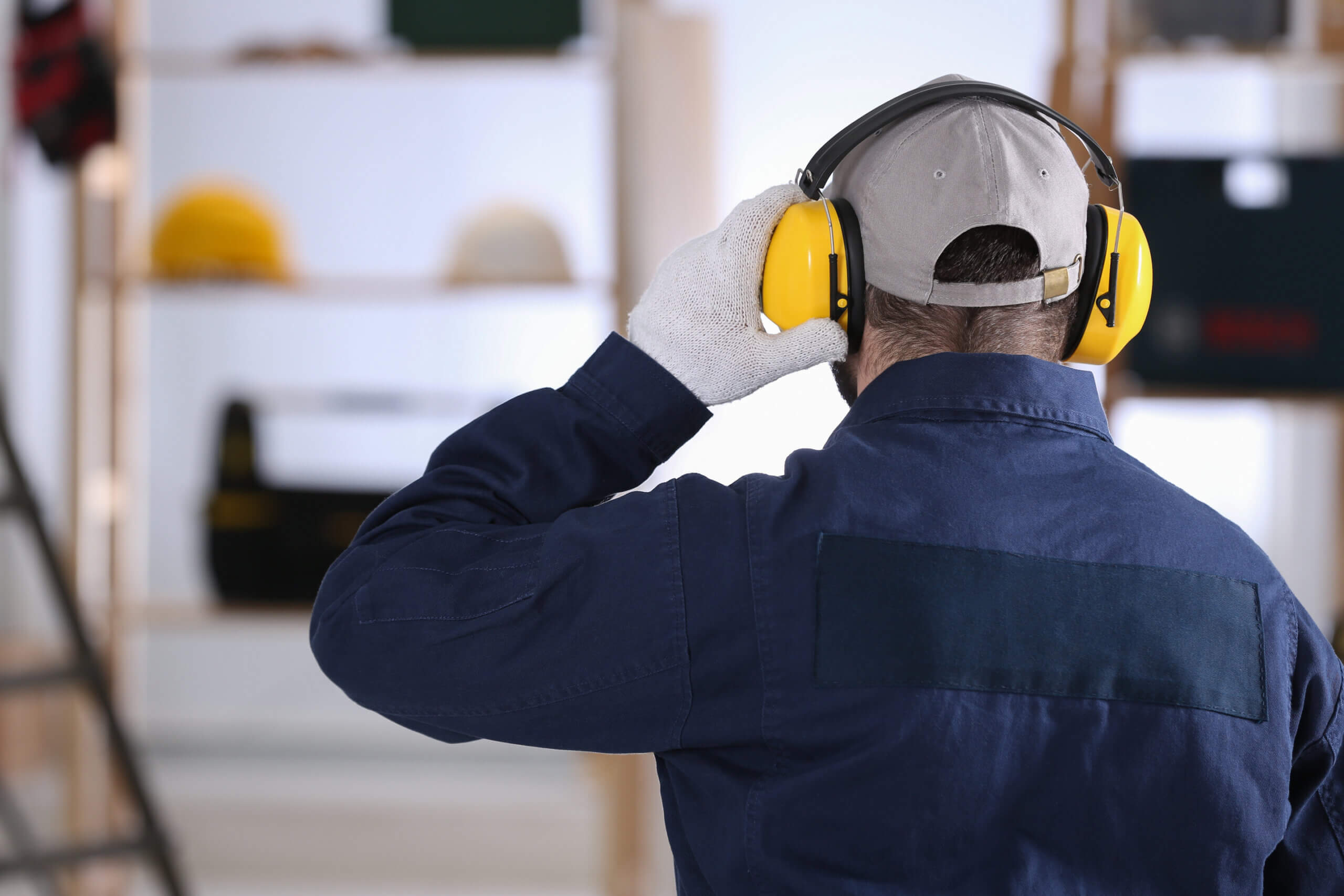
What is Safety in Maintenance?
Ensuring your maintenance team’s health and safety is critical for your organization to avoid hazards, illnesses, and injuries. In addition, manufacturers often cite safety controls as even more important than profitability because their safety programs impact all parts of the business, from compliance to employee retention to production line efficiency.
This guide explains why ensuring your maintenance team’s health and safety is essential, the rules to be mindful of, and how a CMMS can help.
“Workplace health and safety is all about sensibly managing risks to protect your workers and your business. Good health and safety management is characterised by strong leadership involving your managers, workers, suppliers, contractors and customers.”
IOSH
Safety in maintenance is about providing a work environment free of risks associated with maintenance activities.
The nature of maintenance work requires proper planning and technicians to perform unusual and non-routine tasks, often in exceptional conditions or confined spaces. For example, technicians may need to disassemble and reassemble machinery or work in extreme temperatures. In addition, maintenance technicians often need to work under time pressure because downtime is expensive, increasing the risk of injury.
Profitability is one thing, but putting safety measures in place and providing employees with safe environments is an ethical responsibility.
What Are the Safety Rules during Maintenance?
Three rules to follow to ensure workplace safety for your maintenance technicians are:
1. Provide Appropriate Equipment and Tools
Your maintenance team needs various tools and equipment to perform maintenance tasks safely. For example, you should provide personal protective equipment (PPE) to protect them against exposure to hazardous substances like asbestos or pesticides.
The equipment should have instructions to minimize the risk of injury from improper operation. Lockout Tagout instructions are an excellent example. Lockout Tagout is a safety procedure that ensures maintenance technicians completely shut down hazardous equipment while completing repair work.
The maintenance team should be trained to determine if the equipment is suitable for a specific environment. For example, your team should never use a sparking tool in a flammable environment.
Also, always consider the technician’s health when providing a piece of equipment. Finally, ensure the equipment is ergonomic and fits the technician well with the proper adjustments.
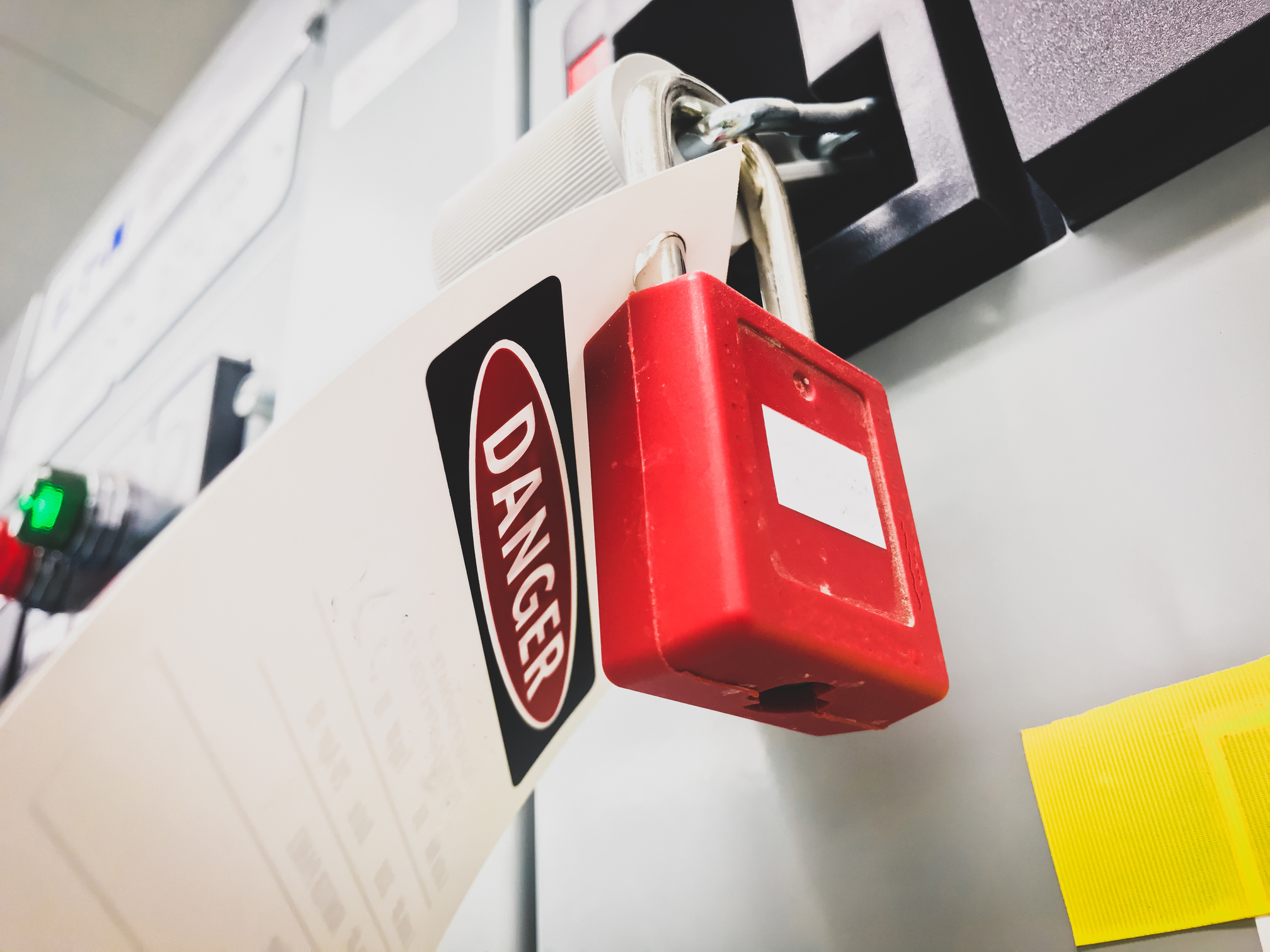
2. Provide Access to Complete Information
Making sure critical information and safety guidelines are visible across the shop floor is critical to ensure worker safety. Placing barriers and signs to mark hazardous areas and prevent unauthorized access to those work areas is a good starting point.
The areas on the shopfloor must be clean, and technicians should have a safe route to enter and exit the site wherever they need to perform maintenance. In addition, repair locations should have temporary ventilation and a proper lockout to protect the machinery.
Work orders should include photos and diagram labels explaining all safety procedures necessary to perform maintenance. For example, pressing the wrong switch can lead to an accident that could’ve been easily avoided with a safety label.
Technicians should also have access to maintenance and repair history to identify potential issues and previous accidents. While these health and safety measures may seem complicated, a computerized maintenance management system (CMMS) can help ensure technicians have all the information at their fingertips.
3. Provide Thorough Safety Instructions
Ensure technicians access maintenance health and safety instructions for all maintenance tasks. When creating work orders, include safety instructions for each task and be specific. Add instructions to handle each machine part and high-risk activity required to complete the maintenance task.
Each task should have an expected duration. Each procedure should end with a test confirming the machine is safe for others to use. If the technician has questions about a maintenance task, they should be able to reach out to you or a relevant person for help. Using a CMMS with in-app chat capabilities ensures the safety of maintenance workers.
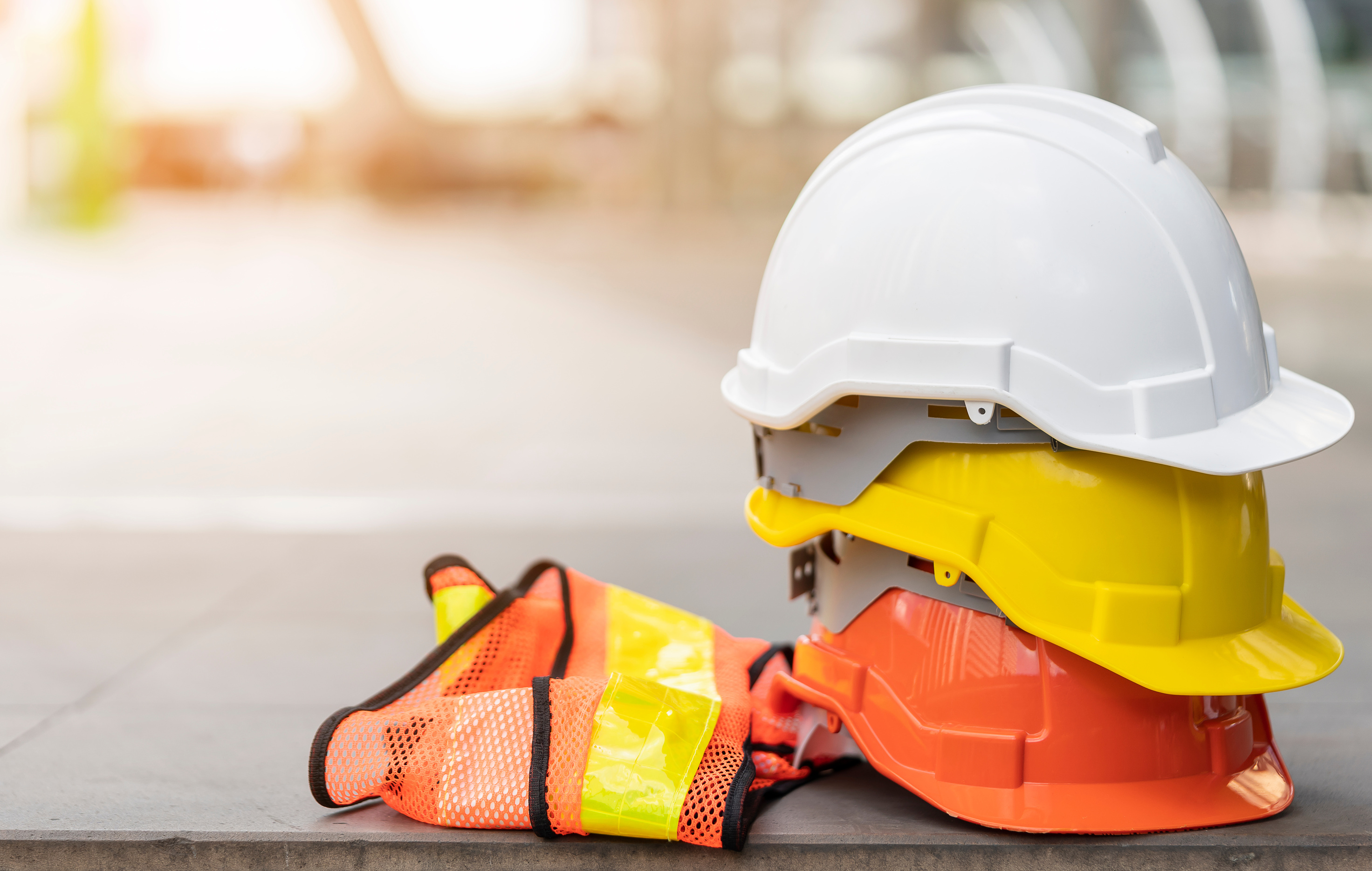
Why Is Maintenance Important for Safety?
Maintenance ensures equipment reliability. Improperly maintained machinery can be unreliable and become faulty. Fewer instances of breakdowns or potential issues translate to reduced contact with machinery. Maintenance is key in detecting faults early.
Maintenance for safety reasons is also a regulatory requirement. OSHA (Occupational Safety and Health Administration) has guidelines for the U.S. Other countries also provide workplace safety regulations. For example, CCOHS (the Canadian Centre for Occupational Health and Safety ) and the UK’s PUWER (Provision and Use of Work Equipment Regulations 1998) also regulate workplace safety and health.
What Are the Four Types of Maintenance?
You can implement four types of regular maintenance operations at your factory. However, it’s best to use multiple types of maintenance approaches based on the type of assets and maintenance safety requirements.
1. Corrective Maintenance
Corrective maintenance involves detecting a problem using non-destructive testing techniques like ultrasonic testing and vibration analysis. Corrective maintenance ensures the issue is addressed before it escalates.
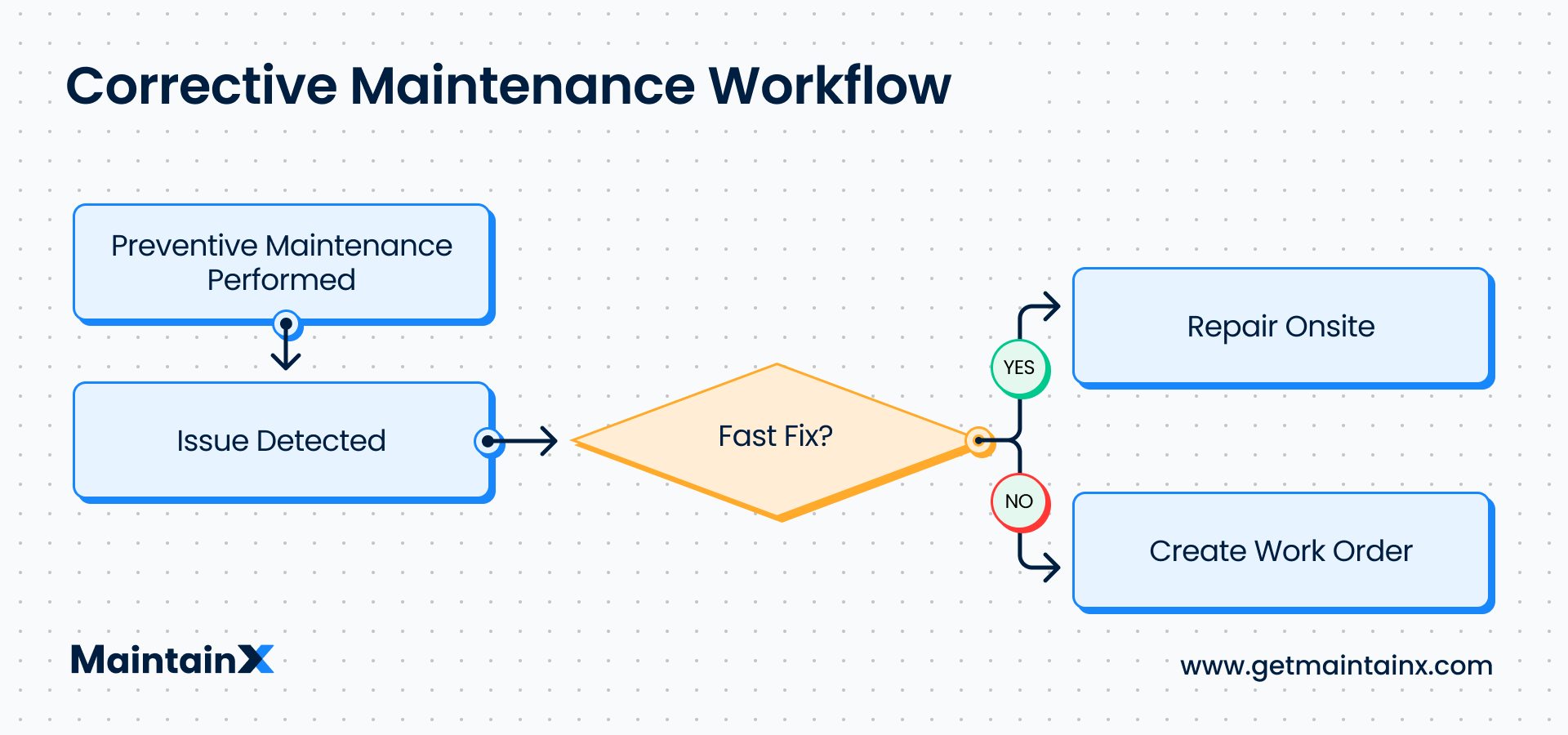
2. Preventive Maintenance
Preventive maintenance involves scheduling maintenance tasks to ensure problems are addressed before they occur. For example, tasks like lubrication, cleaning, and spare parts inspection are completed at a predefined frequency to avoid issues or breakdowns.
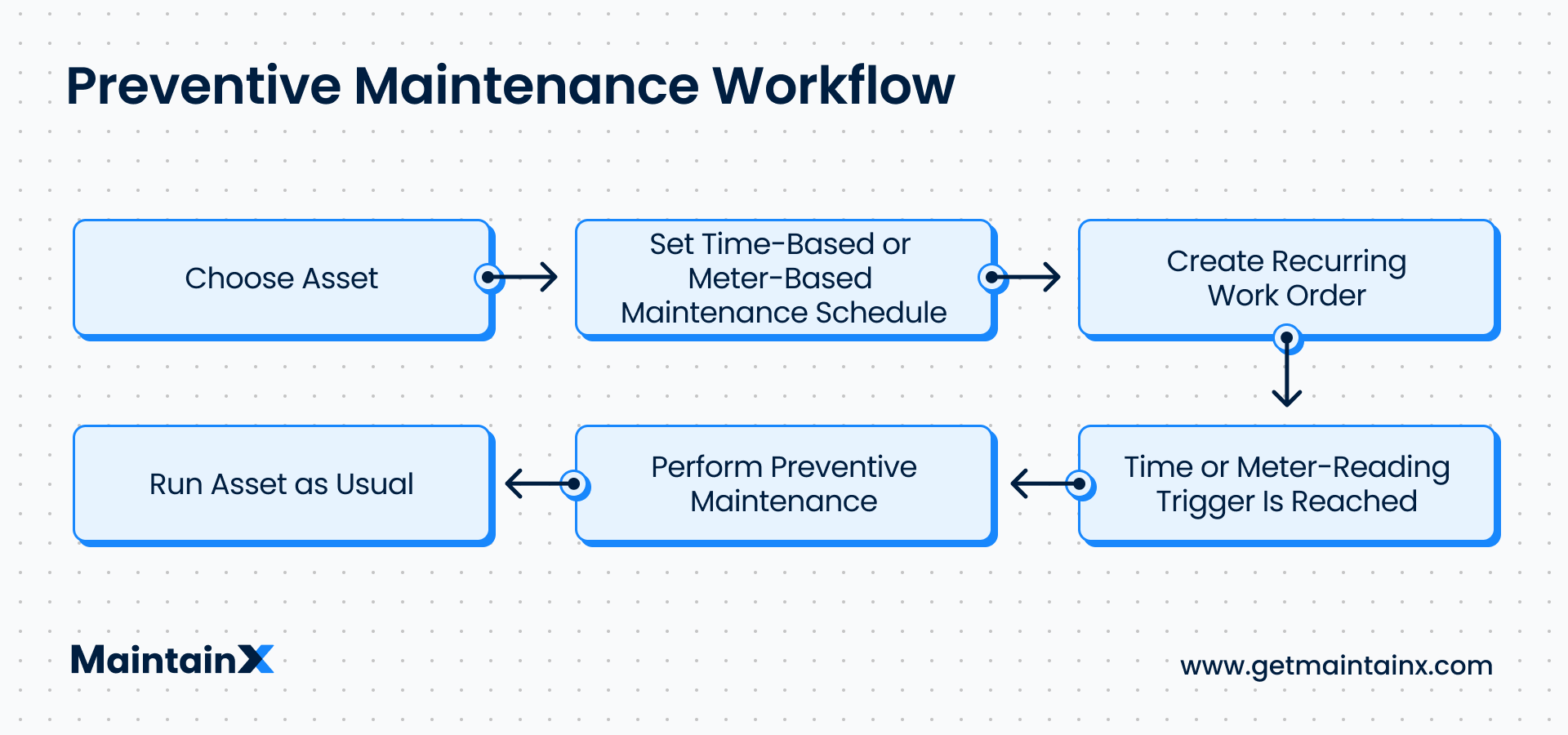
3. Condition-Based Maintenance
Condition-based maintenance involves using specialized equipment and IoT devices to detect problems using signals like temperature and sound frequencies. Unlike preventive maintenance, condition-based maintenance is performed on an as-needed basis.
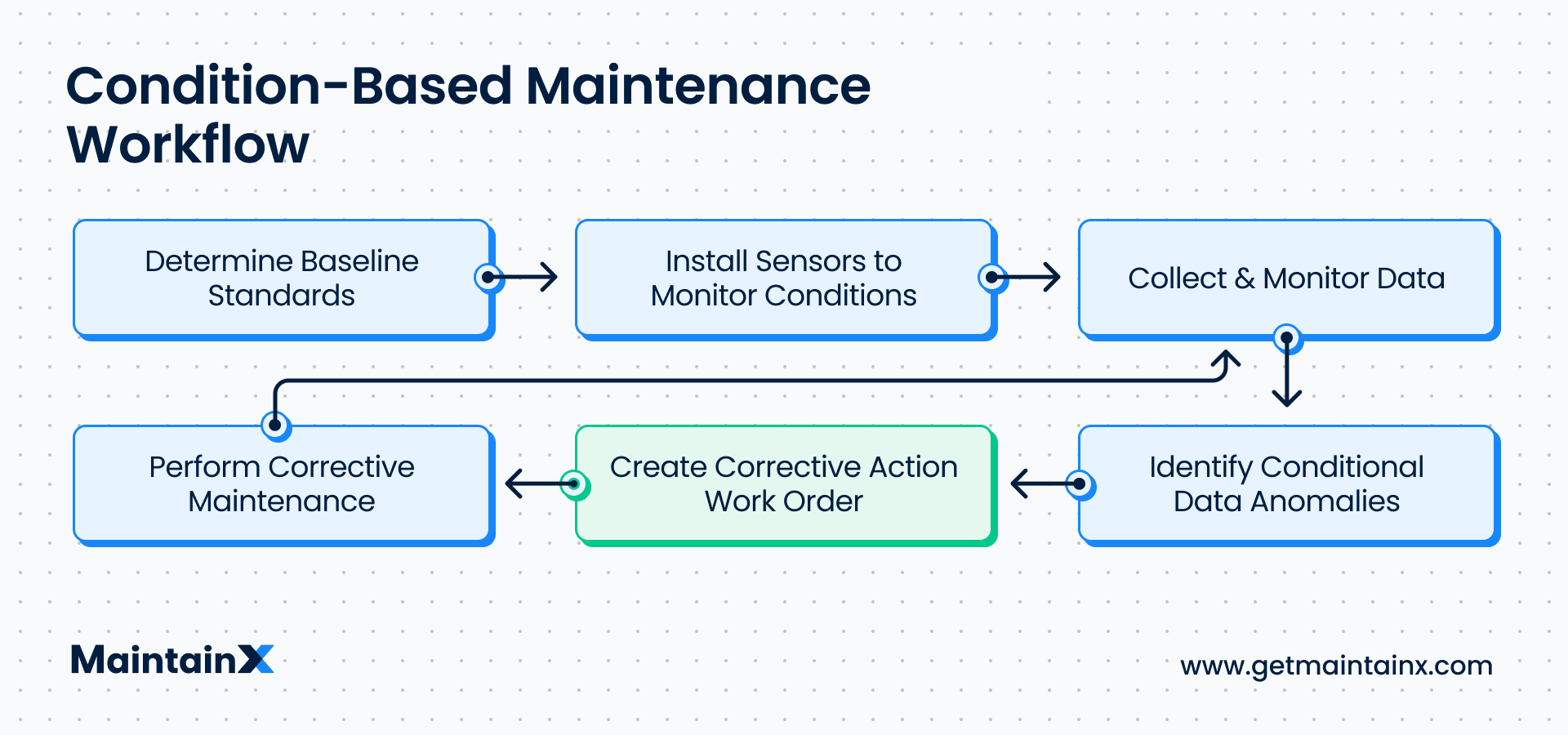
4. Predictive Maintenance
Predictive maintenance involves monitoring the equipment’s condition and predicting potential failure based on the collected data. The idea is similar to condition-based maintenance, except that the predictive maintenance algorithm tries to predict the possibility of future failures.
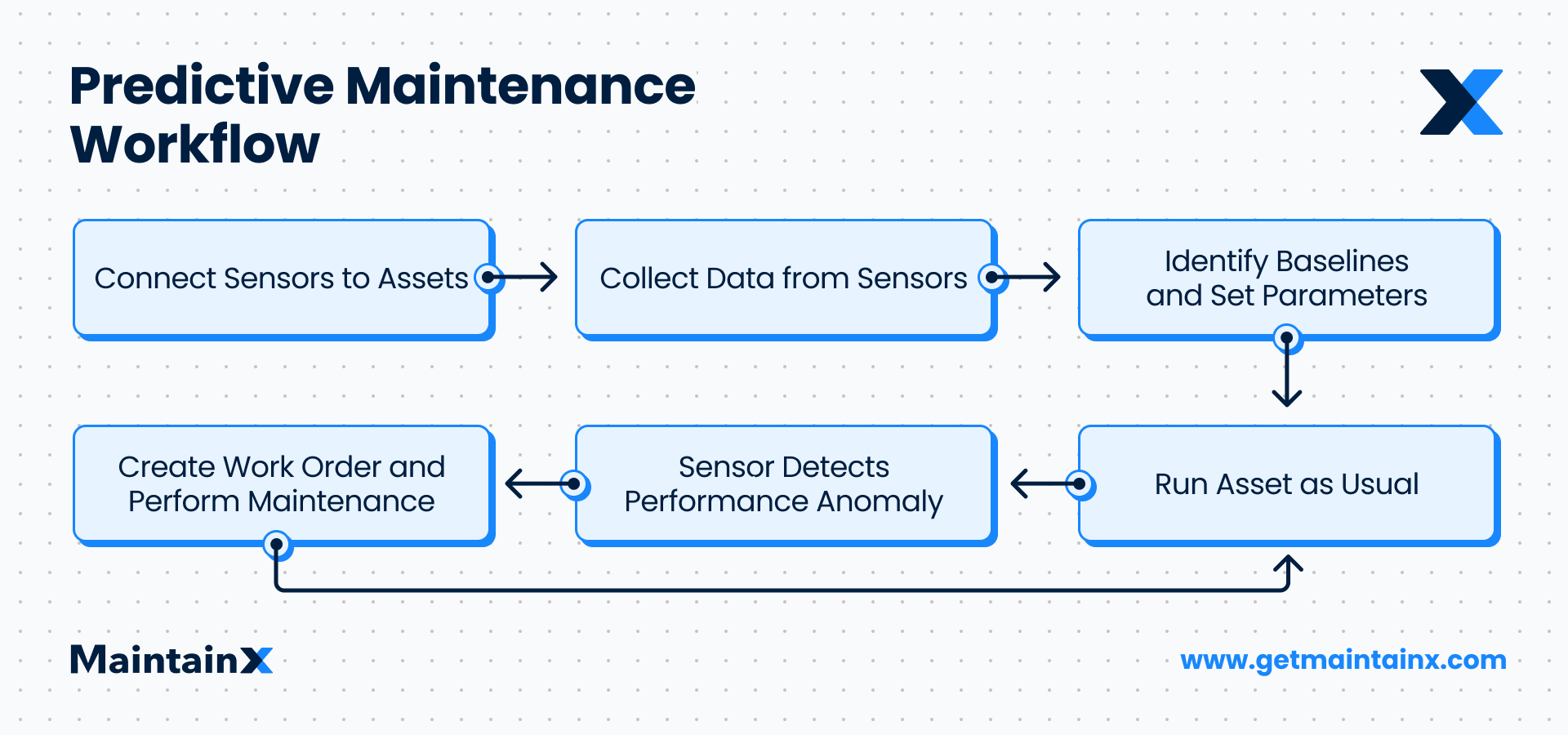
Use MaintainX to Ensure Health and Safety
MaintainX is a mobile-friendly CMMS that helps you implement safety measures more efficiently. For example, a manager can create and assign reactive work order procedures during an emergency from the spot of the breakdown, eliminating the time needed to get back to the office and assign a team.
Also, all safety procedures for that particular asset can be attached to the work order. Once the machine is back up, technicians using the digital work order can upload pictures after completing the repair, automatically storing this data in the cloud.
With a CMMS, technicians have complete visibility over repair and maintenance history. In addition, they can view all maintenance activities using MaintainX on their mobile phone and use the built-in chat feature in case they have questions. If that sounds interesting, try MaintainX for free today.
FAQs
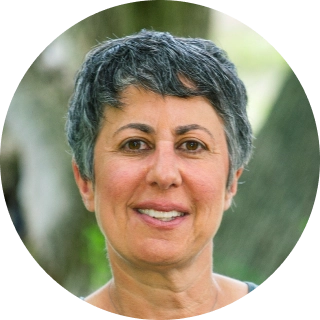
Caroline Eisner is a writer and editor with experience across the profit and nonprofit sectors, government, education, and financial organizations. She has held leadership positions in K16 institutions and has led large-scale digital projects, interactive websites, and a business writing consultancy.