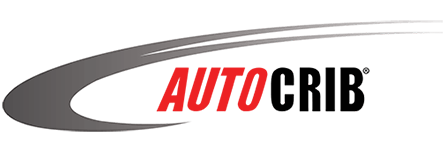
Overview
Optimize critical parts inventory with AutoCrib and MaintainX
- Prevent stockouts with real-time inventory tracking.
- Reduce costs by optimizing inventory levels and aligning stock with production needs.
- Streamline maintenance by associating consumed parts to work orders for accurate tracking and faster task completion.
- Improve maintenance planning and decision-making based on comprehensive parts data and insights.
- Automatically sync AutoCrib bins and items to MaintainX, and create or update parts as needed.
- Ensure consistency by synchronizing part details like descriptions, quantities, and unit costs in both systems.
- Create and update AutoCrib jobs from MaintainX work orders, complete with job numbers for easy tracking.
- Retroactively associate consumed parts from AutoCrib with work orders in MaintainX for precise inventory tracking.
How it works
STEP 1:
Connect with your account representative to discuss workflows and objectives for integrating AutoCrib with MaintainX.
STEP 2:
Identify the team members who will oversee testing and implementation, such as those from Operations, Maintenance, Supply Chain, and IT.
STEP 3:
A MaintainX integration consultant will meet with you to determine the scope of the integration before providing the cost and statement of work. If you choose to proceed, your consultant will map AutoCrib bins and items, and configure the scheduled sync.
STEP 4:
Test the integration with your team to ensure accuracy and functionality. Prepare internal training materials to set your users up for success.
STEP 5:
Use the integrated systems to automate inventory updates, track parts usage, and streamline maintenance workflows.
Requirements
- Must have AutoCrib inventory management solutions with data configured.
- Must have MaintainX's Premium or Enterprise Plan.
Hear from a satisfied customer
"Integrating AutoCrib with MaintainX has been a game changer for us. Their team worked closely with ours to automatically sync part records and quantities, making us more efficient. We’re already seeing the benefits of this integration in our daily operations."
Darren LeBlanc, MRO Buyer
IMT Defence
FAQs
What data is synced between AutoCrib and MaintainX?
AutoCrib bin and item data, including part descriptions, quantities, and unit costs can sync automatically with MaintainX.
How often does data sync between AutoCrib and MaintainX?
Bins and items sync can be scheduled daily, or every 8 hours. Part transactions (i.e. quantities of parts consumed) are synced the moment a work order is closed.
How does AutoCrib sync parts with MaintainX?
The integration retrieves all bins and items from AutoCrib, consolidates them into a parts list, and compares them with MaintainX parts to create or update entries accordingly.
Can AutoCrib and MaintainX track parts usage retroactively?
Yes, parts consumed from AutoCrib are retroactively associated with the correct MaintainX work order upon completion to ensure accurate usage tracking.
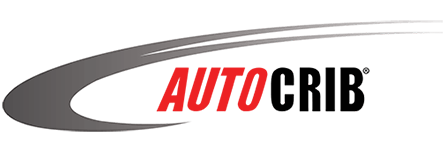
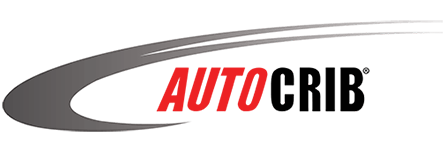
Find other integrations

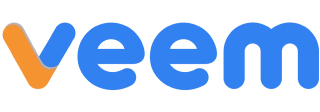
Get more done with MaintainX
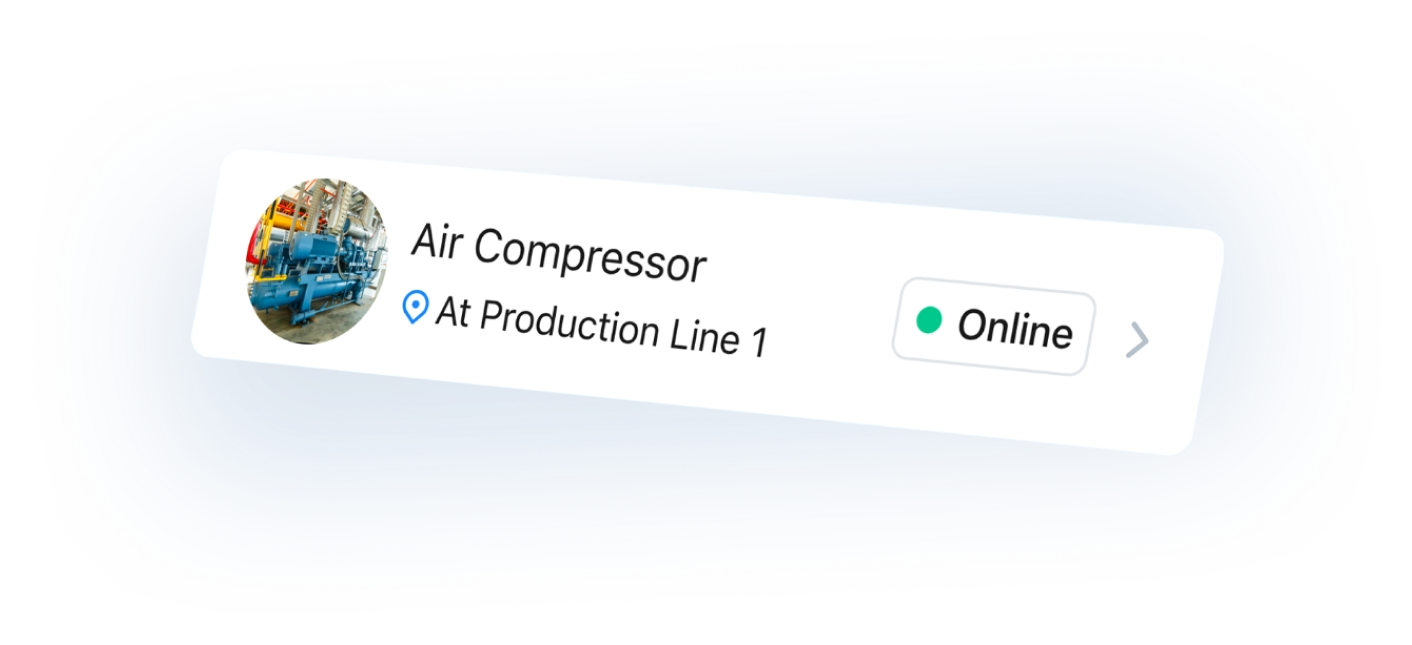
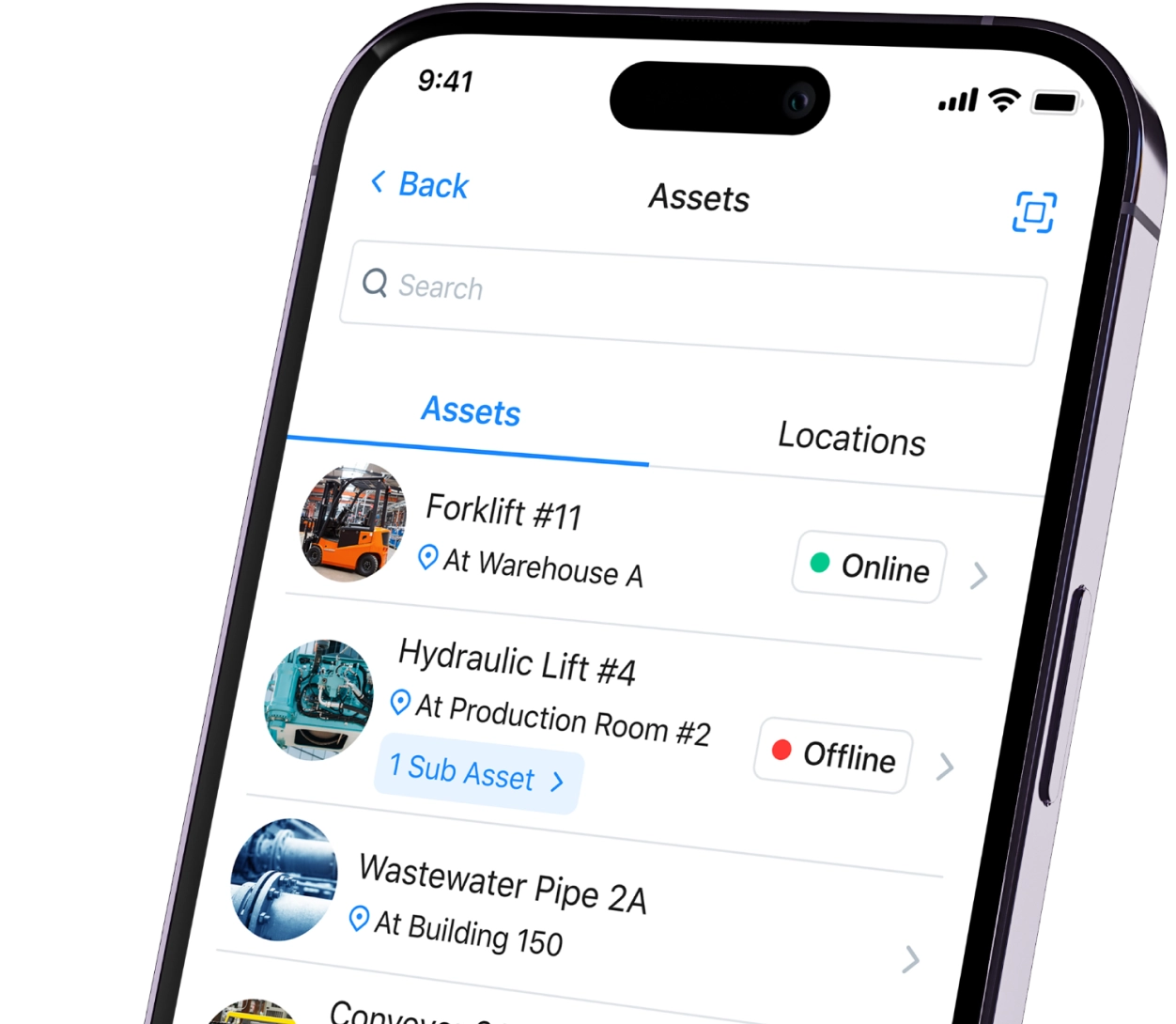