Check pressure. Record temperature.”
- Start each sentence with a verb using active voice.For ex., “Press stop” instead of “You should press stop.”For ex., “Turn the valve to the left” instead of “The valve goes to the left.”
- Write each step as a separate instruction.
- Start each instruction with the verb unless you need to tell the technician where to begin.For ex., “From the right side of the conveyor, turn the belt clockwise.”
- Use a period at the end of each step.
The Technician’s Response in Maintenance Procedures
Select the way in which the technician indicates that each step has been performed correctly.
For example, say the procedure is to turn on the light. John the technician will be asked to indicate he performed the action by checking the box next to the instruction. A simple checked box will indicate he turned on the light. In other words, a checklist for this type of procedure may be more effective than a short answer response.
The instruction would not, in other words, ask John to fill in a numerical value in response to his following the instruction to turn on the light.
In MaintainX, procedures include a “field” for the technician to indicate the instruction has been carried out. Select the field type that best fits the expected response to the steps in your procedure. If the technician attempts to input the wrong type of response in a field, say a number, when text is required, MaintainX will reject the input.
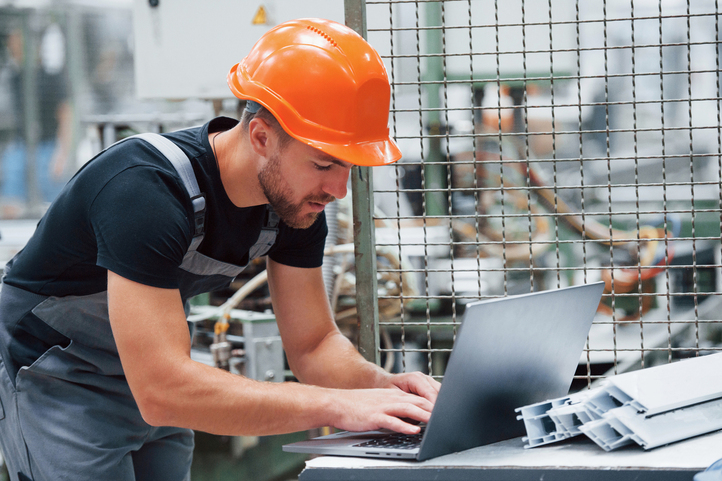
Check out these other posts on writing high-quality standard operating procedures:
Writing Standard Operating Procedures to Reduce Downtime
Standard operating procedures are detailed instructions that detail routine, work-related tasks. Businesses of all types use written SOPs for many reasons, including maintaining stakeholder satisfaction, increasing efficiency, onboarding new employees, and decreasing downtime costs.
Are Manufacturing Standard Operating Procedures Really That Important? (Yes!)
Strategic SOP programs bolster equipment maintenance, quality assurance, maintenance management systems, and supply-chain stability. Repeatable processes can always be made more efficient with effective SOPs.
The Beginner’s Guide to Standard Operating Procedures — SOPs (SOP Templates Included)
In this guide, you will learn how to organize fundamental and routine tasks into step-by-step processes that are easy to follow. With the help of a standard procedure template, you also will learn about different SOP formats and SOP documents, how to write new SOPs, and how to enhance compliance with digitization.
FAQs
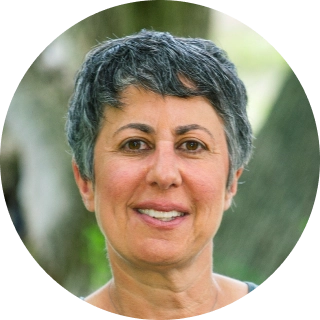
Caroline Eisner is a writer and editor with experience across the profit and nonprofit sectors, government, education, and financial organizations. She has held leadership positions in K16 institutions and has led large-scale digital projects, interactive websites, and a business writing consultancy.