
Maintaining a world-class facility isn’t easy.
Universities, hospitals, and large organizations of all types depend on complex equipment. Facility management teams must ensure hundreds of building necessities are continually running without interruption.
HVAC, plumbing, and technology systems all require preventive maintenance (PM) to run at optimal capacity without replacement. Though running machinery to failure requires less routine outsourcing and fewer in-house hours, studies show preventive efforts often lead to larger cost savings over time.
According to one ITIC survey, an hour of downtime costs companies an average of $300K. Obviously, such astronomical losses would not apply to a few leaking toilet tanks. However, even small nuisances can drain budgets.
As organizations become increasingly reliant on interconnected networks to conduct business— servers, applications, the Internet of Things (IoT)— the need for strategic preventive maintenance planning will continue to grow. However, it’s not unusual for leadership to overlook the long-term value of scheduled maintenance. As the saying goes: Out of sight, out of mind.
For this reason, facility managers must sometimes become advocates for the preventive maintenance programs they know will increase productivity, save money, and increase asset longevity. Are you in the process of making a case for a PM budget increase? In this article, we’ll provide a few tips for strengthening your case for preventive maintenance:
3 Facility Preventive Maintenance Buy-In Tips
1. Create an executive-friendly report
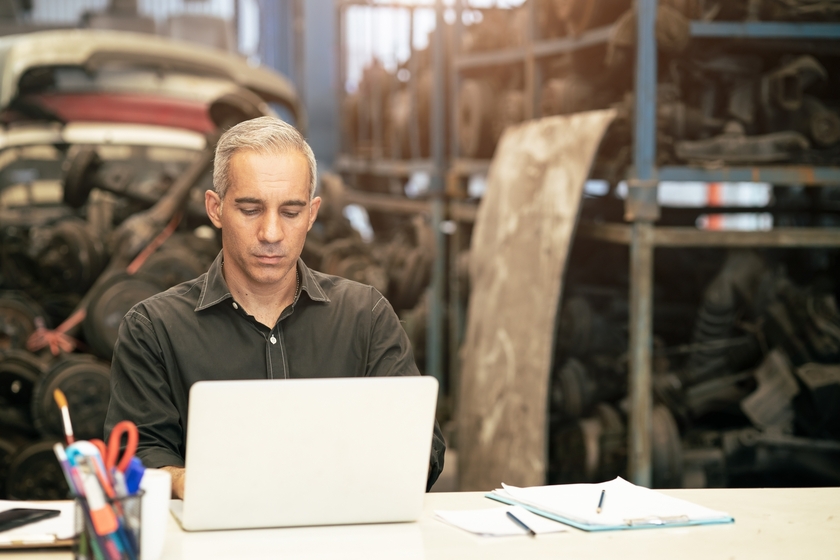
Top executives are most concerned with the big picture. They spend their days asking themselves questions like: How can we be more efficient as an organization? Do we have any unidentified opportunities for cutting costs? How can we provide even higher value to our customers and/or constituents?
Since executives are overseeing several departments at once, they won’t have time to delve into the nitty-gritty of facility maintenance. Instead, they will count on you to summarize the challenges, potential solutions, and supporting data in a digestible format to inform decision making.
FacilitiesNet contributor Darrell Rounds recommends using the A3 one-page report format to make your case. Toyota originally developed the format to help managers address questions executives most care about:
- How does this investment relate to business operations?
- How is the current problem impacting department objectives?
- What is the root cause of the problem?
- What is the desired outcome?
- What countermeasures will we take, assuming the outcome is met?
- What will be the follow-up process for monitoring progress?
Use as much data as possible to support your proposal, including internal reporting numbers and external maintenance statistics. Some key metrics that might be helpful include asset unscheduled downtime, equipment availability Mean-Time-to-Failure (MTTF), Mean-Time-to-Repair (MTR), Planned Maintenance Percentage (PMP), maintenance overtime, and annual costs in equipment repairs.
With that said, some of these metrics are difficult to track without a Computerized Maintenance Management Software (CMMS). If you haven’t been monitoring all of these KPIs, don’t worry. Just include the information you have that illustrates why beginning to track different types of maintenance tasks, in conjunction with a preventive maintenance program, could save long-term costs.
2. Assume the role of the expert
Once you have finished drafting your report, prepare to present the information to executive leadership. Here is where many facility managers make a common mistake; they treat the presentation as if they are “asking for a favor.”
Remember: leadership expects you to be the authority on the subject of facility maintenance. So, approach the conversation in exactly that manner. Don’t assume executives know more about the equipment, vendors, and team members you work with every day.
“Keep things objective, and channel your emotions only as necessary–for example, when speaking with passion about a need, that, if not addressed, would impact human health and safety,” says Rounds. “Managers need to make sure that leaders clearly understand the impact of the decision to fund or not to fund the need. Managers are responsible for efficiently, cost-effectively operating, and maintaining facilities that house the processes critical to the profitability of the enterprises they serve.”
Use the A-3 format to lead the discussion and stay away from unimportant issues. Understand the importance of maintenance schedules and preventive maintenance checklists.
3. Evaluate ROI of CMMS
The larger the facility, the more difficult it becomes to manage competing preventive maintenance asset schedules. Assuming your new preventive maintenance program is approved, you will need a system for creating, assigning, and following through on work orders and maintenance work. The easiest way to launch a successful PM program is with the support of a CMMS solution, EAM software, and work order software.
With that said, one of the most common objectives executives have around preventive maintenance programs is inaccurate cost assumptions. Facility managers should calculate the potential return on investment (ROI) on behalf of company leadership: CMMS ROI = CMMS Value - CMMS Cost
The CMMS Value is your expected reduction in maintenance costs after implementing CMMS.
Reduced maintenance costs fall into five categories:
- Increased asset lifespans
- Reduced downtime
- Inventory optimization
- Labor optimization
- Decreased utilities.
Don’t forget to also consider less tangible benefits like improved customer satisfaction, positive testimonials, and company loyalty.
Depending on the size of your organization, and choice of vendor, your one-year ROI might not be very impressive. That’s because many CMMS vendors charge introductory fees for implementation, installation, and equipment.
For this reason, most ROI calculations include one-year, three-year, and five-year intervals. However, new SaaS providers are now delivering quicker ROIs with freemium maintenance apps.
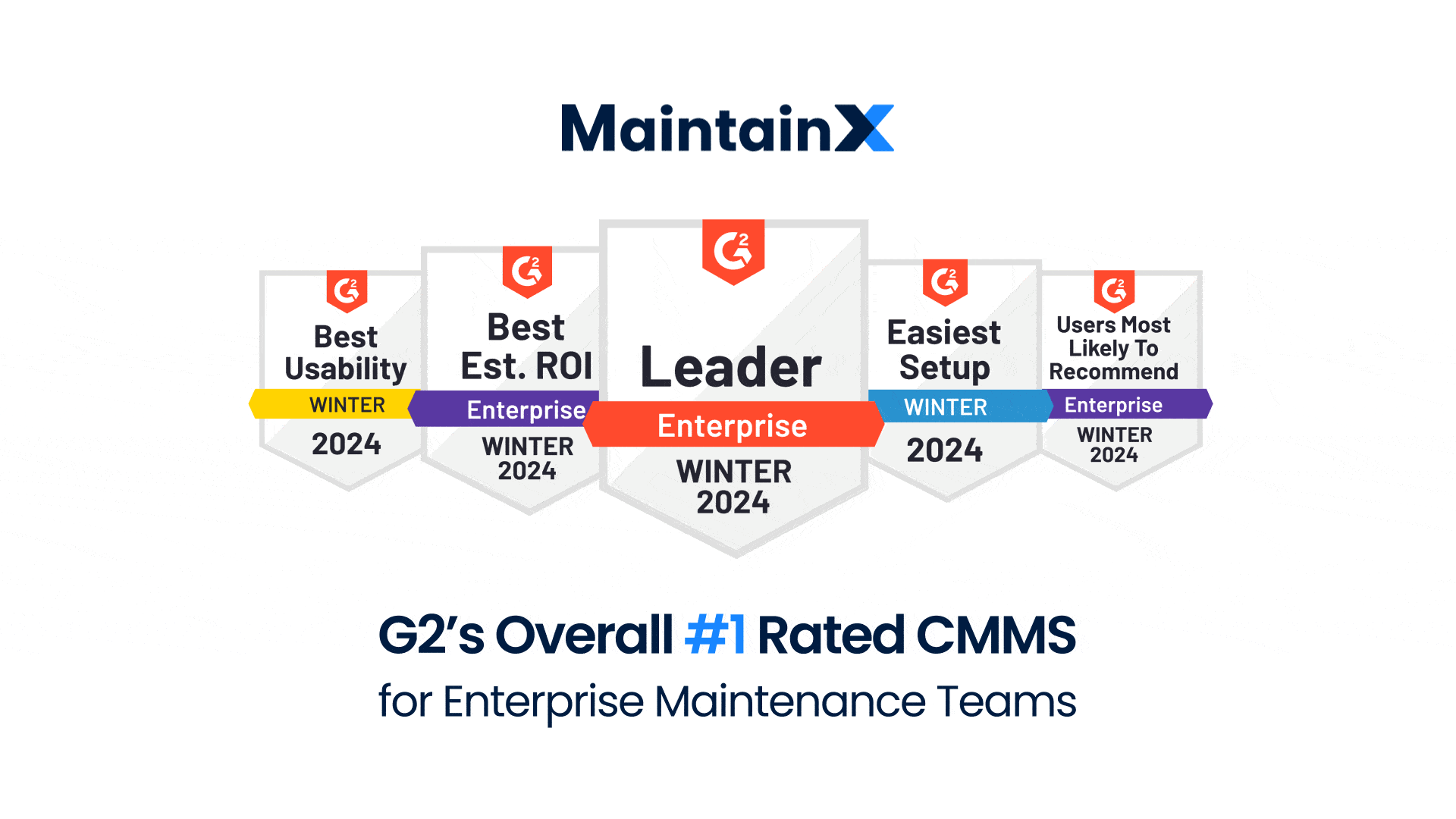
Facility preventive maintenance technicians can access assignments, upload equipment photographs, PM schedules, maintenance requests, chat with managers, and mark orders complete via mobile app with little to no required training. Managing maintenance doesn’t have to be hard on a mobile device. Easily manage maintenance care for pieces of equipment, door locks, and assets on the go. The full-stack software also includes advanced reporting capabilities to help identify spending patterns, root causes, and savings opportunities.
While we truly believe we’re the best in the marketplace, don’t take our word for it. Research customer reviews in app stores, blog articles, and industry Websites when comparing CMMS options. Know which features your organization absolutely needs, and which ones you could do without. Finally, factor the cost of your preferred CMMS solution into your ROI calculations.
Streamline Facility Maintenance
Most organizations that begin implementing comprehensive PM programs experience anywhere from 20 to 200% ROI within 12 months. However, as previously mentioned, executive leadership often isn’t aware of the long-term value of a maintenance management solution.
Decreased downtime, increased productivity, asset longevity, optimized labor hours, and optimized inventory are achievable goals for your facility. Are you currently unable to track work orders in real time? Are you in the process of making a case for preventive maintenance?
If so, we invite you to download our app for free. Companies like Hilton, Marriott, and McDonald's are already streamlining their operations with MaintainX.
FAQs
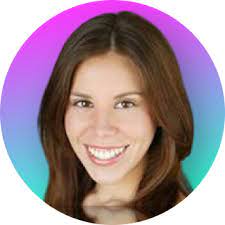