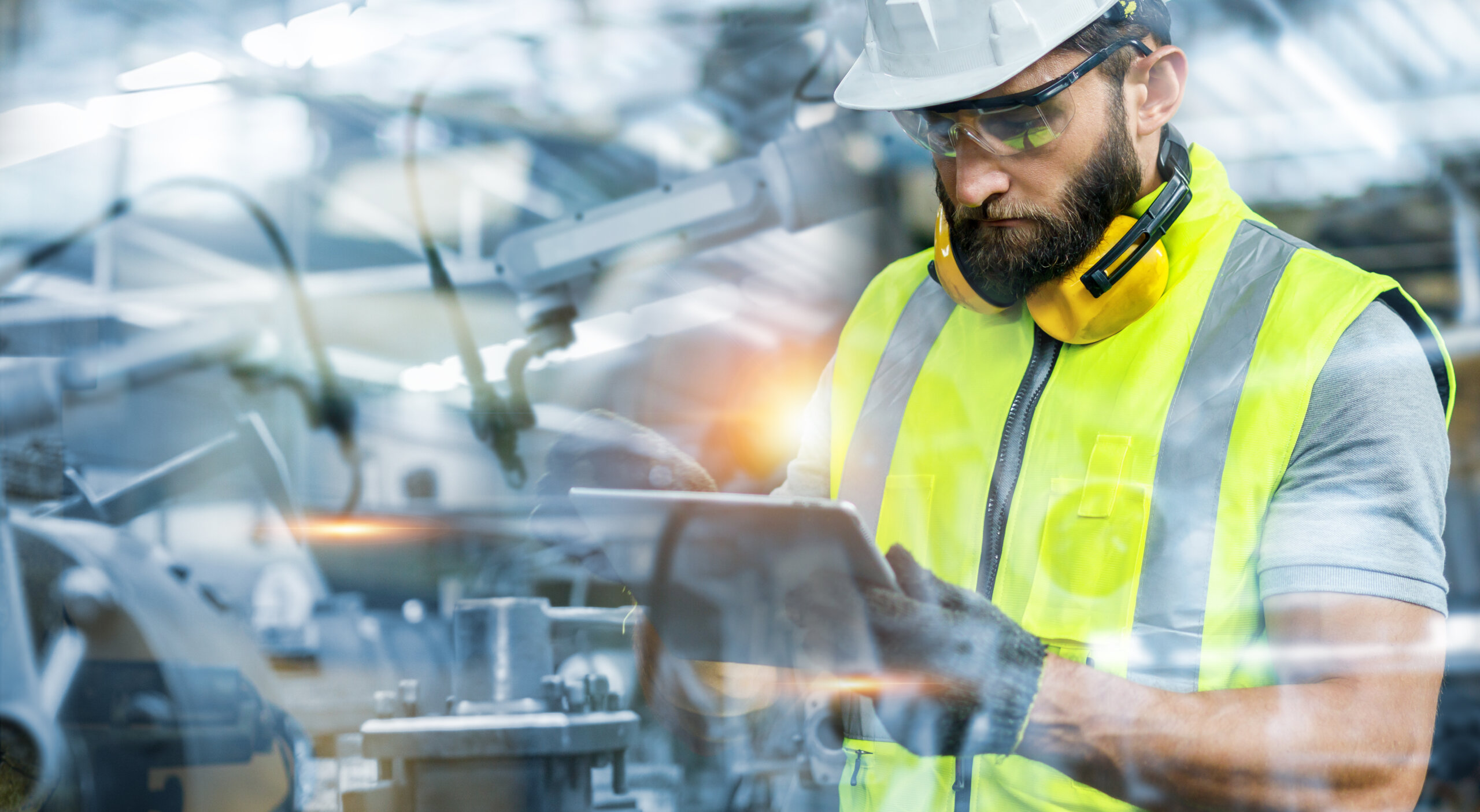
Preventive maintenance (PM) is the practice of running regular maintenance activities on assets to mitigate breakdowns and unplanned downtime. In other words, fixing minor problems before they become big ones.
Studies show organizations can save between 12% and 18% in costs by implementing preventive maintenance strategies, with some companies reporting as much as a 30% decrease in unplanned downtime. The combination of slowing down asset deterioration, reducing downtime, and increasing productivity caused one telecommunications firm to experience a 545% ROI after committing to preventive maintenance programs.
While approximately half of all organizations follow preventive maintenance programs, many SMBs still get by with reactive maintenance operations. Given the apparent benefits, you might wonder why they don’t all just switch to preventive maintenance.
Perhaps it’s because preventive maintenance requires smart scheduling and asset tracking, both of which are hard to execute without the right tools. Managers who use Excel spreadsheets to juggle work orders and maintenance operations for hundreds of assets often feel overwhelmed. And those who rely upon whiteboards or paper stacks may forgo asset tracking altogether.
Understandably, most complex organizations can’t pull off preventive facility maintenance without a Computer Maintenance Management System (CMMS) in place.
Unfortunately, simply adopting a CMMS might not solve the problem either, as traditional CMMS solutions come with steep learning curves, complex interfaces, and expensive invoices. The good news? More modern free CMMS systems remove such obstacles for industries across the board. In fact, one of the best digital maintenance solutions available right now is free for organizations of all sizes.
“Computerized maintenance management software is a tough one to argue against with continued pressure on materials handling, equipment uptime, and performance efficiency without interruption. In fact, it can make both maintenance and operations better.”
MMH.com
7 Reasons to Try MaintainX’s Free CMMS Software Program
Are you feeling skeptical? We understand.
Many of us internalize the belief that more expensive equals better:
Filet mignons taste juicer than ribeyes. Lamborghinis drive smoother than Hondas. And Bose headphones sound richer than off-the-shelf earbuds.
However, the cost-quality rule doesn’t always apply to modern computerized maintenance management software. Today’s cloud-based solutions are often cheaper AND more user-friendly than traditional legacy options. MaintainX is the top-rated maintenance management system designed for mobile devices.
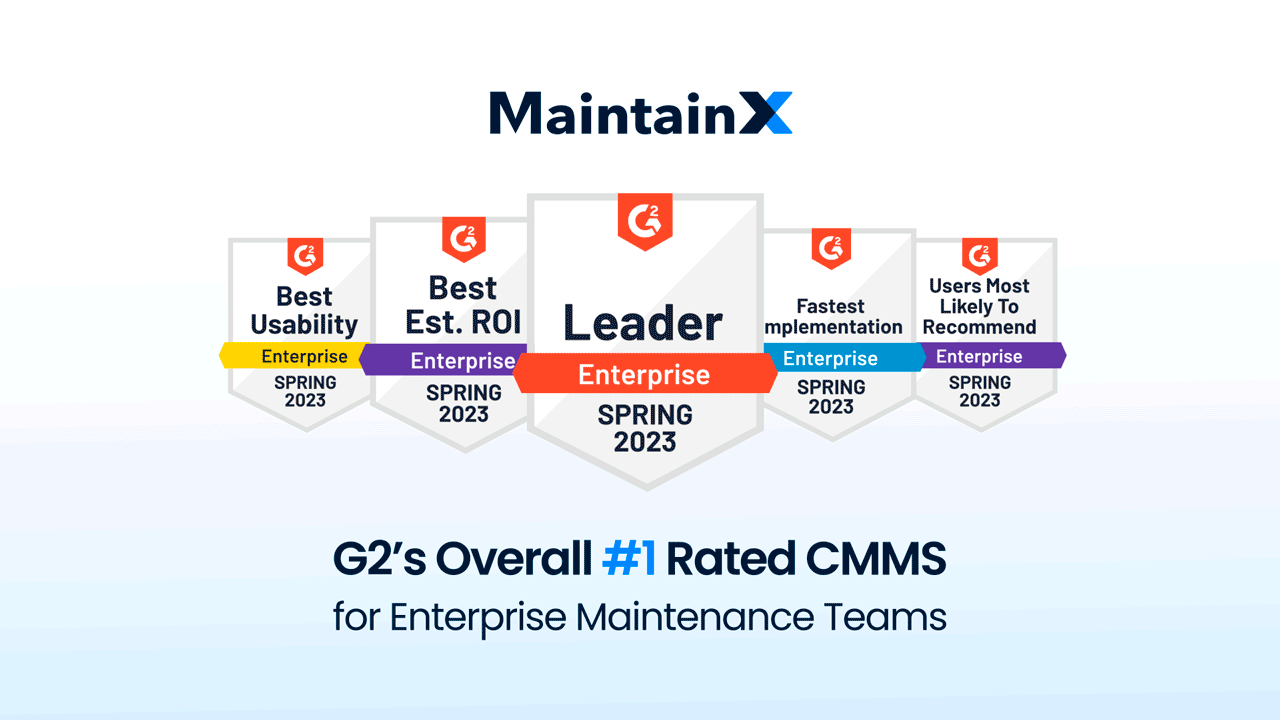
While the MaintainX paid version contains powerful premium features, our free version packs a strong punch. We’ve combined enhanced functionality with the simplicity of modern smartphone apps to deliver what we believe is the best work order software product on the market―free or not.
Here are seven reasons to try MaintainX:
1. Super Easy to Use
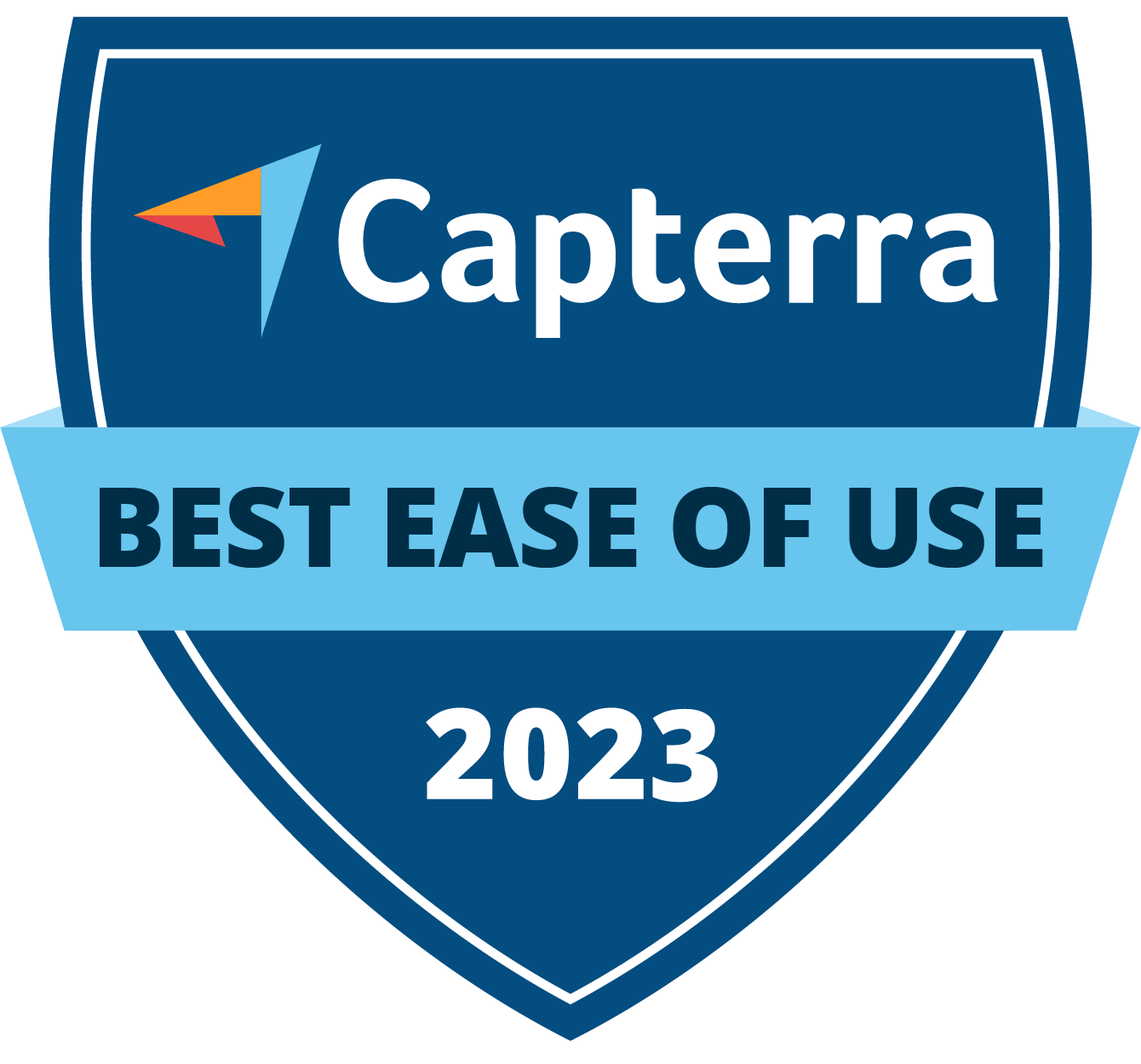
For a CMMS that appears simple, MaintainX does a lot. When designing our native-first mobile application for iOS and Android, we aimed to create an intuitive user experience precisely because we understood who would use MaintainX the most.
However, an intuitive user experience was definitely not what we discovered after surveying the marketplace. Most of today’s computerized maintenance management system vendors built their apps for desktop computers before reprogramming and redesigning them for smartphones.
Not surprisingly, these user experiences are clunky, dated, and complicated.
With MaintainX, users don’t have to sacrifice features for simplicity. Our smartphone, iPad, and desktop app allows managers to:
- Create reactive and preventive maintenance work orders via the work order module and directly from chat. This means that if a user reports an incident, a manager can instantly create a work order based on that message.
- Assign recurring maintenance tasks to both teams and individuals.
- Monitor progress by maintenance category, priority level, and worker, to name just a few of our filters.
- Analyze maintenance costs and KPIs for greater efficiency and savings.
- Hold text conversations with team members in real time.
When we say that anyone with a smartphone can download the app and get started now, we aren’t kidding. The app really is that easy to use. Don’t just take our word for it, though. Capterra currently names us “Best Ease of Use,” and G2 names MaintainX “Most Implementable” and “Easiest Setup.”
2. Chat with Workers in Real Time
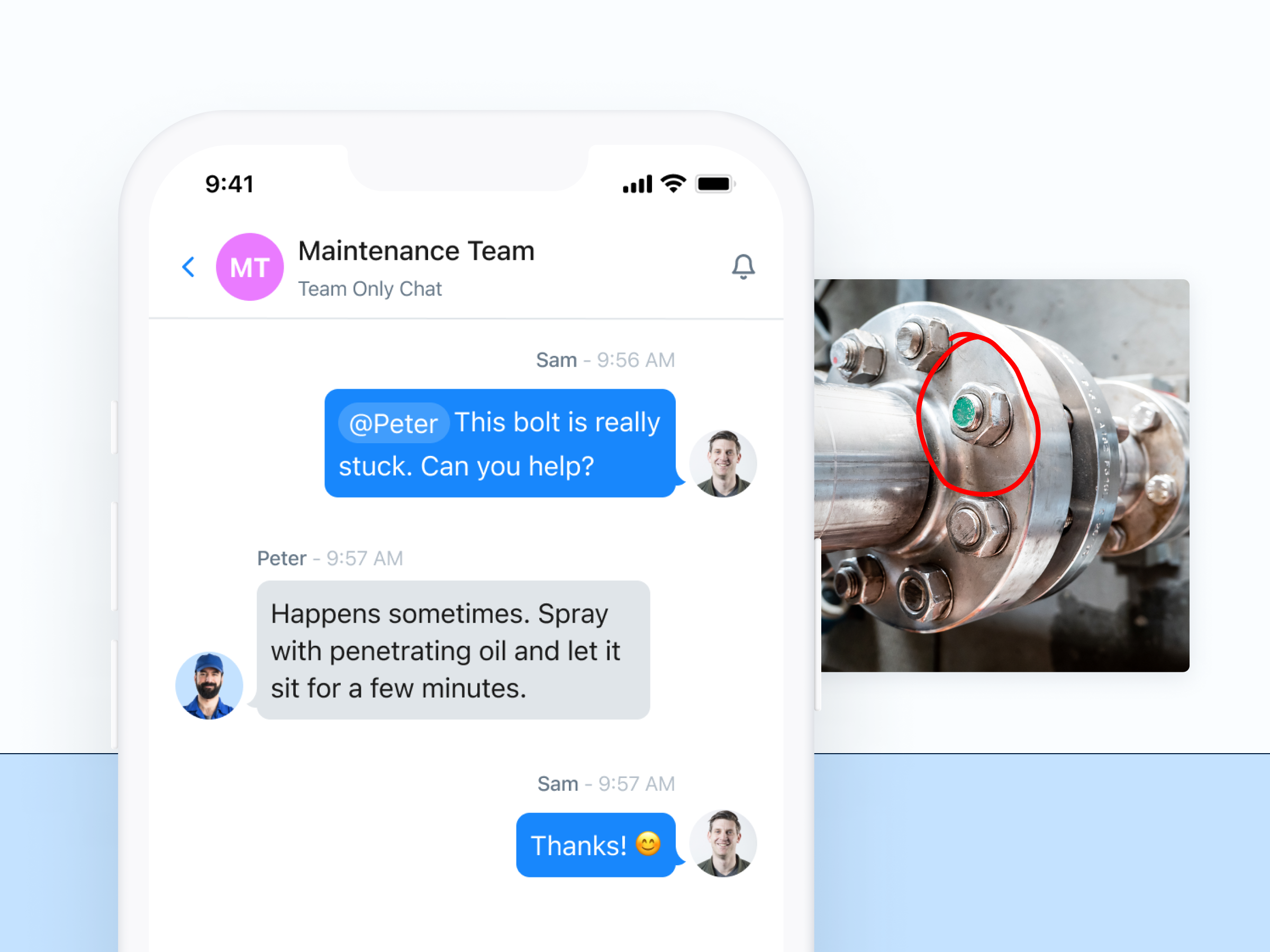
How does your maintenance team communicate? Do you ever lose track of important messages or maintenance requests in email threads, voice mails, text messages, or worse, on paper? Do you waste time repeating the same information over and over again?
With MaintainX, team members can chat in-app with one another in real time. You can even organize your conversations by individual team member, teams, and projects.
You can also communicate within specific work orders via the app’s comment feature. With this, workers can quickly reference essential notes, ask questions, and keep track of project guidelines, troubleshooting tips, and any other nuances with the task at hand.
Of all of MaintainX’s capabilities, messaging pleasantly surprises our users the most. Put simply, this will become the communication hub of your team. You won’t know how you managed your team without it.
3. Manage Assets Easily in the Cloud
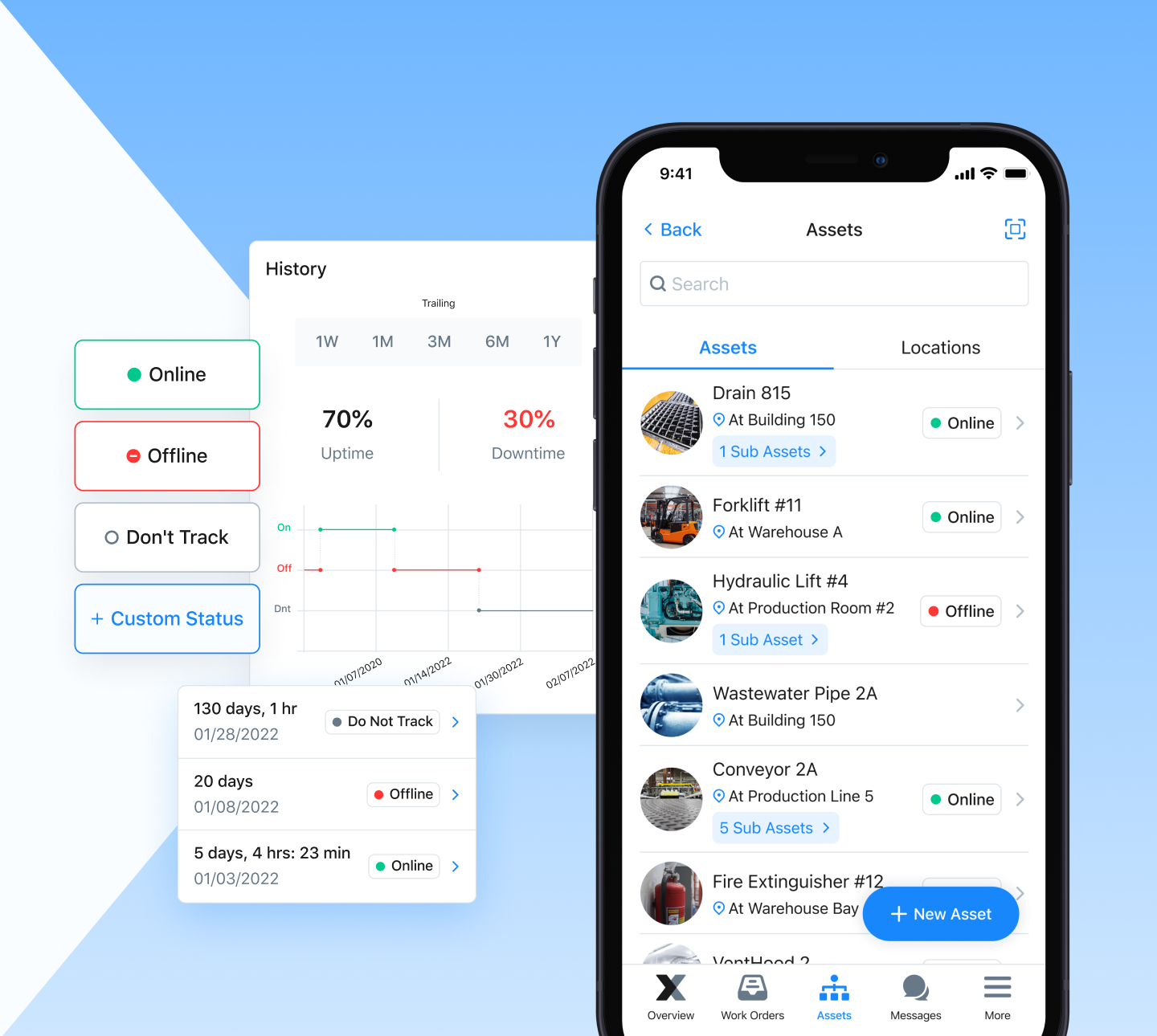
Another compelling reason to try MaintainX? It will help simplify your asset management. Whether your organization has 20 or 2000 assets, you can catalog them in our cloud-based software for free. Of course, cataloging assets is only one step, and you need a streamlined management system. MaintainX scans QR and bar codes to make it easy to look up assets.
Are your assets currently organized in an Excel spreadsheet? We will even help you import the information into our platform. Comparatively, most CMMS solutions charge a monthly fee to catalog more than a few dozen assets.
4. Upload Photos and Collect eSignatures
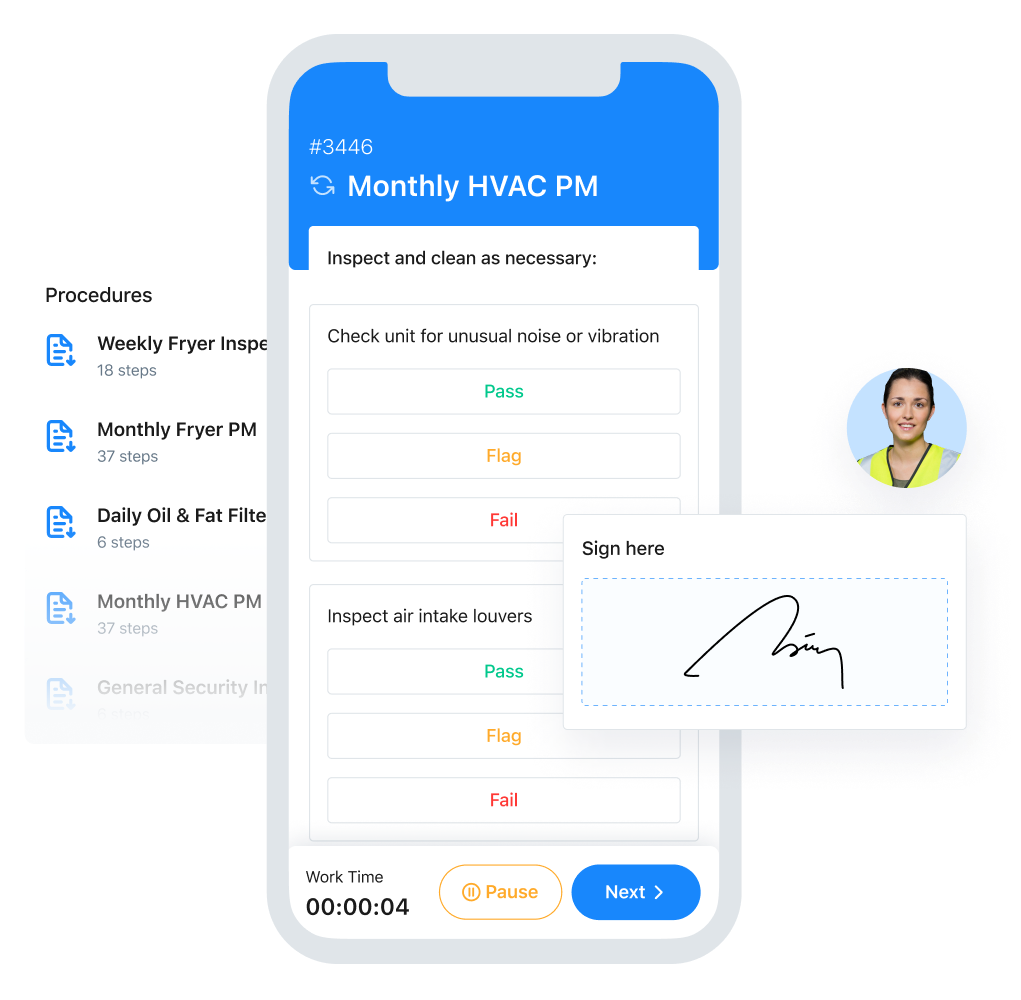
They say a picture is worth a thousand words. In the maintenance world, the phrase takes on fresh meaning. Every worker will eventually run into an unanticipated equipment failure they don’t know how to handle or don’t want to describe in a lengthy email.
Photos can convey what can’t easily be explained. MaintainX allows workers to upload photos directly into digital chat threads for real-time troubleshooting. Managers can further clarify procedures by uploading equipment photos directly into individual work orders. Even more, techs can draw on and annotate photos to add details and emphasis.
Photos can clarify maintenance work and asset and inventory management. Cataloging photos of equipment, spare parts, and other assets can make identifying them on the shop floor and in storage easier.
5. Conduct Cost Analysis with Robust Reporting
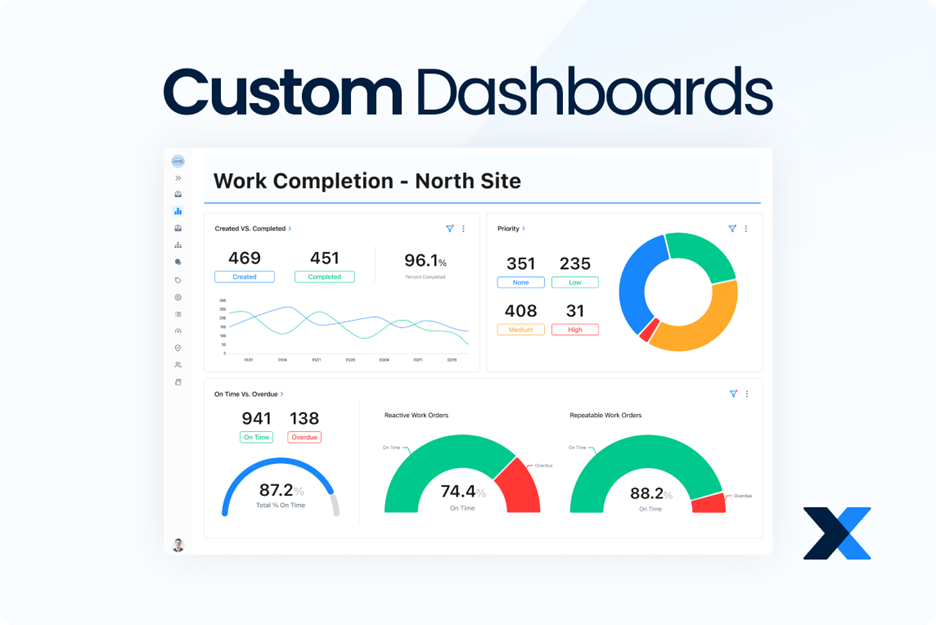
Thorough cost analysis programs are often what separate run-of-the-mill maintenance teams from world-class maintenance teams. While our Reporting feature is behind a paywall, it’s worth knowing about it after experiencing gains with our freemium plan.
With MaintainX Reporting, you can gain immediate insight into critical metrics and quickly identify areas to improve. Reporting enables you to make real-time, data-driven decisions. You can optimize your maintenance planning and track costs over time to identify spending patterns, root causes, and savings opportunities. With MaintainX Reporting dashboards, you can track KPIs and metrics like:
- Mean Time to Repair (MTTR)
- Inspection checks
- Preventive Maintenance vs. Reactive Maintenance Work Order Completion
- Work Orders by Status and Priority
Note: Reporting is only accessible on desktop.
6. Use Well-Designed Forms
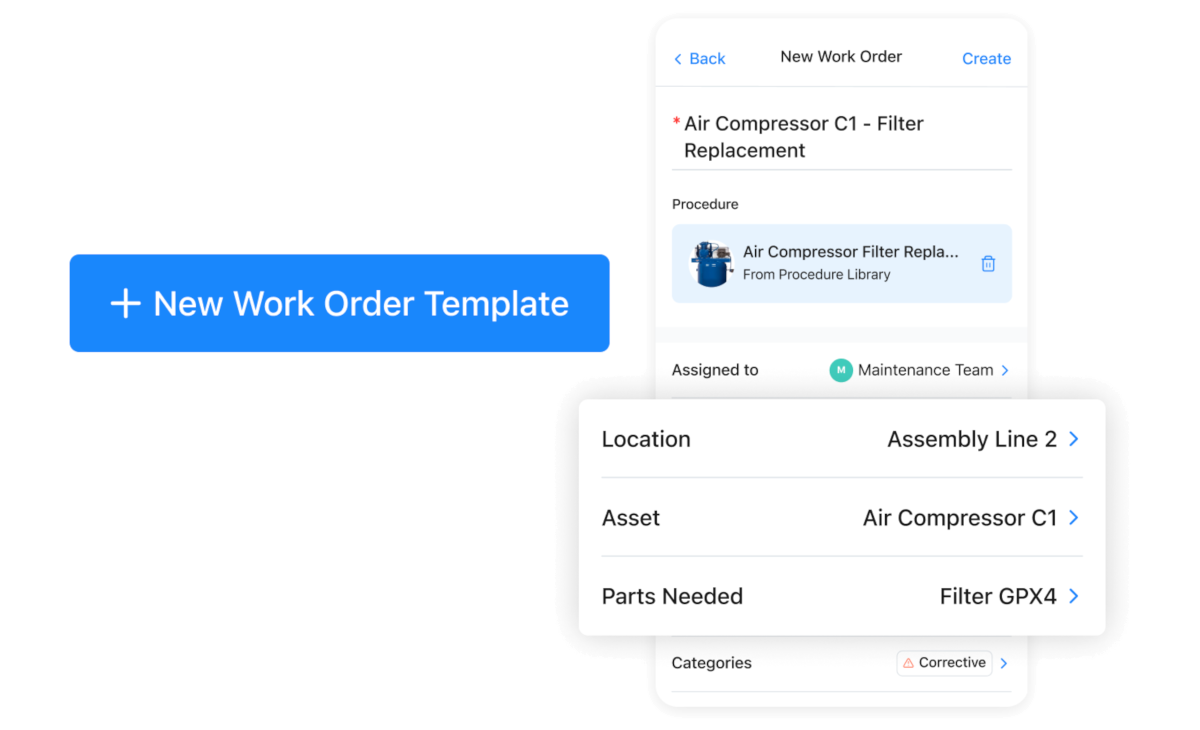
Are you a sucker for beautiful checklists? Yeah, we are too. However, it’s not only about aesthetics. Research shows that people pay more attention to documents that are legible, organized, and visually appealing.
MaintainX provides several form item options for managers wanting to capture important information across your operation. The app also houses a template and global procedure library with checklists and standard operating procedures (SOPs) across industries and use cases. SOPs help eliminate trial and error in the workplace. While it’s normal for team members to use different approaches to solve similar problems, SOPs establish a consistent approach, ensuring workers stick to tried, tested, and dependable solutions.
At the risk of sounding over-confident, MaintainX work orders may be the easiest procedures and checklists you have ever made.
7. Experience Foolproof Accountability
Finally, MaintainX’s facility management software provides maintenance teams with foolproof accountability of digital audit trails. Managers can see team members sign off in real time, and maintenance workers can experience the satisfaction of digitally completing action items (i.e., no more time-consuming paper trails).
Digital audit trails are crucial for troubleshooting, getting offline equipment up and running, and root cause analyses. They function as robust records of activities that facilitate investigations and problem-solving. In addition, they simplify the process of proving compliance. By digitizing compliance activities with CMMS work orders that store work histories, teams can eliminate the need to compile compliance records after the fact.
MaintainX: Where Simplicity Meets Quality
As you know, expensive doesn’t always mean better. Some might even say that “the best things in life are always free.” MaintainX’s more advanced features are fee-based. However, our free CMMS software program provides as much, or more, value than similar paid platform providers in the marketplace. However, don’t take our word for it.
Use MaintainX to streamline workflows, optimize maintenance operations, and prevent breakdowns. Get the best out of both our web-based and mobile apps with features such as:
- Streamlined work order management
- Barcodes and QR codes for inventory management
- Parts management modules to organize your spare parts
- Simplified equipment upkeep with maintenance scheduling with push notifications
- Digital work requests
And much more. Download MaintainX now, and try us out for yourself. It’s free!
FAQs
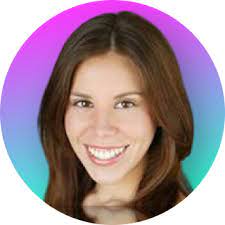