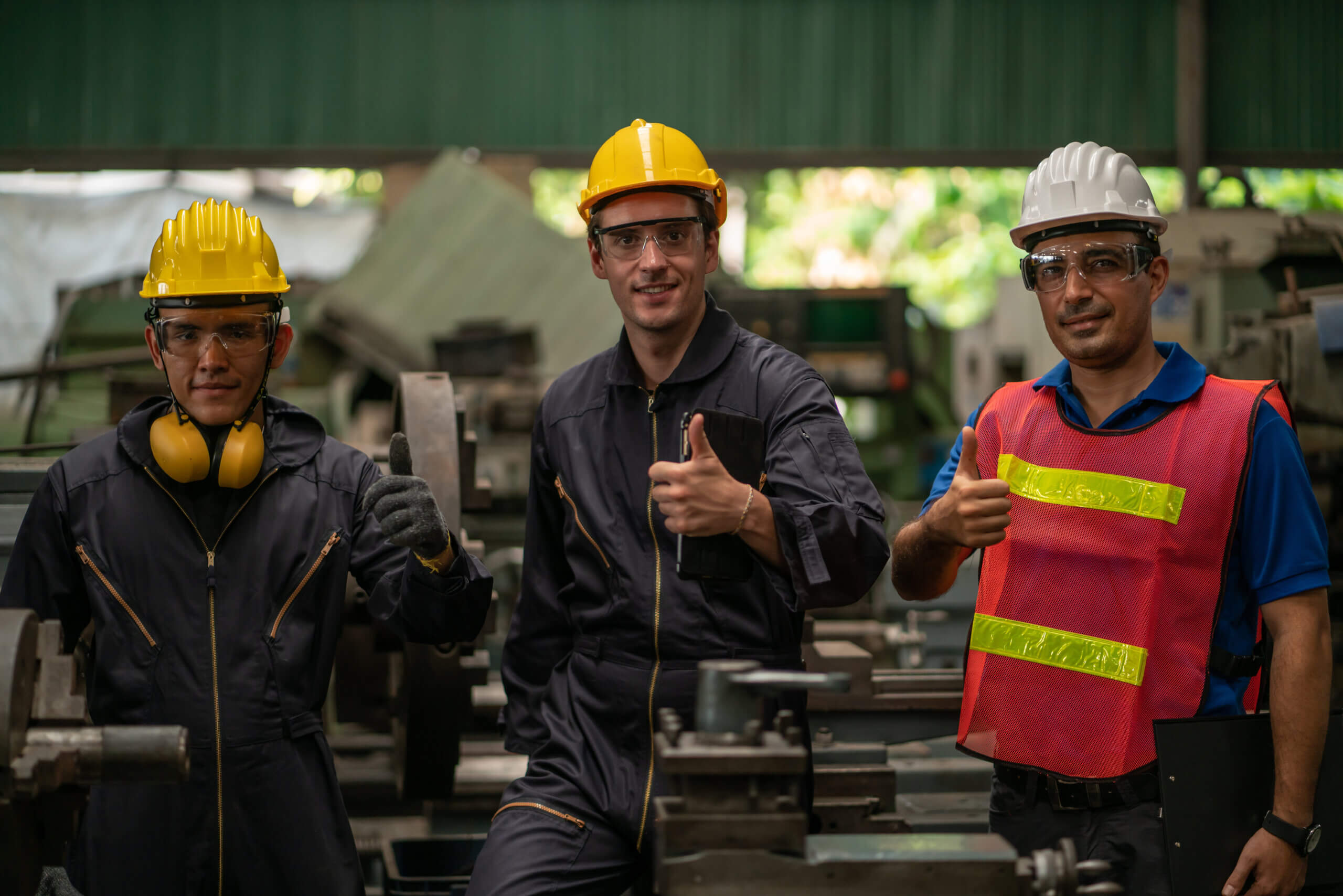
It will be a long while before the world fully recovers from the impact of the COVID-19 pandemic. Beyond supply chain disruptions, consider labor shortages. According to the U.S. Bureau of Labor Statistics, nonfarm payroll employment increased by 315,000 in August 2022.
However, the increased demand has caused a labor shortage. The U.S. Chamber of Commerce cites four reasons for the labor shortage in the current U.S. economy:
- Increase in savings
- Early retirements
- Lack of access to childcare
- Preference for entrepreneurship
The pandemic may have triggered the “great resignation,” but the factors leading to this low labor force participation rate have been brewing for about a decade. Furthermore, manufacturers reported that finding the right talent is now 36% harder than it was in 2018. That’s even with the unemployment rate nearly doubling the supply of available workers.
“Record job openings and quit rates highlight employees’ growing emphasis on feeling valued by their organization, supportive management, and flexibility and autonomy at work.”
McKinsey
These days, the government is working to alleviate labor supply challenges. But it may be a while before we see the worker shortage return to pre-pandemic levels.
Just look at the number of job openings on LinkedIn, from non-profits to private companies, open to those with high school diplomas and advanced degrees. Conversely, the number of unfilled jobs, from food service to industrial maintenance, continues to rise.
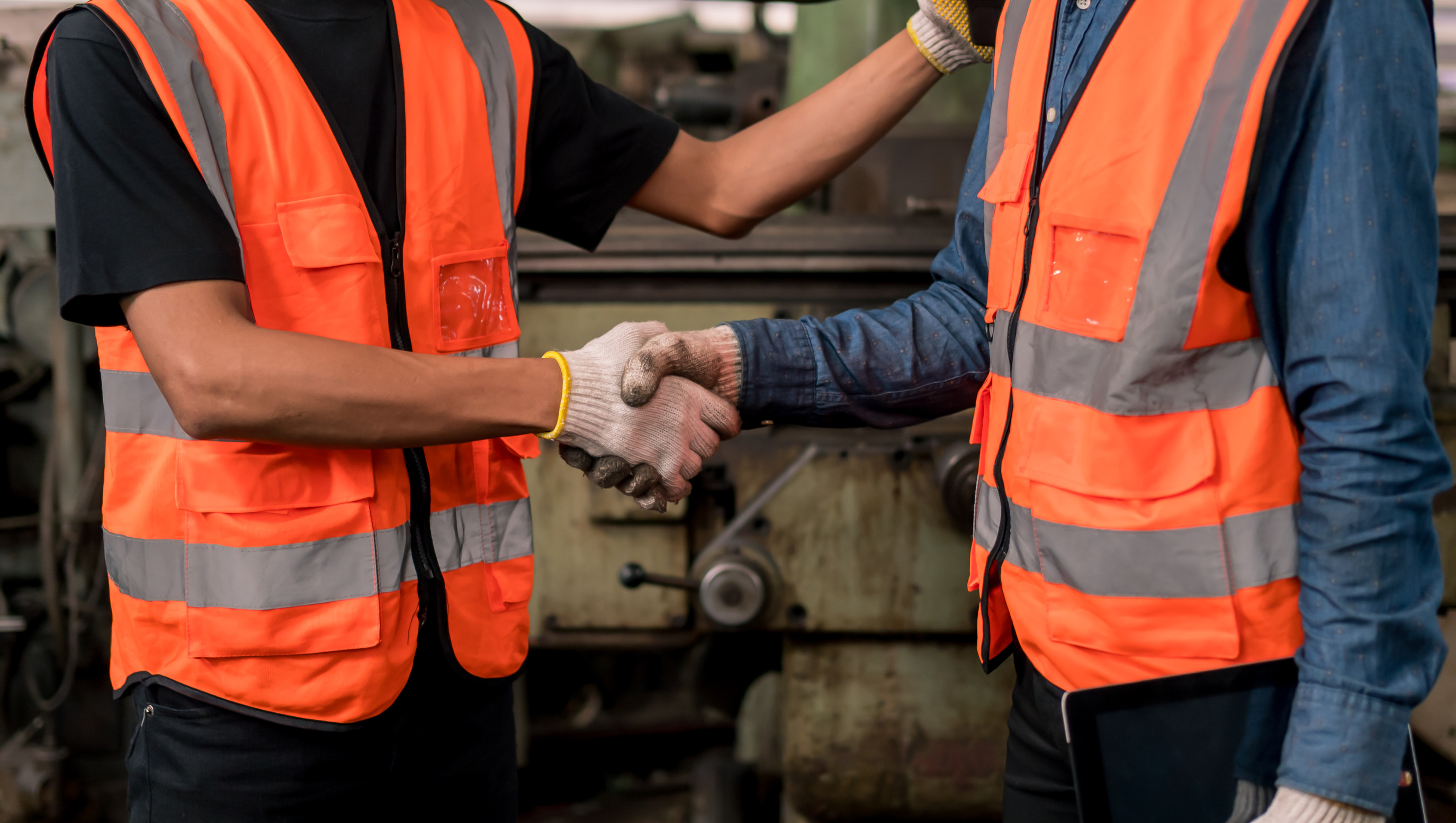
Labor Shortages in Manufacturing
The manufacturing sector is no different. In fact, you may need help finding and retaining maintenance technicians, service providers, and managers. Here are some stats regarding the industry as a whole:
- According to Forbes, Deloitte estimates a shortage of more than two million American manufacturing workers by 2030, representing an opportunity cost of $1 trillion dollars per year.
- According to the same survey, almost 45% of U.S. manufacturers turned down business opportunities due to a need for more workers.
- The National Association of Manufacturers has expressed concern that 2.1 million manufacturing jobs could remain unfilled by 2030.
- In addition to slowing down manufacturing competitiveness, Deloitte predicted in 2021 that the opportunity cost of this manufacturing workforce shortfall to be about $1 trillion.
“Many manufacturers still struggle to fill critical jobs, and companies should continue to find ways to broaden the talent pipeline, foster inclusive cultures, and create ongoing upskilling programs for the digital future of manufacturing.”
Deloitte
Okay. That sounds pretty bad. And you’re probably wondering: if things are this bad for the industry, what hope does my factory have? It’s not all doom and gloom, though. Wading through the talent pool is challenging, but finding and retaining skilled workers is possible.
5 Strategies to Deal with Labor Shortages
You caHere are a few initiatives we’ve considered to reduce the impact of the manufacturing labor shortage. You can adapt the following strategies to suit your situation as you work to tackle the labor shortage in your industry.
1. Use a CMMS
CMMS (computerized maintenance management system) is a software solution that streamlines and automates maintenance processes. Deploying a CMMS can eliminate the need for your existing technicians to spend time on reactive maintenance tasks and empower them to complete preventive maintenance tasks more efficiently.
With MaintainX, for example, it’s easier to schedule planned maintenance, create work orders, assign procedural maintenance, and communicate with technicians rather than using a spreadsheet. In addition, the CMMS automates scheduling and preventive maintenance. And you can monitor maintenance task completion through real-time data, procedure scoring, and key performance indicators (KPIs).
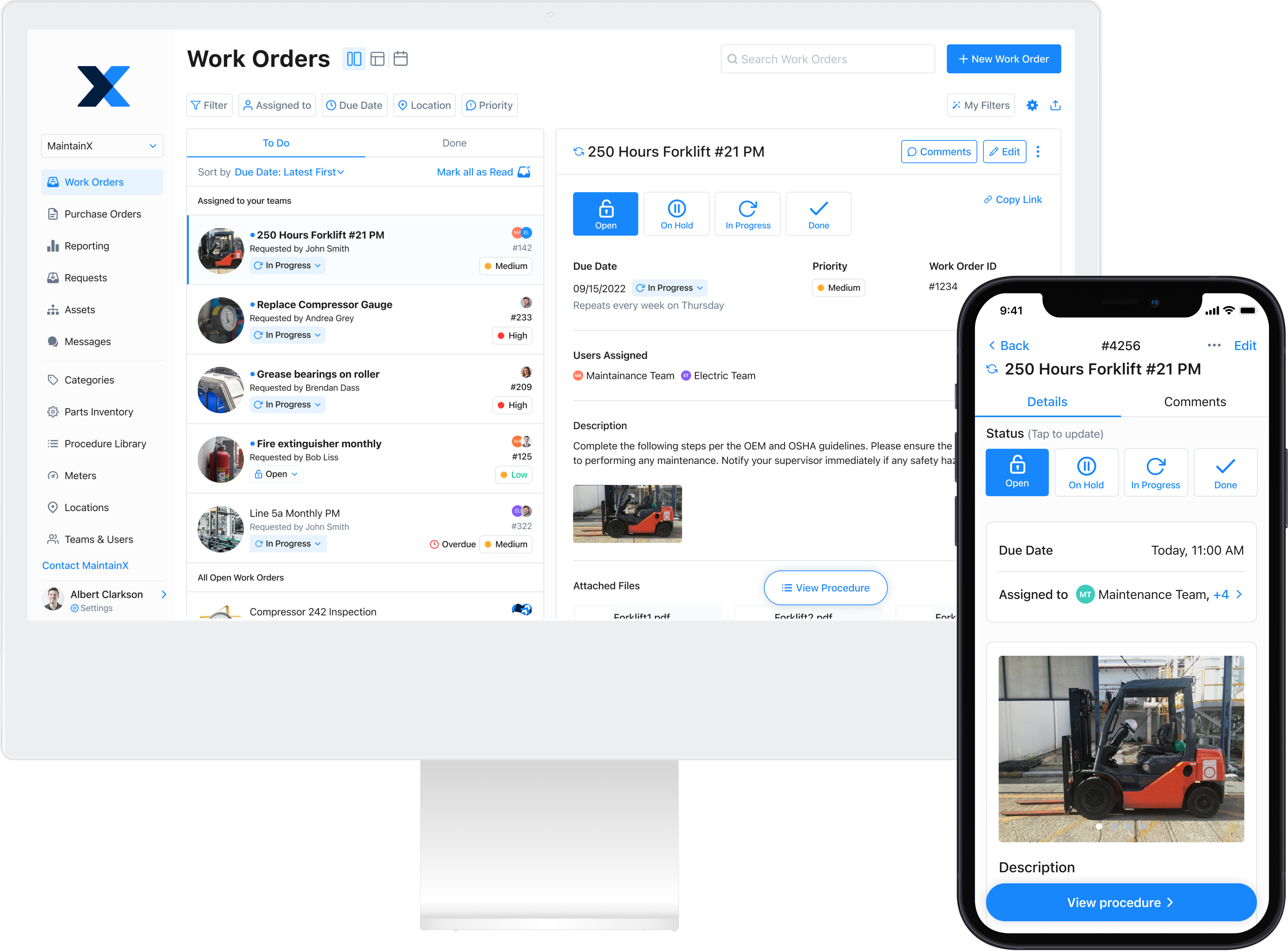
2. Invest in Training
Even with the labor shortage, training current employees is an ongoing need. Many employees seek other opportunities because they feel unfulfilled and underutilized. Young professionals with opportunities to grow within a company are more likely to stay.
If you’re looking for new talent, investing in retaining that talent is critical. Maintenance professionals want to upskill because they see automation as a threat to their employment.
Employee retention isn’t the only benefit of training your staff, though. Training programs also allow your staff to sharpen their maintenance skillset. Training your team on more advanced processes like predictive maintenance, for example, will help improve their work and reduce your downtime. If this sounds like a lot of effort, you can put in place apprenticeship programs encouraging younger workers to learn from more experienced employees.
Whether you train your teams to use new technologies like a CMMS or help them earn maintenance certifications, upskilling will help your workers feel secure in their jobs.
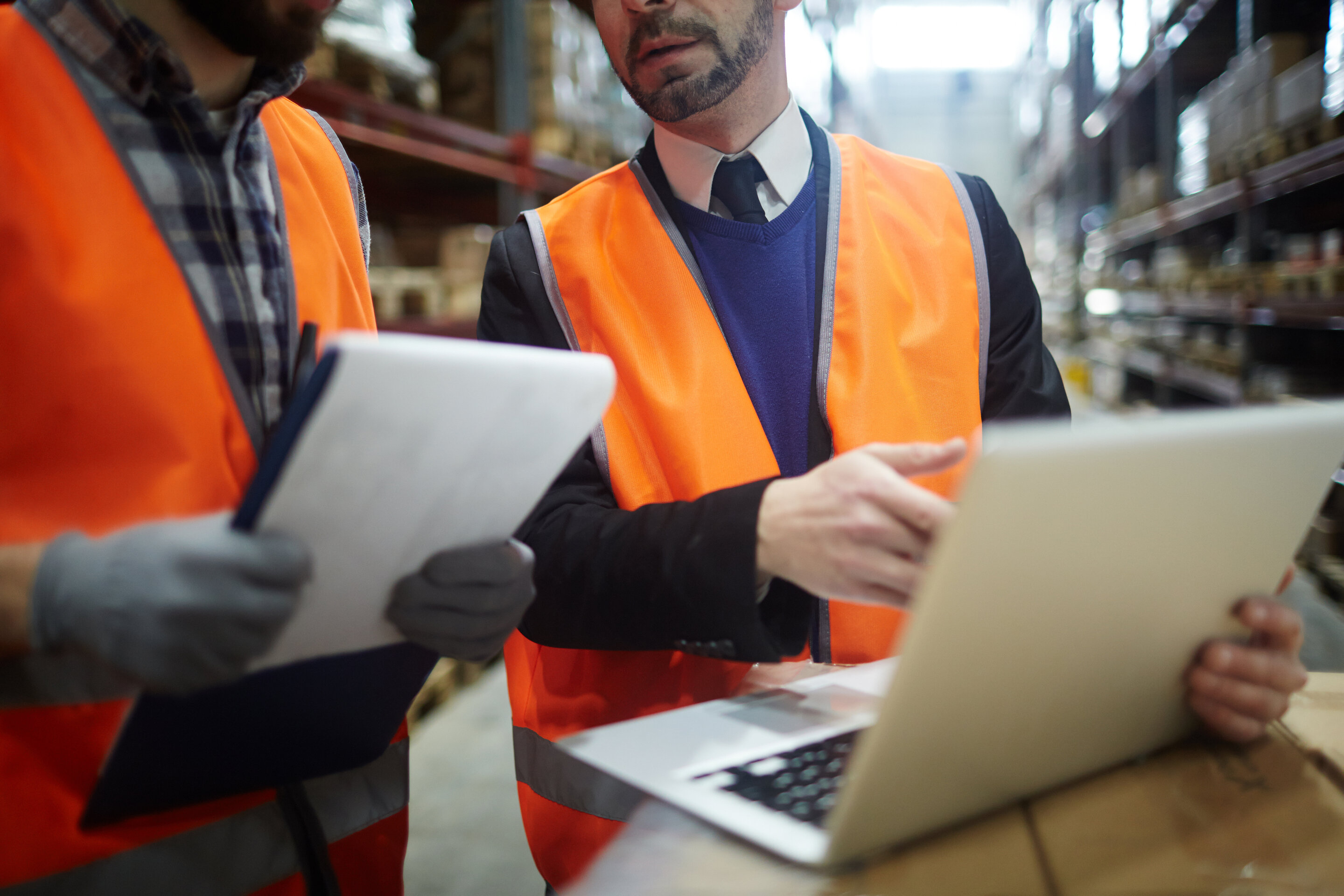
3. Offer a Referral Bonus
A referral program rewards employees who refer qualified people to a job opening at your company. Economists find employers are 4x more likely to offer a job to referrals than unknown website applicants. This means you’ll hire faster and spend less per hire. Also, referred employees are more likely to stay longer with the company compared to employees hired from job boards.
When asking for referrals, specify the requirements for all open positions, even for employees in the same department you are hiring. Incentivize employees to refer job applicants by mixing monetary and non-monetary rewards.
4. Provide Clarity on Career Progression
Your employees want to grow at your company in terms of seniority and pay over time. Clarifying their growth trajectory helps them feel confident about their growth within your company. In addition, you’ll retain top talent by promoting them to senior roles and rewarding their performance for work well done.
For example, in a survey of manufacturing workers by Deloitte and The Manufacturing Institute, fifty-eight percent of respondents said they feel manufacturing jobs have limited career prospects. However, 80% said they’d be interested in roles with enhanced training and clear career paths in the manufacturing industry.
Consider also that baby boomers still hold a large number of manufacturing jobs. However, replacing them will be difficult as they retire because young people are currently leaning towards jobs in healthcare and technology. This is due in part to the opportunities for career progression in those industries. Therefore, if you want to attract the next generation of workers, make career progression a priority.
Career progression may be more than just promotions. Employees may value job security more than a promotion if layoffs are frequent. They may want to move from part-time to full-time employees, acquire new skills, and work on complex tasks. Ask employees what they want their career growth to look like.
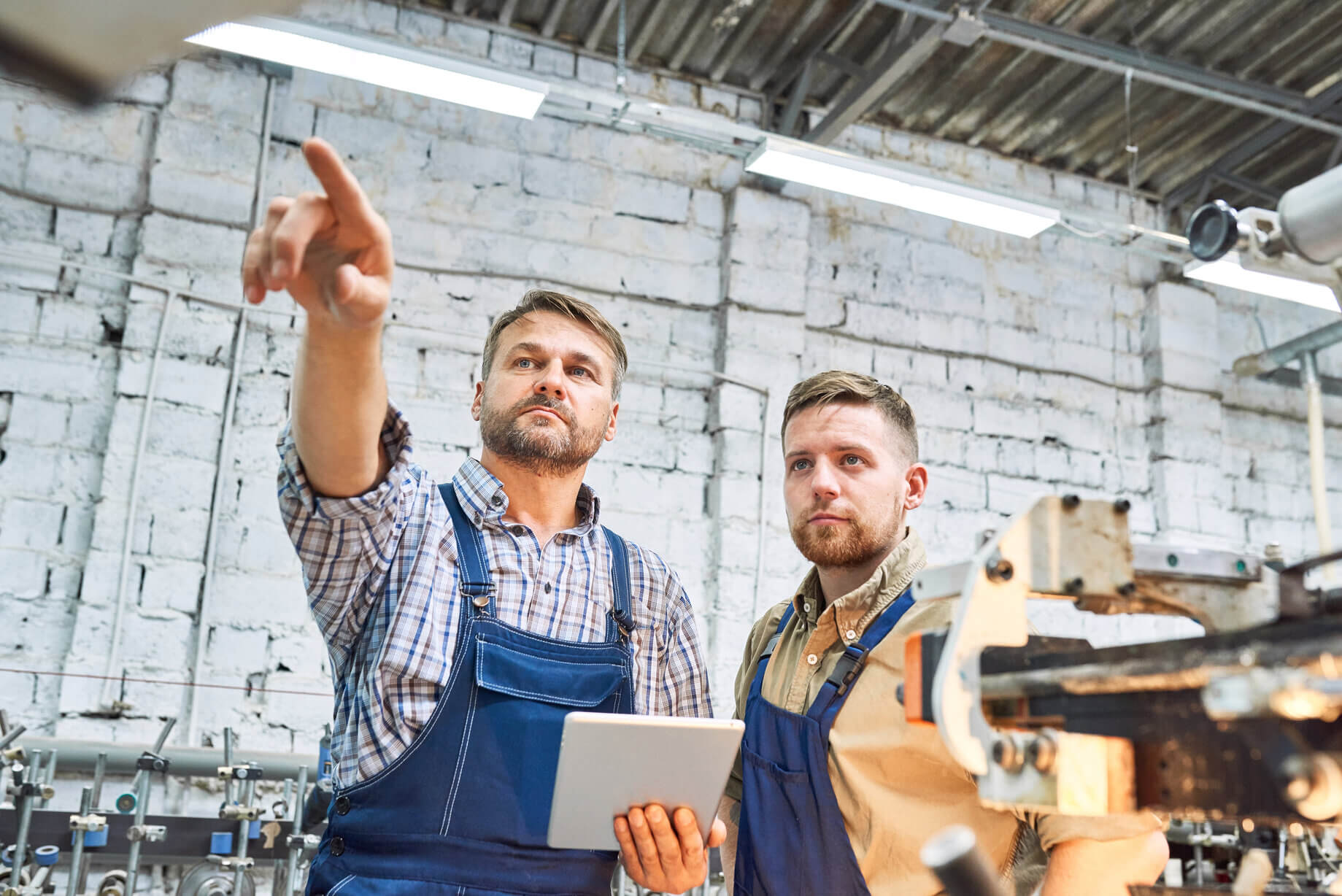
5. Provide a Supportive and Safe Work Environment
Working conditions are essential for both—bringing in employees and retaining them. A supportive and safe work environment is critical to providing employees, even entry-level employees, with fulfilling work experiences regardless of the industry.
According to Liberty Mutual, “Beyond causing stress, the lack of skilled workers has heightened workplace injury, product liability, and property damage risk for these businesses.”
In addition, employees need to feel engaged and passionate about their work. However, in 2021, only 33% of American and Canadian employees felt engaged in their work.
Monetary compensation is an essential part of the equation for your employees. And also is a powerful lever to drive employee productivity. For example, you can offer employees a per-piece incentive rather than a fixed amount for excellent performance. It’s a win-win because you’ll keep employees motivated to achieve rather than aiming for a single production threshold.
However, money is not the only element in the equation. In addition to wage growth, employees want to work with managers they admire on challenging tasks.
You also need to provide a safe environment, keep the workload reasonable to ensure good mental health, and provide benefits like healthcare in line with what your industry competitors offer.
Get MaintainX to Help Manage the Labor Shortage
Using a CMMS like MaintainX to help you automate your maintenance programs, keep track of employee successes and completion rates, and train them as they take on more complicated tasks will help create a more unified and productive workforce. In addition, MaintainX can help improve maintenance efficiency and reduce unplanned downtime, emergency repairs, and inventory costs. Check us out.
FAQs
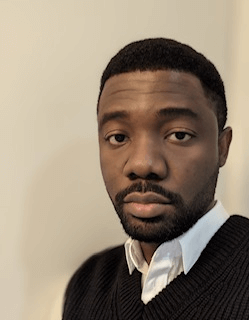
Lekan Olanrewaju is a content writer with years of experience in media and content creation. He has held positions at various media organizations, working with and leading teams at print magazines, digital publications, and television productions.