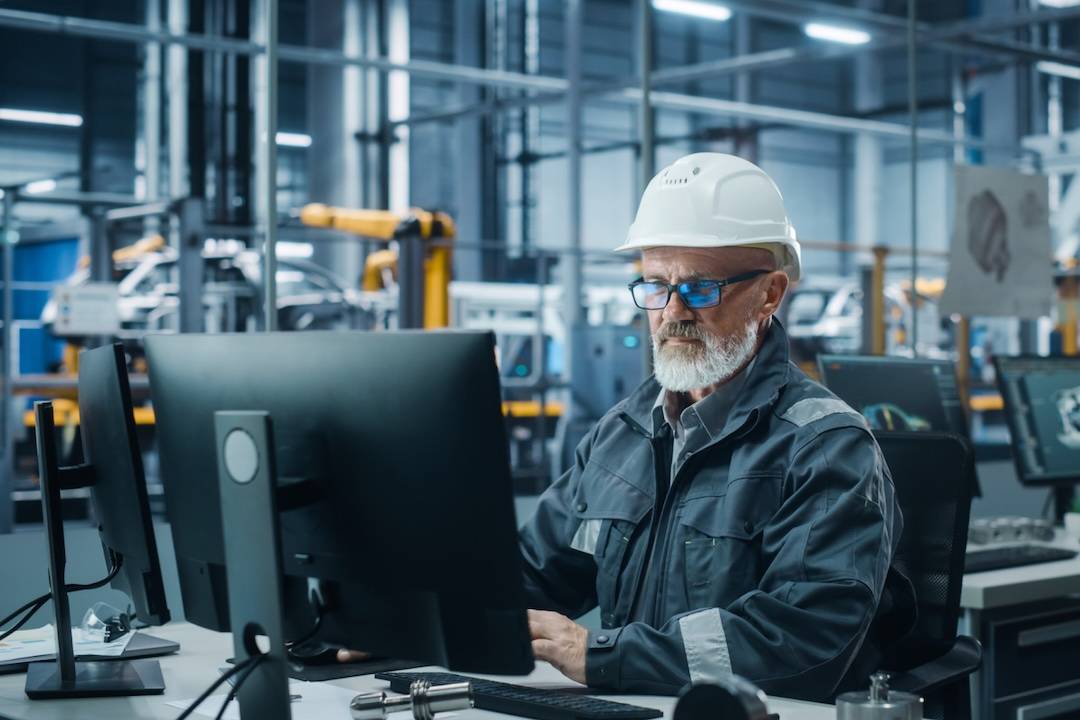
Maintenance managers and leaders are under a tremendous amount of pressure. To meet growing business demands, it's essential to keep equipment not only running, but performing at its best.
Information is piling up in systems, expert technicians are retiring, and unplanned downtime is costing valuable time and resources. And while technicians face these challenges on the ground, managers need big-picture solutions to keep operations running smoothly.
AI is stepping in to help with tools that not only support technicians but also make a real impact on management goals. By streamlining maintenance processes, providing data-backed insights, and improving workforce efficiency, AI is turning into an essential resource for maintenance leaders.
Here are three ways AI can address the biggest challenges facing maintenance leaders today:
1. Standardize maintenance work across sites
One of the hardest parts of maintenance management is making sure everyone follows the right procedures to keep equipment reliable and safe. Creating digital work orders and procedures can be time-consuming and difficult—especially when you have to dig through hundreds of pages to find and consolidate information into a single process.
AI changes this by turning asset manuals and past work orders into standardized procedures and work orders. With tools like AI Assistants, managers can create digital maintenance documents in minutes instead of hours, ensuring every technician follows the same process. This consistency helps extend asset life, improve reliability, and reduce unexpected downtime. Plus, when work is standardized across all locations, maintenance becomes more predictable and easier to manage.
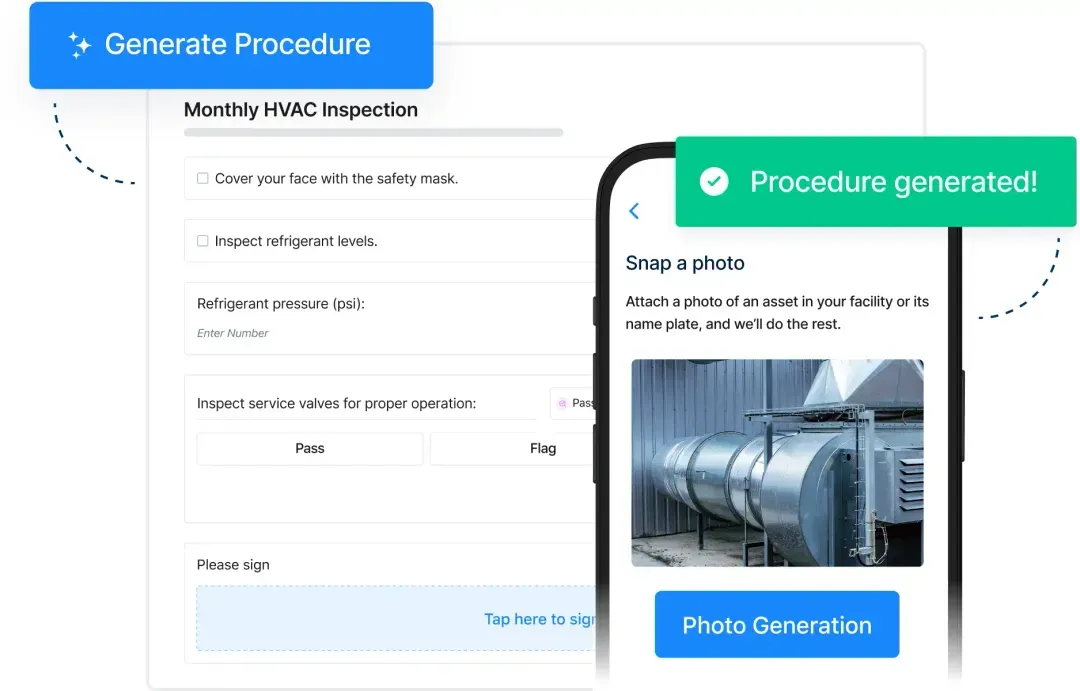
2. Improve Planning Estimates
With maintenance processes standardized, you can also start to collect more focused data on how long each step will take. As you’ve likely experienced, that information is critical to having the right inventory and materials on-hand, avoiding overtime costs, and maximizing wrench hours. But estimating today can often be a best-guess, especially for complex tasks or when a team has varying levels of experience.
AI-powered estimates can take the guesswork out of planning. By analyzing data from past work orders, it can provide accurate estimates for new tasks, giving you a realistic idea of how long each job should take. These insights can help you to balance workloads, plan ahead to avoid unplanned overtime, and maximize the team’s capacity to keep everything running smoothly. With AI-driven estimates, planning becomes more strategic, leading to better productivity across the team.
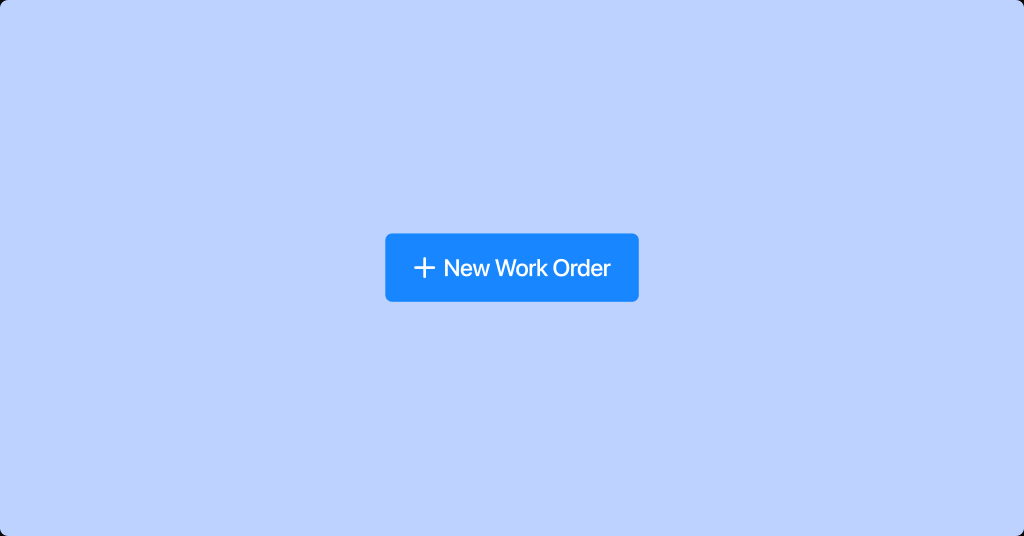
3. Equip technicians with the right AI tools
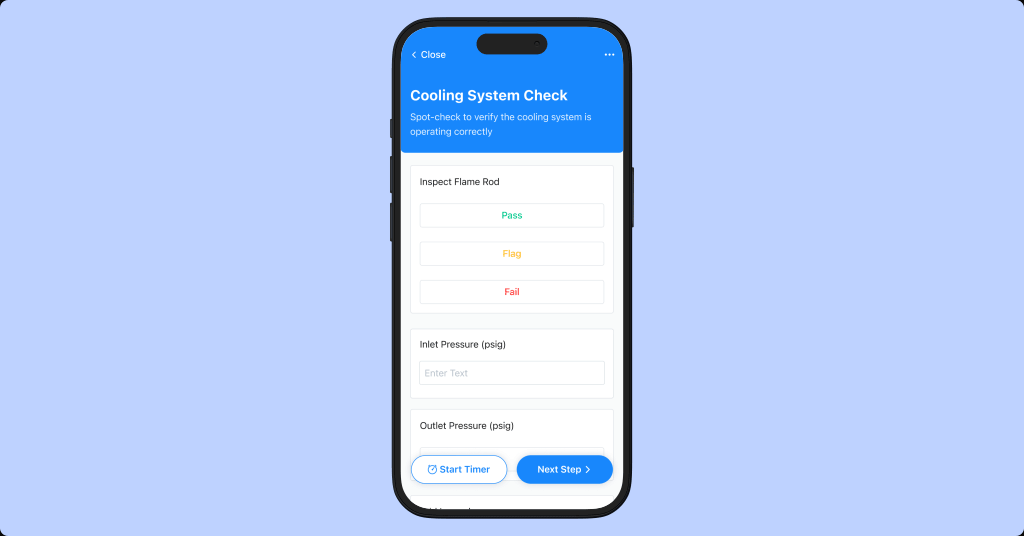
One of the most impactful ways to benefit from AI is by equipping your technicians with tools that help them work smarter, faster, and more efficiently. These AI-driven tools include:
- AI Assistants that enable technicians to create accurate maintenance documents directly from the facility floor and provide real-time guidance from asset manuals during tasks.
- Anomaly Detection to catch potential errors in data entry or identify early signs of equipment issues, helping prevent small problems from becoming big ones.
- Voice Transcription that keeps technicians’ hands free for the work itself, reducing the need for manual documentation.
With these tools, technicians can work more confidently and accurately, leading to fewer errors, more consistent maintenance, and a more efficient team. This means more effective wrench hours, more assets serviced, and ultimately, improved asset reliability and availability across the board.
The future of maintenance is AI-driven
As maintenance continues to evolve, AI is proving to be more than just a tool—it’s a strategic advantage. By standardizing work, improving planning accuracy, and empowering technicians with real-time insights, AI offers maintenance teams the support they need to keep assets at their best. For managers, this means achieving greater operational consistency and reliability across sites, while reducing downtime and optimizing resources. With AI as a key part of the maintenance strategy, teams are positioned to meet growing demands, overcome workforce challenges, and keep operations running smoothly into the future.
Ready to learn more about AI? Read about challenges AI can help maintenance teams solve in our latest whitepaper.
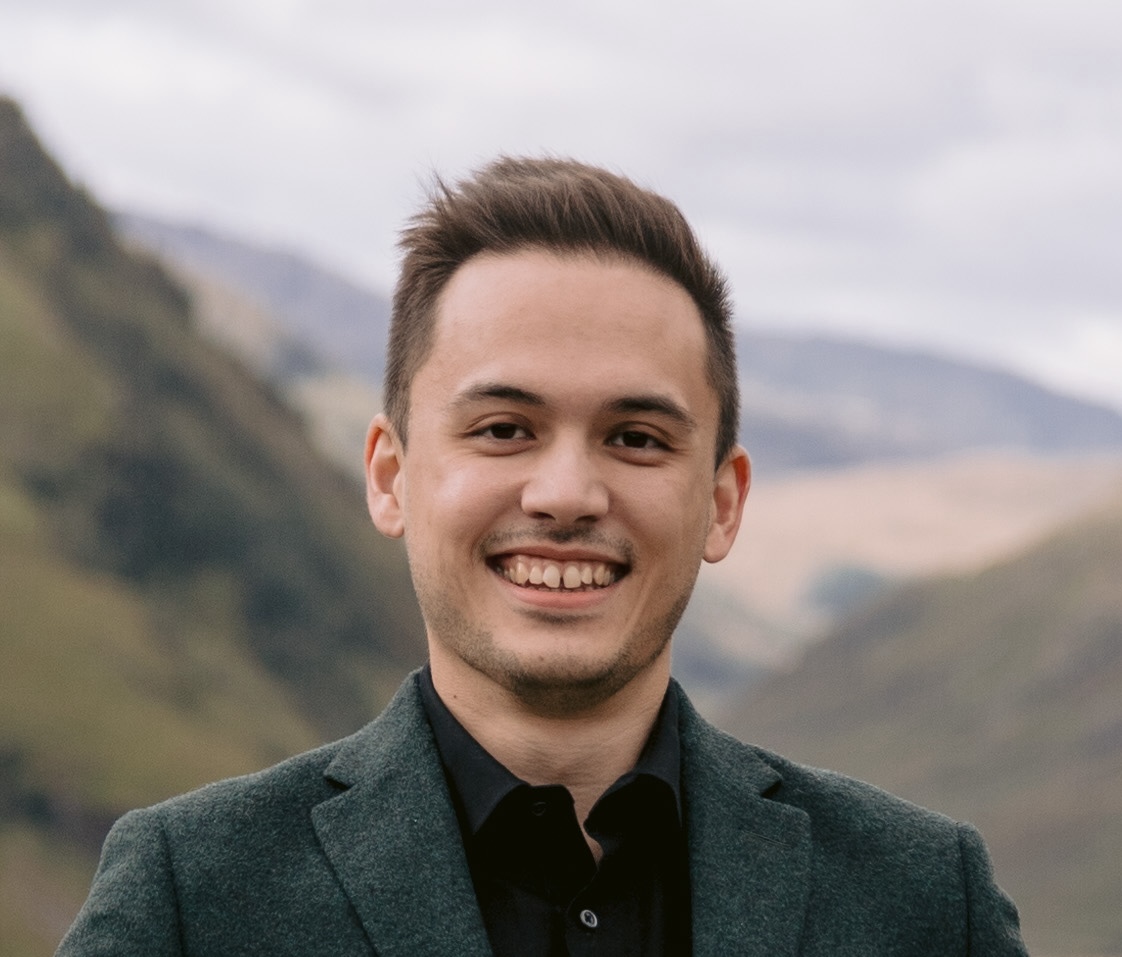
Andrew Benjamin is a Senior Product Marketing Manager at MaintainX with nearly a decade of experience marketing SaaS products. Of late, he’s guided organizations through digital transformation initiatives, and enabled them to harness actionable insights from their data using AI & ML models.