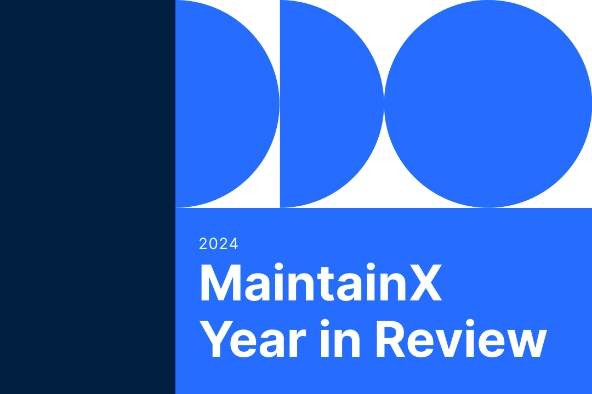
As 2024 draws to a close, we’re reflecting on another milestone year supporting industrial companies in eliminating unplanned downtime.
More than 10,000 organizations now run their frontline operations on MaintainX. And in the past year, we updated MaintainX around 140 times with new functionality to help them protect their assets, standardize maintenance, and work more efficiently.
This focus on rapid innovation has kept MaintainX at the very top of G2's CMMS rankings for nine straight quarters. And to cap off the year, MaintainX earned the #1 spot in G2’s EAM rankings as well.
The MaintainX team also doubled in size for the second year running, landing us in the Deloitte Technology Fast 500 and making us a better partner to you.
Let’s look back at MaintainX’s highlights of the past year—and why customers should be excited about 2025.
Enabling smarter, faster maintenance with AI and automation
The volume and quality of shop floor data captured in MaintainX is impressive. Almost 5 million assets are now managed in the system, and around 17 million work orders were closed in 2024 alone.
Some of our most impactful updates over the past year enabled customers to turn this data into clear action—steps that protect equipment from failing.
More than 40,000 procedures were generated with AI in 2024, helping customers digitize equipment manuals and checklists quickly. MaintainX’s AI also averted major failures, catching more than 22,000 equipment anomalies and triggering thousands of corrective actions.
With 200,000+ meters, including IoT devices, also registered in MaintainX, we released Workflow Automations last month to enable more powerful and cost-effective condition-based workflows.
MaintainX is now enabling companies to connect their equipment data and leverage AI quickly—which is set to add thousands of production hours to our customers’ operations over the next 12 months.
Scaling operational excellence with multi-site standardization
With better visibility and insight than ever before, MaintainX customers standardized processes and optimized inventories at great scale in 2024.
Global Parts Management launched in March, enabling enterprise companies to share inventory across sites to reduce overstocking and emergency shipping fees. And in September, Global Procedures helped multi-site leaders standardize best practices by sharing and updating procedures across all their facilities at once.
Continuous updates to our Reporting module, including new asset reliability insights, also helped companies allocate their resources better in 2024. Precise and actionable insights were served to maintenance and reliability leaders around 2 million times, both in real-time and via scheduled emails.
On the road building stronger partnerships with customers
The MaintainX team travelled more than a million miles in 2024, visiting customers and partners at industry trade shows, factory tours, and on-site implementations.
We exhibited at more than 20 conferences in the United States, including IMTS, FABTECH, PackExpo, and the International Maintenance Conference (IMC).
The year got underway with the 50th Anniversary of the World of Concrete, where MaintainX won the People’s Choice Award for Most Innovative Product across all Business & Technology Software & Services.
IMTS was another highlight, as we unveiled Asset Connect to the world. The platform allows OEMs to monitor deployed customer equipment across facilities, boosting post-sales revenue and customer satisfaction.
The SAP Industry Ecosystem team hosted MaintainX at Hannover Messe in Germany, where we showcased a joint case study with Duracell, the #1 trusted consumer battery manufacturer.
Events like SAP Innovation Day in Las Vegas demonstrated how partnerships help customers streamline processes and achieve their goals through connected technology.
MachineMetrics, our long-term partner in connected machine data and automation, joined us on a special Wrench Factor episode to explore how manufacturers can use real-time maintenance data to drive productivity, sustainability, and smarter capital planning.
Our professional services team completed many on-site implementations throughout 2024, helping teams increase their efficiency with MaintainX as quickly as possible.
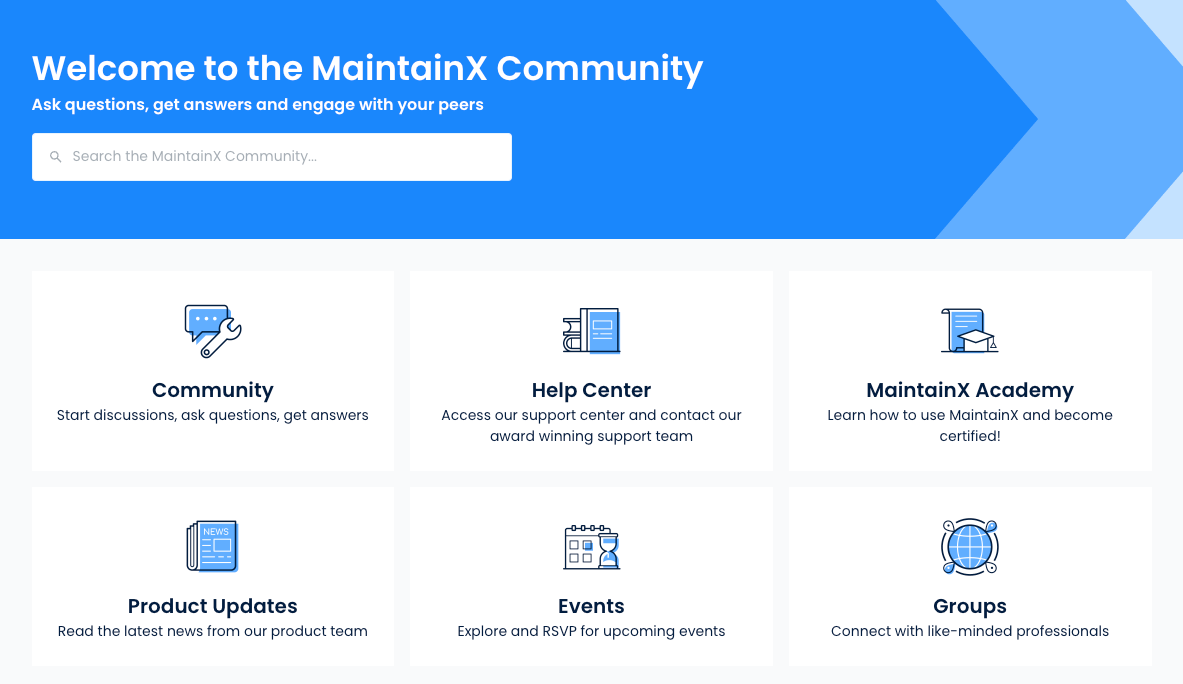
Investing more in support, implementation, and engineering
With great growth comes great responsibility. And as we extended our customer roster in 2024, we also bolstered our support infrastructure with new programs and headcount.
The year got off to a flying start as we unveiled the MaintainX Community. Thousands of MaintainX users have been sharing recommendations and best practices with each other since the forum went live in January.
Shortly afterwards, we extended our support hours to 24/7 and rolled out new certifications in the MaintainX Academy to help our customers learn and get the answers they need, whether day or night.
We also tripled the size of our customer support, professional services, and customer success teams, which worked tirelessly to import data, build PM strategies and asset hierarchies, and deliver powerful business outcomes throughout 2024.
Our focus on service excellence was recognized in this year’s Stevie Awards, as MaintainX won Customer Service Team of the Year.
And it helped manufacturers like Interroll and Wauseon Machine to cut downtime by 20% and reduce parts inventory spend.
Another year of building with our customers
Our success in 2024 couldn’t have been achieved without continued feedback and inspiration from our customers. Every enhancement was built and released with input and guidance from maintenance and reliability leaders.
We’d like to thank everybody for submitting feedback, helping us design new features, and testing them with us before we brought them to market.
If you’re not yet a customer of MaintainX, book a tour today and get a sneak peek of what’s in store for 2025.
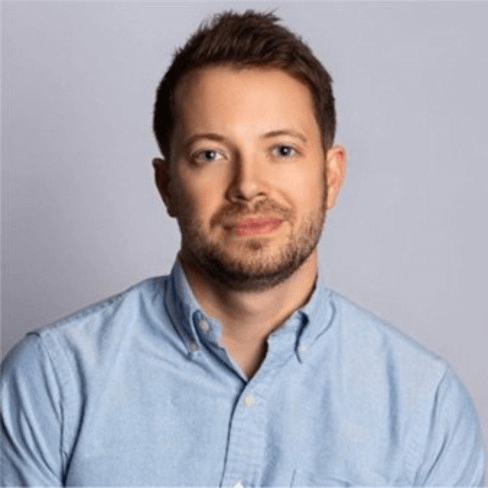
Colin Strachan is a Senior Product Marketing Manager at MaintainX, with a background in journalism and almost a decade of experience in SaaS marketing. In the past few years, he has worked with some of the world’s largest enterprises to adopt software that empowers their employees to work more effectively.