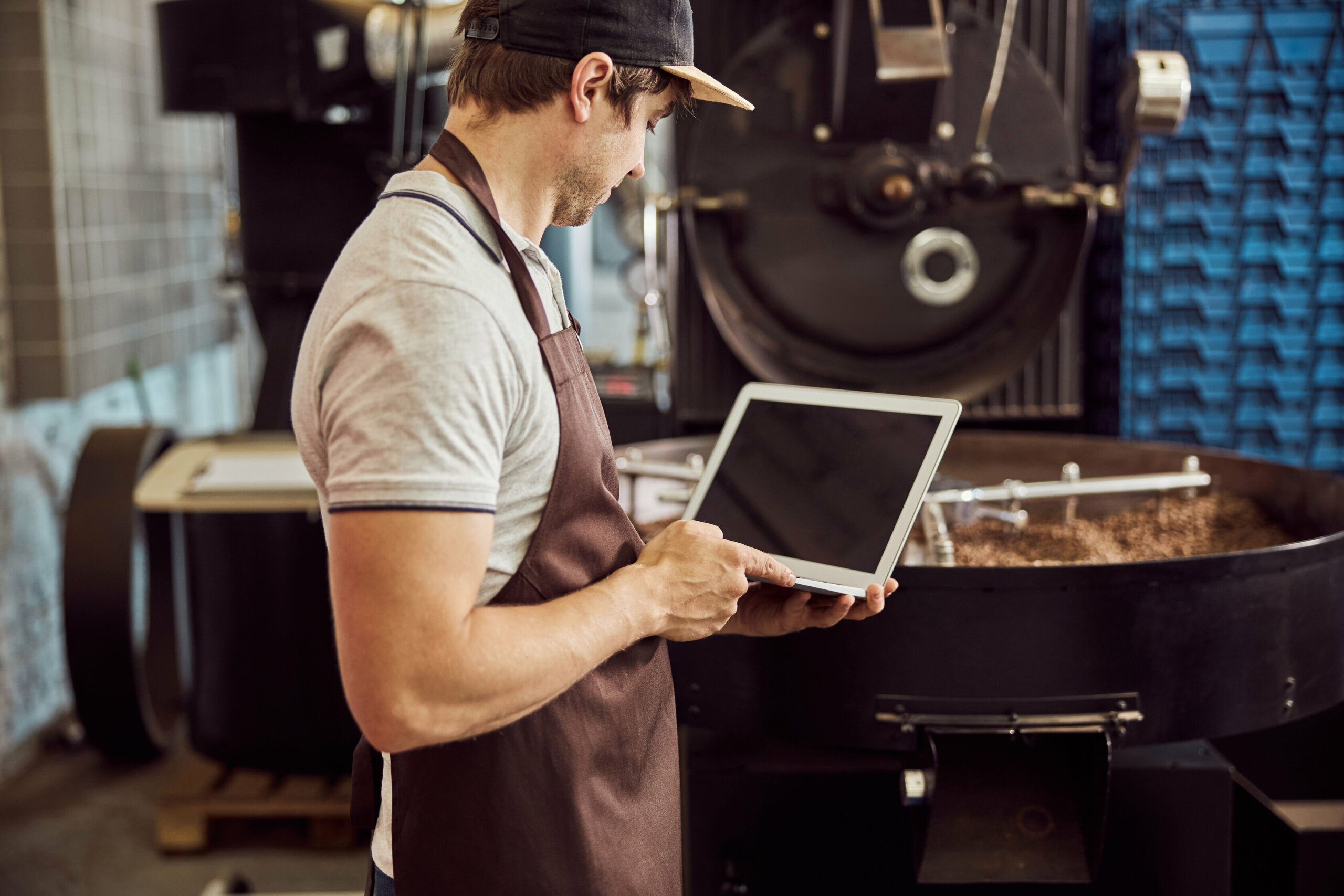
Why do we use abbreviations and acronyms so frequently, especially when referring to maintenance practices?
There are a few reasons why they are so common. First, they help make information digestible, especially when reporting issues or publishing maintenance manuals. Two, they can make more complex terms, practices, and formulas easier to understand.
Acronyms aren’t anything new. They are believed to have originated as far back as ancient Rome to save space and work. However, it seems like there’s an acronym for everything these days. In fact, they may be more prevalent in maintenance and manufacturing than anywhere else. Notably, when it comes to preventative maintenance, maintainability, asset management, and management systems.
To learn more about some of the most common terms in the industry, we’ve put together a list. So whether you’re new to the industry or just want a review, you’ve come to the right place.
“Abbreviations and acronyms are shorter versions of existing words and phrases. They’re designed to save time and take up less space (whether you’re typing or writing by hand), and can even make your writing easier to read.”
GFCGlobal
Common Maintenance Abbreviations and Acronyms
CMMS
The CMMS acronym stands for computerized maintenance management system. CMMS is a software program that helps businesses store, organize, and easily access any maintenance-related data or information. A good CMMS can assist with tracking, data capture, and quickly delivering information to key team members.
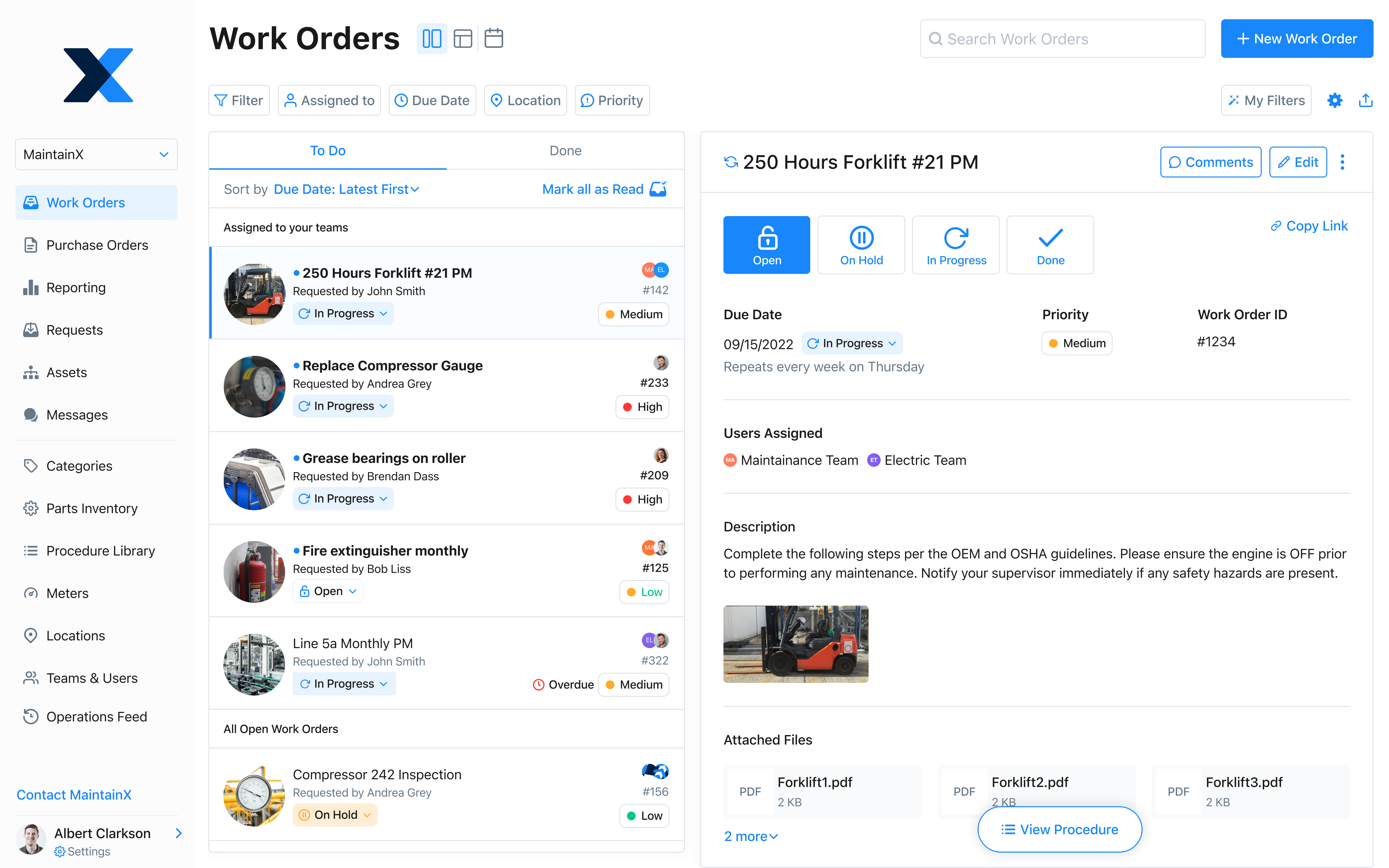
EAM
Enterprise Asset Management Software (EAM) is a type of maintenance software that collects, houses, and analyzes asset data from design to disposal. EAMs help organizations manage every phase of the equipment life cycle by tracking the acquisition of new assets, active asset activity, and the removal of unusable assets. Some CMMS, like MaintainX, are also EAMs.
IT
Information technology can refer to either a profession or a department that handles and utilizes accrued information.
KPI
Key performance indicators are performance measurements to help set goals and targets they want to meet in the coming days, weeks, months, or even years. KPIs help show a company how quickly or slowly it is meeting any designated goals to make adjustments. KPIs help to measure the likes of work order efficiency, downtime, productivity, performance, inventory, maintenance, spending, and more.
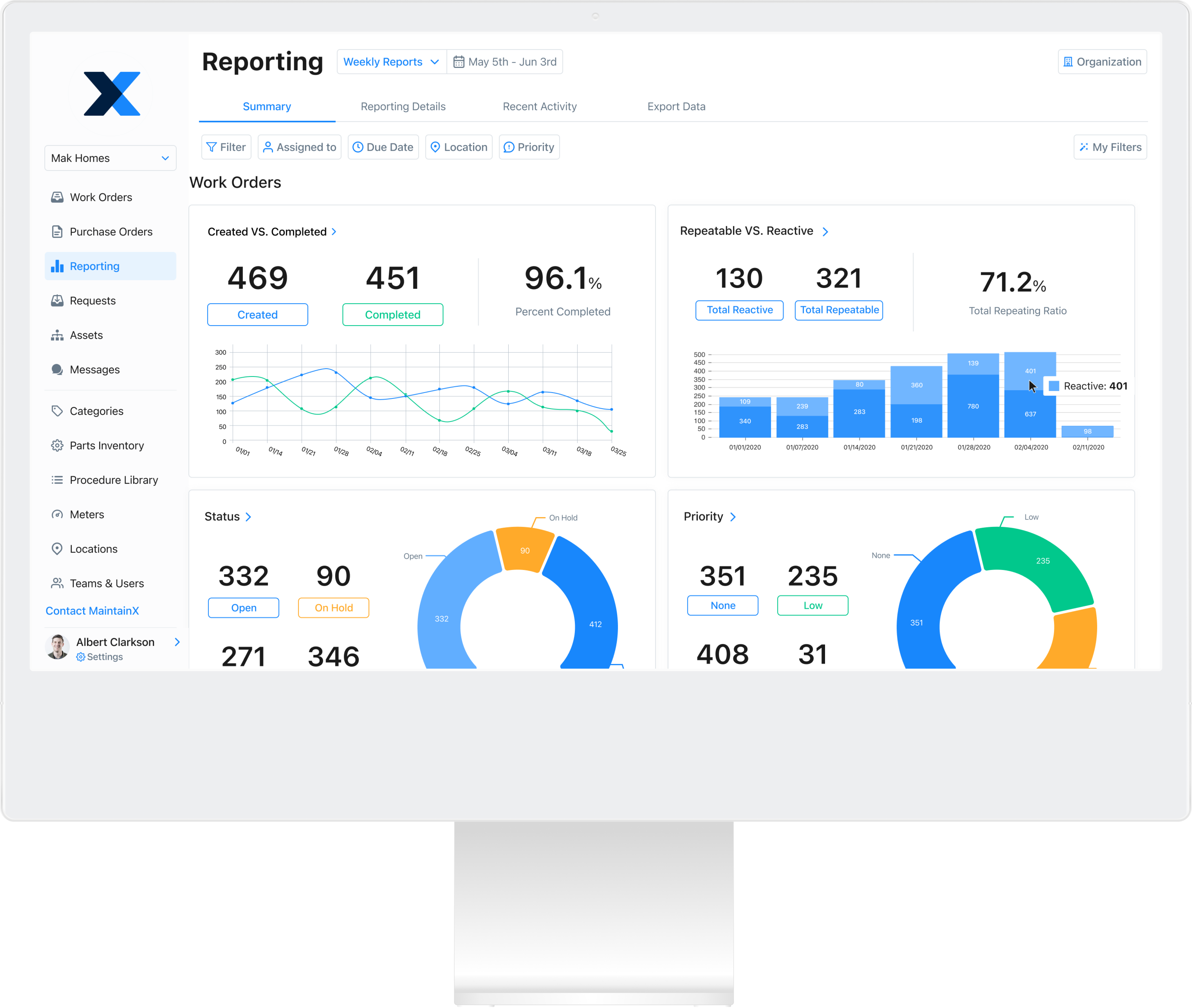
QA
Quality assurance (QA) is defined as planned activities within the manufacturing process that help ensure the product’s overall quality and safety. QA tends to be more preventive and proactive, as the strategy aims to reduce defects and issues by assessing the process rather than the output.
SOP
This one may be obvious: Standard operating procedure. SOPs are step-by-step documentation of repetitive work-related tasks and business processes to achieve desired outcomes. They often accompany preventive maintenance (PM) work orders, inspection audits, and quality-control checklists.
Additional Maintenance Abbreviations and Acronyms
CBM
Condition-based maintenance involves continuously monitoring any assets or equipment and using any data gleaned from this continuous monitoring to better plan preventative maintenance. Though you may think of this as a predictive maintenance tool, team members make sense of the received data and perform maintenance accordingly. Like PDM, this strategy may also involve sensors and other detection technology.
CMRP
Certified Management & Reliability Professional (CMRP) is a credential managed by the Society for Maintenance and Reliability Professionals and accredited by the ANSI National Accreditation Board (ANAB). The CMRP exam tests your ability to apply your knowledge, existing skills, and experience in the maintenance industry.
FMEA
Failure Mode and Effects Analysis (FMEA) assesses the potential causes and impacts of equipment failures. It’s a proactive, data-driven, and team-oriented method for identifying the relative effect of various failure modes on productivity goals. Therefore, FMEA is also referred to as failure modes, effects, and criticality analysis (FMECA), and potential failure modes and effects analysis.
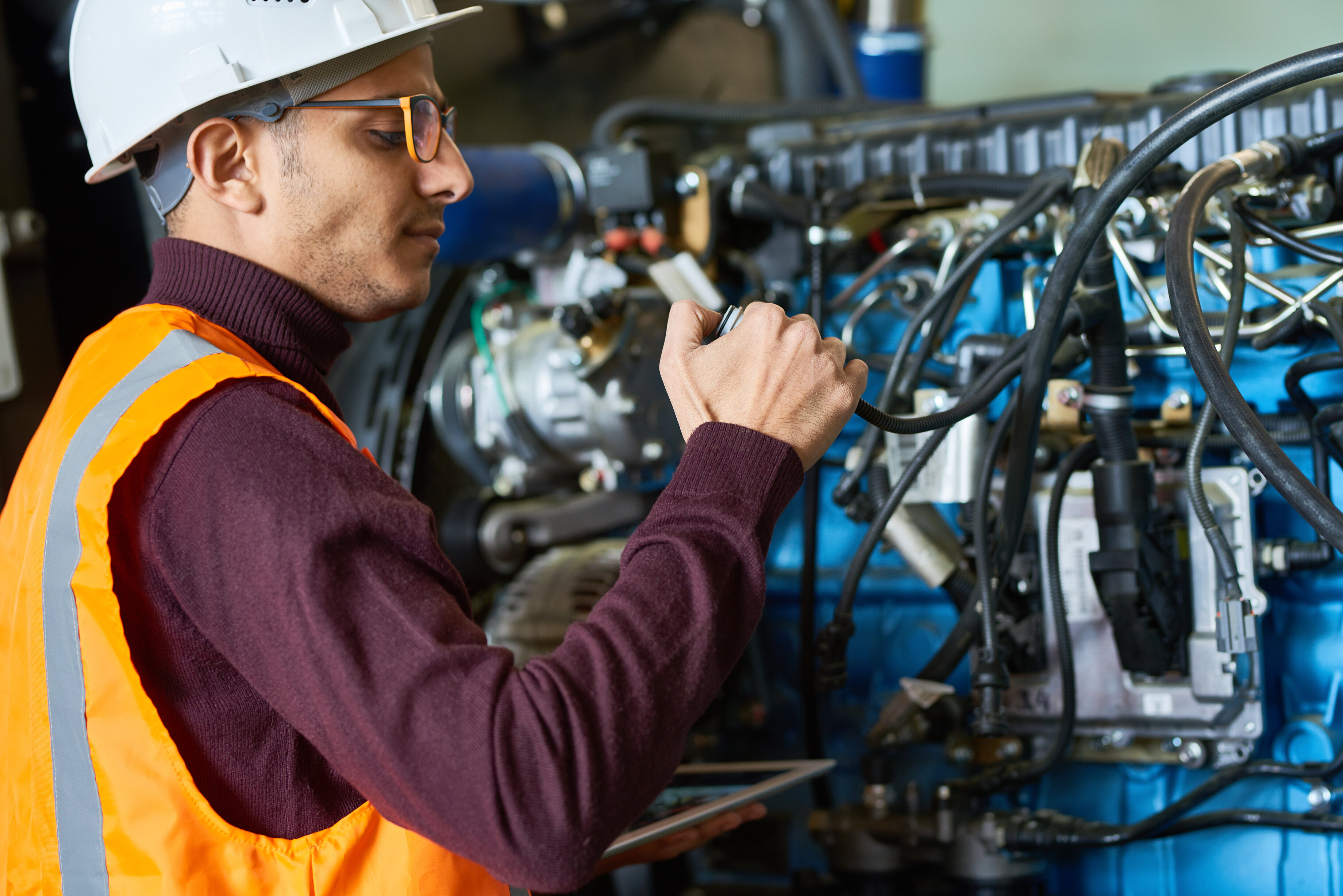
FMS
Facilities management services is a maintenance team or division that works to maintain and repair assets and equipment.
FRACAS
The acronym stands for Failure Reporting Analysis and Corrective Action System. Unplanned downtime costs manufacturers nearly $1 trillion in lost productivity, unsatisfied customers, and revenue each year. FRACAS underscores the importance of identifying maintenance issues early so technicians can make reactive fixes fast.
LDAR
Leak Detection and Repair (LDAR) is the process of identifying leaking equipment and repairing it to minimize emissions. Regulators, like the Environmental Protection Agency (EPA), require manufacturers to follow LDAR guidelines. However, an LDAR program isn’t just to ensure regulatory compliance. It can save money.
MRO
Maintenance, repair, and overhaul is designed to keep equipment and components operational and prevent unplanned downtime. It includes tests, supplies, and equipment to keep equipment operational.
MOC
A Management of Change (MOC) policy is a standard operating procedure that allows management teams to address company-wide changes in a structured way. MOC provides a safe and systematic approach to managing changes in your organization. These changes can include updating equipment, training a new workforce, opening new maintenance facilities, or updating maintenance procedures.
MTBF
Mean Time Between Failure is the average timespan between failures. Maintenance teams and manufacturers use MTBF as a predictor of preventative maintenance. For instance, based on data, companies can zero in on when teams should perform maintenance on equipment and components before failure. Ideally, this will result in less downtime and business interruption.
OEE
Overall Equipment Effectiveness helps to measure manufacturing productivity. More specifically, it helps identify the percentage of time spent in manufacturing that is productive. The higher the OEE score, the more efficient your company’s manufacturing process is. The lower the score, the more stop time, quality issues, and speed limitations.
OEM
An original equipment manufacturer is a company that either builds or designs a product for an end user. It can also refer to a company that provides products to another company, thereby creating a product for the end user. OEM is a popular acronym in the automotive industry. Many suppliers create automobile parts and components.
PdM
PdM is an acronym for predictive maintenance. This type of maintenance uses technology—such as sensors—to monitor equipment and alert management to any problems. This allows management to react quickly and avoid costly unplanned downtime. PDM may also stand for “product data management,” which involves managing design and engineering data in one central location.
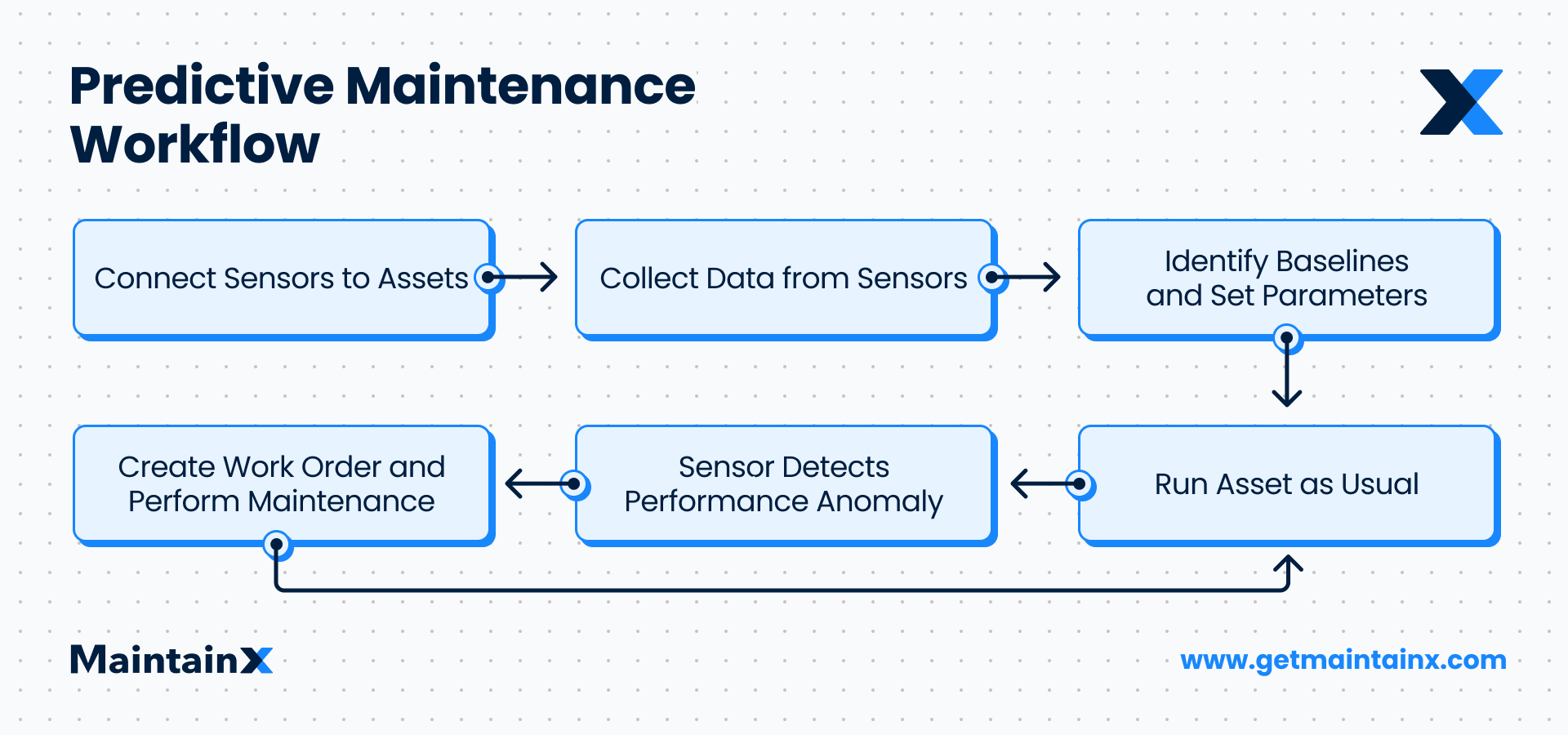
RCM
Reliability-Centered Maintenance (RCM) is a corporate-level maintenance strategy designed to optimize maintenance programs by establishing safe minimum levels of equipment upkeep. RCM emphasizes matching individual assets with the maintenance techniques most likely to deliver cost-effective outcomes. The successful implementation of RCM enhances reliability, equipment uptime, and company savings.
SCADA
This is the acronym used for Supervisory Control and Data Acquisition. Organizations use a computer system to gather and analyze equipment data in real time. Industries such as transportation, oil and gas, energy, waste control, water, and telecommunications use SCADA systems to monitor and control complex machinery.
TPM
Total productive maintenance describes a process that is designed to maximize productivity in a workplace. This can be done through efficient use of space and equipment and via the cooperation and buy-in of the entire workforce.
MaintainX, CMMS, and Maintenance Abbreviations and Acronyms
We could go on and on. Using and understanding acronyms and abbreviations is just one way to speed up all things maintenance related. Check out MaintainX’s Learning Center for more explanations about common maintenance acronyms and abbreviations.
And then check out MaintainX. It’s free.
FAQs
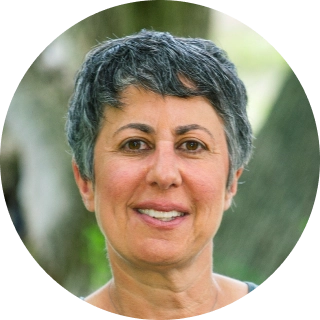
Caroline Eisner is a writer and editor with experience across the profit and nonprofit sectors, government, education, and financial organizations. She has held leadership positions in K16 institutions and has led large-scale digital projects, interactive websites, and a business writing consultancy.