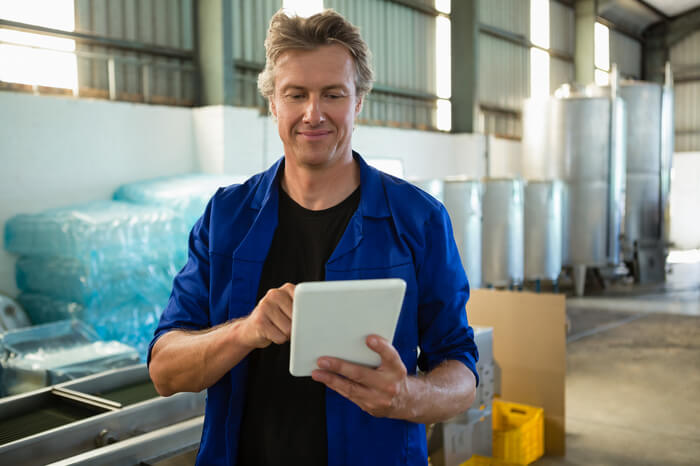
Standard operating procedures (SOPs) are documented, step-by-step instructions for completing assigned processes. They help to improve workflow efficiency, ensure consistency in production and performance, and enhance regulatory compliance. Developing standard operating procedures makes it easier for employees to perform routine tasks without errors.
Consistency is the hallmark of longevity.
Companies known for continually releasing high-quality deliverables have one thing in common: they don’t reinvent the wheel every Monday morning!
Regardless of industry, effective leaders break routine procedures into repeatable steps that are easy to follow. Work instructions are used in manufacturing, warehouses, property management, government institutions, hospitality, and fleet management.
Whether attempting to sell the world’s tangiest loaves of sourdough bread or recycle 5K tons of non-ferrous metals every day, standard operating procedures (SOP) help busy teams consistently meet consumer demand and company standards with minimal errors.
Of course, the larger a company grows, the more difficult it becomes to maintain consistency without sacrificing quality control, operational efficiency, and worker safety. During pivotal points of growth, operational managers often revisit SOPs to ensure accuracy, scalability, and effectiveness.
This article will highlight our best tips for documenting standard operating procedures that actually get used. We’ll also share how to potentially save 10 to 30 management hours a week by digitally creating, assigning, and monitoring your SOPs.
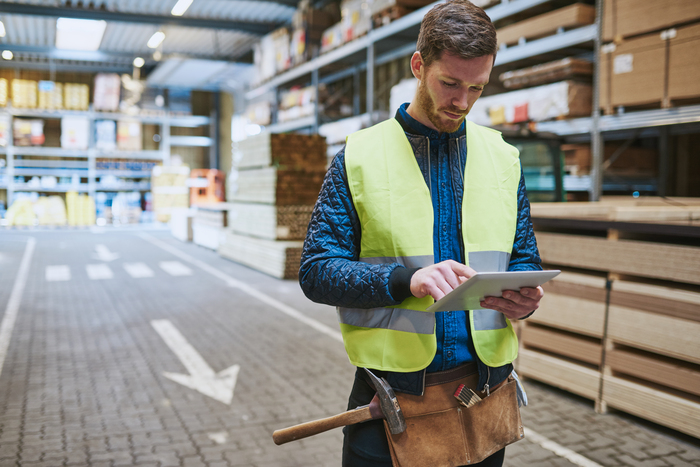
8 Tips for Developing Standard Operating Procedures
Implementing effective standard operating procedures seems pretty straightforward, doesn’t it? Though simple in practice, the exercise has proven itself difficult to apply for many businesses. Why do SOPs fail to deliver their intended results?
Management sometimes overlooks critical steps involved in executing routine tasks. It also often fails to distribute standard operating procedures documents in an employee-friendly manner and create a structurally sound program review process. Without further ado, let’s look at how to develop effective SOPs that support your business needs.
1. Use SOP Templates
The number of new SOPs you need will depend on your organization’s size, industry, and scope of operations. Consequently, you could, potentially, find yourself responsible for managing hundreds if not thousands of SOPs!
With this in mind, adapting user-friendly templates provides an excellent starting point SOP template is a document used to lay out, organize, and describe specific tasks. Industry-vetted templates will save you time, energy, and unnecessary formatting battles.
Of course, there is no definitive way to organize procedural documentation—SOP checklists, hierarchical lists, and process workflows are common. Choose which format best conveys how to complete the task at hand. Commonly included template elements are listed below:
Elements of SOP Templates
- Title
- Table of Contents
- Scope
- Overview
- Necessary Tools
- Procedural Steps
- Attached Manuals
- Target department
- Accountability Measures
Here’s an example of what a standard SOP template looks like:
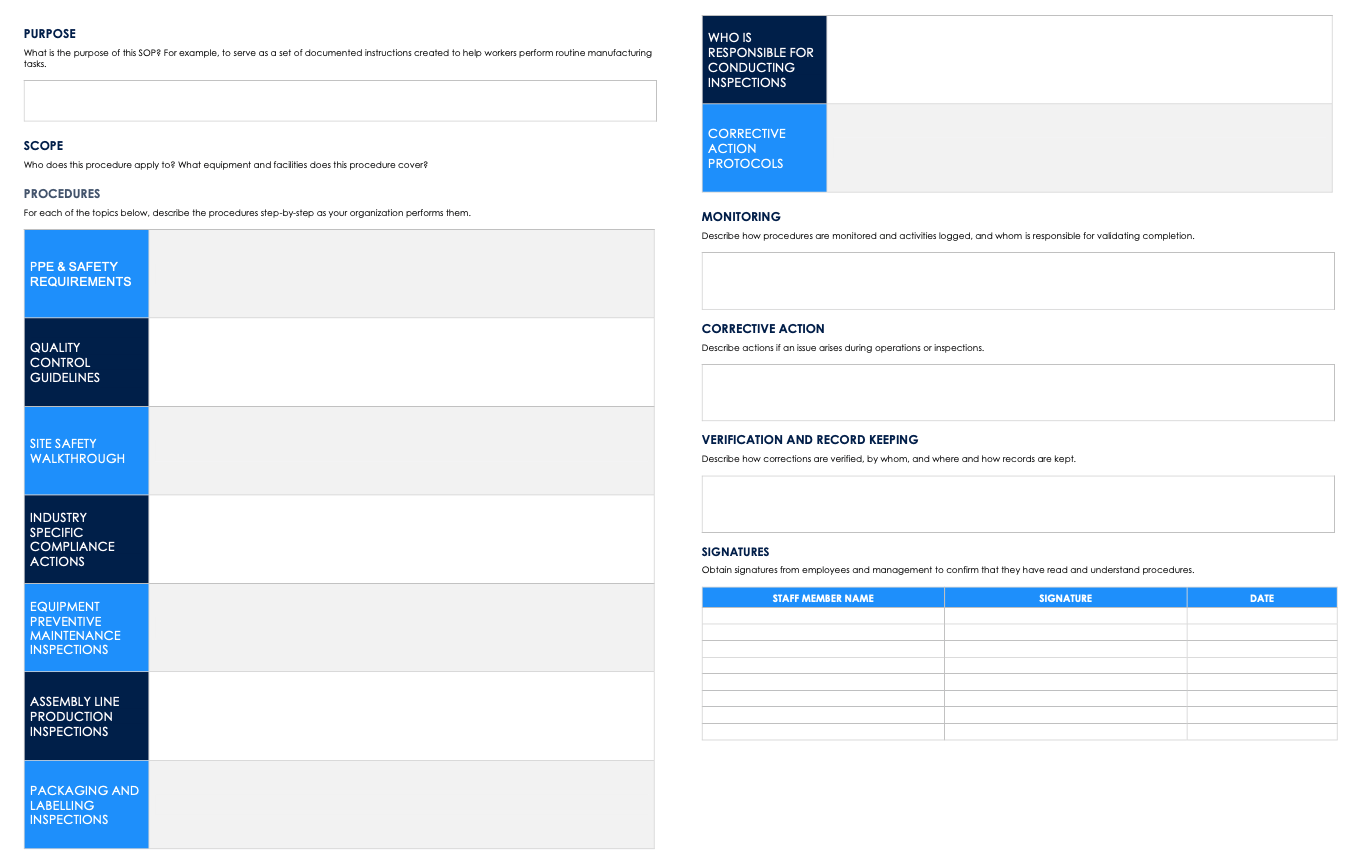
Instead of formatting outlines from scratch and racking your brain to recall unending, minute details, why not stand on the shoulders of those who came before you?
Several online SOP repositories are available, providing templates sourced by O&M managers. MaintainX’s Global Procedure Library contains hundreds of free templates spanning nearly every industry.
MaintainX’s library houses expertly sourced SOPs for safety audits, routine inspections, and maintenance processes. We even have several commonly referenced industrial equipment manuals available for free download.
Click here to download the above standard operating procedure template for free.
2. Write SOPs to Reduce Waste
According to Taiichi Ohno, the world-renowned Toyota manager who inspired O&M’s Lean Six Sigma methodology, the primary goal of developing hierarchical SOPs is to eliminate waste.
Ohno identified seven specific types of operational waste that impede efficient resource utilization. Before you begin writing standard operating procedures, think about how your organization can eliminate these common types of waste:
World-class managers don’t just document SOPs, they consistently look for new ways to eliminate these common types of waste. For example, a plant manager may realize his workers waste 30 minutes walking across the facility each time a forklift needs a battery change. The solution is to store the batteries in a closer location.
This is just one small example of how managers can benefit from proactively looking for opportunities to eliminate waste before enforcing standardization.
Effective SOPs increase productivity, enhance job satisfaction among employees, and maximize efficiency!
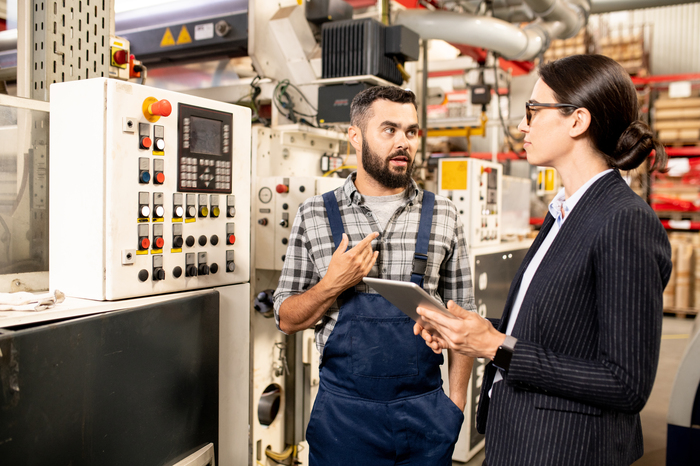
3. Gather Employee Input
According to the Harvard Business School, involving team members in decision-making processes often leads to better business outcomes. Ask your employees how the routine tasks they are responsible for handling should be performed.
In a McKinsey Quarterly survey of 2,207 executives, “only 28 percent said that the quality of strategic decisions in their companies was generally good, 60 percent thought that bad decisions were about as frequent as good ones, and the remaining 12 percent thought good decisions were altogether infrequent.”
After speaking with the individuals directly involved, you may be surprised to learn certain tasks involve more or fewer steps than you had anticipated. Such instances could go one of two ways: the employees could have developed more efficient ways to execute procedures on their own or missing essential hierarchical steps necessary for quality control, cost control, and stakeholder safety.
Once your initial SOP draft is completed, consult the same team members to identify any missing or complicated steps. Afterward, perform a final review for quality assurance. Besides obtaining first-hand information on how tasks are actually performed, involving team members may boost morale.
Included employees often possess a stronger sense of ownership over their assigned tasks. According to analytics and advisory firm Gallup, engaged employees yield significantly better outcomes, stay at organizations longer, and experience less burn-out.
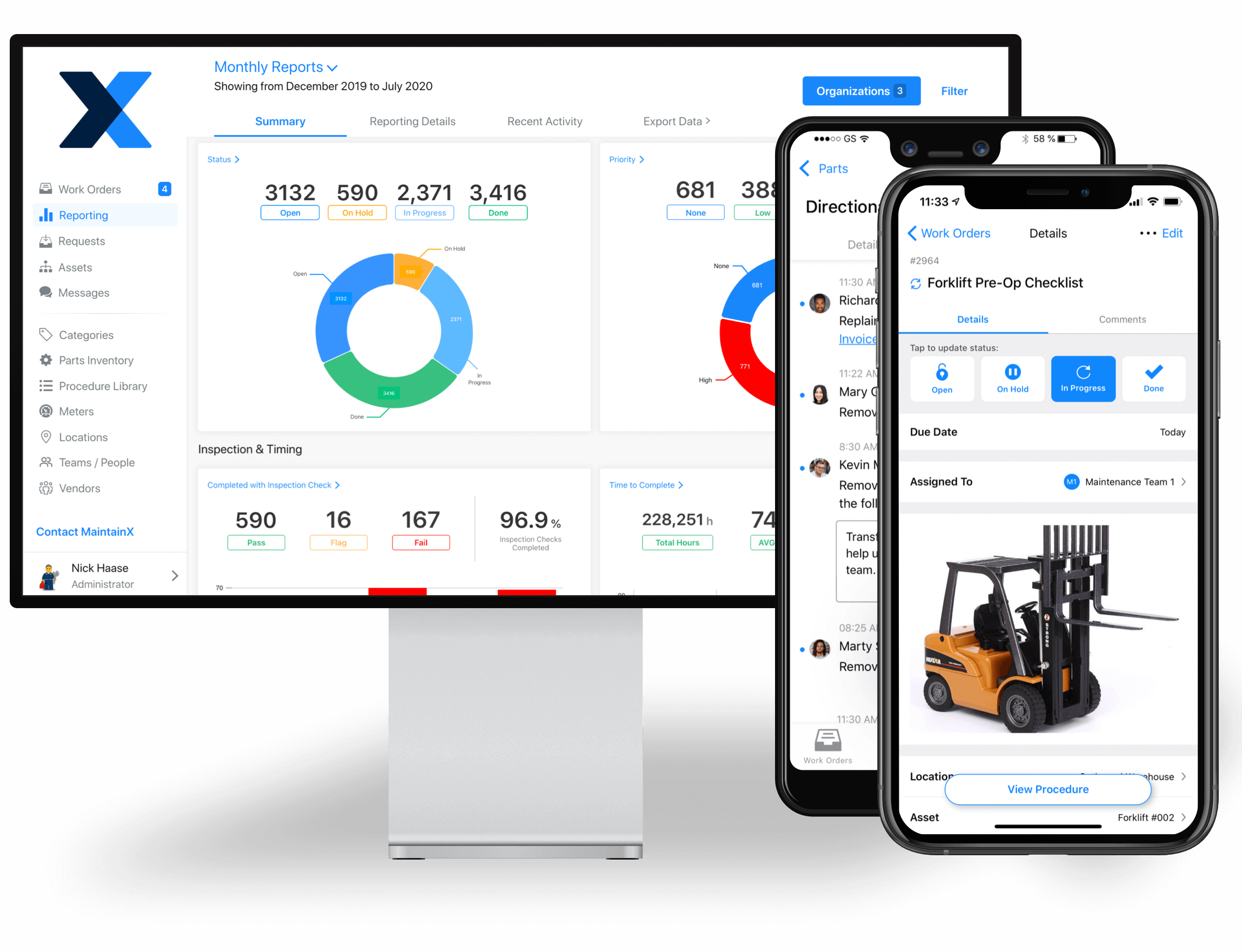
4. Use an Electronic Data Management System (EDMS)
Developing and managing multiple SOPs can be challenging, even for small businesses without many departments. As previously mentioned, the process becomes even more difficult as businesses reach new heights.
This is why it’s important to use an electronic data management system (EDMS) such as SOP software or computerized maintenance management system (CMMS) software. EDMS allows managers to automate SOP development with several convenient features.
User-friendly platforms make it easy to download, customize, and save SOP templates; assign, monitor, and troubleshoot worker progress; and ensure regulatory compliance with cloud-based audit trails for quick referencing.
The best SOP software programs allow workers to quickly complete SOP checklists on their smartphones, even when working from remote locations offline.
Benefits of SOP Digitization
- Enhanced decision-making by accessing insightful information such as job performance, time on task, and other important metrics
- Streamlined audits and inspections
- Secure cloud-based data storage
- Increased efficiency in implementation
- Improved quality-control processes
- Optimization of employee talent and skills
- Saved time
Generally, EDMS will make your SOPs easier to implement, track, and monitor for improvement. Digitizing documents—instead of managing disorganized file cabinets packed with paper records—also make it easier to scale up as the company grows.
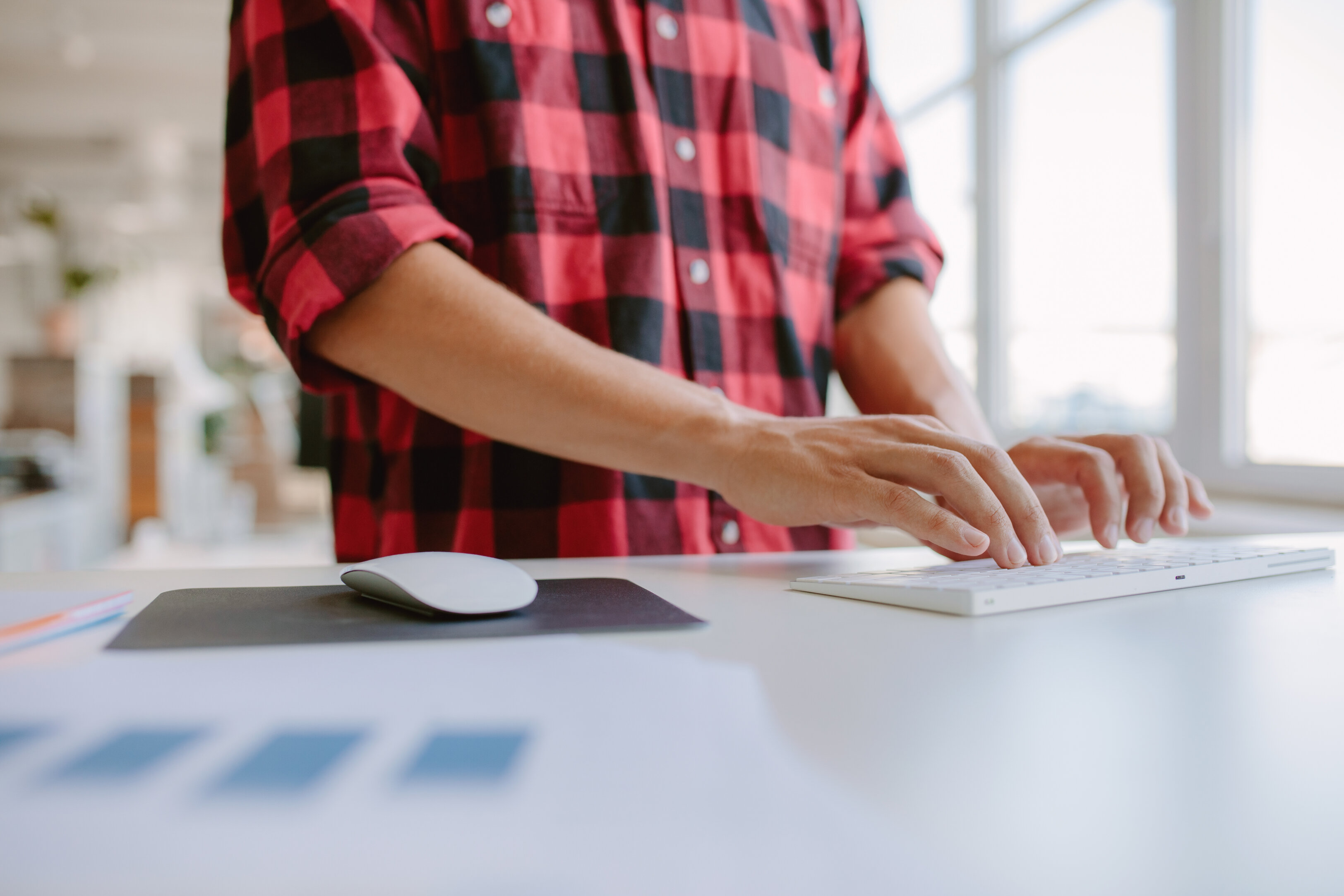
5. Write SOPs from the End User’s Perspective
Writing SOPs without a clear picture of how they relate to associated tasks and overarching organizational goals is a recipe for miscommunication. While management maintains a pulse on “the big picture,” workers on the ground often have a better sense of the relationship between specific procedures.
Put yourself in the assigned employees’ shoes and see what pieces of information they will need to complete the task. There’s only one way to do this, and that’s asking your employees for their input, as mentioned earlier.
But knowing the desired end result isn’t enough. You also must write SOPs clearly so that they leave no room for confusion, ambiguity, or employee errors.
Tips for Writing End User-Focused SOPs
- Use common language (avoid acronyms).
- Write the task’s scope first.
- Write in the active voice.
- Keep it brief ( attach work instructions, if needed).
- Use words that match the words on controls and panels.
- Avoid unfamiliar abbreviations (attach a glossary, if needed).
- Follow consistent language and formatting across company-wide documents.
- Use flow charts and diagrams to illustrate any process being defined.
- Issue warnings, cautions, and notes BEFORE the steps they reference.
Additionally, exercise caution when using terms, such as “may,” “must,” and “should.” Workers are likely to misunderstand the differentiation between the phrases. For example, “must” generally refers to mandatory instructions, while “may” alludes to flexibility in decision-making. When in doubt, keep it simple, describe every step, and be consistent!
6. Create SOPs for Reviewing SOPs
You can sort SOP documents into two categories: technical and management SOPs:
- Technical SOPs: These SOPs are the subject of this article; they provide workers with step-by-step instructions on how to complete given tasks.
- Management SOPs: These documents are guidelines for how to create, review, and update standardized tasks.
Management SOPS are essential for maintaining consistency across organizational lines. For best results, management should consistently revisit SOPs to validate their accuracy within existing workspace environments, quality control standards, and regulatory requirements.
7. Experiment with SOP Formats
When developing standard operating procedures, managers typically follow one of three different types of formats, including:
- Simple Steps Format: This format is suitable for short, routine, and easy-to-follow procedures. It’s usually a simple, bulleted list with short sentences. The format is mostly used for safety guidelines and mandatory documentation.
- Hierarchical Steps Format: For SOPs that involve a lot of steps, consider a hierarchical steps format. This layout lists a task’s main steps as primary checkboxes, followed by their related substeps as secondary checkboxes.
- Flowchart Format: Managers use process flowcharts for SOPs that involve several possible outcomes and decisions along the way. The chart maps out and plans potential procedures to follow in the event of unpredictable situations.
The right SOP format is always the one that best explains how to complete the task at hand. Again, different formats are ideal for different types of tasks.
For example, you can use the simple steps format to outline how to clean lab equipment. However, more complex tasks such as Lockout/Tagout processes may necessitate hierarchical steps or flowchart formats.
8. Use MaintainX to Manage SOPs
Lastly, we recommend using MaintainX’s CMMS platform for developing standard operating procedures. The desktop and mobile platforms allow you to automate the creation, assignment, and management of SOPs. Of course, enhanced automation translates to more time saved.
McDonald’s Franchise Owner Steve Nesbit saves 10 to 30 management hours a week using MaintainX. Here’s a screenshot of a standard SOP checklist written for the purpose of maintenance training:
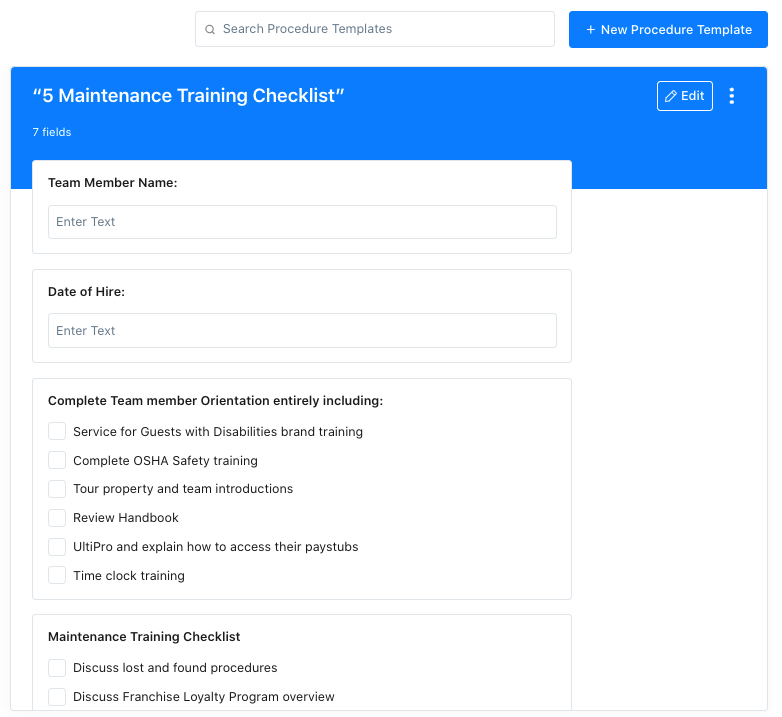
In addition to streamlining maintenance work orders, the mobile and desktop software allows managers to customize user-friendly SOP checklists within minutes.
The best part? MaintainX users have access to our Global Procedure Library, which houses hundreds of commonly used SOPs for restaurants, warehouses, factories, and more.
You can use MaintainX to simplify several tasks, including:
- Assigning recurring SOP tasks to specific employees.
- Attaching photographs, manuals, policies, and work instructions.
- Streamlining employee training and onboarding.
- Monitoring employee performance with real-time updates.
- Reviewing, updating, and revising SOPs whenever necessary.
- Proving compliance with digital audit trails.
- Storing company data securely in the cloud.
- Scaling up SOPs as the business grows.
MaintainX also enables managers to streamline communication, workflows, and accountability. As the world’s first industrial-maintenance app with chat, MaintainX allows managers and technicians to communicate via work order commenting, team messaging, and private messaging in real time.
Download MaintainX for free from your mobile app store and try the premium features for 30 days before deciding to upgrade. Our Basic Plan is always free.
You can view our payment plans here.
Using MaintainX to Create Standard Operating Procedures
The bottom line: every employee in an organization has a role in ensuring consistent quality output. The most effective managers develop standard operating procedures for performing routine tasks to avoid confusion, improve efficiency, train new employees, and keep everyone safe.
Are you ready to optimize your business processes and reduce unnecessary downtime with digital SOPs? Check out MaintainX’s new Procedure Builder, complete with Conditional Logic Fields and procedure scoring.
If you are not yet a MaintainX customer but want to see how you can turbocharge your SOPs, get in touch for a live walkthrough from one of our product experts!
FAQs
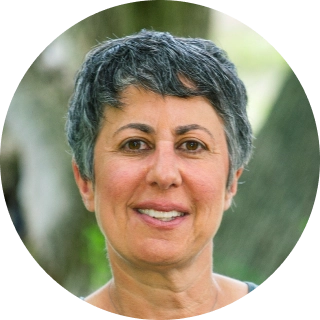
Caroline Eisner is a writer and editor with experience across the profit and nonprofit sectors, government, education, and financial organizations. She has held leadership positions in K16 institutions and has led large-scale digital projects, interactive websites, and a business writing consultancy.