Maintenance is key to balancing an asset’s efficiency and lifespan. This post explains the meaning of factory maintenance, maintenance strategies, and the types of skills maintenance team members need to optimize factory maintenance.
More complex manufacturing processes and automation make maintenance services more challenging. However, with the right strategies, you can minimize the cost of maintaining assets and improve production efficiency.
Factory maintenance (or industrial maintenance) is the process of ensuring all assets operate optimally. The best maintenance managers aim to hit the sweet spot between controlling maintenance expenses and maintaining assets in excellent condition.
A robust factory maintenance program helps you consistently achieve production targets and produce the best quality products. More importantly, it helps prevent costly downtime from keeping your production running. The right basic maintenance—based on planning for the regular wear and tear on company assets—leads to continuous improvement.
Downtime results in idle time, wasted resources, and other implicit expenses. Unplanned downtime costs manufacturers up to $50 billion annually, and that’s why investing in maintenance can pay rich dividends in the long term.
Factory Maintenance Strategies
Factory maintenance strategies differ in terms of technique, budget, and maintenance needs. Traditionally, manufacturers relied on reactive maintenance strategies. However, modern businesses focus on proactive maintenance strategies like the ones discussed below.
Ideally, you should use multiple strategies based on your assets’ maintenance needs and the availability of maintenance equipment and other resources.
Preventive Maintenance (PM) Factory Maintenance
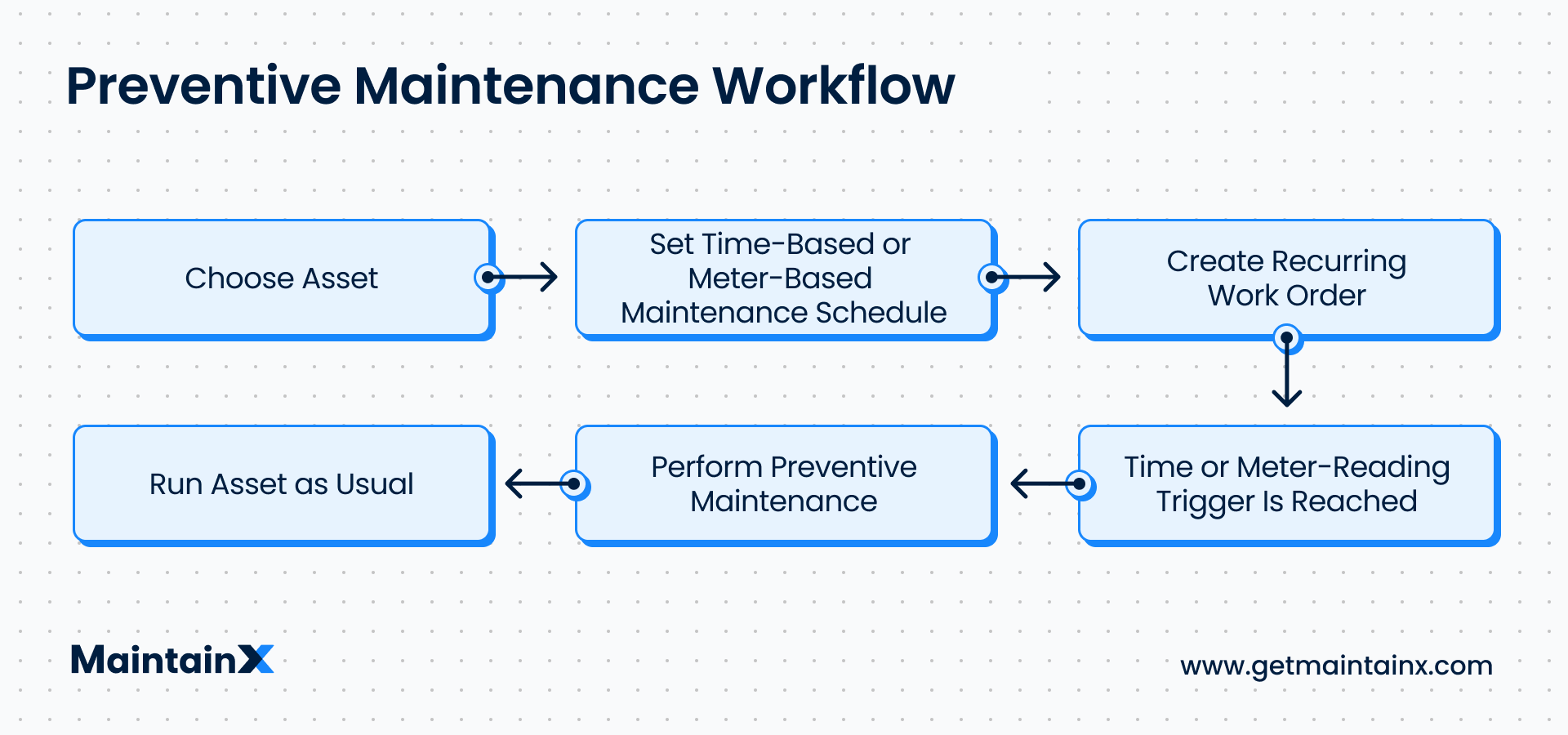
The best way to prevent a breakdown is to address problems before the equipment breaks down. Preventive maintenance is the most cost-effective factory maintenance strategy, provided you implement it consistently.
Preventive maintenance refers to scheduled maintenance activities completed to keep assets in optimal condition, prevent unplanned downtimes, and maintain safety. Common PM tasks include inspecting, cleaning, lubricating, adjusting, replacing, and repairing equipment parts before a breakdown.
Managers schedule PM work orders based on time, usage, or behavioral triggers. Operational managers schedule, assign, and track recurring tasks. Simple examples of preventive maintenance are taking your car in for an oil change every 3000 miles or calendar-based lubricating of all ball bearings on a roller every two weeks. Manually managing maintenance data for a PM program can become challenging. That’s why you need a computerized maintenance management system (CMMS).
A CMMS like MaintainX can manage your data, present it visually so it’s easier to make decisions, and provide in-app chat functionality so you can easily collaborate with your team members on maintenance tasks.
Run-to-Failure (RTF) Maintenance Factory Maintenance
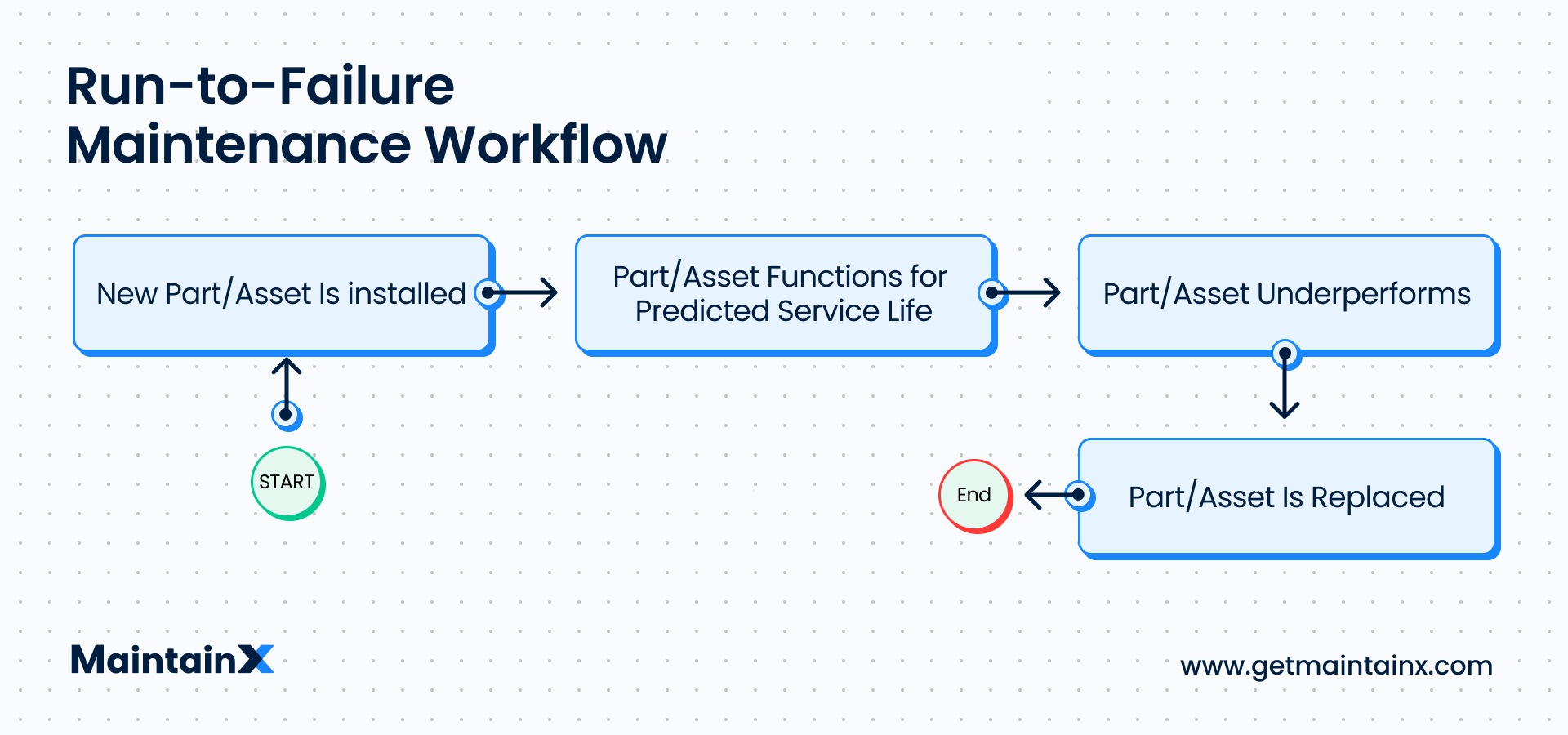
Run-to-failure might not sound like the most intuitive strategy, but it sometimes makes sense. This maintenance solution involves deliberately allowing assets to operate until they fail, and only then performing necessary maintenance tasks to restore functionality.
Run-to-failure maintenance should not be confused with neglecting a piece of equipment until it fails. Instead, it involves a deliberate plan for remedial actions to be taken post-breakdown. A good RTF plan also means that inventory management is crucial because replacement parts need to be available when an asset fails.
With supply chain challenges these last few years, you need to make sure you plan ahead and have spare parts on hand. A well-run RTF should not mean that your company’s profitability takes a hit anytime an asset fails.
Also, running an asset to failure makes the most financial sense if an asset doesn’t cost a lot to replace or if the maintenance cost is higher than the cost of replacing the asset.
Contrary to common belief, RTF requires careful planning and assessment to ensure you have the needed resources like staffing and inventory when failure does occur. In addition, you must ensure that the standard operating procedures (SOPs) are up-to-date and easily accessible.
Condition-Based Maintenance (CBM) Factory Maintenance
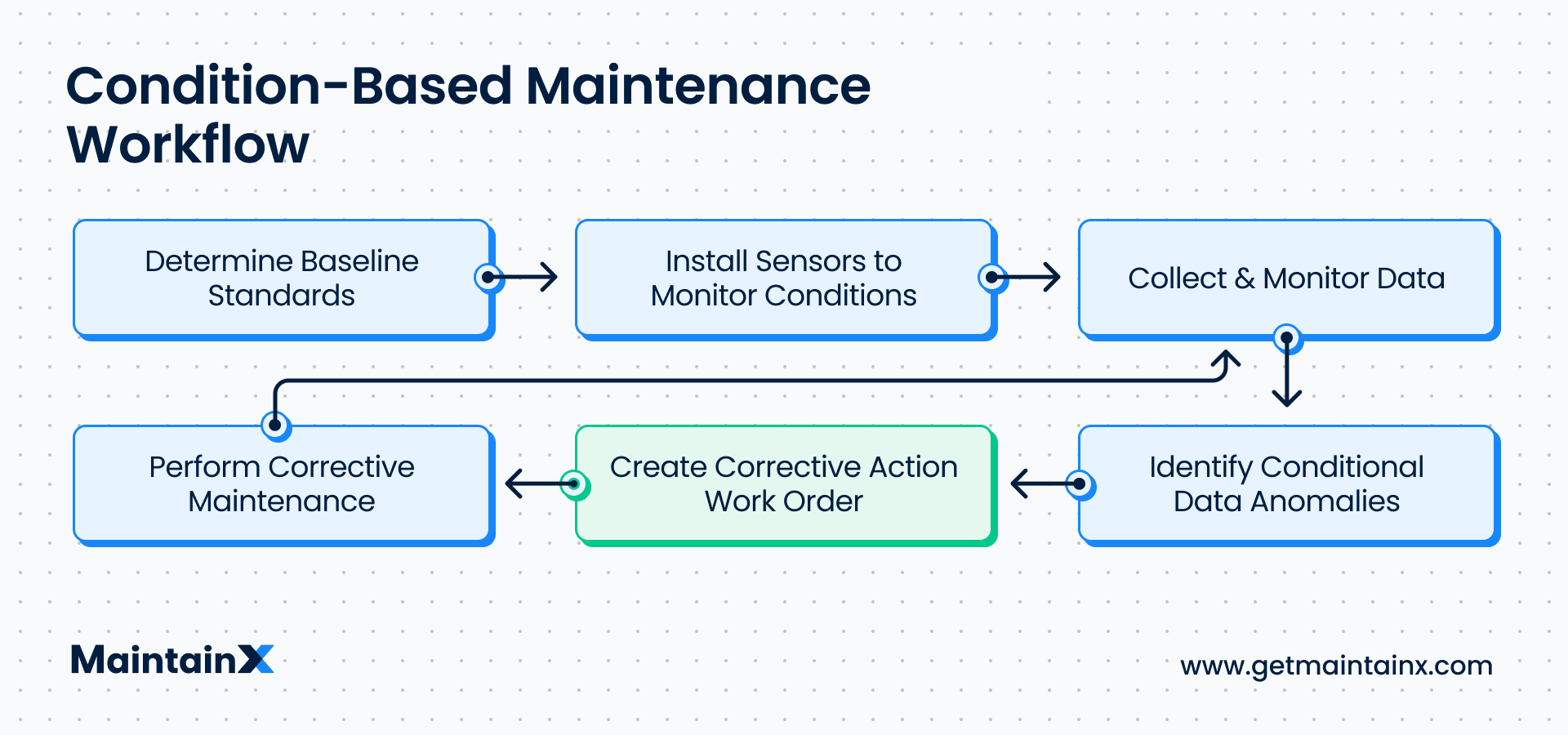
Condition-based maintenance (CBM) is a type of maintenance strategy that involves monitoring an asset’s current condition using methods like vibration analysis, visual inspection, and other non-destructive testing (NDT) techniques. CBM techniques allow you to detect changes before the equipment fails.
However, CBM is still a valuable plant maintenance strategy to minimize downtime. The information you get from CBM also can inform your preventive maintenance schedule to increase uptime and reduce the chances of future problems with the asset.
Predictive Maintenance (PdM) Factory Maintenance
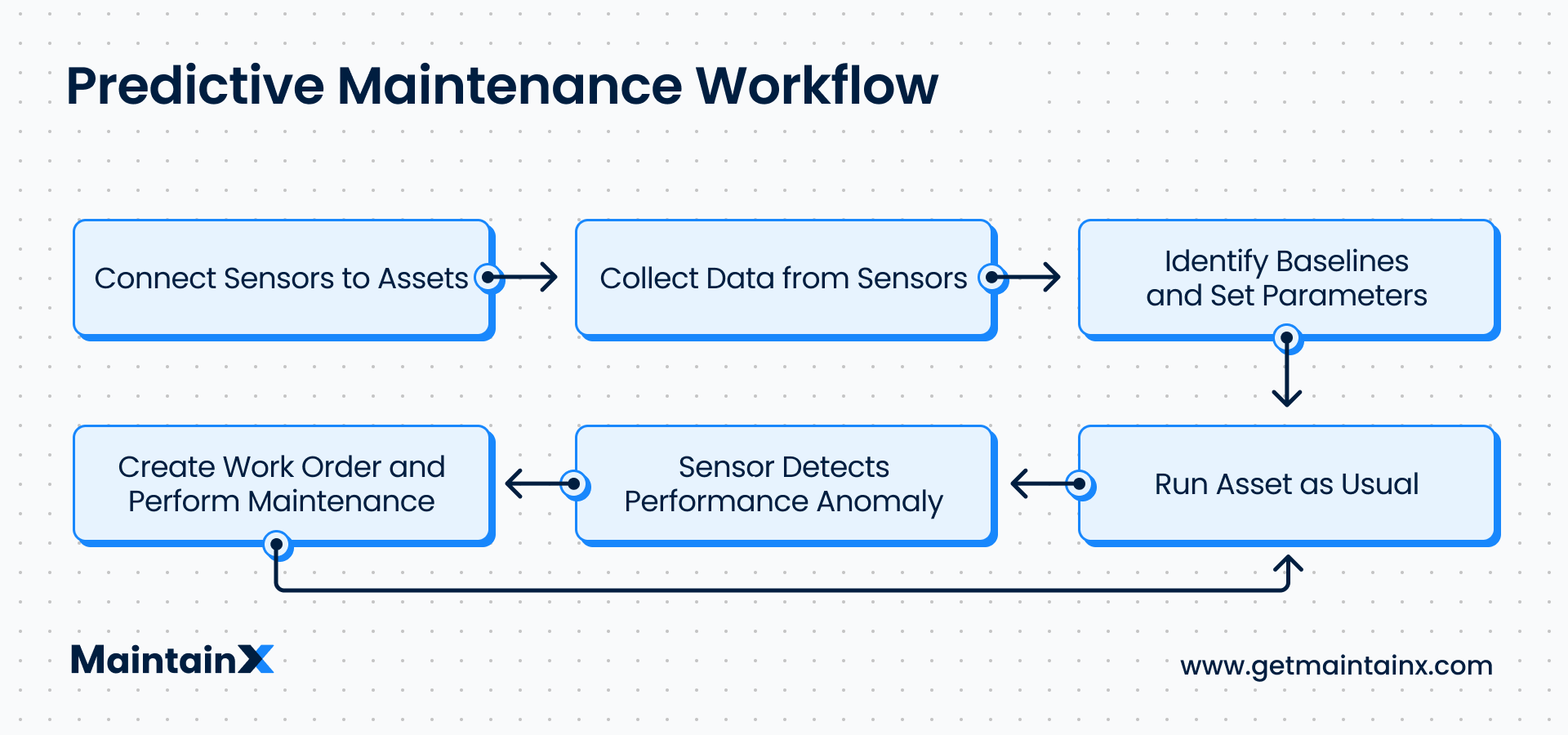
Predictive maintenance uses the data compiled by condition-monitoring equipment like sensors and infrared thermography cameras to identify patterns in problems related to an asset or asset class.
PdM relies on machine learning to establish a benchmark for operational data. The PdM algorithm then uses these metrics to predict an asset’s future performance. Put simply, PdM uses your current and historical data collected through condition-monitoring equipment and IoT devices and identifies the potential for failure.
Training and Certifications for Industrial Maintenance
Effective maintenance requires experts with practical knowledge and hands-on experience maintaining industrial equipment.
When hiring new members to the maintenance team or helping your existing team members upskill, you may want to consider the maintenance certifications mentioned below. The median salary for industrial maintenance technicians is ~$50,000. Completing these certifications can help maintenance professionals demand better salaries closer to $65,000 at the upper end of the range.
Certified Maintenance and Reliability Professional (CMRP)
The Society for Maintenance and Reliability Professionals (SMRP) offers the CMRP certification, accredited by the American National Standards Institute (ANSI) as per the International Standardization Organization (ISO) standards.
The CMRP certification enables maintenance professionals to acquire a working knowledge of supervising maintenance processes from an administrative point of view.
The CMRP Body of Knowledge includes five distinct pillars: business management, manufacturing process reliability, equipment reliability, organization and leadership, and work management. Collectively, these subjects help maintenance professionals acquire the skill set to oversee maintenance activities.
Certified Maintenance and Reliability Technician (CMRT)
SMRP also offers CMRT. Unlike CMRP, CMRT focuses only on maintenance skills. It’s an excellent certification for professionals who want to strengthen their core maintenance skill set.
The certification’s competency exams test professionals in areas like troubleshooting and analysis, preventive and predictive maintenance, corrective maintenance, and facility maintenance practices.
The exams cost $300 each, and you can take an exam once every six months. Test takers don’t require additional coaching or training—SMRP provides resources to study for the tests.
Certifications from the Institute Maintenance Institute (IMI)
The IMI offers certifications for professionals at various stages in their careers and areas of specialization. You can take an IMI test to hone your technical and management capabilities.
You can choose from three domains: Certified Maintenance Technician, Certified Maintenance Professional, and Certified Maintenance Manager. IMI offers certifications at various levels in these domains—you can pick one based on your goals.
Use MaintainX to Streamline Factory Maintenance
Factory maintenance looks different for manufacturers depending on the industry, size, and type of manufacturing facility. However, all manufacturers should manage and centralize data to streamline the processes in their maintenance plan.
MaintainX is a mobile-friendly CMMS software with a built-in chat option. It automates maintenance processes and makes it easier to perform maintenance work. To make intelligent decisions, you can create a maintenance checklist, work orders, standard operating procedures, and metric-driven reports.
Ready to digitize your maintenance program to MaintainX? It’s free.
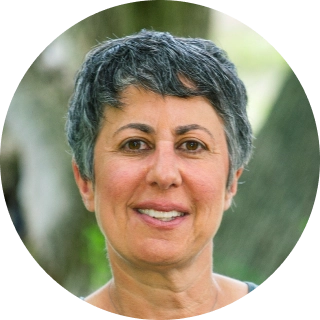
Caroline Eisner
Caroline Eisner is a writer and editor with experience across the profit and nonprofit sectors, government, education, and financial organizations. She has held leadership positions in K16 institutions and has led large-scale digital projects, interactive websites, and a business writing consultancy.
See MaintainX in action