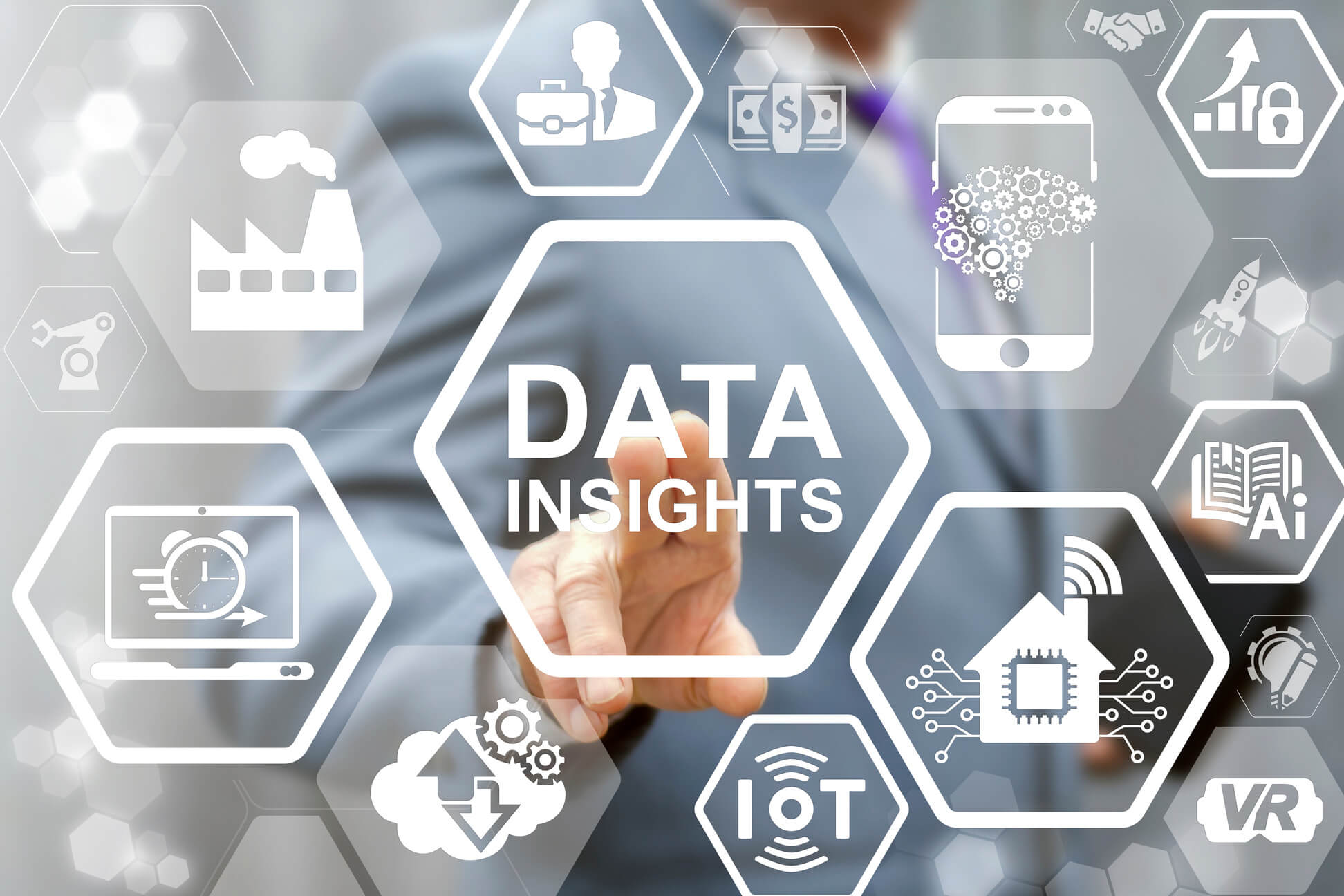
Manufacturing analytics refers to using data from operations and manufacturing to improve and ensure the quality of an organization’s performance. When applied to manufacturing and maintenance standard operating procedures (SOP), analytics provide actionable insights to optimize costs and drive efficiencies. This data and resulting performance metrics should guide a manufacturer’s process standardization.
“High uncertainty and low growth have already forced manufacturers to squeeze every asset for maximum value. The next target is their own data."
McKinsey
Manufacturing analytics is an essential part of the Internet of Things and Industry 4.0, which helps optimize business processes, manufacturing operations, and quality control.
Of course, using data to optimize processes is nothing new. Lean manufacturing and the kaizen principle of continuous improvement rely on data to improve processes and workflows. Technological advancements and digital transformation have given manufacturers tools for collecting real-time, on-site data.
Business owners can analyze manufacturing data using “big data analytics” and other forms of data analysis.
“Big data analytics examines large amounts of data to uncover hidden patterns, correlations, and other insights. With today’s technology, it’s possible to analyze your data and get answers from it almost immediately.”
SAS
With metrics and KPIs in hand, teams can generate valuable and actionable insights regarding their workflows, quality assurance, health, and safety compliance, and the manufacturing process.
This process enables robust and data-driven decision-making by team members, managers, and other stakeholders when creating standard operating procedures (SOPs). In addition, referring to your data analytics as you write up SOPs can significantly improve your maintenance team’s effectiveness.
“Advanced analytics also help manufacturers solve previously impenetrable problems and reveal those that they never knew about, such as hidden bottlenecks or unprofitable production lines.”
McKinsey
How Can You Use Manufacturing Analytics?
Manufacturing analytics should play a significant (and helpful) role in figuring out, crafting, and establishing standard operating procedures for your facility. In general, making data-driven decisions fosters a solid project management approach to leading effective, efficient, and satisfied maintenance and manufacturing teams.
Furthermore, when it comes to managing assets, you want to avoid human error and miscommunication. As a result, developing and establishing SOP templates and workflows will help you know what methods are working and which aren’t.
“Quality management plans and SOP provide opportunities to locate inefficiency and downtime in the manufacturing process. SOP also provides evidence of regulatory compliance on the factory and warehouse floor. Online SOP templates can help build an organizational culture of excellence.”
Reliability Connect
Maintenance Management
If you want to reduce your downtime costs, preventive maintenance is the way to go. However, regular or time-based preventive maintenance may not always be feasible, especially when dealing with limited resources.
Predictive manufacturing analytics can help forecast the likelihood of breakdowns, alerting you when to carry out maintenance activities. Here, manufacturing analytics can also provide insights about your corrective actions by analyzing specific metrics and KPIs. For example, data analytics play a key role in Root Cause Analysis.
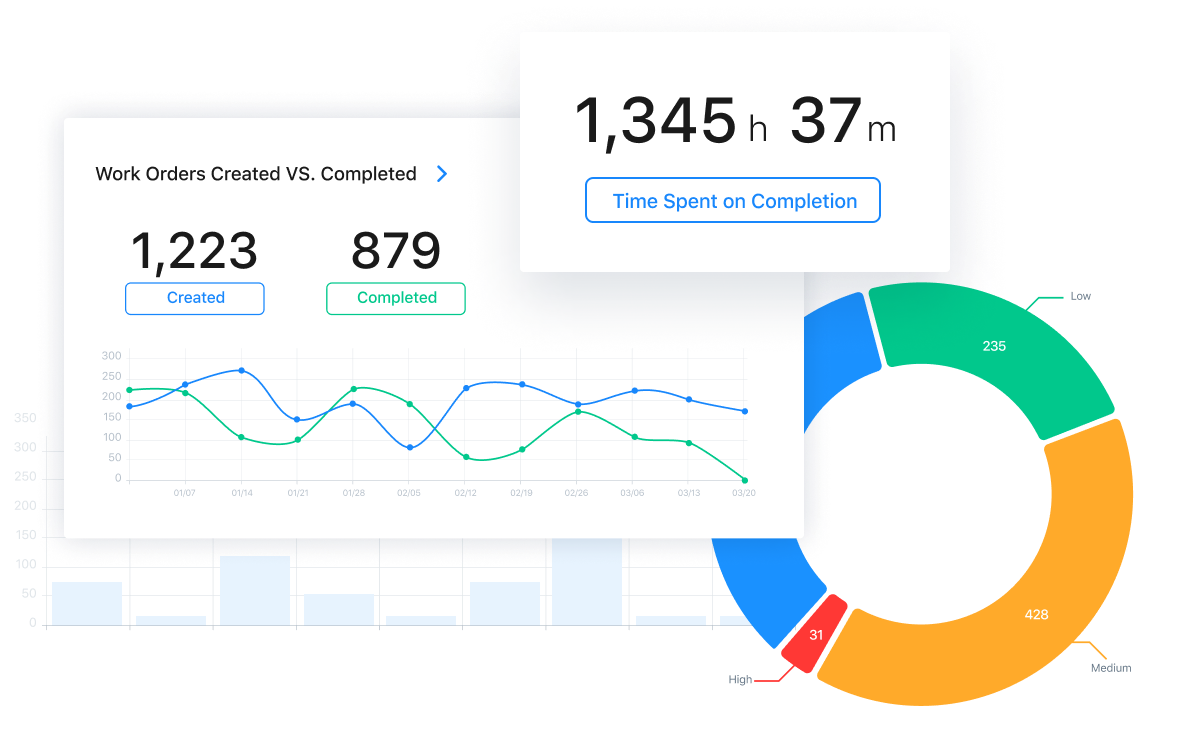
Supply Chain Management
Analytics can help you manage multiple aspects of the supply chain, from manufacturing to inventory to product delivery. For example, manufacturers can forecast output expectations using insights from shop floor data. Combining this with data about supply chain shortages and delays, and customer expectations affords manufacturers greater decision-making power.
A robust CMMS like MaintainX provides time and cost tracking across parts inventory, work orders, asset repairs, and downtime. You can use this data to create preventive maintenance workflows and to know just how much product to make and what pricing figures to set.
“Manufacturers getting the most value from analytics start with a solid business case first, based on a known problem they’ve been trying to solve either in their supply chains, production or fulfillment operations.”
Forbes
Quality Management
Developing a robust quality management system with standards like those in ISO 9001 requires reliable data. In general, data analytics can help you develop insights into stages in the production process. Manufacturing insights can support automation, reducing human error and improving quality control and product validation.
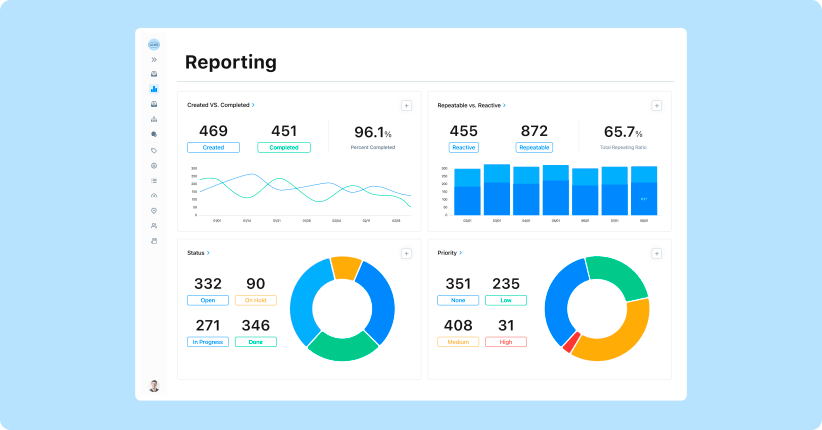
Why Use Manufacturing Analytics?
We’ve talked about manufacturing analytics use cases, so now let’s look at some potential benefits.
Reduce Costs
Using manufacturing analytics to manage your maintenance can help make your maintenance activities more effective. Data analytics can provide the insights necessary to plan your predictive maintenance and for root cause analysis to reduce equipment downtime.
Root cause analysis gives you deeper insight into the nature of a problem, ensuring you’re not spending time and energy on treating symptoms that are not the actual cause. In other words, when you address issues at the source, you eliminate redundant attempts to fix the problem. Quickly finding the source of breakdowns reduces your maintenance costs.
Increase Profits
Manufacturing analytics help optimize production. With insights gleaned from data, you can set the best and most cost-effective conditions to execute production and maintenance workflows.
Likewise, insights into supply chain challenges will help you maximize production times and optimize product pricing.
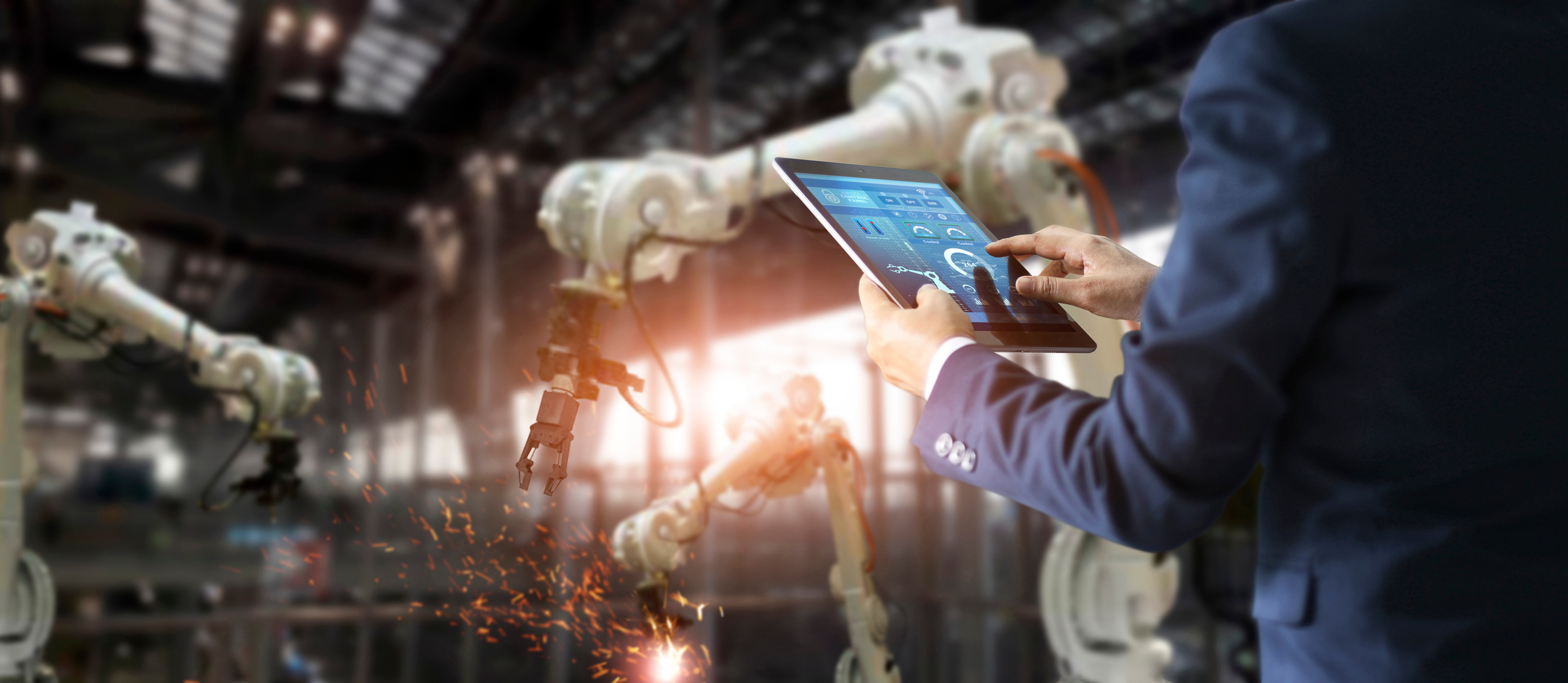
Using a CMMS for Your Manufacturing Analytics
If you want to take advantage of manufacturing analytics to supercharge your production and maintenance, a robust computerized maintenance management system (CMMS) can help in multiple ways. These include the following:
Manage Your Data
Manufacturing analytics begins with the data. The best CMMS come with data collection, storage, and tracking features. MaintainX, for example, is a mobile CMMS that records data in real time from the shop floor. With MaintainX, you can analyze your data via a range of reporting dashboards—Created vs. Completed Work Orders, Reactive vs. Repeatable Work Orders, Time and Cost Tracking, MTTR, etc.—to generate actionable insights.
Create Standard Operating Procedures
To extract maximum benefits from manufacturing analytics, we recommend standardizing your procedures. You need to have details and specifications about work processes available to teams when needed. A CMMS like MaintainX is an excellent SOP software for creating work instructions and tracking progress.
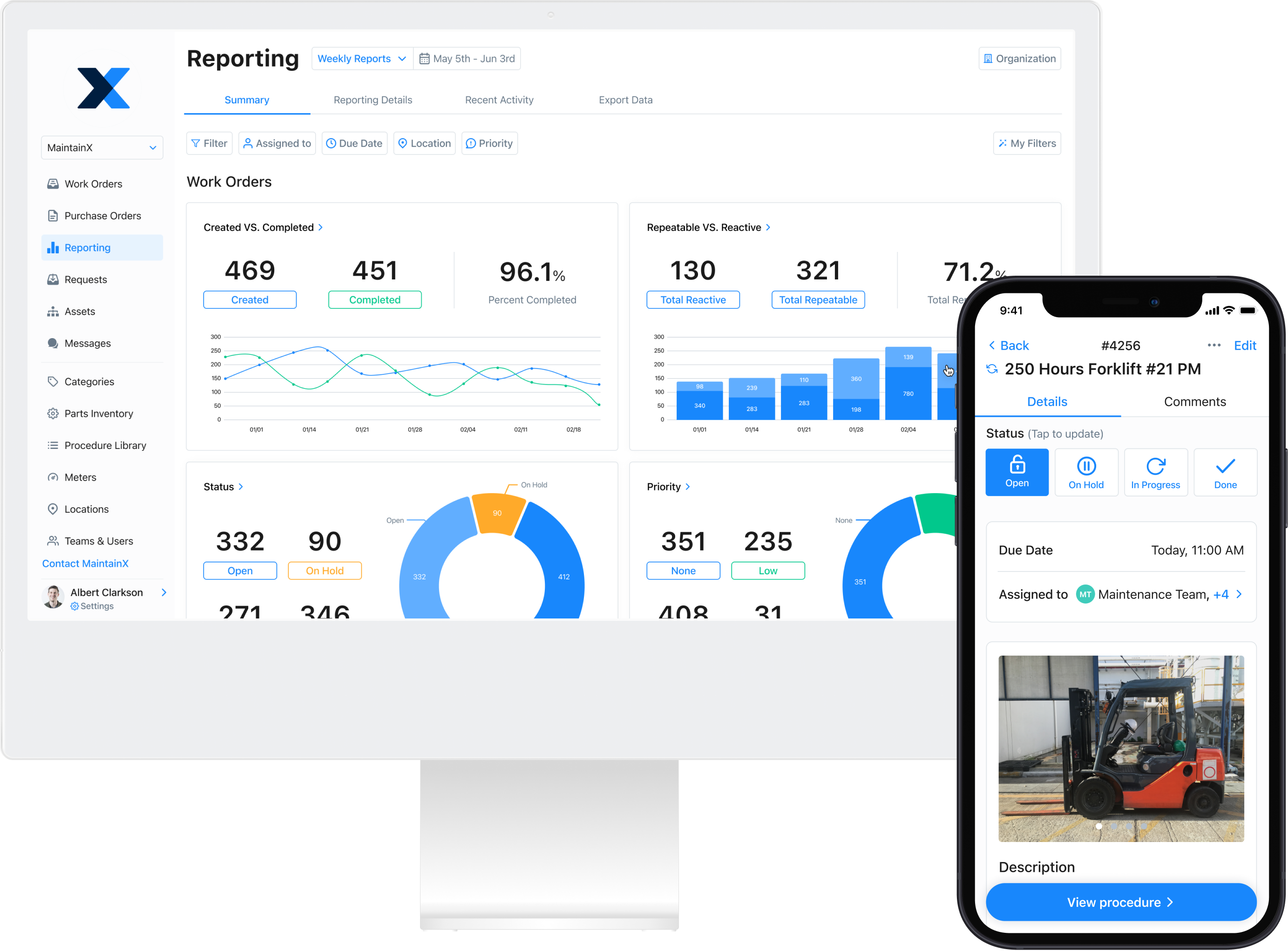
Optimize Your Manufacturing Analytics with MaintainX
If you’re ready to get serious about manufacturing analytics, get your hands on a CMMS. A CMMS (Computerized Maintenance Management System) can help you collect, store, manage, and analyze data on your manufacturing systems, inventory management, production processes, and maintenance plans. In addition, a CMMS like MaintainX can help you streamline your data workflows with features with essential real-world applications like:
- Dashboards for data processing, aggregation, analysis, and visualization
- Mobile application connectivity for real-time data collecting and sharing
- ERP integration
If you’re thinking about preventative maintenance programs in particular, MaintainX offers powerful functionalities such as:
- Asset and parts management
- Maintenance tracking
- Real-time updates
- Maintenance scheduling
MaintainX also helps facilitate work order automation and instant chat for real-time communication from the shop floor. Try MaintainX today!
FAQs
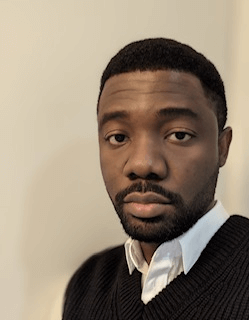
Lekan Olanrewaju is a content writer with years of experience in media and content creation. He has held positions at various media organizations, working with and leading teams at print magazines, digital publications, and television productions.