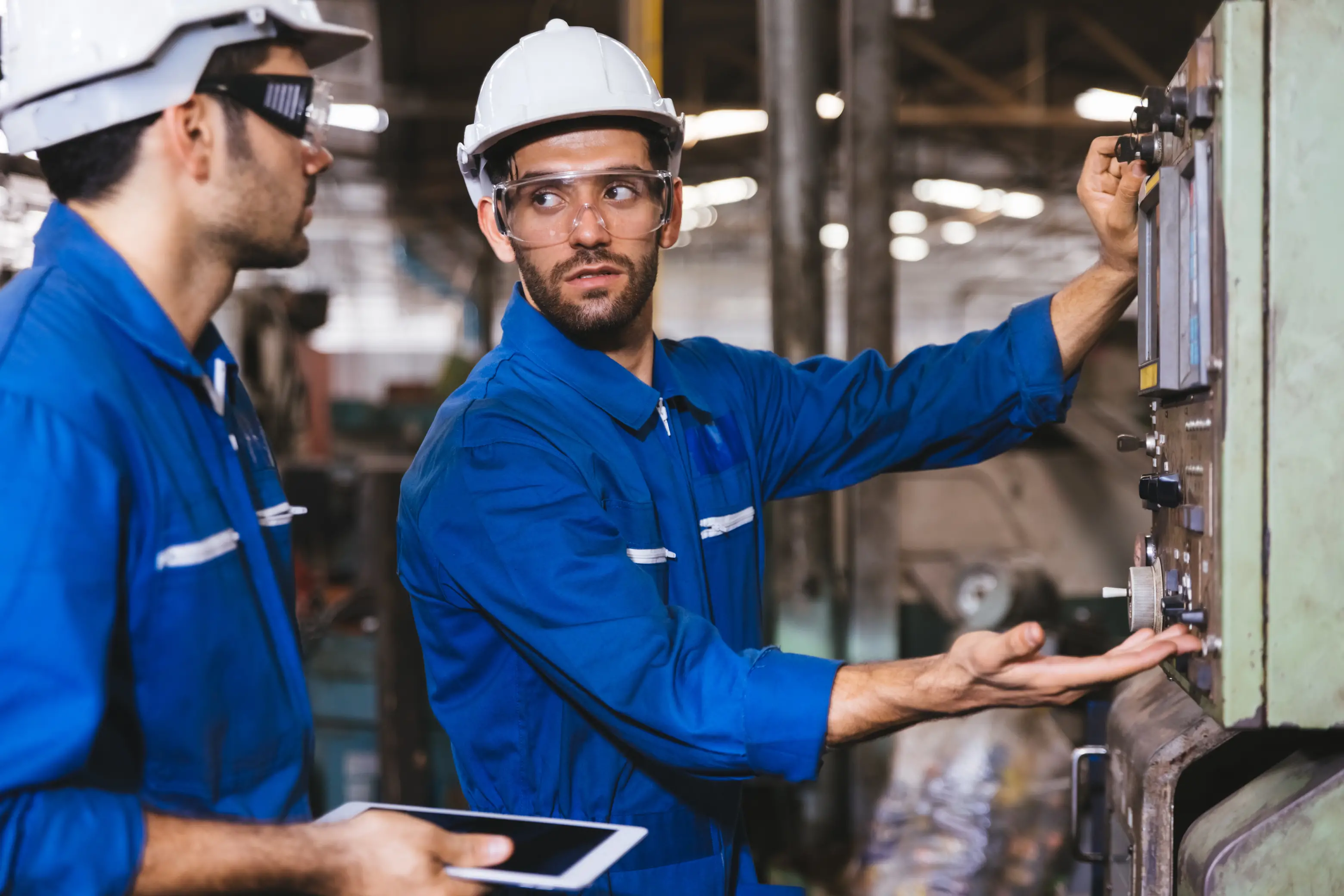
Failure metrics tell a story—the story about your maintenance team’s effectiveness and how you might be losing productivity during failure events. Tracking failure metrics provides excellent insights into how you can minimize downtime. That’s where the meantime and CMMS (computerized maintenance management system) combination is useful.
In this guide, we explain how to calculate these metrics and how CMMS software can help track them.
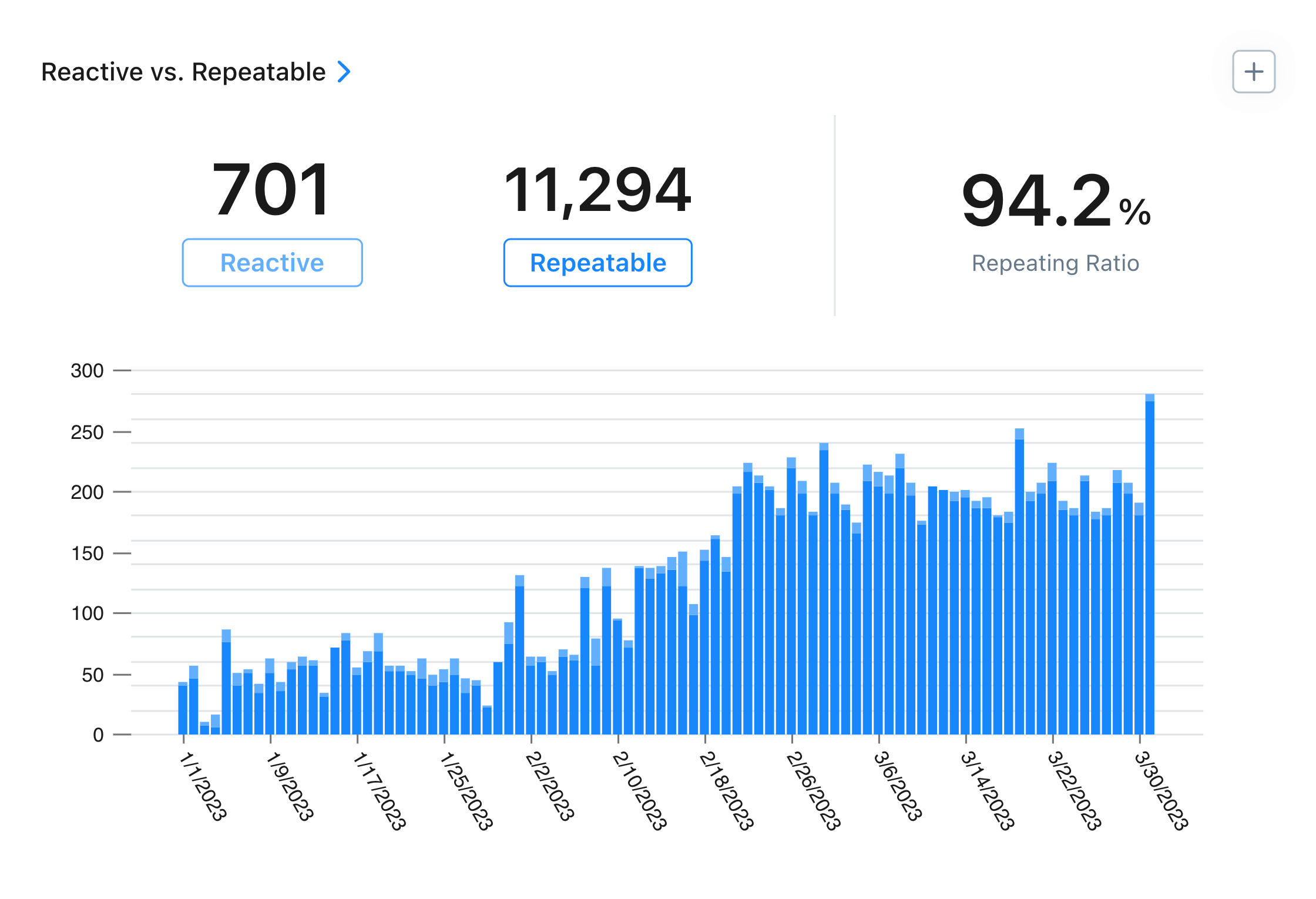
Why Track Failure Metrics?
Metrics like mean time to repair (MTTR), mean time between failure (MTBF), and mean time to failure (MTTF) help assess maintenance effectiveness. They provide the insights you need to optimize maintenance operations and minimize unplanned downtime.
A CMMS solution collects relevant data and helps monitor these KPIs (key performance indicators) so you can maximize uptime.
What Is Mean Time to Repair (MTTR)?
MTTR calculates the average time your maintenance team takes to repair a piece of equipment. Here’s the formula used for MTTR calculation:
MTTR = Total Maintenance Time ÷ Number of Repairs
For example, suppose your maintenance team spends 100 hours on the unplanned maintenance of a specific asset. The asset broke down 10 times during the year. The asset’s MTTR is 10 hours.
Note that the uptime doesn’t affect this maintenance metric. It measures maintenance efficiency based on breakdown frequency by measuring how quickly the maintenance team fixes the issue. MTTR improves when the maintenance team can minimize the time needed for unplanned maintenance tasks.
What Is Mean Time Between Failure (MTBF)?
MTBF calculates the average time that an asset runs between two failure events. Here’s how you can calculate MTBF:
MTBF = Total Uptime of Repairable Asset ÷ Number of Failures of Asset Within Given Time Period
For example, an asset ran for 20,000 hours over the last year and failed four times. The MTBF for the machine is 5,000 hours.
When calculating total uptime, you include planned or preventive maintenance work and exclude only unplanned maintenance. Also, the number of failures can include incidents where the asset failed to meet the intended production levels it was designed to achieve.
What Is Mean Time to Failure (MTTF)?
MTTF measures the average time it takes for non-repairable assets to fail. These are assets that must be replaced when they fail. Examples include tires, conveyor belt balls, and motors.
Here’s how you can calculate MTTF:
MTTF = Total Hours of Operation ÷ Total Number of Assets in Use
Suppose you purchased 40 motors last year, and by year-end, all of them failed. The total operational time for those forty motors was 20,000 hours. The MTTF, in that case, is 500 hours.
This means the average lifespan of a motor at your facility is 500 hours. It would make sense to arrange for a new motor after 500 hours of operation. Of course, a motor may last more or less than 500 hours.
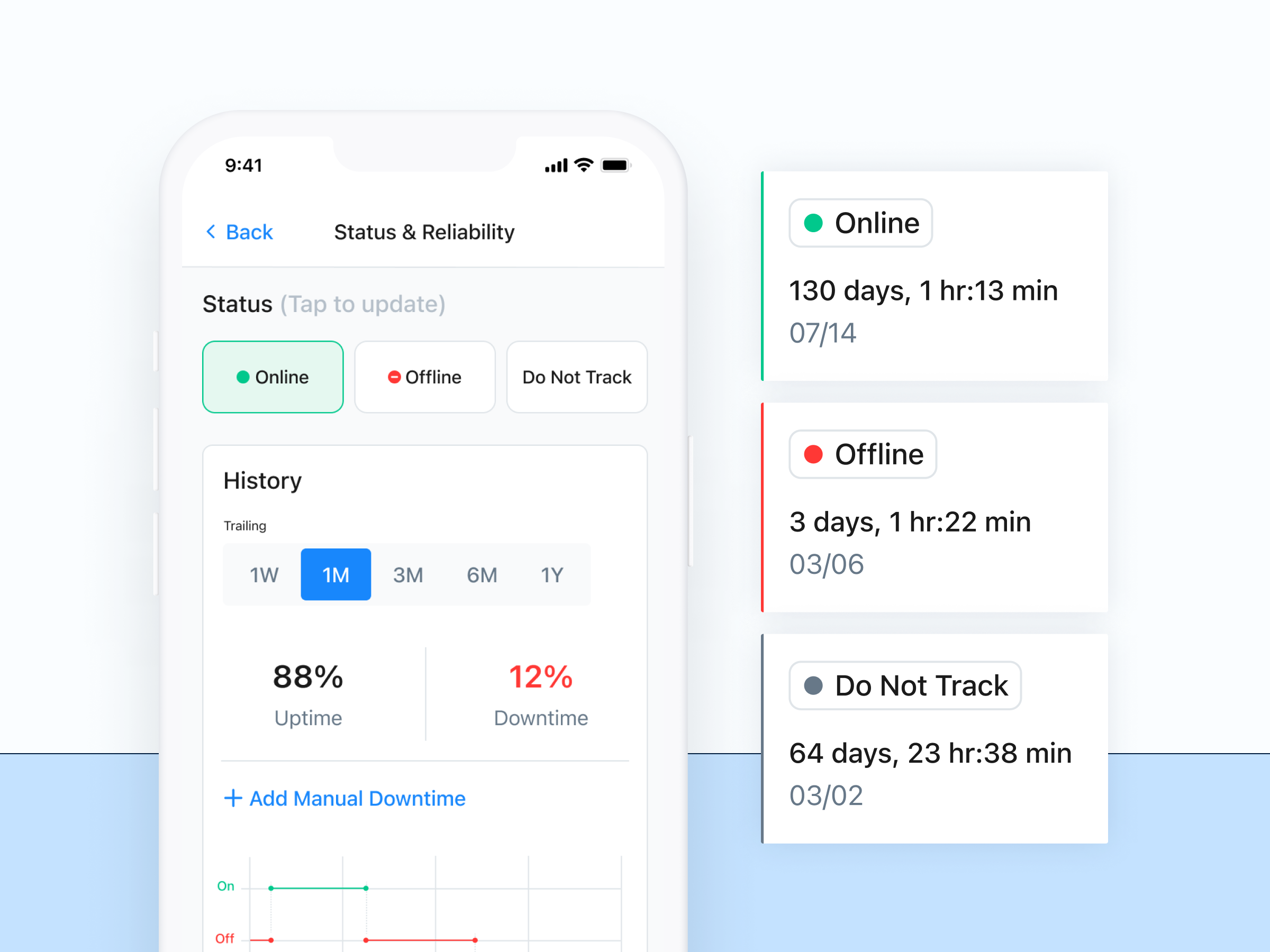
MTTR vs. MTBF vs. MTTF
Here are the key differences between the three:
How to Track Mean Times with CMMS
Tracking mean times on a spreadsheet can be time-consuming. Collecting data, aggregating it into one sheet, and calculating multiple failure metrics can be a lengthy and cumbersome process.
CMMS can automate the entire process. A CMMS like MaintainX can automatically collect and store asset performance and work order data throughout an asset’s life cycle. Once the data is in the system, MaintainX can help calculate and track failure metrics.
The built-in reporting capabilities and custom dashboards help you optimize the asset management strategy and maintenance plan. This helps improve failure metrics like MTTR, MTBF, and MTTF.

How to Improve Failure Metrics
If your failure metrics tell you there’s room for improvement, here’s what you can do:
- Proactive maintenance: Techniques like predictive maintenance and condition-based maintenance can significantly improve MTBF and MTTF. In many cases, proactive maintenance can minimize MTTR by providing you with access to data that can help troubleshoot the problem and find the root cause.
- Follow standard operating procedures: Standard operating procedures (SOPs) eliminate guesswork and save time. Creating a repair checklist and SOP helps the team streamline repairs for known causes of failure. You might also assign checklist items to a specific technician based on their expertise to expedite the process.
- Buy quality parts: Buy spare parts from trustworthy vendors and producers. Parts and materials that meet quality standards offer better durability, saving you hours of time by minimizing failure events.
- Invest in training: Train your maintenance team to use the most efficient repair methods and reactive maintenance techniques to minimize MTTR. The team will perform repairs faster as they get more practice. Technicians should also receive training to perform maintenance processes faster.
- Use a CMMS: Data in maintenance software fast-tracks diagnosis by allowing you to access preventive and corrective maintenance histories. CMMS like MaintainX can help create SOPs that list maintenance activities or repair tasks, allowing teams to fix problems faster.
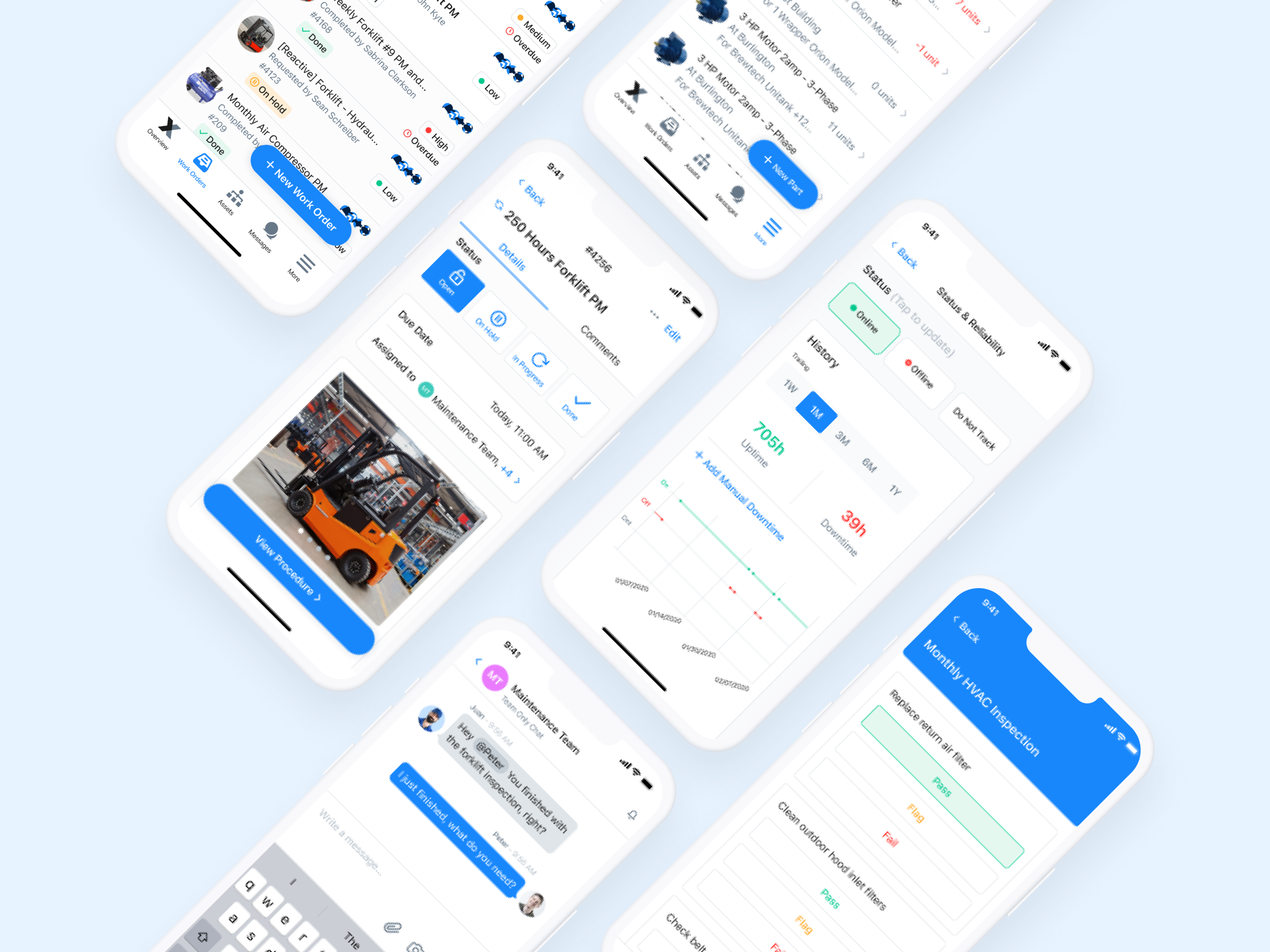
MaintainX: Track Failure Metrics with a Powerful CMMS
Tracking failure metrics like MTTR, MTBF, and MTTF is vital to monitoring the asset’s efficiency. If one or more of these failure metrics are too low, re-evaluate your preventive maintenance schedule.
Using work order management software like MaintainX is an excellent step towards more efficient execution of your maintenance program and improving these failure metrics.
MaintainX is a mobile-friendly CMMS that automatically collects data when you perform facility management tasks. It converts this data into comprehensive reports. You can also create custom dashboards to track failure metrics and make data-driven decisions.
Don’t take our word for it—try MaintainX for your business today!
FAQs
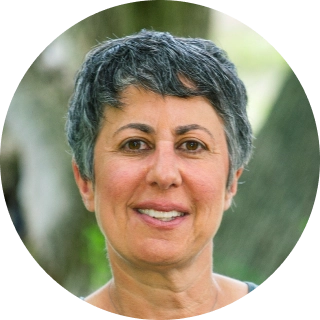
Caroline Eisner is a writer and editor with experience across the profit and nonprofit sectors, government, education, and financial organizations. She has held leadership positions in K16 institutions and has led large-scale digital projects, interactive websites, and a business writing consultancy.